Introduction to WLCSP-PCB
Wafer-Level Chip Scale Package (WLCSP) is an advanced packaging technology that has gained significant popularity in the electronics industry due to its compact size, high performance, and cost-effectiveness. WLCSP-PCB refers to the integration of WLCSP components onto a printed circuit board (PCB). This article will explore the world of PCB Assembly service providers and their capabilities in handling WLCSP packages.
What is WLCSP?
WLCSP is a packaging technology where the entire wafer is packaged and tested before being singulated into individual chips. The package size is essentially the same as the die size, making it one of the smallest form factors available. WLCSP eliminates the need for traditional packaging materials, such as wire bonding and substrate, resulting in a more compact and lightweight package.
Parameter | WLCSP | Traditional Packaging |
---|---|---|
Package Size | Same as die size | Larger than die size |
Packaging Materials | None | Wire bonding, substrate |
Cost | Lower | Higher |
Performance | High | Lower |
Advantages of WLCSP-PCB
- Miniaturization: WLCSP allows for the creation of extremely small packages, enabling the development of miniaturized electronic devices.
- Improved Performance: The direct connection between the die and the PCB reduces parasitic inductance and capacitance, resulting in improved electrical performance.
- Cost Reduction: WLCSP eliminates the need for additional packaging materials and processes, leading to lower manufacturing costs.
- Enhanced Reliability: The absence of wire bonds and other interconnects in WLCSP reduces the potential for failure points, improving overall reliability.
PCB Assembly Service Providers
Capabilities and Expertise
PCB assembly service providers play a crucial role in the successful integration of WLCSP components onto PCBs. These providers possess the necessary expertise, equipment, and processes to handle the unique challenges associated with WLCSP-PCB assembly.
Equipment and Processes
- Pick and Place Machines: Advanced pick and place machines with high precision and accuracy are essential for handling the tiny WLCSP components.
- Solder Paste Printing: Specialized solder paste printing techniques, such as stencil printing or jet printing, are employed to ensure precise solder paste deposition on the PCB pads.
- Reflow Soldering: Optimized reflow soldering profiles are used to achieve reliable solder joints between the WLCSP components and the PCB.
- Inspection and Testing: Automated optical inspection (AOI) and X-ray inspection are used to verify the quality of the solder joints and detect any defects.
Design Support and Optimization
PCB assembly service providers often offer design support and optimization services to ensure the successful integration of WLCSP components. They work closely with customers to review and optimize PCB layouts, considering factors such as pad size, pitch, and solder mask openings.
Qualification and Certification
When selecting a PCB assembly service provider for WLCSP-PCB projects, it is crucial to consider their qualifications and certifications. Some key certifications to look for include:
- ISO 9001: Quality management system certification
- IPC-A-610: Acceptability of electronic assemblies standard
- J-STD-001: Requirements for soldered electrical and electronic assemblies
- IPC-7093: Guidelines for design and assembly process implementation for bottom termination components
These certifications demonstrate a provider’s commitment to quality, reliability, and adherence to industry standards.
WLCSP-PCB Design Considerations
Pad Size and Pitch
One of the critical design considerations for WLCSP-PCB is the pad size and pitch. WLCSP components typically have a fine pitch, ranging from 0.3mm to 0.5mm. The PCB pads must be designed to match the size and pitch of the WLCSP bumps accurately. Proper pad size and pitch ensure reliable solder joint formation and prevent short circuits or open connections.
Solder Mask Openings
Solder mask openings play a vital role in the assembly of WLCSP-PCB. The openings should be designed to expose the pads adequately while providing sufficient clearance for solder paste deposition and reflow. Improper solder mask openings can lead to solder bridging or insufficient solder joint formation.
Thermal Management
WLCSP components generate significant heat due to their high power density. Effective thermal management is crucial to ensure reliable operation and prevent thermal-induced failures. PCB designers must incorporate appropriate thermal dissipation techniques, such as thermal vias, heatsinks, or thermal interface materials, to manage the heat generated by WLCSP components effectively.
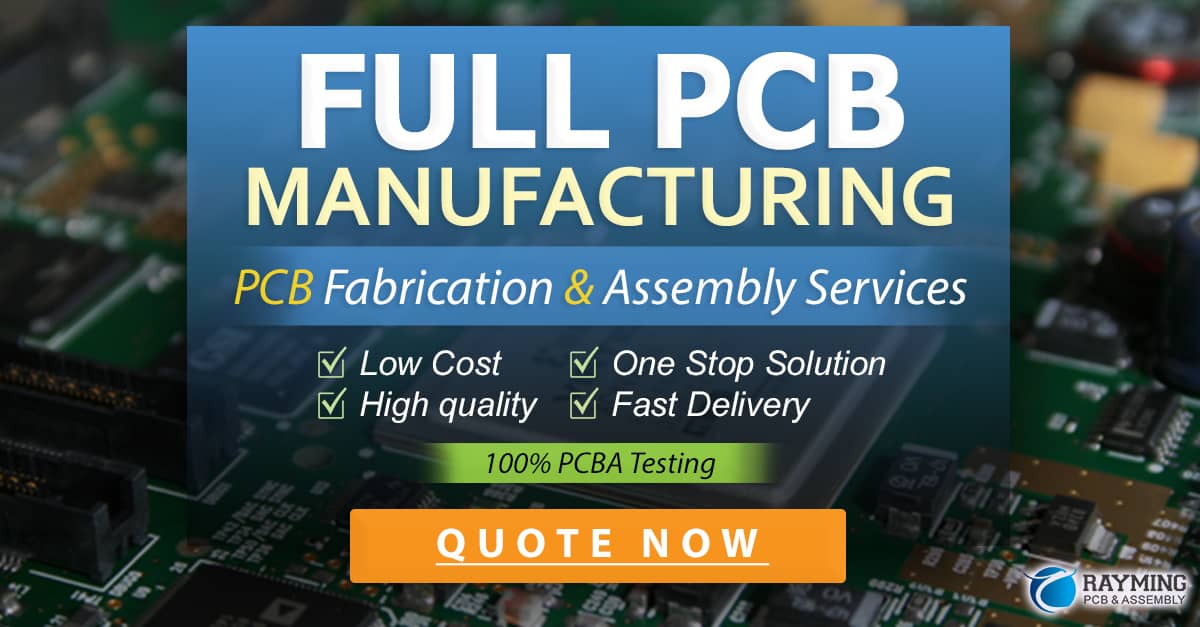
Assembly Process Flow
Solder Paste Printing
The assembly process for WLCSP-PCB begins with solder paste printing. Specialized stencils or jet printing techniques are used to deposit solder paste onto the PCB pads accurately. The solder paste volume and consistency must be carefully controlled to ensure optimal solder joint formation.
