Introduction to PCB Contract Manufacturing
Printed circuit board (PCB) manufacturing is an essential part of bringing electronic products to market. A PCB provides the foundation on which components like integrated circuits and connectors are mounted. While some companies manufacture PCBs in-house, many choose to work with a contract manufacturer for reasons of cost, quality, and flexibility.
PCB contract manufacturing refers to outsourcing the production of printed circuit boards to a specialized provider. The contract manufacturer is responsible for fabricating the boards according to the customer’s specifications. This allows the customer to focus on their core competencies like design and marketing while leaving PCB fabrication to experts.
This guide provides a comprehensive overview of PCB contract manufacturing, including its advantages and disadvantages, the steps in the process, key factors to consider when choosing a manufacturer, and tips for building an effective relationship.
Benefits of Using a Contract Manufacturer
There are several compelling reasons to outsource PCB production rather than manufacture boards in-house:
Cost Savings
Contract manufacturers achieve economies of scale by aggregating orders across customers. Their expertise also leads to efficiency gains. This results in lower per-unit costs compared to in-house production.
Specialized Equipment and Skills
PCB fabrication requires significant capital investment in equipment like etching and drilling machines. It also needs staff with specialized skills in process engineering. Outsourcing avoids these expenditures.
Quality and Reliability
Leading contract manufacturers adhere to rigorous quality control standards and are ISO certified. This results in high-reliability boards.
Flexibility and Speed
Contract manufacturers maintain excess production capacity to accommodate rush orders and fluctuations in demand. This provides flexibility that is difficult to achieve in-house.
Focus on Core Competency
Outsourcing PCB fabrication allows a company to direct more resources towards its true core competency like firmware development or product design.
While cost savings is a major driver, the other benefits like quality, flexibility, and focus on competency are also compelling reasons to use a contract manufacturer.
The PCB Contract Manufacturing Process
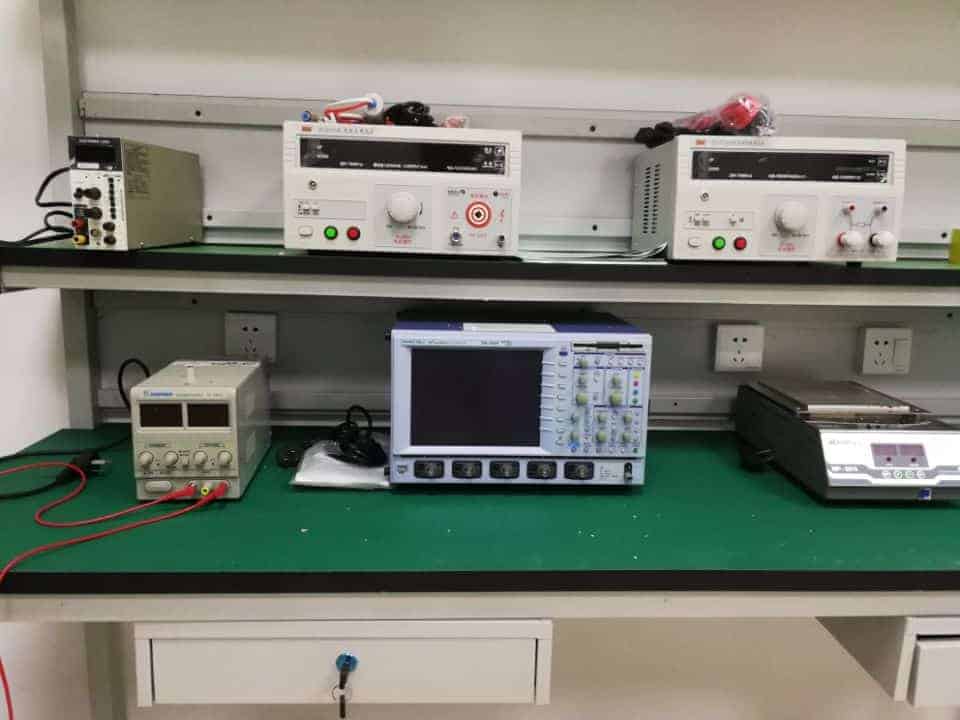
The typical process for taking a printed circuit board from initial concept to volume production with a contract manufacturer involves several key steps:
1. Design
The customer creates circuit schematics and PCB layouts using CAD software. For complex boards, a physical prototype may be produced and tested first. The deliverables to the manufacturer include Gerber files, drill files, and a bill of materials specifying components.
2. Prototyping
The contract manufacturer produces a small number of prototype boards for design verification and testing. This may involve multiple iterations to fix issues like trace clearance violations.
3. Fabrication Engineering
The manufacturer’s engineers analyze the board design and specify the optimal processes and material types. This includes decisions like number of layers, board thickness, and surface finishes.
4. Fabrication
Production boards are fabricated using processes like lithography, chemical etching, lamination, drilling, and plating. Automated optical inspection checks for defects.
5. Assembly
Components are soldered onto the boards either manually or by pick-and-place machines. More complex parts may require prior solder paste application.
