What are Metal-Core PCBs?
Metal-core printed circuit boards (MCPCBs) are PCBs that have a metal base or substrate, typically aluminum, instead of the traditional FR-4 material. The metal core provides excellent thermal conductivity, allowing for efficient heat dissipation from high-power components mounted on the board. This makes MCPCBs ideal for applications that generate significant amounts of heat, such as:
- Power electronics
- LED lighting
- Automotive electronics
- High-performance computing
MCPCBs consist of three main layers:
- The top insulating layer, which is a thin dielectric material
- The metal core, usually made of aluminum
- The bottom layer, which can be another insulating layer or a solderable surface for component attachment
Advantages of Metal-Core PCBs
Metal-core PCBs offer several advantages over traditional FR-4 PCBs:
-
Enhanced thermal management: The metal core provides a low-resistance thermal path, allowing for efficient heat dissipation from power-hungry components. This helps to maintain optimal operating temperatures, improving the performance and longevity of the components.
-
Improved reliability: By keeping components cooler, MCPCBs reduce the risk of thermal stress and damage, leading to improved system reliability and longer product lifespans.
-
Reduced size and weight: MCPCBs enable the design of more compact and lightweight electronic systems, as the metal core can serve as both a heat sink and a structural support.
-
Cost-effective: For high-power applications, MCPCBs can be a more cost-effective solution compared to using separate PCBs and heat sinks.
Choosing the Right Metal-Core PCB Manufacturer
When selecting a metal-core PCB manufacturer, consider the following factors:
-
Experience and expertise: Look for a manufacturer with a proven track record in producing high-quality MCPCBs. They should have experience working with a variety of metal core materials and dielectric layers.
-
Manufacturing capabilities: Ensure that the manufacturer has the necessary equipment and processes in place to produce MCPCBs that meet your specific requirements, such as layer count, minimum feature size, and surface finish.
-
Quality control: A reputable MCPCB manufacturer should have robust quality control procedures in place to ensure consistent product quality and reliability.
-
Customer support: Choose a manufacturer that offers excellent customer support, including assistance with design review, prototyping, and troubleshooting.
-
Certifications: Look for manufacturers with relevant industry certifications, such as ISO 9001, ISO 14001, and UL listing, which demonstrate their commitment to quality and environmental responsibility.
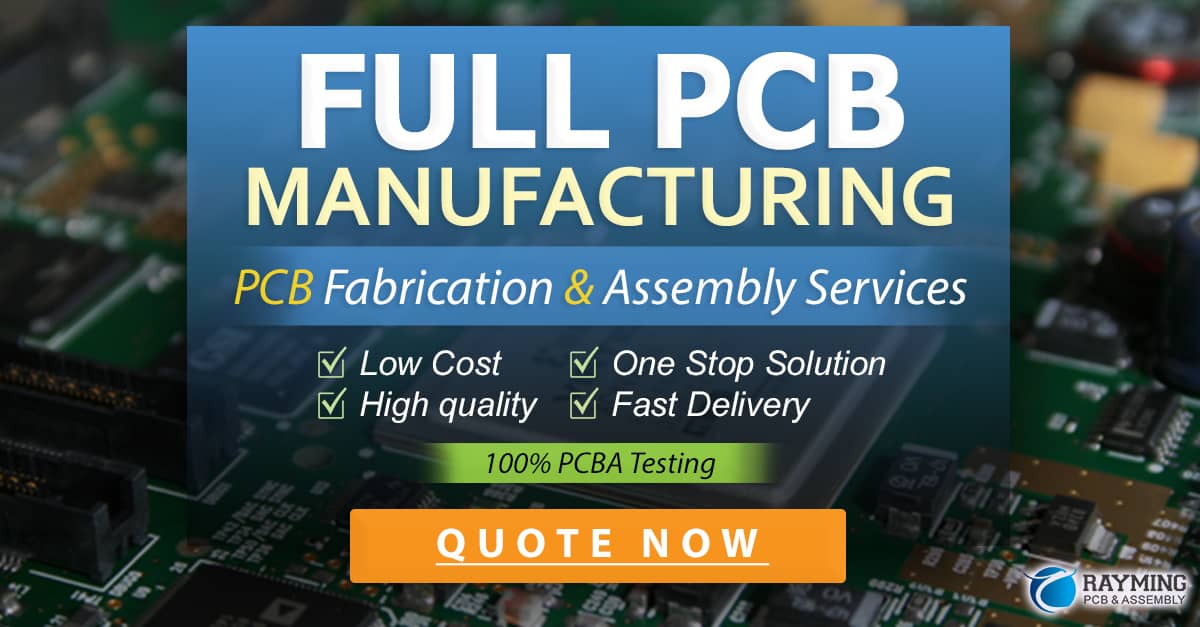
Top Metal-Core PCB Manufacturers & Fabricators
Here are some of the leading metal-core PCB manufacturers and fabricators:
- TT Electronics Power and Hybrid
- Headquarters: Bedlington, United Kingdom
- Website: www.ttelectronics.com
-
Specialties: High-power MCPCBs, thick film substrates, and advanced thermal management solutions
-
Millennium Circuits Limited (MCL)
