Types of PCB Assembly & Fabrication Equipment
1. PCB Fabrication Equipment
1.1 PCB Plotter
A PCB plotter is used to print the circuit design onto the copper-clad laminate. It uses a high-precision, computer-controlled pen to draw the circuit pattern on the board’s surface.
Advantages | Disadvantages |
---|---|
High precision | Slower than other methods |
Cost-effective for low-volume production | Not suitable for complex designs |
Easy to operate | Limited to single-layer boards |
1.2 PCB Etching Machine
After the circuit pattern is printed on the board, a PCB etching machine is used to remove the unwanted copper from the laminate, leaving only the desired circuit pattern. There are two main types of etching machines:
- Spray Etching Machine: Uses a chemical spray to remove the unwanted copper.
- Bubble Etching Machine: Immerses the board in an etchant solution and uses air bubbles to agitate the solution for even etching.
Etching Machine Type | Advantages | Disadvantages |
---|---|---|
Spray Etching | Fast etching process | Higher equipment cost |
Suitable for high-volume production | Requires regular maintenance | |
Bubble Etching | Lower equipment cost | Slower etching process |
Easy to maintain | Less suitable for high-volume production |
1.3 PCB Drilling Machine
A PCB drilling machine is used to create holes in the board for component leads and vias. There are two main types of drilling machines:
- Mechanical Drilling Machine: Uses high-speed steel or carbide drill bits to create holes.
- Laser Drilling Machine: Uses a focused laser beam to burn holes in the board.
Drilling Machine Type | Advantages | Disadvantages |
---|---|---|
Mechanical Drilling | Lower equipment cost | Slower drilling process |
Suitable for larger hole sizes | Drill bits require frequent replacement | |
Laser Drilling | Fast drilling process | Higher equipment cost |
High precision for small hole sizes | Not suitable for larger hole sizes |
2. PCB Assembly Equipment
2.1 Solder Paste Printer
A solder paste printer applies solder paste to the pads on the PCB where components will be placed. The most common type is the stencil printer, which uses a stencil with openings that correspond to the pads on the board.
Advantages | Disadvantages |
---|---|
Precise solder paste application | Stencils require periodic cleaning and maintenance |
High-speed operation | Initial setup can be time-consuming |
Consistent results | Solder paste must be refrigerated and has a limited shelf life |
2.2 Pick and Place Machine
A pick and place (P&P) machine automatically places surface mount components onto the PCB. It uses a vacuum nozzle to pick up components from feeders and place them on the board with high precision.
Advantages | Disadvantages |
---|---|
High-speed component placement | High initial equipment cost |
High precision and accuracy | Requires skilled operators |
Suitable for high-volume production | Limited flexibility for different component types and sizes |
2.3 Reflow Oven
After components are placed on the board, a reflow oven is used to melt the solder paste and create a permanent bond between the components and the board. Reflow ovens use a carefully controlled temperature profile to ensure proper solder joint formation.
Advantages | Disadvantages |
---|---|
Consistent solder joint quality | High energy consumption |
Suitable for high-volume production | Requires careful temperature profile optimization |
Automated process | Limited control over individual component heating |
2.4 Wave Soldering Machine
For through-hole components, a wave soldering machine is used to solder the component leads to the board. The machine pumps molten solder into a wave that contacts the bottom of the board, creating a solder joint.
Advantages | Disadvantages |
---|---|
Fast soldering process | Not suitable for surface mount components |
Suitable for high-volume production | Can cause thermal stress on components |
Automated process | Requires regular maintenance and solder bath management |
3. PCB Inspection Equipment
3.1 Automated Optical Inspection (AOI)
AOI machines use high-resolution cameras and advanced image processing algorithms to inspect PCBs for defects such as missing components, solder bridges, and incorrect component placement.
Advantages | Disadvantages |
---|---|
Fast and accurate inspection | High initial equipment cost |
Detects a wide range of defects | Requires skilled operators for setup and maintenance |
Suitable for high-volume production | May not detect all defect types (e.g., hidden solder joints) |
3.2 X-Ray Inspection
X-ray inspection machines use x-rays to create images of the internal structure of the PCB, allowing for the detection of defects that are not visible on the surface, such as voids in solder joints or misaligned BGA components.
