Introduction to PCB Equipment
Printed Circuit Board (PCB) manufacturing requires a range of specialized equipment to produce high-quality, reliable boards. From design and prototyping to assembly and testing, each stage of the PCB production process relies on specific tools and machines. In this comprehensive article, we’ll explore the essential PCB equipment used in the industry, discussing their functions, benefits, and key considerations for manufacturers.
PCB Design Software
Computer-Aided Design (CAD) Tools
PCB design begins with the use of Computer-Aided Design (CAD) software. These tools allow engineers to create detailed schematics and layouts for the PCB, specifying component placement, traces, and other critical features. Popular PCB CAD software include:
- Altium Designer
- KiCAD
- Eagle
- OrCAD
- Cadence Allegro
Schematic Capture Tools
Schematic capture tools are used to create the initial electronic schematic of the PCB, representing the interconnections between components. These tools often integrate with PCB layout software to ensure consistency and accuracy throughout the design process. Some well-known schematic capture tools include:
- Altium Designer
- KiCAD
- Eagle
- OrCAD Capture
- Cadence OrCAD
PCB Prototyping Equipment
3D Printers
3D printers have revolutionized PCB prototyping by allowing manufacturers to quickly and cost-effectively create physical models of their designs. These printers can produce PCB enclosures, fixtures, and even functional prototypes using materials like ABS, PLA, and resin.
CNC Machines
Computer Numerical Control (CNC) machines are used for milling and drilling prototype PCBs. These machines offer high precision and repeatability, making them ideal for creating small batches of boards for testing and validation.
Rapid PCB Prototyping Services
Many manufacturers opt for rapid PCB prototyping services, which provide quick turnaround times for prototype boards. These services often use advanced equipment like UV laser imaging and direct imaging systems to produce high-quality prototypes in a matter of days.
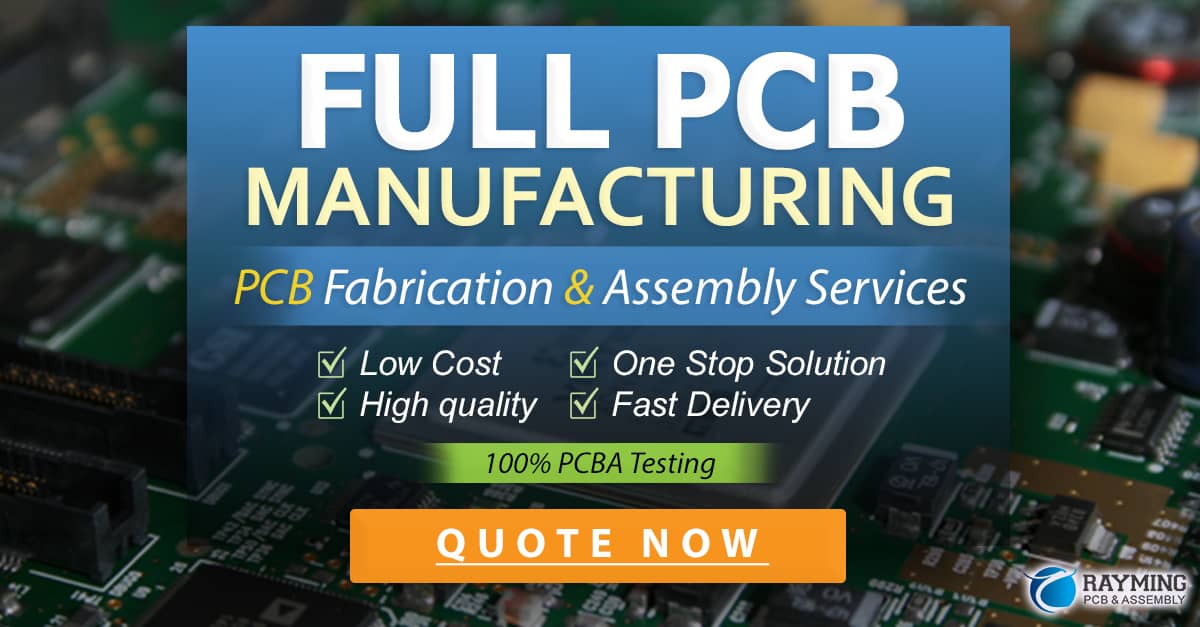
PCB Fabrication Equipment
PCB Material Handling Systems
PCB material handling systems are used to store, transport, and manage the raw materials used in PCB production, such as copper-clad laminates, prepregs, and solder masks. These systems ensure efficient material flow and minimize the risk of damage or contamination.
