Introduction to LDI in PCB Manufacturing
Laser Direct Imaging (LDI) is a state-of-the-art technology that has revolutionized the printed circuit board (PCB) manufacturing industry. This innovative process uses a high-powered laser to directly image the circuit pattern onto the PCB substrate, eliminating the need for traditional photolithography processes that involve masks and exposure units. LDI offers numerous advantages over conventional methods, including higher precision, improved reliability, and faster production times.
In this comprehensive article, we will delve into the world of LDI and explore its role in PCB manufacturing. We will discuss the principles behind LDI technology, its benefits, and its applications in various industries. Additionally, we will compare LDI with traditional PCB manufacturing methods and examine the future trends and developments in this field.
How Does Laser Direct Imaging Work?
The LDI Process
Laser Direct Imaging is a digital imaging process that uses a high-powered laser to directly transfer the circuit pattern onto the PCB substrate. The process begins with the creation of a digital file containing the circuit design. This file is then loaded into the LDI machine, which uses a precision laser to expose the desired pattern onto the photoresist-coated PCB substrate.
The LDI machine typically consists of the following components:
- Laser source: A high-powered laser, usually an ultraviolet (UV) laser, is used to expose the photoresist.
- Optics system: A series of lenses and mirrors is used to focus and direct the laser beam onto the PCB substrate.
- Scanning system: A high-precision scanning system is employed to move the laser beam across the PCB substrate, exposing the desired pattern.
- Substrate handling system: An automated handling system is used to load and unload the PCB substrates into the LDI machine.
Advantages of LDI over Traditional PCB Manufacturing Methods
Laser Direct Imaging offers several advantages over traditional PCB manufacturing methods, such as photolithography and screen printing. Some of the key benefits of LDI include:
- Higher resolution and accuracy: LDI can achieve resolutions as high as 25 microns, enabling the production of ultra-fine pitch components and high-density interconnects (HDI).
- Improved registration and alignment: The digital nature of LDI ensures perfect registration and alignment between layers, reducing the risk of misalignment and improving overall quality.
- Faster production times: LDI eliminates the need for masks and exposure units, reducing setup times and enabling faster overall production.
- Reduced environmental impact: LDI uses less chemicals and generates less waste compared to traditional methods, making it a more environmentally friendly option.
- Cost-effectiveness: Although the initial investment in LDI equipment may be higher, the long-term cost savings from reduced material usage, faster production times, and improved yield make it a cost-effective solution.
Applications of LDI in Various Industries
Laser Direct Imaging has found applications in various industries due to its ability to produce high-quality, high-density PCBs. Some of the key industries that have adopted LDI technology include:
- Consumer electronics: LDI is widely used in the production of PCBs for smartphones, tablets, laptops, and other consumer electronic devices.
- Automotive: The increasing complexity of automotive electronics, such as advanced driver assistance systems (ADAS) and infotainment systems, has driven the adoption of LDI in the automotive industry.
- Aerospace and defense: LDI’s ability to produce high-density, high-reliability PCBs makes it ideal for aerospace and defense applications, where performance and durability are critical.
- Medical devices: The medical device industry requires PCBs with high precision and reliability, making LDI a preferred choice for medical device manufacturers.
- Industrial automation: As industrial automation systems become more complex and interconnected, LDI has become essential for producing the high-density PCBs required for these applications.
