Types of PCB Conveyors
There are several types of PCB conveyors available, each with its own unique features and benefits. Here are some of the most common types:
Belt Conveyors
Belt conveyors are the most widely used type of PCB conveyor. They consist of a continuous belt that moves PCBs along a predetermined path. The belts can be made from various materials, such as PVC, polyurethane, or rubber, depending on the specific requirements of the application.
Advantages of belt conveyors include:
– Smooth and consistent motion
– Ability to handle a wide range of PCB sizes and shapes
– Easy to maintain and replace belts
– Cost-effective solution for most applications
Roller Conveyors
Roller conveyors use a series of rollers to transport PCBs. The rollers can be driven by a motor or can be gravity-fed, depending on the system design. Roller conveyors are ideal for applications that require gentle handling of PCBs or for transporting larger, heavier boards.
Advantages of roller conveyors include:
– Gentle handling of PCBs
– Ability to handle larger and heavier boards
– Reduced friction compared to belt conveyors
– Easy to maintain and replace rollers
Chain Conveyors
Chain conveyors use a series of interconnected chains to move PCBs along a predetermined path. These conveyors are known for their durability and ability to handle high loads, making them suitable for demanding applications or harsh environments.
Advantages of chain conveyors include:
– High load capacity
– Durability in harsh environments
– Ability to transport PCBs over long distances
– Customizable chain configurations for specific applications
Overhead Conveyors
Overhead conveyors transport PCBs suspended from an overhead track or rail system. This type of conveyor is ideal for applications where floor space is limited or when PCBs need to be transported between different levels or workstations.
Advantages of overhead conveyors include:
– Efficient use of vertical space
– Ability to transport PCBs between different levels or workstations
– Reduced risk of damage due to suspended transport
– Customizable track configurations for specific layouts
PCB Handling Systems
In addition to conveyors, various PCB handling systems are used to facilitate the movement and manipulation of boards throughout the manufacturing process. Some common PCB handling systems include:
PCB Magazines and Racks
PCB magazines and racks are used to store and transport PCBs between different stages of the production process. These systems can be static or mobile and are designed to protect boards from damage during handling and storage.
PCB Loaders and Unloaders
PCB loaders and unloaders are automated systems that transfer PCBs between conveyors, magazines, or racks. These systems help to streamline the production process and reduce the risk of human error or damage to the boards.
PCB Manipulators and Flippers
PCB manipulators and flippers are used to rotate, flip, or otherwise manipulate PCBs during the manufacturing process. These systems are essential for applications that require access to both sides of the board, such as double-sided assembly or inspection.
Benefits of PCB Conveyors and Handling Systems
Implementing PCB conveyors and handling systems in your manufacturing process offers several key benefits:
-
Increased Efficiency: Automated conveyors and handling systems streamline the production process, reducing manual handling and minimizing bottlenecks.
-
Improved Quality: Consistent and gentle handling of PCBs reduces the risk of damage, leading to higher quality end products.
-
Enhanced Safety: Automated systems minimize the need for manual handling, reducing the risk of worker injuries related to repetitive strain or accidents.
-
Space Optimization: Overhead conveyors and compact handling systems help to optimize floor space, allowing for more efficient use of the production area.
-
Scalability: Modular conveyor and handling systems can be easily expanded or reconfigured to accommodate changes in production volume or product mix.