6. Testing
Each board undergoes electrical tests for continuity, resistivity, and functionality. Automated test fixtures improve efficiency.
7. Delivery
The finished boards are shipped to the customer’s facility. Reputable manufacturers provide anti-static packing along with comprehensive documentation.
While prototyping often uses standard processes, fabrication engineering aims to optimize the production boards for cost, manufacturability, and performance. Testing ensures each board meets specifications before shipment.
Choosing a PCB Contract Manufacturer
Selecting the right contract manufacturer is crucial for getting high-quality boards delivered on time and within budget. Here are key factors to consider during selection:
Capability
- Range of board technologies supported (multilayer, HDI, flex/rigid)
- Available board materials like FR-4, Rogers, ceramic
- Minimum/maximum board dimensions
- Soldermask and finish options
- Certifications like ISO, IPC, ITAR
Capacity
- Monthly manufacturing capacity
- Facility locations and their capabilities
- Ability to handle fluctuating demand
- Experience with high-volume production
Quality
- defect rates
- quality certifications
- quality control procedures
- AOI, test and inspection equipment
- employee training procedures
Services
- Design for manufacturability analysis
- prototyping services
- procurement and management of components
- handling of counterfeit components
- testing services
- logistic and shipping capabilities
Cost
- Pricing model (per unit, per panel)
- Minimum order quantities
- Cost reduction capabilities over time
- Payment terms
Customer Service
- Ease of communication
- Responsiveness to requests and issues
- Ability to support interactive design process
- Experience supporting similar customers
Capabilities, quality, and services are leading indicators of the manufacturer’s expertise and long-term compatibility. Assessing capacity gives insight into their ability to meet fluctuating demand. Finally, cost and customer service impact budget and overall experience. Visiting the facility helps verify promoted capabilities.
Building an Effective Manufacturer Relationship

A productive working relationship between customer and contract manufacturer is essential for manufacturing success. Here are some tips:
- Involve manufacturing early – Get input during schematic design to avoid manufacturability issues later.
- Communicate effectively – Clearly convey requirements and be responsive to manufacturer requests.
- Build trust – Start with lower-risk production to establish a track record.
- Plan for scaling – Forecast demand so manufacturer can allocate capacity.
- Allow time for iterations – Leave room in schedule for potential prototype respins.
- Monitor quality – Audit processes and inspect deliveries but avoid micromanaging.
- Negotiate win-win deals – Seek reasonable pricing but avoid over-optimizing on cost alone.
- Protect IP – Use NDAs and limit access to proprietary information.
- Resolve issues professionally – Collaborate on solutions rather than assigning blame.
Fostering an environment of trust, transparency, and mutual benefit establishes the foundation for a lasting partnership. Both parties should see the relationship as strategic rather than transactional.
Pros and Cons of Contract Manufacturing
While there are many benefits, outsourcing PCB fabrication also comes with some downsides to consider:
Pros
- Lower costs
- Access to specialized expertise and equipment
- High quality through process maturity
- Increased flexibility in production capacity
- Faster time to market
- Allows focus on core competencies
Cons
- Longer feedback loops vs. in-house
- Exposure to supply chain risks
- Lower control over IP and quality
- Communications more difficult across time zones
- Potential for disputes on accountability
The relative importance of the pros and cons depends on the specific company’s situation. For example, startups may value fast time to market and flexibility more than incumbents. Weighing the trade-offs allows selecting an optimal electronics manufacturing strategy.
Conclusion
Contract manufacturing provides compelling advantages in cost, quality, flexibility, and time-to-market for PCB fabrication. However, finding the right partner and building an effective relationship is crucial to realizing those benefits in full. This requires carefully evaluating manufacturers based on their capabilities, capacity, cost, and commitment to customer service. With a data-driven selection process and a spirit of trust and collaboration, companies can leverage outsourcing to focus their resources on the most impactful product innovations.
Frequently Asked Questions
What are the typical steps in the PCB manufacturing process?
The major steps are design, prototyping, fabrication engineering, board fabrication, assembly, testing, and delivery. The process often involves multiple iterations of prototyping and testing before moving to high volume fabrication.
Should I use a US or overseas PCB manufacturer?
Overseas manufacturers, especially in China, offer lower costs while US manufacturers provide proximity for better communication and control. Factors like volume requirements, cost sensitivity, IP protection needs, and ability to travel for in-person reviews help determine the ideal location.
How can I estimate PCB fabrication costs?
Key drivers are board layer count, materials, size, volume, and lead time. Use online quoting tools or request sample quotes from multiple manufacturers to estimate costs. Expect more comprehensive pricing after the manufacturer reviews full specifications.
What are some key certifications held by reputable PCB manufacturers?
Leading manufacturers are certified to standards like ISO 9001 for quality management and ISO 14001 for environmental management. They also comply with industry standards like IPC and ITAR.
How can I protect my intellectual property when outsourcing manufacturing?
Use NDAs, limit communication to essential information, and monitor who has access to designs. Overseas providers in countries with weaker IP laws present greater risks. Splitting work across multiple vendors provides additional protection.
0 Comments