Introduction
Printed circuit boards (PCBs) are essential components in nearly all modern electronic devices. As an electrical engineer or product designer, you may need to work with a contract manufacturer for assembling your custom PCB designs into finished boards. With so many PCB assembly factories to choose from, how do you select the right one?
This comprehensive guide covers key factors to consider when choosing a factory for PCB assembly. We’ll look at capabilities, quality, costs, turnaround times, and other criteria to help you find the ideal manufacturing partner for your project.
Assessing PCB Assembly Capabilities
The first step is determining if a potential factory has the technical capabilities to assemble your boards. Here are some questions to get answers for:
What assembly processes are supported?
There are two main types of PCB assembly:
- Through-hole assembly – For PCBs with leads that pass completely through holes in the board. Soldering forms the connections.
- Surface-mount technology (SMT) – For attaching components directly onto pads on the surface of PCBs. Reflow soldering with solder paste is commonly used.
Many factories will offer both SMT and through-hole assembly. Ask what maximum board sizes, smallest components, ball grid array (BGA) chips, and other specialized assembly they can handle.
What components can be sourced and assembled?
The factory should be able to procure common passive components like resistors, capacitors, LEDs, etc. Ask if they stock or can source any specialized or high-value components your design requires.
What testing and inspection capabilities are available?
PCBs should be electrically tested after assembly to verify there are no shorts, opens or faulty connections. Inspection should also check for physical defects like misaligned parts or poor solder joints. Ask what testing methods the factory uses, like flying probe, in-circuit test (ICT), or automated optical inspection (AOI).
What are the maximum and minimum assembly quantities?
Factories often have order size requirements based on their production processes. For instance, manual assembly may require building at least 10-25 boards, while automated SMT lines are ideal for large production runs of hundreds or thousands of boards.
What documentation is required from the customer?
To quote and successfully build your boards, the factory will need:
- Bill of materials (BOM) listing all components
- Printed circuit board fabrication files (Gerber files)
- Assembly drawings showing reference designators, placements, etc.
Confirm what format and lead time they need for this documentation.
Evaluating Quality and Reliability
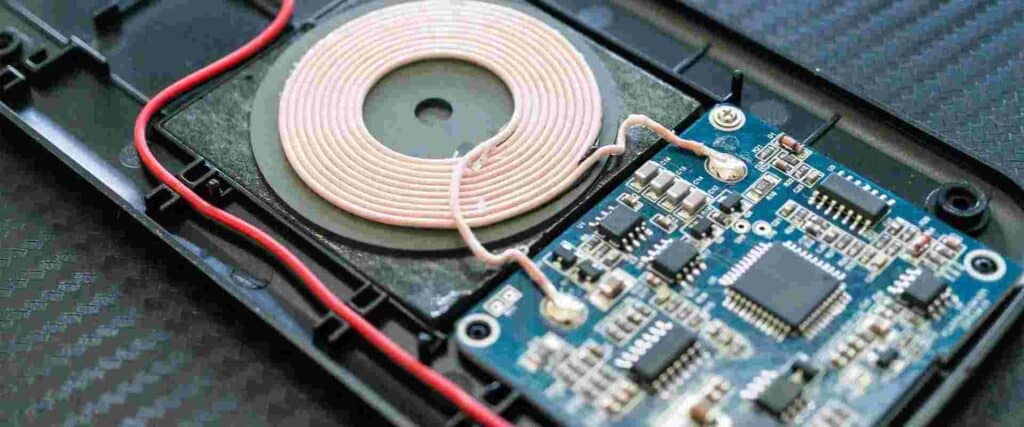
Getting high-quality PCB assembly work is critical. Asking these questions will reveal how reliable and consistent a factory’s processes are:
What quality certifications has the factory obtained?
The most common certification is ISO 9001, which verifies a comprehensive quality management system. ISO 13485 adds requirements for medical devices. IATF 16949 is an automotive-focused certification. These certifications are rigorous to obtain and maintain, giving confidence in the factory’s capabilities.
What quality control procedures are in place?
A strong quality process will include inspections at every major production stage, testing of all boards after completion, quality training for staff, document control, escalation procedures for issues, corrective action systems, control of obsolete components, and more.
What is the typical defect rate or Cpk level?
