Introduction to PCB Architectures
Printed Circuit Board (PCB) architectures have evolved significantly over the years to meet the growing demands of modern electronic devices. With the increasing complexity and miniaturization of electronic components, high-density PCB Construction has become a crucial aspect of PCB design. This article explores the latest advancements in PCB architectures and their impact on high-density PCB construction.
The Need for High Density PCB Construction
The need for high-density PCB construction arises from several factors:
- Miniaturization of electronic devices
- Increased functionality and performance requirements
- Cost reduction and space optimization
- Improved signal integrity and reduced electromagnetic interference (EMI)
Traditional PCB Architectures
Before delving into the new PCB architectures, let’s briefly discuss the traditional PCB architectures that have been widely used in the industry.
Single-Layer PCBs
Single-layer PCBs consist of a single conductive layer, typically made of copper, laminated onto an insulating substrate. These PCBs are simple, cost-effective, and suitable for low-complexity circuits.
Double-Layer PCBs
Double-layer PCBs have two conductive layers, one on each side of the insulating substrate. The layers are connected through plated through-holes (PTHs). Double-layer PCBs offer increased routing flexibility and higher component density compared to single-layer PCBs.
Multi-Layer PCBs
Multi-layer PCBs consist of three or more conductive layers separated by insulating layers. The layers are interconnected using PTHs and blind or buried vias. Multi-layer PCBs provide enhanced routing capabilities, improved signal integrity, and reduced EMI.
Advanced PCB Architectures for High Density Construction
To meet the demands of high-density PCB construction, several advanced PCB architectures have emerged. These architectures leverage innovative materials, manufacturing techniques, and design strategies to achieve higher component density, improved performance, and reduced form factors.
HDI (High Density Interconnect) PCBs
HDI PCBs are characterized by fine pitch traces, small vias, and high layer counts. They enable the integration of a large number of components in a compact space. HDI PCBs utilize advanced manufacturing techniques such as microvias, sequential lamination, and blind and buried vias to achieve high density.
Advantages of HDI PCBs
- Increased component density
- Improved signal integrity
- Reduced form factor
- Enhanced thermal management
HDI PCB Design Considerations
- Via types and sizes
- Trace width and spacing
- Impedance control
- Thermal management strategies
Rigid-Flex PCBs
Rigid-flex PCBs combine rigid and flexible substrates in a single PCB Assembly. The rigid sections provide mechanical support and house the majority of the components, while the flexible sections allow for bending and folding, enabling 3D packaging and space-saving designs.
Advantages of Rigid-Flex PCBs
- Reduced form factor and weight
- Improved reliability and durability
- Elimination of connectors and cables
- Enhanced design flexibility
Rigid-Flex PCB Design Considerations
- Material selection for rigid and flexible sections
- Bend radius and bend cycle requirements
- Stiffener placement and design
- Coverlay and adhesive selection
Embedded Component PCBs
Embedded component PCBs involve the integration of passive components, such as resistors and capacitors, within the PCB substrate. This technique reduces the surface area required for component placement and improves signal integrity by minimizing the distance between components.
Advantages of Embedded Component PCBs
- Reduced board size and thickness
- Improved electrical performance
- Enhanced reliability and durability
- Simplified assembly process
Embedded Component PCB Design Considerations
- Component selection and compatibility
- Embedding process and materials
- Thermal management and heat dissipation
- Testing and inspection techniques
3D PCBs
3D PCBs, also known as multi-level PCBs or 3D molded interconnect devices (3D-MIDs), involve the creation of three-dimensional circuit structures. These PCBs utilize advanced manufacturing techniques, such as 3D printing, laser direct structuring (LDS), and two-shot molding, to create complex 3D shapes and integrate electronic components.
