Introduction to Micro-BGA PCB Assembly
Micro-BGA (Ball Grid Array) is a type of surface-mount packaging used for integrated circuits (ICs) with a high pin count and small footprint. This packaging technology has gained popularity in recent years due to the increasing demand for miniaturization and high-density interconnects in electronic devices. Micro-BGA PCB assembly requires specialized equipment and expertise to ensure reliable and efficient assembly processes.
In this article, we will explore the various aspects of Micro-BGA PCB assembly, including the advantages and challenges, the assembly process, and the key considerations when selecting a PCB assembly service provider for Micro-BGA packages.
Advantages of Micro-BGA Packaging
Micro-BGA packaging offers several advantages over traditional packaging methods, such as:
- Reduced Package Size: Micro-BGA packages have a smaller footprint compared to other packaging types, allowing for higher component density on PCBs.
- Improved Electrical Performance: The shorter interconnect lengths in Micro-BGA packages result in reduced inductance and improved signal integrity.
- Enhanced Thermal Performance: The ball grid array configuration provides better thermal dissipation compared to peripheral lead packages.
- Increased Reliability: Micro-BGA packages offer better resistance to mechanical stress and thermal cycling, improving overall reliability.
Challenges in Micro-BGA PCB Assembly
Despite the advantages, Micro-BGA PCB assembly presents several challenges that must be addressed to ensure a successful assembly process:
- Precise Alignment: The small pitch and high pin count of Micro-BGA packages require precise alignment during the assembly process to avoid bridging or open connections.
- Thermal Management: Proper thermal management is crucial to prevent overheating and ensure reliable operation of Micro-BGA components.
- Inspection and Testing: The small size and high density of Micro-BGA packages make visual inspection and testing more challenging, requiring specialized equipment and techniques.
- Rework and Repair: Reworking or repairing Micro-BGA components can be difficult due to the small size and the risk of damaging adjacent components.
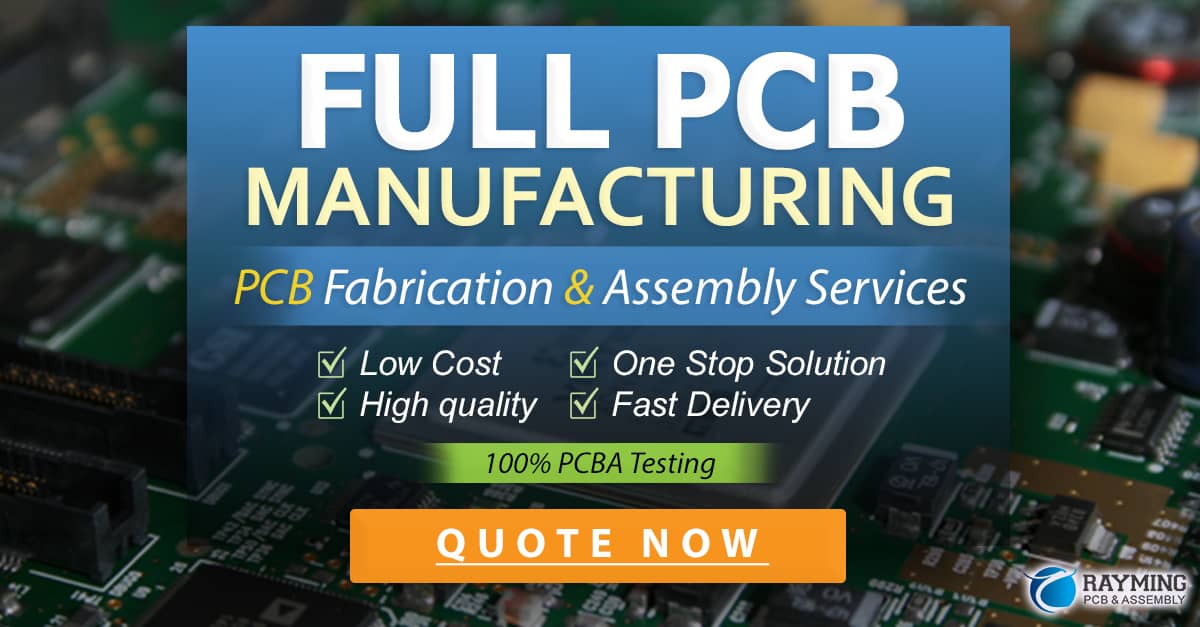
Micro-BGA PCB Assembly Process
The Micro-BGA PCB assembly process typically involves the following steps:
- Solder Paste Printing: A stencil is used to apply solder paste onto the PCB pads where the Micro-BGA component will be placed.
