Introduction to PCB Fabrication and FR4 Semi Flex PCBs
PCB fabrication is the process of creating printed circuit boards (PCBs) that are used in various electronic devices. One specific type of PCB is the FR4 Semi Flex PCB, which combines the rigidity of standard FR4 material with the flexibility of a flexible substrate. This unique combination makes FR4 Semi Flex PCBs suitable for applications that require both stability and flexibility.
What is FR4 Material?
FR4 (Flame Retardant 4) is a common material used in PCB fabrication. It is a composite material made of woven fiberglass cloth with an epoxy resin binder. FR4 is known for its excellent mechanical and electrical properties, making it an ideal choice for many PCB applications.
Property | Value |
---|---|
Dielectric Constant | 4.5 – 4.7 |
Dissipation Factor | 0.02 |
Thermal Conductivity | 0.3 W/mK |
Tensile Strength | 310 MPa |
Flexural Strength | 415 MPa |
Advantages of FR4 Semi Flex PCBs
FR4 Semi Flex PCBs offer several advantages over traditional rigid PCBs:
- Flexibility: The flexible substrate allows the PCB to bend and conform to various shapes, making it suitable for applications with limited space or unique form factors.
- Durability: The combination of rigid FR4 and flexible substrate makes the PCB more durable and resistant to vibrations and shocks.
- Reduced Assembly Time: FR4 Semi Flex PCBs can reduce assembly time by eliminating the need for connectors and cables between rigid sections.
- Improved Signal Integrity: The reduced number of connectors and shorter signal paths in FR4 Semi Flex PCBs can lead to improved signal integrity compared to traditional rigid PCBs with separate flexible sections.
PCB Fabrication Process for FR4 Semi Flex PCBs
The fabrication process for FR4 Semi Flex PCBs is similar to that of standard rigid PCBs, with a few additional steps to incorporate the flexible substrate. The process typically involves the following steps:
1. Design and Layout
The first step in PCB fabrication is designing the circuit and creating the PCB layout using specialized software. The layout must consider the placement of components, routing of traces, and the specific requirements of the FR4 Semi Flex PCB, such as the location and size of the flexible sections.
2. Material Selection and Preparation
Once the design is finalized, the appropriate materials are selected. For FR4 Semi Flex PCBs, this includes the FR4 substrate for the rigid sections and the flexible substrate material, such as polyimide or polyester. The materials are cut to the required sizes and cleaned to remove any contaminants.
3. Lamination
The FR4 and flexible substrates are laminated together using heat and pressure. The lamination process ensures a strong bond between the layers and prevents delamination during the subsequent fabrication steps.
4. Drilling
Holes are drilled through the laminated board to accommodate through-hole components and vias. The drilling process is carefully controlled to ensure the holes are precise and do not damage the flexible sections.
5. Plating and Patterning
The drilled board undergoes a plating process to deposit a thin layer of copper on the hole walls, creating electrical connections between layers. The copper is then patterned using photolithography and etching to form the desired circuit traces. This process is repeated for each layer of the PCB.
6. Solder Mask Application
A solder mask is applied to the outer layers of the PCB to protect the copper traces from oxidation and prevent accidental short circuits during soldering. The solder mask also provides insulation and improves the PCB’s appearance.
7. Surface Finish
A surface finish, such as HASL (Hot Air Solder Leveling), ENIG (Electroless Nickel Immersion Gold), or OSP (Organic Solderability Preservative), is applied to the exposed copper areas to protect them from oxidation and enhance solderability.
8. Silkscreen Printing
Silkscreen printing is used to apply text, logos, and other markings on the PCB surface. This helps with component placement and identification during assembly.
9. Cutting and Profiling
The fabricated panel is cut and profiled to separate individual PCBs and create the desired shape, including the flexible sections. This process requires precision to ensure the flexible sections are not damaged during cutting.
10. Electrical Testing
Each PCB undergoes electrical testing to verify its functionality and ensure that it meets the specified requirements. This includes continuity tests, insulation resistance tests, and other relevant electrical tests.
Challenges in FR4 Semi Flex PCB Fabrication
While FR4 Semi Flex PCBs offer many advantages, their fabrication also presents some challenges:
- Material Compatibility: The different properties of FR4 and flexible substrates can make it challenging to achieve a strong and reliable bond between the layers.
- Dimensional Stability: The flexible sections of the PCB can be prone to dimensional changes during the fabrication process, which can affect the alignment and registration of layers.
- Handling and Processing: FR4 Semi Flex PCBs require special handling and processing techniques to prevent damage to the flexible sections during fabrication and assembly.
- Electrical Performance: The transition between rigid and flexible sections can introduce signal integrity issues if not designed and fabricated properly.