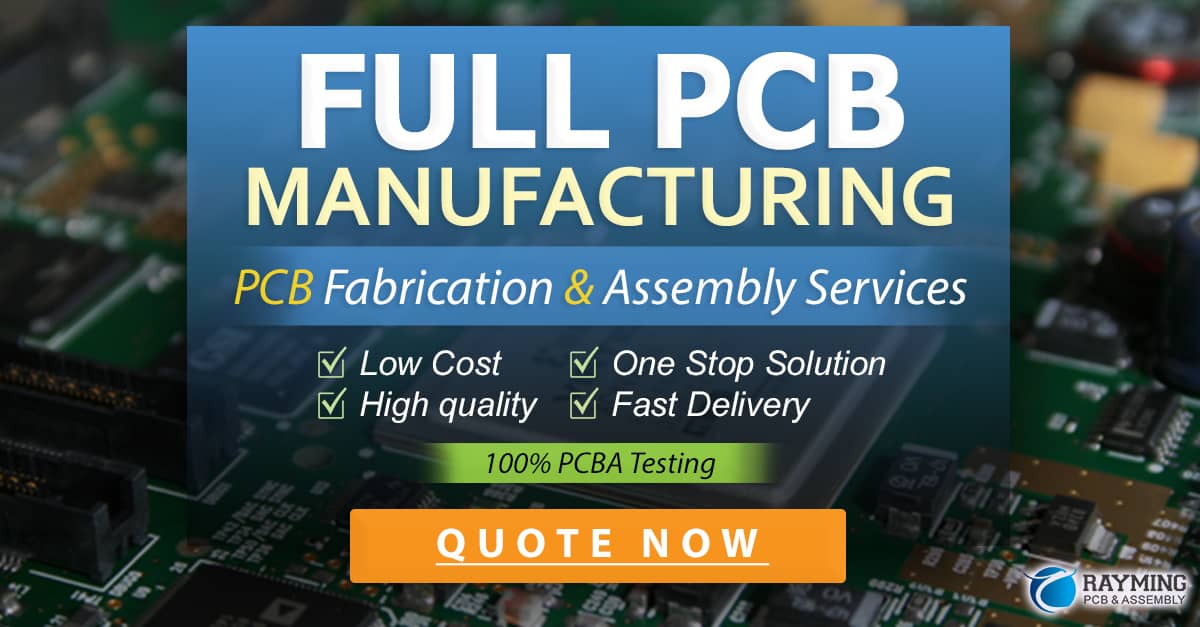
Key Considerations for Selecting PCB Conveyors and Handling Systems
When choosing PCB conveyors and handling systems for your manufacturing process, consider the following factors:
-
PCB Size and Weight: Ensure that the selected system can accommodate the dimensions and weight of your PCBs.
-
Production Volume: Choose a system that can handle your current production volume and has the capacity to scale up as your business grows.
-
Facility Layout: Consider the available floor space and layout of your production area when selecting conveyors and handling systems.
-
Integration with Existing Equipment: Ensure that the new system can seamlessly integrate with your existing manufacturing equipment and processes.
-
Maintenance and Support: Select a vendor that offers comprehensive maintenance and support services to minimize downtime and ensure optimal system performance.
Frequently Asked Questions (FAQ)
1. What is the difference between a belt conveyor and a roller conveyor?
Belt conveyors use a continuous belt to transport PCBs, while roller conveyors use a series of rollers. Belt conveyors offer smooth and consistent motion, while roller conveyors provide gentle handling and are suitable for larger, heavier boards.
2. Can PCB conveyors be customized to fit my specific manufacturing needs?
Yes, most PCB conveyor systems can be customized to meet specific requirements, such as unique layouts, special handling needs, or integration with existing equipment.
3. How do I determine the best type of PCB conveyor for my production process?
The best type of PCB conveyor depends on factors such as PCB size and weight, production volume, facility layout, and specific handling requirements. Consult with a conveyor specialist or vendor to determine the most suitable solution for your needs.
4. What maintenance is required for PCB conveyors and handling systems?
Regular maintenance for PCB conveyors and handling systems typically includes lubrication, belt or chain tension adjustment, and inspection for wear or damage. Refer to the manufacturer’s guidelines for specific maintenance recommendations.
5. How can I ensure the safe handling of PCBs during the manufacturing process?
To ensure safe PCB handling, implement automated conveyor and handling systems that minimize manual handling, use appropriate PCB magazines and racks for storage and transport, and train employees on proper handling techniques and safety protocols.
Type of Conveyor | Advantages |
---|---|
Belt Conveyor | – Smooth and consistent motion |
– Handles wide range of PCB sizes and shapes | |
– Easy to maintain and replace belts | |
– Cost-effective for most applications | |
Roller Conveyor | – Gentle handling of PCBs |
– Handles larger and heavier boards | |
– Reduced friction compared to belt conveyors | |
– Easy to maintain and replace rollers | |
Chain Conveyor | – High load capacity |
– Durable in harsh environments | |
– Transports PCBs over long distances | |
– Customizable chain configurations | |
Overhead Conveyor | – Efficient use of vertical space |
– Transports PCBs between different levels or workstations | |
– Reduced risk of damage due to suspended transport | |
– Customizable track configurations |
In conclusion, PCB conveyors and handling systems play a crucial role in optimizing electronics manufacturing processes. By understanding the different types of conveyors and handling systems available, their benefits, and key considerations for selection, manufacturers can make informed decisions when implementing these solutions in their production lines. Investing in the right PCB conveyor and handling system can lead to increased efficiency, improved product quality, enhanced safety, and ultimately, a more competitive position in the market.
0 Comments