- Component Placement: The Micro-BGA component is precisely aligned and placed onto the PCB using a pick-and-place machine with high accuracy.
- Reflow Soldering: The PCB with the placed components is subjected to a controlled heating process in a reflow oven, allowing the solder paste to melt and form reliable connections between the component and the PCB.
- Inspection and Testing: After the reflow process, the assembled PCB undergoes visual inspection and electrical testing to ensure proper functionality and reliability.
Key Considerations for Selecting a Micro-BGA PCB Assembly Service Provider
When choosing a PCB assembly service provider for Micro-BGA packages, consider the following factors:
- Experience and Expertise: Look for a service provider with extensive experience in Micro-BGA PCB assembly and a proven track record of success.
- Equipment and Facilities: Ensure that the service provider has the necessary equipment, such as high-precision pick-and-place machines and reflow ovens, to handle Micro-BGA Assembly.
- Quality Control and Testing: Inquire about the service provider’s quality control measures and testing capabilities to ensure the reliability and functionality of the assembled PCBs.
- Turnaround Time and Cost: Consider the service provider’s turnaround time and pricing structure to ensure they align with your project requirements and budget.
Micro-BGA PCB Assembly Equipment
To successfully assemble Micro-BGA components onto PCBs, specialized equipment is required. Some of the essential equipment for Micro-BGA PCB assembly includes:
- High-Precision Pick-and-Place Machines: These machines are capable of accurately placing Micro-BGA components onto PCBs with a placement accuracy of ±0.025 mm or better.
- Reflow Ovens: Reflow ovens with precise temperature control and profiling capabilities are necessary to ensure proper solder joint formation and prevent component damage during the reflow process.
- Automated Optical Inspection (AOI) Systems: AOI systems are used to inspect the assembled PCBs for defects such as missing components, misaligned components, or solder bridging.
- X-ray Inspection Systems: X-ray inspection systems enable non-destructive inspection of solder joints beneath Micro-BGA components, ensuring the integrity of the connections.
Micro-BGA PCB Assembly Materials
In addition to the equipment, the selection of appropriate materials is crucial for successful Micro-BGA PCB assembly. Some of the key materials include:
- Solder Paste: A high-quality solder paste with the appropriate alloy composition and particle size is essential for reliable solder joint formation.
- Flux: Flux helps to remove oxides and improve the wetting of the solder paste during the reflow process.
- PCB Substrate: The PCB substrate should have the appropriate surface finish (e.g., ENIG, HASL) and dimensions to accommodate the Micro-BGA package.
- Micro-BGA Components: The Micro-BGA components should be sourced from reputable suppliers and meet the required specifications, such as ball size, pitch, and material composition.
Micro-BGA PCB Assembly Design Considerations
To ensure the successful assembly of Micro-BGA components, PCB designers should consider the following factors:
- Pad Size and Pitch: The pad size and pitch should be appropriate for the specific Micro-BGA package to ensure proper solder joint formation and prevent bridging.
- Solder Mask Opening: The solder mask opening should be designed to provide adequate clearance for the solder balls while preventing solder bridging.
- Thermal Considerations: Proper thermal management should be incorporated into the PCB design, such as the use of thermal vias or heatsinks, to dissipate heat generated by the Micro-BGA components.
- Signal Integrity: The PCB layout should be optimized for signal integrity, minimizing crosstalk and impedance mismatches, especially for high-speed applications.
Micro-BGA PCB Assembly Testing and Inspection
To ensure the reliability and functionality of the assembled Micro-BGA PCBs, various testing and inspection methods are employed, including:
- Visual Inspection: Visual inspection is performed to identify any obvious defects, such as missing or misaligned components, solder bridging, or damaged components.
- Automated Optical Inspection (AOI): AOI systems use computer vision techniques to inspect the assembled PCBs for defects, providing fast and accurate inspection results.
- X-ray Inspection: X-ray inspection is used to examine the solder joints beneath the Micro-BGA components, detecting any voids, cracks, or insufficient solder coverage.
- Electrical Testing: Electrical testing, such as in-circuit testing (ICT) or functional testing, is performed to verify the electrical functionality of the assembled PCBs.