Drilling Machines
PCB Drilling machines create the holes required for component leads and vias. These machines use high-speed spindles and precise positioning systems to drill holes with diameters ranging from 0.1mm to 6.35mm. The two main types of PCB drilling machines are:
- Mechanical Drilling Machines
- Laser Drilling Machines
Machine Type | Advantages | Disadvantages |
---|---|---|
Mechanical Drilling | – Lower cost – Suitable for larger hole sizes |
– Slower than laser drilling – Limited hole size range |
Laser Drilling | – High speed and precision – Able to drill smaller holes |
– Higher cost – Limited material compatibility |
Plating and Etching Equipment
Plating and etching equipment are used to create the conductive traces and pads on the PCB. The most common processes are:
- Electroless and Electrolytic Plating: Deposits a thin layer of copper onto the PCB surface and drilled holes.
- Panel Plating: Plates the entire PCB panel with copper, tin, or other metals for improved conductivity and solderability.
- Etching: Removes unwanted copper from the PCB surface, leaving only the desired traces and pads.
Process | Purpose |
---|---|
Electroless Plating | Creates a thin, uniform copper layer on the PCB surface and drilled holes |
Electrolytic Plating | Increases the thickness of the copper layer for improved conductivity |
Panel Plating | Plates the entire PCB panel with a specific metal for enhanced performance |
Etching | Removes unwanted copper, creating the desired traces and pads |
Solder Mask Application Equipment
Solder mask application equipment applies a protective coating to the PCB surface, leaving only the exposed pads and contact points. This coating helps prevent solder bridges and short circuits during the assembly process. The two primary methods for applying solder mask are:
- Screen Printing: Uses a mesh screen to apply the solder mask ink to the PCB surface.
- Photoimaging: Uses a photosensitive solder mask and UV exposure to create the desired pattern.
Method | Advantages | Disadvantages |
---|---|---|
Screen Printing | – Lower cost – Faster setup times |
– Lower resolution – Limited feature size |
Photoimaging | – High resolution and accuracy – Smaller feature sizes possible |
– Higher cost – Longer setup times |
Legend Printing Equipment
Legend printing equipment applies the component identifiers, logos, and other markings to the PCB surface. The most common methods for legend printing are:
- Screen Printing: Similar to solder mask screen printing, but using ink instead of solder mask.
- Ink-Jet Printing: Uses a digital inkjet printer to apply the legend directly to the PCB surface.
- Laser Marking: Uses a laser to etch the legend onto the PCB surface.
PCB Assembly Equipment
Pick-and-Place Machines
Pick-and-place machines automatically place surface-mount components onto the PCB. These machines use computer vision and precise placement heads to accurately position components at high speeds. Some advanced pick-and-place machines can place over 100,000 components per hour.
Reflow Soldering Equipment
Reflow soldering equipment is used to solder surface-mount components to the PCB. The PCB is heated in a controlled manner, causing the solder paste to melt and form a strong bond between the components and the board. The two main types of reflow soldering equipment are:
- Convection Reflow Ovens: Uses hot air convection to heat the PCB and melt the solder paste.
- Vapor Phase Reflow Systems: Uses a heated vapor to melt the solder paste, providing a more uniform heating process.
Equipment Type | Advantages | Disadvantages |
---|---|---|
Convection Reflow Ovens | – Lower cost – Suitable for most PCB types |
– Potential for uneven heating – Slower than vapor phase |
Vapor Phase Reflow Systems | – Uniform heating – Faster process |
– Higher cost – Limited PCB size range |
Wave Soldering Machines
Wave soldering machines are used to solder through-hole components to the PCB. The board is passed over a wave of molten solder, which flows into the through-holes and creates a strong bond between the components and the board.