Advantages of 3D PCBs
- Increased design freedom and flexibility
- Reduced form factor and weight
- Integration of mechanical and electrical functions
- Improved thermal management and shielding
3D PCB Design Considerations
- 3D modeling and simulation tools
- Material selection and compatibility
- Manufacturing process and limitations
- Component placement and interconnect design
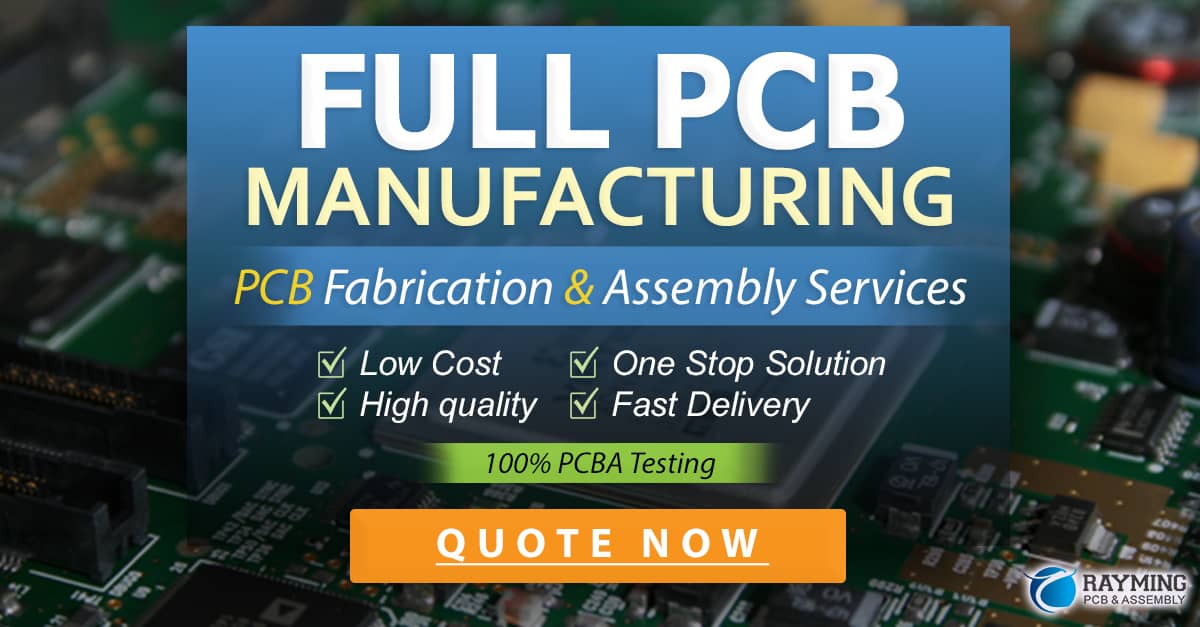
PCB Material Advancements for High Density Construction
In addition to the architectural advancements, the development of new PCB materials has played a significant role in enabling high-density PCB construction. These materials offer improved electrical, thermal, and mechanical properties, facilitating the design and manufacture of high-performance PCBs.
Low-Loss Dielectric Materials
Low-loss dielectric materials, such as polytetrafluoroethylene (PTFE), liquid crystal polymer (LCP), and hydrocarbon ceramic (HCC), offer lower dielectric constants and dissipation factors compared to traditional FR-4 materials. These properties enable faster signal propagation, reduced signal loss, and improved signal integrity, making them suitable for high-speed and high-frequency applications.
High-Tg Materials
High-Tg (glass transition temperature) materials, such as polyimide and bismaleimide triazine (BT), provide enhanced thermal stability and mechanical strength. These materials can withstand higher operating temperatures and maintain their dimensional stability during the assembly process, reducing the risk of warpage and delamination in high-density PCBs.
Thermally Conductive Materials
Thermally conductive materials, such as metal-clad PCBs (MCPCBs) and thermally enhanced laminates, offer improved heat dissipation capabilities. These materials help in managing the heat generated by high-power components and prevent thermal-related failures in high-density PCBs.
Manufacturing Techniques for High Density PCBs
The successful implementation of high-density PCB architectures relies on advanced manufacturing techniques. These techniques enable the precise fabrication of fine features, accurate layer registration, and reliable interconnections.
Laser Drilling
Laser drilling is used to create small, precise vias in high-density PCBs. It offers higher accuracy and smaller via diameters compared to mechanical drilling, enabling the creation of microvias and blind and buried vias.
Plasma Etching
Plasma etching is a dry etching process that uses ionized gases to remove unwanted copper from the PCB surface. It provides better control over the etching process, resulting in finer trace widths and spacings, and improved signal integrity.
Additive Manufacturing
Additive manufacturing techniques, such as inkjet printing and aerosol jet printing, enable the direct deposition of conductive materials onto the PCB substrate. These techniques offer the potential for creating fine-pitch traces and reducing the environmental impact of PCB manufacturing.
Design Considerations for High Density PCBs
Designing high-density PCBs requires careful consideration of various factors to ensure optimal performance, reliability, and manufacturability.
Signal Integrity Analysis
Signal integrity analysis is crucial in high-density PCB design to ensure the proper transmission of high-speed signals. It involves simulating and analyzing the behavior of signals, considering factors such as impedance matching, crosstalk, and reflections.
