Introduction
Printed circuit boards (PCBs) are an integral part of medical devices and equipment. From MRI machines to pacemakers, PCBs enable the complex electronics and circuitry that allow these devices to function. However, medical PCB assembly has unique requirements that demand special considerations compared to PCBs designed for other industries. This guide will provide a comprehensive overview of medical PCB assembly, including design, manufacturing, testing, and regulatory compliance. With the right approach, medical device companies can ensure their PCB assemblies meet the highest standards for quality, reliability, and safety.
Medical PCB Design Considerations
The design stage lays the foundation for the rest of the PCB assembly process. Here are some key factors medical device engineers should consider when designing PCBs:
Component Selection
The components used on the board must be biocompatible and meet regulatory body approvals. Engineers should select components from approved vendors and verify sourcing.
Layout
A well-designed layout ensures proper functioning, assembly, and serviceability. Important factors include component spacing, trace width, layer stacking, and accessibility.
Specifications
Medical PCBs have tight tolerance requirements for factors like temperature rating, shock/vibration resistance, and impedance control. These specifications must be defined from the start.
Safety and Redundancy
Safety and redundancy should be built into the design through measures like circuit protection, fail-safe modes, and backup sub-systems. This prevents device failure.
EMI/EMC Control
Electromagnetic interference (EMI) can impact device performance. Proper grounding, shielding, filtering, and PCB coating help control electromagnetic compatibility (EMC).
Miniaturization
Many medical devices require compact PCBs. Engineers must shrink board size while maintaining spacing, trace widths, and adequate heat dissipation.
Medical PCB Manufacturing Process
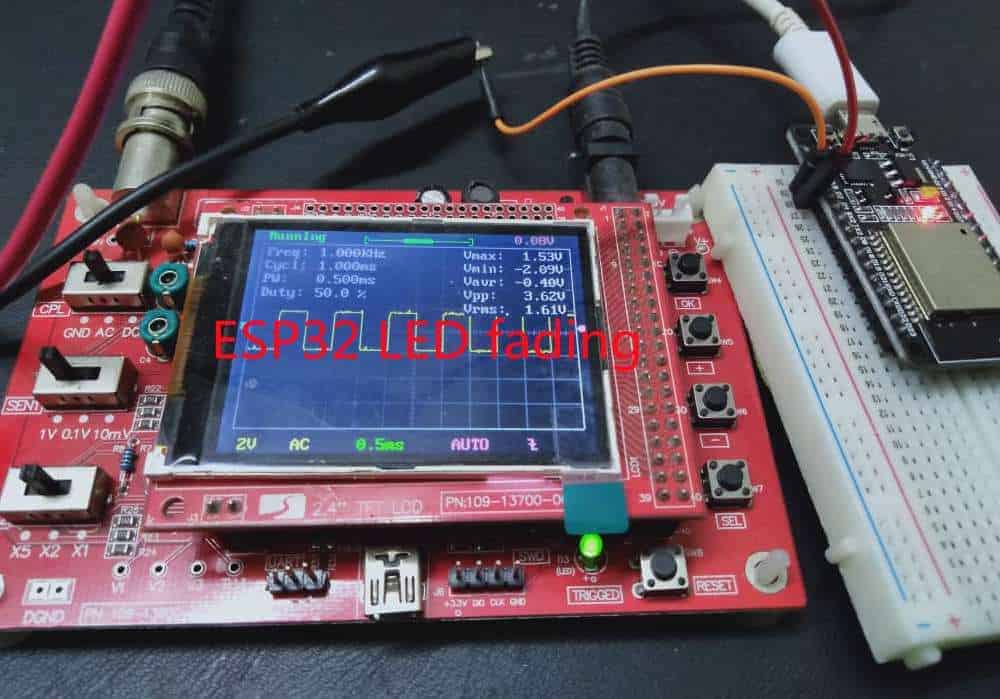
Once the board design is finalized, it moves into manufacturing. Here is an overview of the medical PCB assembly process:
Prototyping
Initial prototypes are built to test design functionality before full production. Any issues found can be addressed with design modifications.
Sourcing Materials
The PCB manufacturer sources all required materials and components approved for medical use per industry standards like ISO 13485.
Board Fabrication
Fabrication includes processes like etching, multi-layer lamination, drilling, plating, masking and patterning to construct the bare PCB.
Component Assembly
Components are precisely assembled on the board by techniques like soldering (SMT and through-hole), conductive adhesive bonding, and wire bonding.
Software Loading
Any required firmware or software is loaded onto chips and memory devices on the board.
Testing and Inspection
Poka-yoke error proofing, optical inspection, x-ray, functional testing, environmental stress screening, and other checks validate assembly quality.
Final Finishing
This includes conformal coating for water resistance and EMI control, silkscreen printing of reference designators, solder masking, and edge trimming.
Testing Medical PCB Assemblies
Testing is woven throughout the assembly process and confirms the product meets specifications. Some key testing aspects include:
Materials Analysis
Raw PCB materials and component leads are tested to verify purity and consistency.
