Introduction to LED PCBs
Light-emitting diode (LED) printed circuit boards (PCBs) are specialized boards designed to power and control LED lights. LEDs are highly efficient, long-lasting, and versatile light sources used in a wide range of applications, from general lighting to automotive, displays, and more. Designing an LED PCB requires careful consideration of various factors to ensure optimal performance, reliability, and longevity.
Key Components of an LED PCB
An LED PCB typically consists of the following main components:
- LEDs: The light-emitting diodes themselves, which convert electrical energy into light.
- Current-limiting resistors: Resistors that limit the current flowing through the LEDs to prevent damage.
- Driver IC: An integrated circuit that controls the power and dimming of the LEDs.
- Connectors: Used to connect the PCB to the power source and other components.
- Heat sink: A component that dissipates heat generated by the LEDs to prevent overheating.
Factors to Consider in LED PCB Design
1. LED Type and Arrangement
The type and arrangement of LEDs on the PCB are crucial factors in the design process. Different LED types have varying forward voltages, current requirements, and optical characteristics. Some common LED types include:
- Through-hole LEDs: Traditional LEDs with long leads that are inserted through holes in the PCB and soldered on the opposite side.
- Surface-mount LEDs: Smaller LEDs that are mounted directly onto the PCB surface, allowing for higher density and automated assembly.
- High-power LEDs: LEDs that require higher current and generate more heat, often used in lighting applications.
The arrangement of LEDs on the PCB depends on the desired illumination pattern, uniformity, and total light output. LEDs can be arranged in various configurations, such as:
- Series: LEDs connected in a single string, sharing the same current.
- Parallel: LEDs connected in multiple strings, each with its own current path.
- Matrix: LEDs arranged in a grid pattern, allowing for individual control of each LED.
2. Current and Voltage Requirements
LEDs are current-driven devices, meaning that the current flowing through them determines their brightness and performance. Each LED has a specific forward voltage (Vf) and maximum current rating. To ensure proper operation and prevent damage, the PCB design must include current-limiting resistors or a constant-current driver IC.
The value of the current-limiting resistor (R) can be calculated using the following formula:
R = (Vs – Vf) / If
Where:
– Vs is the supply voltage
– Vf is the LED’s forward voltage
– If is the desired forward current
For example, if the supply voltage is 5V, the LED’s forward voltage is 3.2V, and the desired forward current is 20mA, the resistor value would be:
R = (5V – 3.2V) / 0.02A = 90Ω
3. Thermal Management
LEDs generate heat during operation, which can impact their performance, color consistency, and lifespan. Proper thermal management is essential to ensure that the LEDs operate within their specified temperature range. Some strategies for managing heat in LED PCBs include:
- Using a metal-core PCB (MCPCB): MCPCBs have a metal substrate, typically aluminum, that acts as a built-in heat sink, efficiently dissipating heat from the LEDs.
- Incorporating thermal vias: Thermal vias are small holes filled with thermally conductive material that transfer heat from the LED pads to the other layers of the PCB.
- Attaching external heat sinks: For high-power LEDs or dense LED arrays, external heat sinks can be attached to the PCB to further enhance heat dissipation.
4. Power and Ground Planes
To ensure stable power delivery and minimize voltage drops, LED PCBs should incorporate dedicated power and ground planes. These planes are typically made of copper and cover a large area of the PCB, providing a low-impedance path for current flow. The thickness of the copper planes should be sufficient to handle the expected current without excessive voltage drop.
5. Layout and Routing
The layout and routing of an LED PCB can significantly impact its performance and reliability. Some key considerations include:
- Minimizing trace lengths: Shorter traces reduce resistance and inductance, minimizing voltage drops and electromagnetic interference (EMI).
- Balancing current paths: Ensure that the current paths to each LED are as symmetrical as possible to maintain consistent brightness and color across the array.
- Avoiding sharp bends: Sharp bends in traces can cause signal reflections and increase EMI. Use gentle curves or 45-degree angles instead.
- Providing sufficient clearance: Ensure adequate clearance between traces, components, and the board edge to prevent short circuits and facilitate assembly.
