Introduction to PCB Assembly and QFN Packages
Printed Circuit Board (PCB) assembly is a crucial process in the electronics manufacturing industry. It involves the placement and soldering of various electronic components onto a PCB to create a functional electronic device. One of the popular package types used in PCB assembly is the Quad Flat No-lead (QFN) package. QFN packages offer several advantages, such as reduced size, improved thermal performance, and lower cost compared to other package types.
In this article, we will explore PCB assembly service providers that specialize in handling QFN packages. We will discuss the challenges associated with QFN assembly, the importance of choosing the right service provider, and the factors to consider when selecting a PCB assembly partner for your QFN projects.
Understanding QFN Packages
What is a QFN Package?
A QFN package is a surface-mount technology (SMT) package that has no leads extending from the package body. Instead, the electrical connections are made through pads on the bottom surface of the package. QFN packages are known for their compact size, low profile, and excellent thermal and electrical performance.
Advantages of QFN Packages
- Smaller footprint: QFN packages have a smaller footprint compared to other package types, allowing for higher component density on the PCB.
- Improved thermal performance: The exposed pad on the bottom of the QFN package provides efficient heat dissipation, enhancing the thermal performance of the device.
- Lower cost: QFN packages are generally less expensive than other package types due to their simpler design and manufacturing process.
- Better electrical performance: The shorter lead lengths in QFN packages result in reduced parasitic inductance and capacitance, improving the overall electrical performance.
Challenges in QFN Assembly
Despite the benefits of QFN packages, they present certain challenges during the PCB assembly process:
- Thermal management: Proper thermal management is crucial to ensure the reliability and performance of QFN devices. Inadequate heat dissipation can lead to device failure.
- Solder joint reliability: The small size and close proximity of the pads in QFN packages require precise solder paste deposition and reflow profile control to achieve reliable solder joints.
- Inspection difficulties: The lack of visible leads in QFN packages makes visual inspection of solder joints challenging. Specialized inspection techniques, such as X-ray inspection, may be necessary.
Choosing the Right PCB Assembly Service Provider for QFN Packages
Factors to Consider
When selecting a PCB assembly service provider for your QFN projects, consider the following factors:
- Experience and expertise: Look for a service provider with extensive experience in handling QFN packages and a proven track record of successful projects.
- Equipment and technology: Ensure that the service provider has the necessary equipment and technology to handle QFN assembly, such as high-precision placement machines, reflow ovens with tight profile control, and advanced inspection systems.
- Quality control processes: Inquire about the service provider’s quality control processes, including incoming material inspection, process monitoring, and final product testing.
- Design support: A good service provider should offer design support to optimize your PCB layout for QFN assembly, considering factors such as pad size, solder mask opening, and thermal relief design.
- Scalability and flexibility: Choose a service provider that can accommodate your production volume requirements and offer flexibility in terms of lead times and order quantities.
Questions to Ask PCB Assembly Service Providers
When evaluating potential PCB assembly service providers for your QFN projects, ask the following questions:
- What is your experience with QFN package assembly?
- What equipment and technology do you use for QFN assembly?
- How do you ensure the reliability of solder joints in QFN packages?
- What inspection methods do you employ for QFN assemblies?
- Can you provide design support to optimize my PCB layout for QFN assembly?
- What are your quality control processes, and how do you handle defects or issues?
- What are your lead times and minimum order quantities for QFN assembly projects?
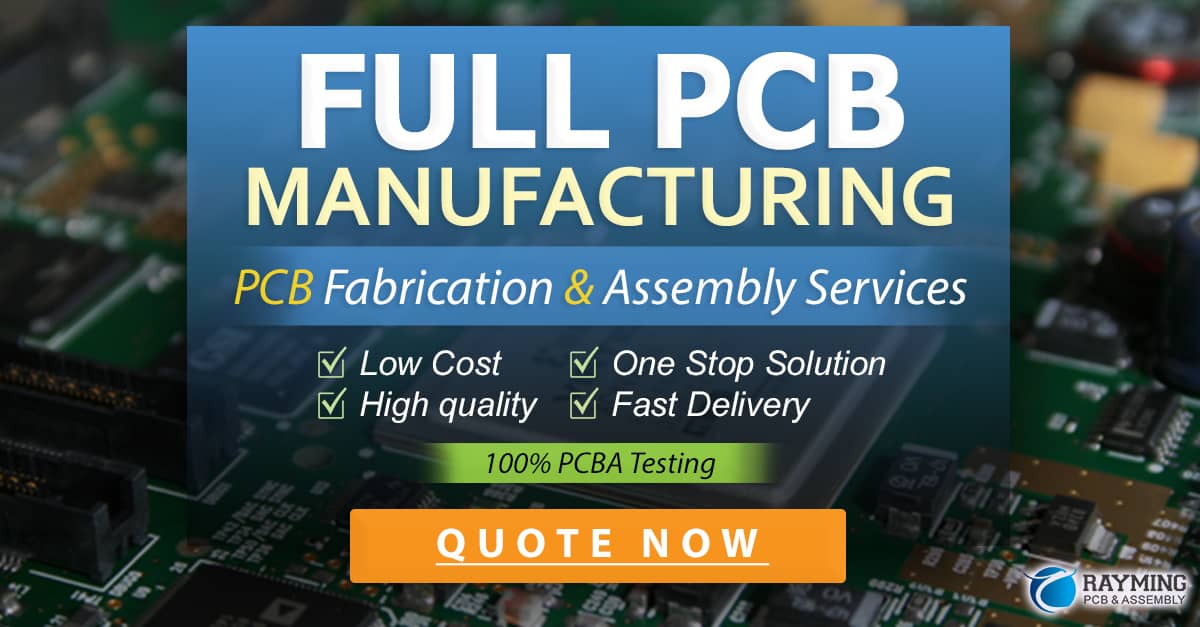
Best Practices for QFN Assembly
To ensure successful QFN assembly, consider the following best practices:
PCB Design Considerations
- Pad size and spacing: Follow the manufacturer’s recommended pad size and spacing guidelines for the specific QFN package. Proper pad design ensures reliable solder joint formation.