Component Placement
After solder paste printing, the WLCSP components are placed onto the PCB using high-precision pick and place machines. The machines must be programmed with the correct placement coordinates and orientation to ensure accurate positioning of the components.
Reflow Soldering
Once the components are placed, the PCB undergoes reflow soldering. The reflow profile must be optimized for WLCSP components, considering factors such as peak temperature, ramp rate, and dwell time. Proper reflow soldering ensures the formation of reliable solder joints between the WLCSP bumps and the PCB pads.
Inspection and Testing
After reflow soldering, the PCB undergoes inspection and testing to verify the quality of the assembly. Automated optical inspection (AOI) is used to detect any visible defects, such as solder bridging or component misalignment. X-ray inspection is employed to assess the quality of the solder joints, particularly for hidden or obscured connections. Electrical testing is also performed to ensure the functionality and performance of the assembled WLCSP-PCB.
Challenges and Solutions
Warpage Control
One of the challenges associated with WLCSP-PCB assembly is warpage control. Due to the thin nature of the WLCSP components and the PCB, warpage can occur during the reflow process. Warpage can lead to misalignment, open connections, or solder bridging. To mitigate warpage, PCB assembly service providers employ techniques such as optimized reflow profiles, specialized fixtures, or vacuum assisted soldering.
Underfill Application
Underfill is often used in WLCSP-PCB assembly to enhance the reliability and mechanical strength of the solder joints. The underfill material fills the gap between the WLCSP component and the PCB, providing additional support and protection against thermal and mechanical stresses. However, applying underfill uniformly and without voids can be challenging. PCB assembly service providers use specialized dispensing equipment and optimized process parameters to ensure proper underfill application.
Rework and Repair
Reworking or repairing WLCSP-PCB assemblies can be challenging due to the small size and delicate nature of the components. Specialized rework equipment and techniques are required to remove and replace WLCSP components without damaging the PCB or neighboring components. PCB assembly service providers invest in advanced rework systems and train their technicians to handle WLCSP rework and repair effectively.
FAQ
-
Q: What is the typical pitch of WLCSP components?
A: The typical pitch of WLCSP components ranges from 0.3mm to 0.5mm. -
Q: Can WLCSP components be reworked or repaired?
A: Yes, WLCSP components can be reworked or repaired, but it requires specialized equipment and techniques due to their small size and delicate nature. -
Q: What are the benefits of using WLCSP-PCB?
A: The benefits of using WLCSP-PCB include miniaturization, improved performance, cost reduction, and enhanced reliability. -
Q: How is thermal management addressed in WLCSP-PCB design?
A: Thermal management in WLCSP-PCB design is addressed through techniques such as thermal vias, heatsinks, or thermal interface materials to effectively dissipate the heat generated by WLCSP components. -
Q: What certifications should I look for when selecting a PCB assembly service provider for WLCSP-PCB?
A: When selecting a PCB assembly service provider for WLCSP-PCB, look for certifications such as ISO 9001, IPC-A-610, J-STD-001, and IPC-7093, which demonstrate their commitment to quality and adherence to industry standards.
Conclusion
WLCSP-PCB assembly presents unique challenges and opportunities for PCB assembly service providers. With the increasing demand for miniaturized and high-performance electronic devices, the adoption of WLCSP technology is expected to grow significantly. PCB assembly service providers play a crucial role in enabling the successful integration of WLCSP components onto PCBs.
By investing in advanced equipment, processes, and expertise, PCB assembly service providers can overcome the challenges associated with WLCSP-PCB assembly, such as warpage control, underfill application, and rework/repair. They offer comprehensive services, including design support, assembly, inspection, and testing, to ensure the reliability and functionality of WLCSP-PCB assemblies.
When selecting a PCB assembly service provider for WLCSP-PCB projects, it is essential to consider their capabilities, qualifications, and certifications. Partnering with an experienced and reputable provider can help navigate the complexities of WLCSP-PCB assembly and achieve successful outcomes.
As the electronics industry continues to push the boundaries of miniaturization and performance, WLCSP-PCB technology will undoubtedly play a significant role in shaping the future of electronic packaging. PCB assembly service providers will remain at the forefront of this evolution, enabling the realization of innovative and cutting-edge electronic devices.
0 Comments