- Headquarters: Harrisburg, Pennsylvania, USA
- Website: www.mclpcb.com
-
Specialties: Quick-turn prototypes, high-volume production, and advanced PCB technologies, including MCPCBs
-
Epec Engineered Technologies
- Headquarters: New Bedford, Massachusetts, USA
- Website: www.epectec.com
-
Specialties: Custom MCPCBs, flex and rigid-flex PCBs, and PCB assemblies
-
Shenzhen FastPCBA Circuit Tech
- Headquarters: Shenzhen, China
- Website: www.pcbmake.com
-
Specialties: Rapid prototyping, high-volume production, and a wide range of PCB types, including MCPCBs
-
P.C.B. Unlimited
- Headquarters: St. Paul, Minnesota, USA
- Website: www.pcbunlimited.com
- Specialties: Custom PCB fabrication, including MCPCBs, flex, and rigid-flex PCBs
Here’s a table comparing the key features of these metal-core PCB manufacturers:
Manufacturer | Headquarters | Specialties | Certifications |
---|---|---|---|
TT Electronics Power and Hybrid | United Kingdom | High-power MCPCBs, thick film substrates, advanced thermal management | ISO 9001, ISO 14001, UL |
Millennium Circuits Limited | USA | Quick-turn prototypes, high-volume production, advanced PCB technologies | ISO 9001, UL, ITAR |
Epec Engineered Technologies | USA | Custom MCPCBs, flex and rigid-flex PCBs, PCB assemblies | ISO 9001, ISO 13485, ITAR |
Shenzhen FastPCBA Circuit Tech | China | Rapid prototyping, high-volume production, wide range of PCB types | ISO 9001, UL, RoHS |
P.C.B. Unlimited | USA | Custom PCB fabrication, including MCPCBs, flex, and rigid-flex PCBs | ISO 9001, ITAR |
Choosing the Right Metal Core Material
The choice of metal core material depends on the specific requirements of your application. The most common metal core materials used in MCPCBs are:
-
Aluminum: Aluminum is the most widely used metal core material due to its excellent thermal conductivity, low cost, and ease of machining. It is suitable for most MCPCB applications.
-
Copper: Copper has even better thermal conductivity than aluminum but is more expensive and heavier. It is used in high-performance applications that require the best possible thermal management.
-
Alloys: Some manufacturers offer MCPCBs with metal cores made of aluminum or copper alloys, which can provide specific advantages, such as improved strength or corrosion resistance.
When selecting the metal core material, consider factors such as:
- Thermal conductivity
- Coefficient of thermal expansion (CTE)
- Weight
- Cost
- Machinability
- Corrosion resistance
Dielectric Layer Materials
The dielectric layer is a thin insulating material that sits between the metal core and the copper circuit layer. The choice of dielectric material is crucial for the performance and reliability of the MCPCB. Some common dielectric materials used in MCPCBs include:
-
Epoxy: Epoxy-based dielectrics are the most common type used in MCPCBs. They offer good thermal conductivity, adhesion, and electrical insulation properties.
-
Polyimide: Polyimide dielectrics are used in high-temperature applications, as they can withstand temperatures up to 250°C. They also offer excellent chemical resistance and mechanical stability.