6. Dimming and Control
Many LED applications require dimming or dynamic control of the light output. There are several methods for dimming LEDs, including:
- Pulse-width modulation (PWM): PWM involves rapidly switching the LEDs on and off at a high frequency, with the duty cycle determining the perceived brightness. PWM dimming provides a wide dimming range and maintains color consistency.
- Analog dimming: Analog dimming involves reducing the current flowing through the LEDs to lower their brightness. This method is simpler to implement but may result in color shifts at lower brightness levels.
- Digital addressable LEDs: Some LEDs, such as WS2812B or APA102, have built-in control chips that allow individual control of each LED in a string using a digital protocol.
The choice of dimming method depends on the specific application requirements, desired dimming performance, and control interface.
LED PCB Assembly Considerations
1. Solder Mask and Silkscreen
A solder mask is a protective layer applied to the PCB surface that prevents solder bridges and short circuits during assembly. For LED PCBs, it’s important to choose a solder mask color that enhances the reflectivity and light output of the LEDs. White solder masks are commonly used for their high reflectivity.
A silkscreen is a printed layer on the PCB that provides component labels, orientation marks, and other visual indicators. Ensure that the silkscreen does not obstruct the LED lenses or interfere with the light output.
2. Soldering Techniques
The choice of soldering technique depends on the LED type and PCB design. Through-hole LEDs are typically hand-soldered or wave-soldered, while surface-mount LEDs are reflow-soldered using solder paste and a reflow oven. Proper solder joint formation is crucial for electrical and mechanical integrity.
3. Quality Control and Testing
After assembly, LED PCBs should undergo thorough quality control and testing to ensure proper functionality and performance. Some common tests include:
- Visual inspection: Check for proper component placement, solder joint quality, and any visible defects.
- Electrical testing: Verify the forward voltage, current consumption, and dimming functionality of each LED.
- Photometric testing: Measure the light output, color temperature, and uniformity of the LED array using specialized equipment.
- Burn-in testing: Subject the PCB to extended operation at elevated temperatures to identify any early failures or performance degradation.