- Solder mask opening: Provide adequate solder mask opening around the pads to allow for proper solder wetting and prevent solder bridging.
- Thermal relief design: Incorporate thermal relief patterns in the PCB layout to improve heat dissipation and prevent thermal stress on the solder joints.
Stencil Design and Solder Paste Deposition
- Stencil thickness: Select an appropriate stencil thickness based on the QFN package height and solder paste requirements. A typical stencil thickness for QFN packages ranges from 0.1 mm to 0.15 mm.
- Aperture size and shape: Optimize the aperture size and shape in the stencil design to ensure proper solder paste deposition. The aperture should be slightly smaller than the pad size to prevent solder bridging.
- Solder paste selection: Choose a solder paste with the appropriate particle size and flux chemistry for QFN assembly. Fine-pitch solder pastes with Type 4 or Type 5 particle sizes are commonly used.
Reflow Profile Optimization
- Peak temperature: Ensure that the peak reflow temperature is within the recommended range for the specific QFN package and solder paste.
- Time above liquidus (TAL): Control the TAL to achieve proper solder wetting and intermetallic compound formation without causing thermal damage to the components.
- Cooling rate: Maintain a controlled cooling rate to minimize thermal stress and prevent solder joint defects.
Inspection and Testing
- Visual inspection: Perform visual inspection of the QFN assemblies using magnification or automated optical inspection (AOI) systems to detect any visible defects.
- X-ray inspection: Utilize X-ray inspection techniques to verify the integrity of solder joints hidden under the QFN package.
- Electrical testing: Conduct electrical testing to ensure the functionality and performance of the assembled PCBs.
Conclusion
QFN packages offer numerous benefits in PCB assembly, including reduced size, improved thermal performance, and lower cost. However, the challenges associated with QFN assembly, such as thermal management and solder joint reliability, require careful consideration when selecting a PCB assembly service provider.
By choosing a service provider with the necessary experience, equipment, and quality control processes, you can ensure the success of your QFN assembly projects. Additionally, following best practices in PCB design, stencil design, solder paste deposition, reflow profile optimization, and inspection and testing can further enhance the reliability and performance of your QFN assemblies.
Frequently Asked Questions (FAQ)
1. What is the difference between QFN and QFP packages?
QFN (Quad Flat No-lead) packages have no leads extending from the package body, while QFP (Quad Flat Package) packages have leads extending from all four sides of the package. QFN packages have a smaller footprint and better thermal performance compared to QFP packages.
2. Can QFN packages be assembled using hand soldering?
While it is possible to assemble QFN packages using hand soldering, it is not recommended due to the small size and close proximity of the pads. Reflow soldering using a stencil and solder paste is the preferred method for QFN assembly to ensure reliable solder joints.
3. What is the purpose of the exposed pad on the bottom of QFN packages?
The exposed pad on the bottom of QFN packages serves as a thermal and electrical connection to the PCB. It helps in dissipating heat from the device and provides a low-impedance ground connection, improving the overall thermal and electrical performance of the package.
4. How can I ensure the reliability of solder joints in QFN packages?
To ensure the reliability of solder joints in QFN packages, consider the following:
– Follow the manufacturer’s recommended pad size and spacing guidelines.
– Use a stencil with the appropriate aperture size and shape for proper solder paste deposition.
– Optimize the reflow profile, including peak temperature, time above liquidus, and cooling rate.
– Perform visual and X-ray inspection to verify the integrity of solder joints.
5. What are the common defects encountered in QFN assembly?
Common defects encountered in QFN assembly include:
– Solder bridging: Solder paste connecting adjacent pads, causing short circuits.
– Insufficient solder joint: Inadequate solder volume, leading to weak or open connections.
– Solder voiding: Trapped gases within the solder joint, reducing the effective contact area and thermal conductivity.
– Component misalignment: Misplaced or rotated components, affecting the electrical connection and performance.
Package Type | Footprint | Thermal Performance | Cost |
---|---|---|---|
QFN | Small | Excellent | Low |
QFP | Larger | Good | Moderate |
BGA | Smallest | Excellent | High |
By selecting the right PCB assembly service provider, following best practices, and understanding the challenges and solutions associated with QFN assembly, you can successfully incorporate QFN packages into your electronic designs and achieve optimal performance and reliability.
0 Comments