Advantages | Disadvantages |
---|---|
Detects hidden defects | High equipment cost |
Provides detailed internal images | Requires skilled operators for interpretation |
Non-destructive testing | Slower inspection process compared to AOI |
Key Considerations for Selecting PCB Equipment
When choosing PCB assembly and fabrication equipment, consider the following factors:
- Production volume and scalability
- PCB complexity and component types
- Equipment precision and accuracy
- Ease of use and maintenance
- Integration with existing processes and systems
- Budget and return on investment (ROI)
Frequently Asked Questions (FAQ)
1. What is the difference between through-hole and surface mount components?
Through-hole components have leads that are inserted into holes drilled in the PCB and soldered on the opposite side. Surface mount components are placed directly on the surface of the board and soldered in place.
2. Can a single machine handle both PCB fabrication and assembly?
No, PCB fabrication and assembly require different types of equipment. Fabrication equipment is used to create the bare PCB, while assembly equipment is used to place and solder components onto the board.
3. How much does PCB assembly and fabrication equipment cost?
The cost of PCB equipment varies widely depending on the type, features, and capacity. Simple manual tools can cost a few hundred dollars, while high-end automated systems can cost several hundred thousand dollars or more.
4. What is the typical lifespan of PCB assembly and fabrication equipment?
The lifespan of PCB equipment depends on factors such as usage, maintenance, and technological advancements. Generally, well-maintained equipment can last 5-10 years or more, but some components may require more frequent replacement.
5. How can I ensure the quality of my PCBs?
Ensuring PCB quality involves a combination of factors, including:
– Selecting high-quality materials and components
– Using appropriate equipment and processes for your specific PCB design
– Implementing strict quality control measures, such as AOI and X-ray inspection
– Regularly maintaining and calibrating your equipment
– Providing thorough training for your operators
By understanding the various types of PCB assembly and fabrication equipment, their functions, and key considerations for selection, you can make informed decisions when investing in equipment for your PCB manufacturing process. With the right equipment and processes in place, you can produce high-quality, reliable PCBs efficiently and cost-effectively.
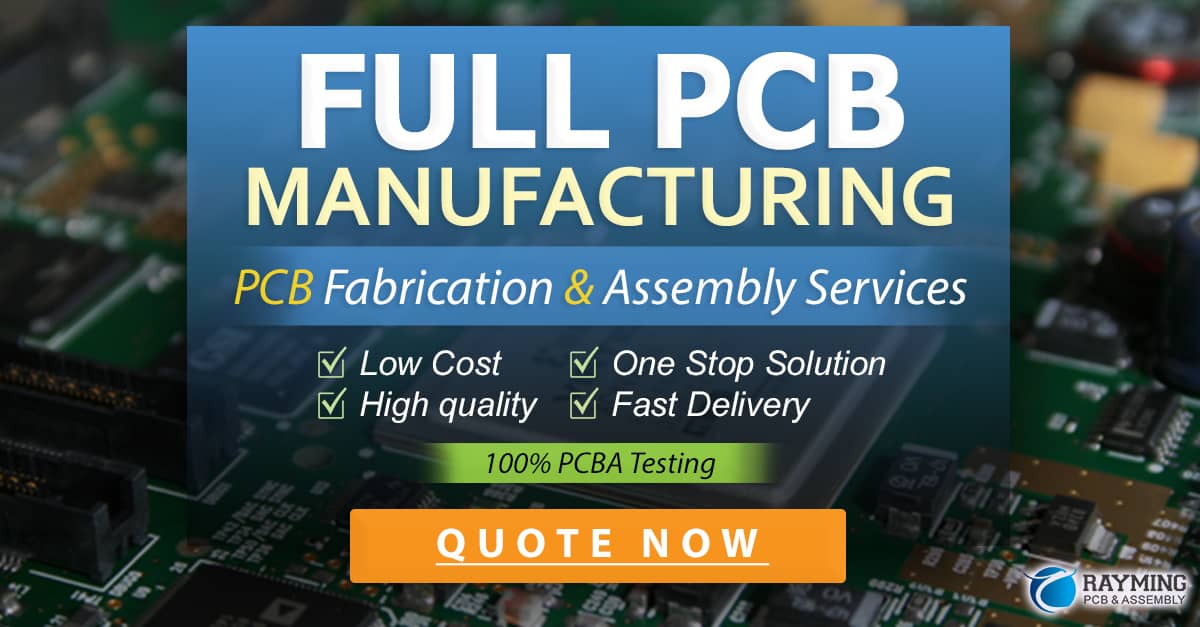
0 Comments