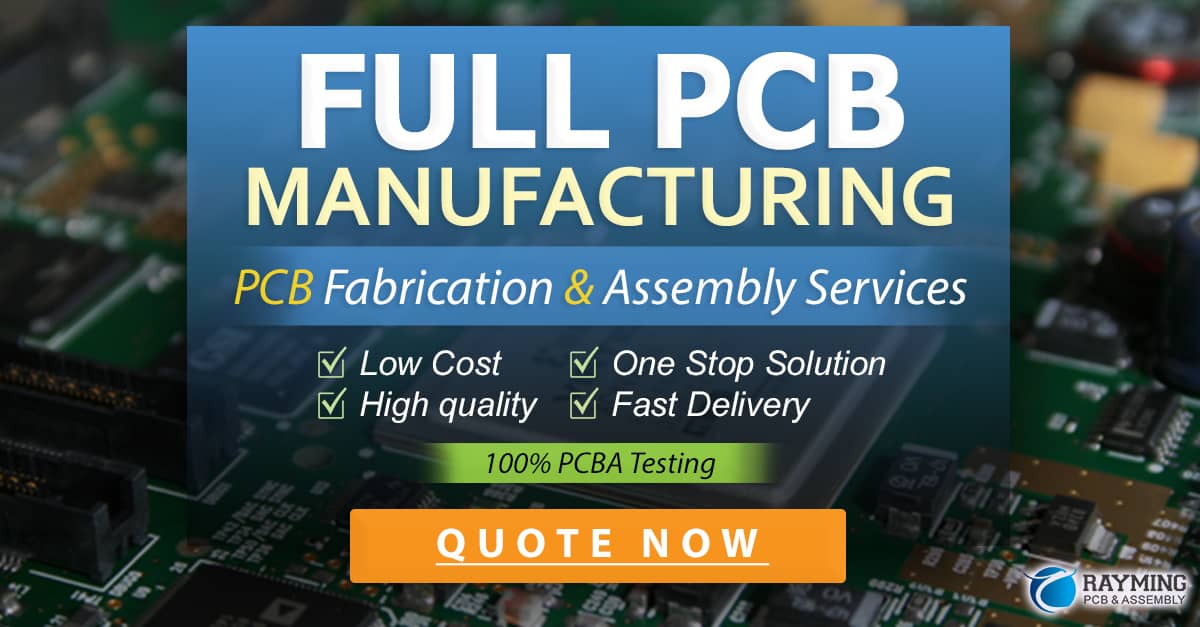
FAQ
1. What is the difference between through-hole and surface-mount LEDs?
Through-hole LEDs have long leads that are inserted through holes in the PCB and soldered on the opposite side, while surface-mount LEDs are smaller and are mounted directly onto the PCB surface. Surface-mount LEDs allow for higher density and automated assembly, while through-hole LEDs are more suitable for hand soldering and some high-power applications.
2. How do I choose the right current-limiting resistor for my LEDs?
To choose the right current-limiting resistor, you need to know the supply voltage, the LED’s forward voltage, and the desired forward current. Use the formula R = (Vs – Vf) / If to calculate the resistor value, where R is the resistor value, Vs is the supply voltage, Vf is the LED’s forward voltage, and If is the desired forward current.
3. What is a metal-core PCB, and when should I use one?
A metal-core PCB (MCPCB) has a metal substrate, typically aluminum, that acts as a built-in heat sink. MCPCBs are used in applications where efficient heat dissipation is crucial, such as high-power LED lighting or dense LED arrays. The metal substrate helps transfer heat away from the LEDs, maintaining their performance and longevity.
4. What is the difference between PWM and analog dimming for LEDs?
Pulse-width modulation (PWM) dimming involves rapidly switching the LEDs on and off at a high frequency, with the duty cycle determining the perceived brightness. PWM dimming provides a wide dimming range and maintains color consistency. Analog dimming, on the other hand, involves reducing the current flowing through the LEDs to lower their brightness. Analog dimming is simpler to implement but may result in color shifts at lower brightness levels.
5. Why is thermal management important in LED PCB design?
Thermal management is crucial in LED PCB design because LEDs generate heat during operation, which can impact their performance, color consistency, and lifespan. Proper thermal management, through techniques such as using metal-core PCBs, thermal vias, or external heat sinks, ensures that the LEDs operate within their specified temperature range, maintaining optimal performance and reliability.
Conclusion
Designing an LED PCB requires careful consideration of various factors, including LED type and arrangement, current and voltage requirements, thermal management, power and ground planes, layout and routing, dimming and control, and assembly considerations. By understanding and addressing these factors, engineers can create LED PCBs that deliver optimal performance, reliability, and longevity in a wide range of applications.
As LED technology continues to evolve, with advancements in efficiency, color quality, and control capabilities, the importance of well-designed LED PCBs will only continue to grow. By staying up-to-date with the latest design techniques and best practices, engineers can create LED PCBs that push the boundaries of illumination and enable new, innovative applications.
Factor | Considerations |
---|---|
LED Type and Arrangement | – Through-hole, surface-mount, or high-power LEDs – Series, parallel, or matrix arrangement |
Current and Voltage Requirements | – Forward voltage (Vf) and maximum current rating – Current-limiting resistors or constant-current driver IC |
Thermal Management | – Metal-core PCB (MCPCB) – Thermal vias – External heat sinks |
Power and Ground Planes | – Dedicated copper planes for stable power delivery – Sufficient thickness to handle expected current |
Layout and Routing | – Minimizing trace lengths – Balancing current paths – Avoiding sharp bends – Providing sufficient clearance |
Dimming and Control | – Pulse-width modulation (PWM) – Analog dimming – Digital addressable LEDs |
Assembly Considerations | – Solder mask color for reflectivity – Silkscreen placement – Soldering techniques (hand, wave, or reflow) |
Quality Control and Testing | – Visual inspection – Electrical testing – Photometric testing – Burn-in testing |
By addressing these factors and following best practices in LED PCB design, engineers can create efficient, reliable, and high-performing LED systems for a wide range of applications.
0 Comments