The Importance of PCB Functional Testing
PCB functional testing is essential for several reasons:
-
Quality Assurance: Functional testing ensures that the manufactured PCB meets the required quality standards and performs as expected. It helps identify defects, shorts, opens, and other issues that may affect the PCB’s functionality.
-
Reliability: By conducting thorough functional tests, manufacturers can ensure that the PCB will operate reliably in its intended environment. This is particularly important for PCBs used in critical applications, such as medical devices, aerospace, and automotive systems.
-
Cost Savings: Identifying and fixing issues during the functional testing stage is more cost-effective than discovering problems after the PCB has been integrated into the final product. Early detection of faults saves time and resources in the long run.
-
Compliance: Functional testing helps ensure that the PCB complies with industry standards and regulations, such as IPC (Institute of Printed Circuits) standards, RoHS (Restriction of Hazardous Substances), and UL (Underwriters Laboratories) certifications.
Types of PCB Functional Tests
There are several types of functional tests performed on PCBs, each targeting specific aspects of the board’s performance. Some of the most common tests include:
In-Circuit Testing (ICT)
In-Circuit Testing is a powerful technique that verifies the functionality of individual components on the PCB. It involves using a bed-of-nails fixture to make contact with the component leads and test points on the board. The test system applies stimuli and measures the response of each component to ensure proper functionality.
Advantages of ICT:
– Tests individual components independently
– Detects component-level faults, such as incorrect values, opens, and shorts
– Provides high test coverage and fault diagnosis
Flying Probe Testing
Flying Probe Testing is an alternative to ICT that does not require a dedicated test fixture. Instead, it uses movable probes to make contact with test points on the PCB. The probes can move freely across the board, allowing for more flexibility in testing different PCB designs.
Advantages of Flying Probe Testing:
– No need for a custom test fixture
– Suitable for low-volume production and prototype testing
– Offers high test coverage and fault diagnosis
Boundary Scan Testing (BST)
Boundary Scan Testing, also known as JTAG (Joint Test Action Group) testing, is a method that uses a special test access port (TAP) to test the interconnections between digital components on the PCB. It is particularly useful for testing complex digital circuits, such as FPGAs, microprocessors, and memories.
Advantages of BST:
– Tests interconnections between digital components
– Detects faults in hard-to-reach areas of the PCB
– Provides high test coverage for digital circuits
Functional Test Fixtures
Functional test fixtures are custom-designed setups that simulate the actual operating environment of the PCB. They include connectors, loads, and interfaces that mimic the PCB’s intended application. Functional test fixtures are used to verify the overall functionality and performance of the PCB under real-world conditions.
Advantages of Functional Test Fixtures:
– Tests the PCB in its intended operating environment
– Verifies overall system functionality and performance
– Detects issues related to signal integrity, power, and connectivity
Test Equipment for PCB Functional Testing
To perform functional testing effectively, manufacturers use various types of test equipment. Some of the essential equipment include:
-
Automated Test Equipment (ATE): ATE systems are computer-controlled test platforms that automate the functional testing process. They include hardware and software components that apply stimuli, measure responses, and analyze test results.
-
Oscilloscopes: Oscilloscopes are used to visualize and measure electrical signals on the PCB. They are essential for debugging and troubleshooting issues related to signal integrity, timing, and noise.
-
Multimeters: Multimeters are versatile instruments that measure various electrical parameters, such as voltage, current, resistance, and continuity. They are used for basic troubleshooting and verification of component values.
-
Logic Analyzers: Logic analyzers are used to capture and analyze digital signals on the PCB. They are particularly useful for debugging complex digital circuits and verifying the timing and functionality of digital components.
-
Thermal Imaging Cameras: Thermal imaging cameras are used to detect hot spots and thermal issues on the PCB. They help identify problems related to power dissipation, component overheating, and thermal management.