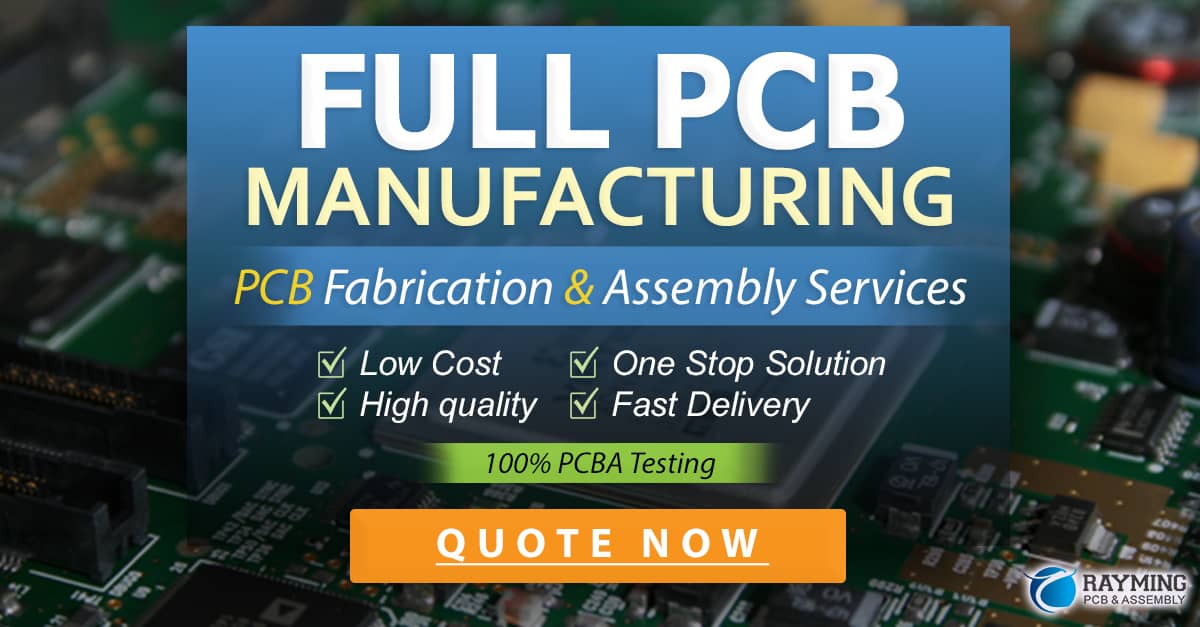
Future Trends and Developments in LDI Technology
As the demand for high-density, high-performance PCBs continues to grow, LDI technology is expected to evolve and improve. Some of the future trends and developments in LDI include:
- Higher resolutions: LDI machines are expected to achieve even higher resolutions, enabling the production of ultra-fine pitch components and HDI PCBs.
- Faster production speeds: Advances in laser technology and scanning systems are expected to further increase the production speeds of LDI machines.
- Integration with other technologies: LDI is likely to be integrated with other advanced technologies, such as additive manufacturing and embedded components, to create more complex and innovative PCB designs.
- Improved software and automation: The development of more sophisticated software and automation systems will streamline the LDI process, reducing human error and improving overall efficiency.
Frequently Asked Questions (FAQ)
-
What is Laser Direct Imaging (LDI)?
Laser Direct Imaging is a digital imaging process that uses a high-powered laser to directly transfer the circuit pattern onto the PCB substrate, eliminating the need for traditional photolithography processes that involve masks and exposure units. -
What are the advantages of LDI over traditional PCB manufacturing methods?
LDI offers several advantages over traditional methods, including higher resolution and accuracy, improved registration and alignment, faster production times, reduced environmental impact, and cost-effectiveness. -
What industries use LDI technology for PCB manufacturing?
LDI technology is used in various industries, including consumer electronics, automotive, aerospace and defense, medical devices, and industrial automation. -
What are the key components of an LDI machine?
The key components of an LDI machine include a laser source, optics system, scanning system, and substrate handling system. -
What are the future trends and developments expected in LDI technology?
Future trends and developments in LDI technology include higher resolutions, faster production speeds, integration with other technologies, and improved software and automation.
Conclusion
Laser Direct Imaging has emerged as a game-changing technology in the PCB manufacturing industry, offering numerous advantages over traditional methods. Its ability to produce high-density, high-precision PCBs has made it a preferred choice for various industries, from consumer electronics to aerospace and defense.
As the demand for more complex and interconnected electronic devices continues to grow, LDI technology is expected to play an increasingly important role in meeting these challenges. With ongoing advancements in laser technology, scanning systems, and automation, LDI is poised to revolutionize the PCB manufacturing landscape, enabling the production of even more sophisticated and innovative electronic products in the future.
Comparison | Laser Direct Imaging (LDI) | Traditional Photolithography |
---|---|---|
Resolution | Up to 25 microns | Typically 50-100 microns |
Registration and alignment | Highly accurate | Prone to misalignment |
Production speed | Faster | Slower |
Environmental impact | Lower | Higher |
Cost-effectiveness | Higher initial investment, | Lower initial investment, |
but long-term cost savings | but higher long-term costs |
Table 1: Comparison between Laser Direct Imaging and Traditional Photolithography in PCB Manufacturing
In conclusion, Laser Direct Imaging represents a significant advancement in PCB manufacturing technology, offering a wide range of benefits that traditional methods cannot match. As the technology continues to evolve and improve, it is clear that LDI will play a pivotal role in shaping the future of the electronics industry.
0 Comments