The factory should track long-term process capabilities statistics like Cpk levels for critical parameters like soldering temperature. Cpk above 1.33 generally indicates good performance. Also ask about typical defect rates found through post-assembly testing. A rate lower than 100 parts per million (PPM) implies robust processes.
What repair and rework capabilities exist?
Despite quality control efforts, some assembled boards may be found with defects. Many factories can repair issues with rework stations or replace individual components. Understanding their repair capabilities can avoid costly discards of boards with minor fixable flaws.
Are there automated optical inspection (AOI) systems?
AOI machines use cameras to quickly scan assembled PCBs and identify defects like missing or misaligned components, poor solder joints, bridging between pads, and other common assembly issues. AOI substantially improves quality by catching flaws the human eye can miss. Ask what systems they use and on what percentage of boards AOI is performed.
What test coverage is provided?
At minimum, basic electrical tests should check for short circuits and verify all components are loaded correctly. More thorough testing looks for specific passive component values and voltages. The best functional testing confirms the board actually operates properly when powered on. Know what level of test coverage is included by default and what additional testing can be added.
Comparing Costs
Balancing capability, quality, and cost is key for choosing a PCB assembly partner. Here are cost factors to understand:
What is included in assembly pricing?
- Basic assembly labor and machine costs
- Solder paste, adhesives, cleaning chemicals
- Typical component sourcing and procurement
- Incoming quality control of components
- Post-assembly board testing
- Any special packaging and shipping requirements
Understand what is covered in the base assembly quote versus any additional NRE charges like test fixture creation.
How are component costs handled?
For procuring components, factories use one of two models:
- Turnkey pricing – The factory purchases reels of standard components needed for assembly. This simplifies purchasing for the customer, but components are marked up.
- Customer-supplied components – The customer sources and pays for all components up front, often at lower prices than the factory can obtain. However, this adds procurement workload for the customer.
Ask what their component pricing model and markups are. Turnkey is simpler, but customer-supplied parts can significantly cut overall costs.
What are typical lead times?
- For a new design, manufacturing lead time may range from 2-6 weeks.
- For repeat orders, assembly can often be completed within 1-2 weeks.
- Prototype and low-volume orders generally take longer than higher volume production.
Confirm standard lead times and what options may be available for expediting orders at additional cost.
What minimum order quantities apply?
As noted previously, factories will have minimum quantities for assembly orders. This spans anywhere from 10-25 boards for manual assembly up to 500+ for SMT production. See what MOQ applies for your required order size.
What pricing breaks apply at higher volumes?
Factories can offer better per-unit pricing as order quantities increase into the hundreds or thousands of boards. This is due to better utilization of fixed manufacturing equipment and labor costs. See what volume discounts may apply for your expected order size.
Are there NRE/setup fees? What is included?
Non-recurring engineering fees may be charged for generating assembly work instructions, testing programs, building fixtures, and other. Understand exactly what is covered by any NRE charges.
Choosing Domestic vs. International Assembly
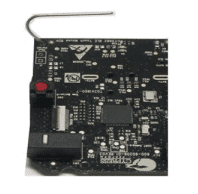
A key decision is using a domestic or international PCB assembly factory. Both have pros and cons to weigh:
Domestic PCB Assembly
- Located within the same country you operate (eg. US plant if you are a US-based company)
- Optimized for smaller build quantities and faster turnaround
- Easier communication and project management in your time zone
- Generally more controlled and transparent processes
However, domestic factories typically have higher per-unit pricing, especially at higher volumes.
International PCB Assembly
- Primarily located in China, but also emerging options in Southeast Asia and Eastern Europe
- Very cost-effective at higher build volumes (1,000+ units)
- Often have large production capacities suitable for high-volume manufacturing
Downsides are longer lead times, more effort for communications, cultural barriers, and less process visibility. Quality can be inconsistent across factories.
If your project has stringent quality needs or fast turnarounds, domestic assembly may be preferred. For mass production of a stable design, overseas factories offer compelling pricing advantages.
Turnaround Time Considerations
Lead time is made up of:
- Documentation processing and quoting
- Sourcing components
- Scheduled production time
- Incoming quality control
- Assembly
- Post-assembly testing
- Final packaging/prep for shipping
For fastest turnaround, choose a factory already familiar with your PCB design so NRE setup is minimal. Have all documentation and components ready to provide upfront. Clearly communicate desired target schedule. Simple, low-component designs assemble quickest.