-
Ceramic: Ceramic dielectrics, such as aluminum nitride (AlN) and boron nitride (BN), provide the highest thermal conductivity among dielectric materials. They are used in high-power, high-temperature applications that demand the best possible thermal management.
When choosing a dielectric material, consider its thermal conductivity, dielectric strength, thermal stability, and CTE compatibility with the metal core and copper layers.
Design Considerations for Metal-Core PCBs
Designing MCPCBs requires a different approach compared to traditional FR-4 PCBs. Here are some key design considerations:
-
Thermal management: The primary purpose of using an MCPCB is to efficiently dissipate heat from power components. Ensure that the layout and component placement optimize thermal transfer to the metal core.
-
Insulation and clearances: The thin dielectric layer in MCPCBs requires careful consideration of insulation and clearance requirements. Follow the manufacturer’s guidelines for minimum insulation thickness and clearances between the metal core and copper layers.
-
CTE mismatch: The different CTEs of the metal core, dielectric layer, and copper layers can lead to stress and warpage during temperature changes. Use appropriate design techniques, such as adding thermal vias and selecting compatible materials, to minimize CTE mismatch issues.
-
Vias and plated through-holes: Vias and plated through-holes in MCPCBs require special attention, as the metal core can affect their thermal and electrical properties. Work with your manufacturer to ensure that vias and PTHs are designed and fabricated correctly for your specific application.
-
Soldermask and finishes: The choice of soldermask and surface finish can impact the thermal performance of the MCPCB. Discuss the options with your manufacturer and select the most appropriate combination for your design.
Assembly Considerations for Metal-Core PCBs
Assembling components on MCPCBs requires some special considerations compared to traditional PCBs:
-
Soldering temperature: The metal core in MCPCBs can act as a heat sink during soldering, which can affect the soldering process. Use appropriate soldering techniques and temperature profiles to ensure proper component attachment.
-
Thermal interface materials: To maximize thermal transfer from components to the metal core, use thermal interface materials (TIMs) such as thermal greases, pads, or adhesives. Select TIMs with the appropriate thermal conductivity and thickness for your application.
-
Mechanical attachment: In some cases, components may need to be mechanically attached to the MCPCB for better thermal contact or structural support. Use appropriate fasteners and techniques to ensure secure attachment without damaging the board or components.
Frequently Asked Questions (FAQ)
1. What is the typical thermal conductivity of aluminum used in MCPCBs?
The thermal conductivity of aluminum used in MCPCBs is typically around 150-200 W/mK, which is significantly higher than the thermal conductivity of FR-4 (around 0.3 W/mK).
2. Can MCPCBs be used in high-voltage applications?
Yes, MCPCBs can be used in high-voltage applications, provided that the dielectric layer is properly designed and fabricated to withstand the required voltage levels. Consult with your manufacturer to ensure that the MCPCB meets your specific high-voltage requirements.
3. Are MCPCBs more expensive than traditional FR-4 PCBs?
In general, MCPCBs are more expensive than FR-4 PCBs due to the additional materials and processing steps involved. However, for high-power applications that require efficient thermal management, MCPCBs can be a more cost-effective solution compared to using separate PCBs and heat sinks.
4. Can MCPCBs be manufactured with multiple copper layers?
Yes, MCPCBs can be manufactured with multiple copper layers, just like traditional PCBs. However, the number of layers may be limited compared to FR-4 PCBs due to the specific fabrication processes and materials used in MCPCBs.
5. How do I select the right metal core thickness for my application?
The choice of metal core thickness depends on several factors, including the power dissipation requirements, the size and weight constraints of your application, and the desired thermal performance. Thicker metal cores provide better thermal conductivity but also increase the weight and cost of the MCPCB. Consult with your manufacturer to determine the optimal metal core thickness for your specific application.
Conclusion
Metal-core PCBs offer a powerful solution for applications that require efficient thermal management and high reliability. By understanding the key features, materials, and design considerations of MCPCBs, you can select the right manufacturer and fabricate boards that meet the specific needs of your application. When designing and assembling MCPCBs, work closely with your chosen manufacturer to ensure optimal performance and long-term reliability.
0 Comments