Selective Soldering Systems
Selective soldering systems are used for soldering specific components or areas on the PCB that cannot be easily soldered using reflow or wave soldering techniques. These systems use a focused solder nozzle or laser to apply solder to the desired locations.
PCB Testing and Inspection Equipment
Automated Optical Inspection (AOI) Systems
Automated Optical Inspection (AOI) systems use computer vision to inspect the PCB for manufacturing defects, such as missing components, solder bridges, or incorrect component placement. AOI systems can quickly identify problems and provide valuable data for process improvement.
X-Ray Inspection Systems
X-ray inspection systems use x-ray imaging to inspect solder joints and other hidden features on the PCB. These systems are particularly useful for examining ball grid array (BGA) and other high-density component packages.
In-Circuit Test (ICT) Equipment
In-Circuit Test (ICT) equipment is used to test the PCB for electrical continuity and component functionality. ICT systems use a bed-of-nails fixture to make contact with the PCB and perform a series of electrical tests to ensure the board is functioning correctly.
Flying Probe Testers
Flying probe testers are an alternative to ICT systems, using moving probes to test the PCB instead of a fixed bed-of-nails fixture. Flying probe testers offer greater flexibility and can be used for testing prototype or low-volume PCBs.
FAQ
1. What is the most important piece of equipment in PCB manufacturing?
It is difficult to pinpoint a single most important piece of equipment, as each stage of the PCB manufacturing process relies on specific tools and machines. However, pick-and-place machines and reflow soldering equipment are often considered the most critical for the assembly process, as they directly impact the quality and reliability of the final product.
2. How much does PCB manufacturing equipment cost?
The cost of PCB manufacturing equipment varies widely depending on the type of equipment, its features, and the manufacturer. Entry-level machines can cost a few thousand dollars, while high-end, fully automated systems can cost several million dollars. It is essential to consider your production needs and budget when selecting PCB manufacturing equipment.
3. Can I manufacture PCBs without investing in expensive equipment?
Yes, it is possible to manufacture PCBs without investing in expensive equipment by outsourcing the production to a PCB fabrication and assembly service provider. Many companies offer a range of services, from prototype to high-volume production, allowing you to benefit from their expertise and equipment without the need for significant capital investment.
4. What should I consider when selecting PCB manufacturing equipment?
When selecting PCB manufacturing equipment, consider factors such as:
- Production volume and throughput requirements
- PCB complexity and component types
- Equipment accuracy, precision, and repeatability
- Ease of use and maintenance
- Integration with existing systems and processes
- Total cost of ownership, including purchase price, operating costs, and maintenance expenses
5. How can I ensure the longevity and reliability of my PCB manufacturing equipment?
To ensure the longevity and reliability of your PCB manufacturing equipment, follow these best practices:
- Perform regular maintenance and calibration according to the manufacturer’s guidelines
- Train operators on proper equipment use and handling
- Use high-quality consumables and spare parts
- Monitor equipment performance and address any issues promptly
- Keep equipment clean and store it in a controlled environment when not in use
- Plan for upgrades and replacements as technology advances and your production needs change
Conclusion
PCB manufacturing requires a wide range of specialized equipment to produce high-quality, reliable boards. From design software and prototyping tools to fabrication, assembly, and testing equipment, each stage of the production process relies on specific machines and technologies. By understanding the functions and benefits of these essential tools, manufacturers can make informed decisions when selecting equipment for their production needs.
Investing in the right PCB manufacturing equipment is crucial for ensuring product quality, efficiency, and profitability. However, it is equally important to consider factors such as production volume, PCB complexity, and total cost of ownership when making equipment purchases. By carefully evaluating your requirements and working with reputable equipment suppliers, you can build a robust and reliable PCB manufacturing process that meets your business goals.
0 Comments