Be realistic about lead times required. For complex designs, assembly can easily take 4-6 weeks. Budgeting inadequate time often leads to delays or rushed assembly work.
Evaluating Overall PCB Assembly Partnership
Beyond technical capabilities and costs, the working relationship is also key for success:
- What design-for-manufacturing guidance do they offer? Good partners will proactively suggest ways to optimize your design for easy, reliable assembly.
- How responsive and transparent is technical support? Expect quick responses to your assembly questions without runarounds.
- Are managers receptive to feedback and focused on continuous improvement? Look for engagement rather than apathy.
- What reviews and progress updates will you receive during assembly? Lack of communication risks surprises or issues going undetected.
- How well will they handle problems if defects are found? You need confidence problems will be quickly addressed.
Take time to communicate with sales representatives and engineers at potential factories. Gauge how well they seem to understand your needs and priorities. The ideal partner will take a genuine consultative interest in ensuring your project’s success.
Conclusion
With careful selection guided by the criteria above, you can find a PCB assembly factory well-matched to your specific project requirements. Keeping business localized reduces logistical issues. However, overseas production may be right for high-volume cost-sensitive consumer electronics. In all cases, verify quality processes are in place to achieve assembly excellence. With attention to detail in choosing your manufacturing partner, you can get your electronics products assembled quickly and reliably.
Frequently Asked Questions
What are the main differences between leaded and SMT PCB assembly?
The primary differences between leaded through-hole and surface mount technology (SMT) assembly include:
- Components: SMT uses smaller chip components soldered directly to the surface while leaded uses larger through-hole parts.
- Process: SMT is highly automated for faster assembly while leaded relies more on manual soldering.
- Soldering method: SMT uses reflow ovens to heat entire boards at once while leaded uses a soldering iron or wave solder machine on each joint.
- Density: SMT assemblies can be more compact and complex with thousands of components.
- Rework difficulty: It’s easier to remove and replace leaded components than surface mount chips.
- Cost: SMT has higher upfront costs for stencils and programming but lower labor.
Should every PCB get tested after assembly?
While complete testing of every board may be ideal, the time and cost constraints of a project may determine a more selective testing approach. Some considerations around testing strategy include:
- For simpler boards, basic electrical tests may be sufficient to catch major flaws.
- Mission-critical boards demand thorough testing of all units.
- High-volume consumer products may rely on statistical sampling such as ANSI/ASQ Z1.4.
- New designs benefit from more extensive testing during early builds.
- Testing percentage can be reduced once a design has proven consistent production reliability.
- Any boards repaired should get re-tested before shipment.
Assessing the risks, production stage, and resources available guides appropriate PCB testing levels.
What can be done if a PCB assembly factory creates defective boards?
If a factory delivers defective assembled PCBs, there are several recourses:
- Have the factory repair the boards if issues are fixable errors like misaligned parts or poor solder joints.
- Require the factory to assemble replacement boards until you receive the full quantity of good boards ordered.
- If quality issues persist across multiple builds, change to a higher reliability factory, likely at greater expense.
- For assembly errors that escape to customers, repairs or replacements can be done but may be costly.
Thoroughly vetting a factory’s quality processes is the best way to avoid needing to take action on excessive defects. Check references and only choose factories with demonstrated capabilities.
How can I estimate lead time for my first PCB assembly order?
For initial assembly orders, a good rule of thumb is 1 week of lead time per 100 components on the board. So for example:
- Board with 50 components: 3 weeks minimum lead time
- 150 components: 6 weeks lead time
- 500 components: 10+ weeks lead time
This accounts for documentation exchange, NRE setup work, procurement, assembly, and testing. Building in buffer for unexpected delays is wise. Once processes are proven for repeat builds, lead time can often be halved. Be conservative when planning your first assembly timeline.
What are some alternatives if I have an urgent PCB assembly need?
If you urgently require a small quantity of assembled PCBs, some alternatives to consider are:
- Local makerspaces or fablabs if available – manual assembly and soldering
- Small machine shop – may offer quick simple assembly
- University engineering departments – student projects
- Local hobbyists or electronics meetup groups
- Crowdsourced assembly like Macrofabrication
- Expedited small-batch assembly from a domestic prototype shop
The work quality may not match larger scale manufacturing, but these methods can be great for bridging the gap during development phases.
0 Comments