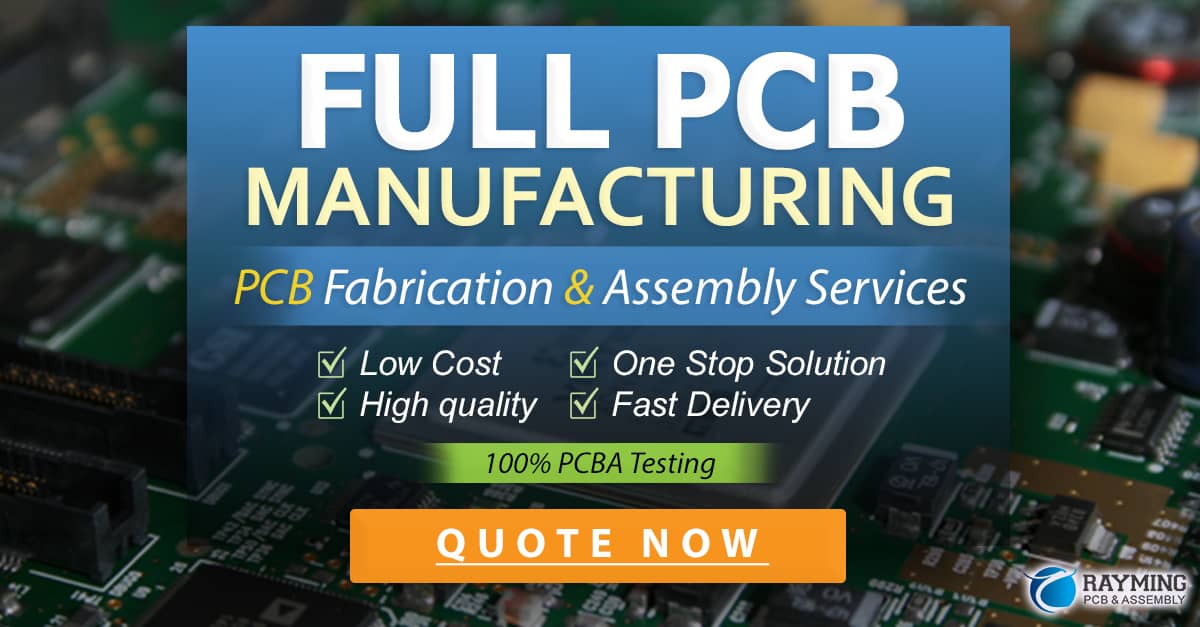
Best Practices for PCB Functional Testing
To ensure effective and efficient functional testing, manufacturers should follow these best practices:
-
Develop a Comprehensive Test Plan: Create a detailed test plan that outlines the specific tests to be performed, test coverage, acceptance criteria, and test sequence. This plan should be based on the PCB design specifications and industry standards.
-
Use Automated Testing: Implement automated testing wherever possible to increase efficiency, reduce human error, and ensure consistent test results. Automated test equipment can perform tests faster and more accurately than manual testing.
-
Maintain Proper Test Documentation: Maintain detailed test documentation, including test procedures, test setup, test results, and failure analysis reports. This documentation serves as a reference for future troubleshooting and process improvement.
-
Implement Statistical Process Control (SPC): Use SPC techniques to monitor and control the functional testing process. SPC helps identify trends, variations, and anomalies in the test results, allowing for early detection and correction of issues.
-
Conduct Regular Calibration and Maintenance: Ensure that all test equipment is regularly calibrated and maintained according to the manufacturer’s guidelines. This helps maintain the accuracy and reliability of the test results.
-
Train and Certify Test Personnel: Provide proper training and certification for test personnel to ensure they have the necessary skills and knowledge to perform functional testing effectively. This includes understanding test procedures, operating test equipment, and interpreting test results.
Frequently Asked Questions (FAQ)
-
What is the difference between functional testing and structural testing?
Functional testing focuses on verifying the overall functionality and performance of the PCB, while structural testing, such as In-Circuit Testing, focuses on testing individual components and their interconnections. -
Can functional testing detect all types of PCB defects?
Functional testing is effective in detecting a wide range of defects, but it may not detect certain types of faults, such as latent defects or intermittent issues. It is important to use a combination of different test methods to achieve comprehensive test coverage. -
How do I determine the appropriate test coverage for my PCB?
The appropriate test coverage depends on various factors, such as the complexity of the PCB, the criticality of the application, and the industry standards and regulations. It is recommended to consult with experienced test engineers and refer to relevant standards to determine the optimal test coverage. -
What are the benefits of using boundary scan testing (BST)?
BST offers several benefits, including the ability to test interconnections between digital components, detect faults in hard-to-reach areas of the PCB, and provide high test coverage for digital circuits. It is particularly useful for testing complex digital designs. -
How often should I calibrate my test equipment?
The calibration frequency of test equipment depends on factors such as the manufacturer’s recommendations, the usage frequency, and the environmental conditions. It is important to follow the manufacturer’s guidelines and establish a regular calibration schedule to ensure the accuracy and reliability of the test results.
Conclusion
PCB functional testing is a critical process that ensures the quality, reliability, and compliance of manufactured PCBs. By conducting thorough functional tests using various techniques and equipment, manufacturers can identify and rectify issues early in the production cycle, saving time and resources. Implementing best practices, such as developing comprehensive test plans, using automated testing, and maintaining proper documentation, further enhances the effectiveness of functional testing.
As PCB designs continue to become more complex and the demands for high-quality and reliable electronics increase, the importance of PCB functional testing will only grow. By staying up-to-date with the latest testing technologies and adhering to industry standards, manufacturers can deliver PCBs that meet the ever-evolving needs of the market.
Test Type | Purpose | Advantages |
---|---|---|
In-Circuit Testing (ICT) | Verifies functionality of individual components | Tests components independently, detects component-level faults |
Flying Probe Testing | Alternative to ICT, uses movable probes | No custom fixture, suitable for low-volume and prototype testing |
Boundary Scan Testing (BST) | Tests interconnections between digital components | Detects faults in hard-to-reach areas, high coverage for digital circuits |
Functional Test Fixtures | Simulates actual operating environment of the PCB | Verifies overall functionality and performance in real-world conditions |
Table 1: Comparison of Different PCB Functional Test Types
By understanding the various types of functional tests, their advantages, and the best practices for implementation, manufacturers can ensure the production of high-quality, reliable PCBs that meet the demands of today’s advanced electronic applications.
0 Comments