Micro-BGA PCB Assembly Rework and Repair
Despite the challenges, rework and repair of Micro-BGA components may be necessary in some cases. The following techniques are commonly used for Micro-BGA Rework and repair:
- Hot Air Rework: A focused hot air nozzle is used to heat the Micro-BGA component and the surrounding area, allowing the component to be removed and replaced.
- Mechanical Removal: In some cases, the Micro-BGA component may be mechanically removed using specialized tools, such as a vacuum pen or tweezers.
- Solder Paste Dispensing: After removing the defective component, solder paste is dispensed onto the PCB pads using a dispensing system or stencil.
- Component Replacement: A new Micro-BGA component is aligned and placed onto the PCB, and the reflow process is performed to establish the solder connections.
Micro-BGA PCB Assembly Service Providers
When selecting a PCB assembly service provider for Micro-BGA packages, it is essential to consider their experience, capabilities, and track record. Some of the top Micro-BGA PCB assembly service providers include:
- Sanmina: Sanmina is a global electronics manufacturing services (EMS) provider with extensive experience in Micro-BGA PCB assembly. They offer a wide range of services, including design, prototyping, and volume production.
- Jabil: Jabil is another leading EMS provider with a strong presence in the Micro-BGA PCB assembly market. They have state-of-the-art facilities and offer comprehensive services, from design to final assembly and testing.
- Foxconn: Foxconn is a well-known electronics contract manufacturer with capabilities in Micro-BGA PCB assembly. They have a global presence and offer a wide range of services, including design, manufacturing, and supply chain management.
- Celestica: Celestica is a multinational EMS provider with expertise in Micro-BGA PCB assembly. They offer a full range of services, from design and prototyping to volume production and after-market services.
Frequently Asked Questions (FAQ)
-
What is Micro-BGA packaging?
Micro-BGA (Ball Grid Array) is a type of surface-mount packaging used for integrated circuits (ICs) with a high pin count and small footprint. It consists of an array of small solder balls on the bottom of the package, which are used to establish electrical connections with the PCB. -
What are the advantages of Micro-BGA packaging?
The advantages of Micro-BGA packaging include reduced package size, improved electrical performance, enhanced thermal performance, and increased reliability compared to other packaging types. -
What challenges are associated with Micro-BGA PCB assembly?
The challenges in Micro-BGA PCB assembly include precise alignment of components, thermal management, inspection and testing difficulties, and challenges in rework and repair due to the small size and high density of the packages. -
What equipment is required for Micro-BGA PCB assembly?
The essential equipment for Micro-BGA PCB assembly includes high-precision pick-and-place machines, reflow ovens with precise temperature control, automated optical inspection (AOI) systems, and X-ray inspection systems. -
How can I select a reliable Micro-BGA PCB assembly service provider?
When selecting a Micro-BGA PCB assembly service provider, consider factors such as their experience and expertise in Micro-BGA assembly, equipment and facilities, quality control measures, testing capabilities, turnaround time, and cost. Research and compare multiple service providers to find the one that best aligns with your project requirements and expectations.
Conclusion
Micro-BGA PCB assembly is a complex process that requires specialized equipment, expertise, and attention to detail. By understanding the advantages, challenges, and key considerations involved in Micro-BGA assembly, you can make informed decisions when selecting a PCB assembly service provider and ensure the success of your projects.
When choosing a Micro-BGA PCB assembly service provider, prioritize experience, capabilities, and a proven track record of delivering high-quality results. By partnering with a reliable service provider, you can leverage their expertise and advanced equipment to overcome the challenges associated with Micro-BGA assembly and achieve reliable, high-performance electronic products.
Micro-BGA PCB Assembly Service Provider | Strengths |
---|---|
Sanmina | – Extensive experience in Micro-BGA assembly – Wide range of services (design, prototyping, volume production) – Global presence |
Jabil | – State-of-the-art facilities – Comprehensive services (design to final assembly and testing) – Strong presence in the Micro-BGA assembly market |
Foxconn | – Well-known electronics contract manufacturer – Capabilities in Micro-BGA assembly – Global presence and wide range of services |
Celestica | – Expertise in Micro-BGA assembly – Full range of services (design, prototyping, volume production, after-market services) – Multinational presence |
By staying informed about the latest advancements in Micro-BGA packaging and assembly technologies, and by collaborating with experienced PCB assembly service providers, you can ensure the success of your electronic products and stay competitive in today’s rapidly evolving market.
0 Comments