The Importance of PCBs in IOT Devices
PCBs are the backbone of IOT devices. They are responsible for connecting various components and ensuring that the device functions as intended. The quality and reliability of PCBs directly impact the performance and longevity of IOT devices.
IOT devices often operate in harsh environments and are subjected to extreme temperatures, vibrations, and moisture. Therefore, the PCBs used in these devices must be able to withstand these conditions and continue to function reliably.
The Role of PCBs in IOT Devices
PCBs play a crucial role in IOT devices by:
- Connecting various components such as sensors, microcontrollers, and communication modules
- Providing a stable and reliable platform for the device to function
- Ensuring that the device can withstand harsh environmental conditions
- Enabling the device to communicate with other devices and the cloud
Challenges in IOT-PCB Manufacturing
Manufacturing PCBs for IOT devices comes with its own set of challenges. These challenges must be addressed to ensure that the PCBs are of high quality and can function reliably in the field.
Miniaturization
IOT devices are becoming smaller and more compact, which means that the PCBs used in these devices must also be miniaturized. Miniaturization poses several challenges, such as:
- Increased component density
- Reduced spacing between components
- Increased heat generation
- Difficulty in handling and assembly
High-Speed Communication
IOT devices often require high-speed communication to transmit data to the cloud or other devices. This requires the PCBs to be designed for high-speed signals, which can be challenging due to:
- Signal integrity issues
- Electromagnetic interference (EMI)
- Impedance matching
- Transmission line effects
Harsh Environmental Conditions
IOT devices are often deployed in harsh environmental conditions, such as:
- Extreme temperatures
- High humidity
- Vibrations
- Dust and debris
The PCBs used in these devices must be able to withstand these conditions and continue to function reliably.
Cost Constraints
IOT devices are often mass-produced, which means that the cost of the PCBs must be kept low. However, the need for high-quality and reliable PCBs can increase the cost of manufacturing.
Smart PCB Manufacturing Techniques
Smart PCB manufacturing techniques can help overcome the challenges of IOT-PCB manufacturing. These techniques leverage advanced technologies and processes to produce high-quality and reliable PCBs at a lower cost.
3D Printing
3D printing is a process that involves building up layers of material to create a three-dimensional object. In PCB manufacturing, 3D printing can be used to create complex shapes and structures that would be difficult or impossible to achieve with traditional manufacturing methods.
Benefits of 3D printing in PCB manufacturing:
- Enables the creation of complex geometries and shapes
- Reduces the need for multiple manufacturing steps
- Allows for rapid prototyping and iteration
- Reduces waste and material usage
Additive Manufacturing
Additive manufacturing is a process that involves building up layers of material to create a three-dimensional object. In PCB manufacturing, additive manufacturing can be used to create conductive traces and other features directly onto the PCB substrate.
Benefits of additive manufacturing in PCB manufacturing:
- Enables the creation of fine-pitch traces and features
- Reduces the need for etching and plating processes
- Allows for the creation of three-dimensional structures
- Enables the integration of components directly onto the PCB
Flexible and Stretchable PCBs
Flexible and stretchable PCBs are designed to bend and stretch without breaking or losing functionality. These PCBs are ideal for IOT devices that require flexibility or must conform to irregular shapes.
Benefits of flexible and stretchable PCBs:
- Enables the creation of wearable and implantable devices
- Allows for greater design freedom and flexibility
- Reduces the risk of damage due to bending or stretching
- Enables the integration of sensors and other components directly onto the PCB
Advanced Materials
Advanced materials, such as high-temperature polymers and ceramic substrates, can be used to create PCBs that can withstand harsh environmental conditions.
Benefits of advanced materials in PCB manufacturing:
- Enables the creation of PCBs that can withstand extreme temperatures and harsh environments
- Reduces the risk of failure due to environmental factors
- Allows for greater design flexibility and functionality
Automated Inspection and Testing
Automated inspection and testing can help ensure that PCBs are of high quality and free from defects. These processes use advanced imaging and analysis techniques to detect and identify defects that may not be visible to the human eye.