In-Circuit Testing
Validates proper connections between components, and checks for shorts, opens, and proper values.
Flying Probe
Checks continuity between nodes, performing rapid analog and digital circuit tests through floating probes.
Boundary Scan
Tests interconnects between components with boundary scan cells that surround key integrated circuits.
X-Ray Inspection
Used to detect defects like insufficient solder, cracks, or bridging under components. Helpful for double-sided boards.
Functional Testing
Confirms overall board performance under operating loads and test suites that simulate field conditions.
Burn-in Testing
Units stressed for an extended time at high temperatures to force latent defects to surface.
EMC/EMI Testing
Validates the board’s electromagnetic emissions are within limits, and its immunity to interference.
Regulatory Considerations for Medical PCBs
Medical devices sold worldwide must meet national and international regulations. Some key requirements related to PCB assembly include:
ISO 13485
Covers quality management system compliance for medical device production. Includes supplier controls.
21 CFR 820
FDA standard for medical device quality system regulation in the US. Covers PCB traceability and documentation.
IEC 60601
International standard for medical electrical equipment safety including PCB layout considerations.
RoHS
Restriction of Hazardous Substances directive limits lead, cadmium, mercury, hexavalent chromium, PBB, and PBDE.
CE Marking
Mandatory for medical devices sold in the European Union. Confirms compliance with health, safety, and environmental protection standards.
Working closely with a contract manufacturer experienced in medical devices is key to successfully navigating these various regulations.
Finding the Right Medical PCB Assembly Partner
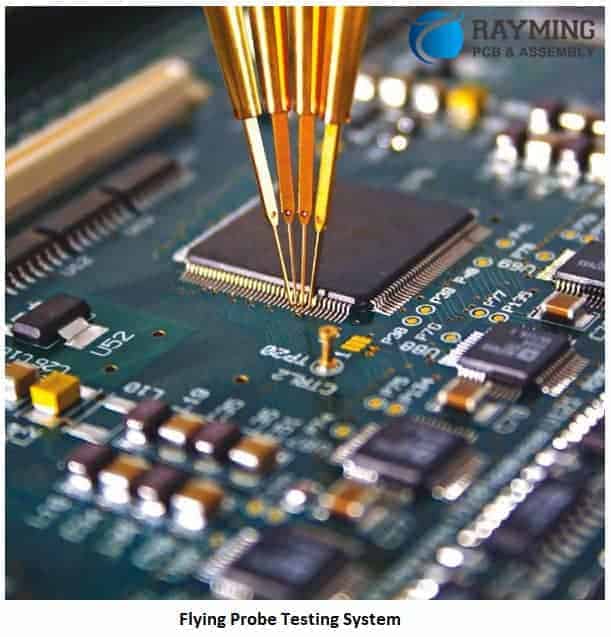
Choosing the right contract manufacturer for medical PCB assembly ensures regulatory compliance, quality manufacturing, and solid support through the product lifecycle. Key factors to consider include:
- Specialization in medical – Seek out manufacturers who focus specifically on medical devices rather than general consumer electronics. They have the right protocols and quality systems in place.
- Proven experience – Look for demonstrated experience building PCBs for medical OEMs, with case studies and customer reviews that reinforce capabilities.
- Certifications – Leading manufacturers have ISO 13485 certification and FDA registration as a baseline indicator of their capabilities.
- Capabilities – Partner with a manufacturer that offers the range of specialized services needed for medical PCBs like design support, rapid prototyping, advanced testing, and documentation management.
- Global supply chain – For international device companies, a contract manufacturer with a global supply chain can support launching globally compliant products efficiently.
Taking the time to find the right medical PCB assembly partner ensures achieving regulatory, quality, and reliability goals while reducing risk and time-to-market.
Frequently Asked Questions on Medical PCB Assembly
##Q: Why are medical PCBs held to higher standards than consumer electronics PCBs?
Medical devices have direct implications for human health and safety, so PCBs used in medical equipment must meet more stringent requirements. PCB failures can’t be tolerated when life-critical devices are involved. Higher standards help ensure consistent performance and reliability.
##Q: How are PCB components and materials verified for medical applications?
All components and materials are sourced from trusted vendors who supply parts specifically approved for medical use. This includes verification through compliance documentation and rigorous testing of leads/connections.
##Q: What design techniques help prevent electromagnetic interference with medical devices?
Proper grounding, shielding around sensitive components, strategic trace routing, noise filtering, board coating and stringent EMI/EMC testing all help minimize interference.
##Q: Why is ISO 13485 certification important for medical PCB assembly?
ISO 13485 verifies the manufacturer has a comprehensive quality management system in place specifically designed to ensure stringent regulatory compliance for medical device production.
##Q: How does a contract manufacturer ensure PCB traceability in case a recall is required?
Through production documentation like lot logs and shop floor data, as well as marking products with serial numbers and date stamps. This allows tracing units back through the process.
0 Comments