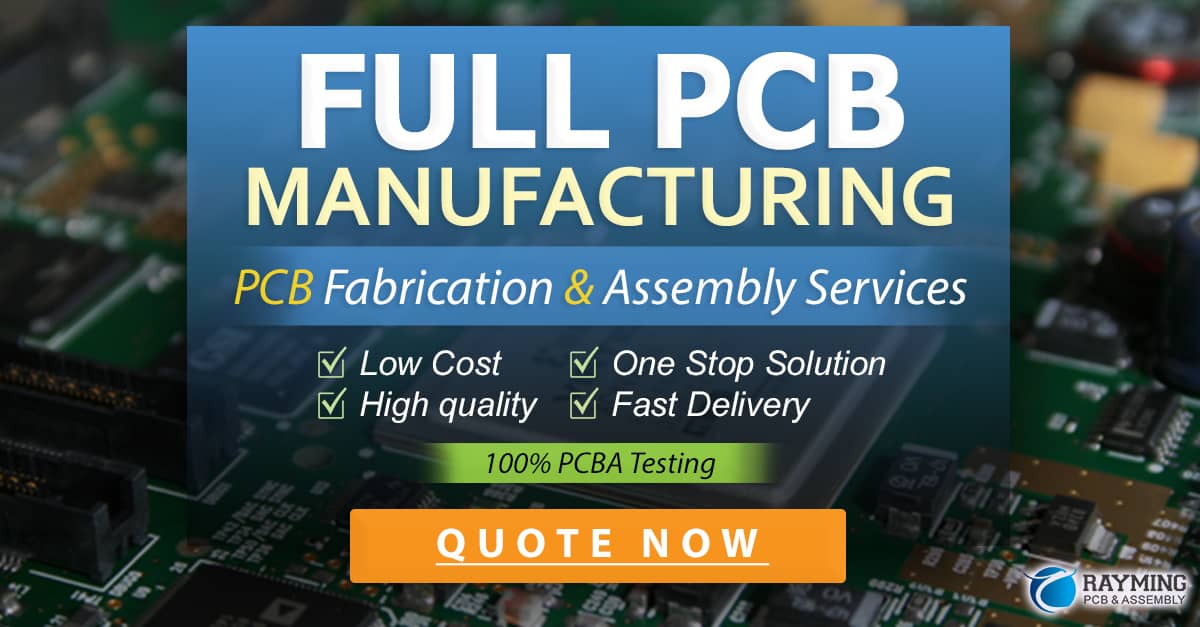
Quality Control and Inspection
To ensure the quality and reliability of FR4 Semi Flex PCBs, strict quality control measures and inspections are implemented throughout the fabrication process. Some common inspection methods include:
- Visual Inspection: PCBs are visually inspected for defects such as scratches, dents, or discoloration.
- Automated Optical Inspection (AOI): AOI systems use cameras and image processing software to detect surface defects and inconsistencies.
- X-Ray Inspection: X-ray systems are used to inspect the internal structure of the PCB, including vias and buried components.
- Microsectioning: Microsectioning involves cutting a small section of the PCB and examining it under a microscope to verify the internal structure and layer alignment.
Applications of FR4 Semi Flex PCBs
FR4 Semi Flex PCBs find applications in various industries and products, including:
- Aerospace and Defense: Avionics systems, satellite communication devices, and military equipment.
- Automotive: In-vehicle infotainment systems, dashboard electronics, and sensor modules.
- Medical Devices: Wearable monitoring systems, implantable devices, and diagnostic equipment.
- Consumer Electronics: Smartphones, tablets, laptops, and wearable devices.
- Industrial Automation: Robotics, machine vision systems, and process control equipment.
Frequently Asked Questions (FAQ)
1. How long does it take to fabricate an FR4 Semi Flex PCB?
The fabrication time for an FR4 Semi Flex PCB depends on various factors, such as the complexity of the design, the number of layers, and the selected surface finish. Typically, the lead time can range from 1-3 weeks, but it may be longer for more complex designs or higher volumes.
2. What is the maximum number of layers possible in an FR4 Semi Flex PCB?
The maximum number of layers in an FR4 Semi Flex PCB is typically limited by the thickness of the flexible substrate and the overall thickness requirements of the application. In general, FR4 Semi Flex PCBs can have up to 20 layers or more, but the number of flexible layers is usually limited to 2-4 layers.
3. Can FR4 Semi Flex PCBs be used in high-temperature environments?
FR4 material is rated for a continuous operating temperature of up to 130°C. However, the temperature rating of an FR4 Semi Flex PCB also depends on the properties of the flexible substrate and other materials used in the fabrication process. It is essential to consult with the PCB manufacturer to determine the temperature rating for a specific FR4 Semi Flex PCB design.
4. How do I choose the right surface finish for my FR4 Semi Flex PCB?
The choice of surface finish depends on several factors, including the intended application, the soldering process, and the environmental conditions. Some common surface finishes for FR4 Semi Flex PCBs include:
- HASL (Hot Air Solder Leveling): Economical and suitable for general-purpose applications.
- ENIG (Electroless Nickel Immersion Gold): Offers excellent solderability and shelf life, making it suitable for high-reliability applications.
- OSP (Organic Solderability Preservative): Provides good solderability and is suitable for applications with short storage requirements.
It is recommended to consult with the PCB manufacturer to determine the most suitable surface finish for your specific application.
5. Can FR4 Semi Flex PCBs be used for high-frequency applications?
FR4 material has a relatively high dielectric constant and dissipation factor, which can limit its performance in high-frequency applications. However, the use of low-loss flexible substrates and careful design techniques can help mitigate these limitations. For high-frequency applications, it is essential to work closely with the PCB manufacturer to optimize the design and material selection for the desired performance.
Conclusion
FR4 Semi Flex PCBs offer a unique combination of rigidity and flexibility, making them suitable for a wide range of applications. The PCB fabrication process for FR4 Semi Flex PCBs involves several steps, including design, material selection, lamination, drilling, plating, patterning, and testing. While the fabrication of FR4 Semi Flex PCBs presents some challenges, careful design, material selection, and process control can help ensure the production of high-quality and reliable PCBs.
As technology continues to advance, the demand for FR4 Semi Flex PCBs is expected to grow, driven by the increasing complexity and miniaturization of electronic devices. By understanding the fabrication process and the advantages of FR4 Semi Flex PCBs, designers and engineers can leverage this technology to create innovative and reliable products across various industries.
0 Comments