Benefits of automated inspection and testing:
- Reduces the risk of defects and failures in the field
- Enables faster and more accurate inspection and testing
- Reduces the need for manual inspection and testing
- Enables real-time monitoring and analysis of the manufacturing process
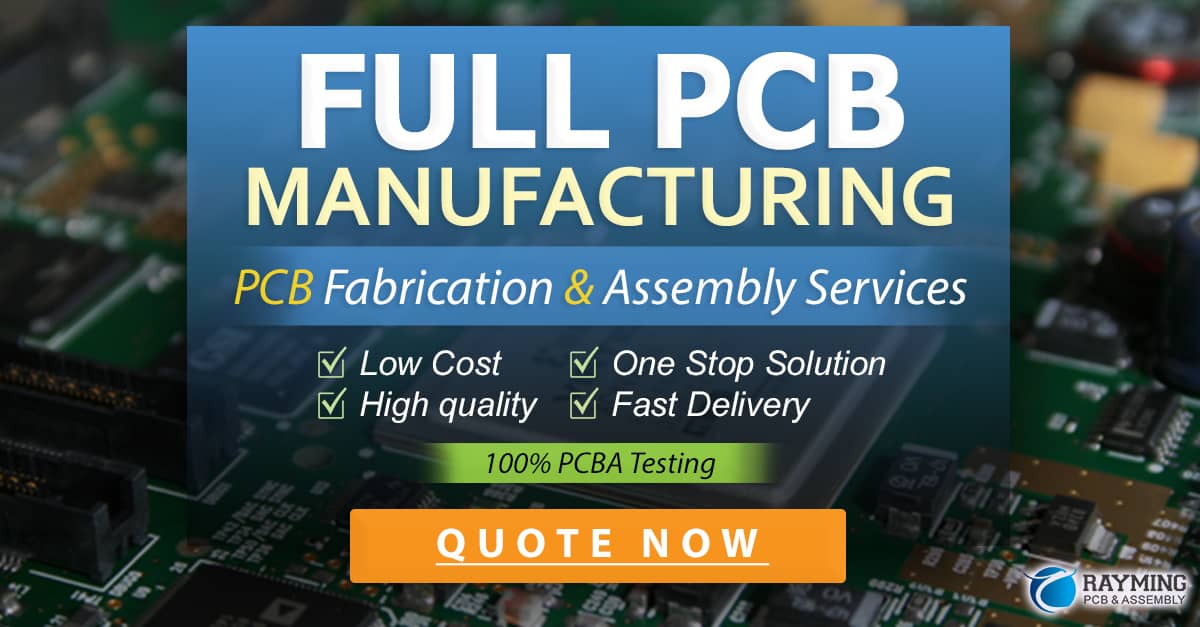
Case Studies
Case Study 1: Smart Agriculture
In this case study, a company developed an IOT device for smart agriculture that could monitor soil moisture, temperature, and nutrient levels in real-time. The device required a small, flexible PCB that could be embedded directly into the soil.
The company used additive manufacturing to create a flexible PCB with embedded sensors and communication modules. The PCB was designed to withstand harsh environmental conditions, including extreme temperatures and moisture.
The result was a highly reliable and accurate IOT device that could provide farmers with real-time data on soil conditions, enabling them to make informed decisions about irrigation and fertilization.
Case Study 2: Wearable Medical Device
In this case study, a company developed a wearable medical device that could monitor a patient’s vital signs and transmit the data to a healthcare provider in real-time. The device required a small, flexible PCB that could be worn comfortably on the patient’s skin.
The company used 3D printing to create a flexible PCB with embedded sensors and communication modules. The PCB was designed to be lightweight and comfortable to wear, while also being able to withstand the rigors of daily use.
The result was a highly accurate and reliable wearable medical device that could provide healthcare providers with real-time data on a patient’s health, enabling them to provide better care and detect potential health issues before they become serious.
Frequently Asked Questions
What is the difference between traditional PCB manufacturing and smart PCB manufacturing?
Traditional PCB manufacturing involves a series of manual processes, such as etching, drilling, and plating, to create the PCB. Smart PCB manufacturing leverages advanced technologies and processes, such as 3D printing and additive manufacturing, to create high-quality and reliable PCBs at a lower cost.
Can smart PCB manufacturing be used for high-volume production?
Yes, smart PCB manufacturing techniques can be scaled up for high-volume production. Automated inspection and testing processes can help ensure that the PCBs are of high quality and free from defects, even in high-volume production runs.
How do flexible and stretchable PCBs differ from traditional PCBs?
Flexible and stretchable PCBs are designed to bend and stretch without breaking or losing functionality. They are ideal for IOT devices that require flexibility or must conform to irregular shapes. Traditional PCBs, on the other hand, are rigid and cannot bend or stretch without breaking.
What are the benefits of using advanced materials in PCB manufacturing?
Advanced materials, such as high-temperature polymers and ceramic substrates, can be used to create PCBs that can withstand harsh environmental conditions. They can also allow for greater design flexibility and functionality, enabling the creation of more advanced and capable IOT devices.
How can automated inspection and testing improve the quality of PCBs?
Automated inspection and testing can help ensure that PCBs are of high quality and free from defects. These processes use advanced imaging and analysis techniques to detect and identify defects that may not be visible to the human eye. This can reduce the risk of defects and failures in the field and enable faster and more accurate inspection and testing.
Conclusion
IOT devices are becoming increasingly complex and sophisticated, requiring high-quality and reliable PCBs that can withstand harsh environmental conditions and enable advanced functionality. Smart PCB manufacturing techniques, such as 3D printing, additive manufacturing, and advanced materials, can help overcome the challenges of IOT-PCB manufacturing and enable the creation of high-quality and reliable PCBs at a lower cost.
By leveraging these advanced technologies and processes, companies can create IOT devices that are more reliable, accurate, and capable than ever before. As the IOT continues to grow and evolve, smart PCB manufacturing will play an increasingly important role in enabling the creation of advanced and innovative IOT devices that can transform industries and improve lives.
0 Comments