Thermal Management
Thermal management is critical in high-density PCBs due to the increased power density and reduced space for heat dissipation. Designers must consider thermal vias, heat spreaders, and thermal interface materials to effectively manage heat and prevent thermal-related failures.
DFM (Design for Manufacturability)
Designing for manufacturability is essential to ensure the successful fabrication and assembly of high-density PCBs. Designers must adhere to manufacturing guidelines, such as minimum trace widths, via sizes, and clearances, to avoid manufacturing issues and improve yield.
EMI/EMC Considerations
Electromagnetic interference (EMI) and electromagnetic compatibility (EMC) are important considerations in high-density PCB design. Proper grounding, shielding, and layout techniques must be employed to minimize EMI and ensure compliance with regulatory standards.
Future Trends in PCB Architectures
As technology advances and the demand for high-density PCBs continues to grow, several emerging trends are expected to shape the future of PCB architectures.
Increased Adoption of Embedded Components
The integration of embedded components is expected to become more prevalent in high-density PCB design. Advances in embedding techniques and materials will enable the incorporation of a wider range of components, including active components and sensors, within the PCB substrate.
Expansion of 3D PCB Applications
The applications of 3D PCBs are expected to expand beyond niche markets and become more mainstream. The development of advanced 3D printing technologies and the availability of new materials will drive the adoption of 3D PCBs in various industries, including automotive, aerospace, and medical devices.
Integration of PCBs with Other Technologies
The integration of PCBs with other technologies, such as flexible electronics, printed electronics, and molded interconnect devices (MIDs), will create new opportunities for high-density PCB construction. These hybrid approaches will enable the creation of complex, multifunctional structures with enhanced performance and functionality.
Frequently Asked Questions (FAQ)
1. What is the difference between HDI PCBs and traditional multi-layer PCBs?
HDI PCBs feature finer pitch traces, smaller vias, and higher layer counts compared to traditional multi-layer PCBs. They utilize advanced manufacturing techniques, such as microvias and sequential lamination, to achieve higher component density and improved signal integrity.
2. What are the benefits of using rigid-flex PCBs in high-density PCB construction?
Rigid-flex PCBs offer several benefits in high-density PCB construction, including reduced form factor and weight, improved reliability and durability, elimination of connectors and cables, and enhanced design flexibility. They enable 3D packaging and space-saving designs by combining rigid and flexible substrates in a single PCB assembly.
3. How do embedded component PCBs improve the performance of high-density PCBs?
Embedded component PCBs improve the performance of high-density PCBs by reducing the surface area required for component placement and minimizing the distance between components. This results in reduced board size and thickness, improved electrical performance, enhanced reliability and durability, and a simplified assembly process.
4. What are the challenges associated with designing and manufacturing 3D PCBs?
Designing and manufacturing 3D PCBs present several challenges, including the need for specialized 3D modeling and simulation tools, material selection and compatibility issues, limitations in manufacturing processes, and complex component placement and interconnect design. Overcoming these challenges requires expertise in 3D design, advanced manufacturing techniques, and close collaboration between designers and manufacturers.
5. How do low-loss dielectric materials contribute to the performance of high-density PCBs?
Low-loss dielectric materials, such as PTFE, LCP, and HCC, offer lower dielectric constants and dissipation factors compared to traditional FR-4 materials. These properties enable faster signal propagation, reduced signal loss, and improved signal integrity, making them suitable for high-speed and high-frequency applications in high-density PCBs.
Conclusion
The advancements in PCB architectures and materials have revolutionized the field of high-density PCB construction. HDI PCBs, rigid-flex PCBs, embedded component PCBs, and 3D PCBs offer unique advantages in terms of component density, signal integrity, form factor, and design flexibility. The development of low-loss dielectric materials, high-Tg materials, and thermally conductive materials has further enhanced the performance and reliability of high-density PCBs.
To successfully implement these advanced PCB architectures, designers must consider various factors, including signal integrity, thermal management, manufacturability, and EMI/EMC. The future of PCB architectures is expected to witness increased adoption of embedded components, expansion of 3D PCB applications, and integration with other technologies.
As the demand for high-density PCBs continues to grow, staying informed about the latest advancements in PCB architectures and materials is crucial for designers, manufacturers, and stakeholders in the electronics industry. By leveraging these advancements, companies can develop innovative, high-performance electronic products that meet the ever-increasing demands of the market.
0 Comments