The Importance of PCBs in Medical and Bio-Medical Devices
PCBs are the backbone of modern electronic devices, and their importance in the medical and bio-medical industries cannot be overstated. Medical devices such as pacemakers, defibrillators, and patient monitoring systems rely heavily on PCBs for their functionality. Bio-medical devices, such as biosensors and lab-on-a-chip systems, also require high-quality PCBs to ensure accurate and reliable results.
The use of PCBs in medical and bio-medical devices offers several advantages, including:
- Miniaturization: PCBs allow for the development of smaller and more compact medical devices, making them more portable and easier to use.
- Reliability: High-quality PCBs ensure the reliable operation of medical devices, reducing the risk of failure and potential harm to patients.
- Cost-effectiveness: The use of PCBs in medical devices helps reduce manufacturing costs, making them more affordable and accessible to a wider range of patients.
Innovations in Bio-Medical PCB Manufacturing
The bio-medical PCB manufacturing industry has witnessed several innovations in recent years, aimed at improving the performance, reliability, and cost-effectiveness of medical devices. Some of these innovations include:
1. Flexible PCBs
Flexible PCBs have gained popularity in the medical and bio-medical industries due to their ability to conform to various shapes and sizes. These PCBs are made from flexible materials, such as polyimide or polyester, and can be bent or folded without compromising their electrical properties. Flexible PCBs are particularly useful in the development of wearable medical devices, such as smart bandages and health monitoring patches.
Advantage | Description |
---|---|
Conformability | Flexible PCBs can conform to various shapes and sizes, making them ideal for wearable medical devices. |
Durability | Flexible PCBs are more durable than rigid PCBs, as they can withstand repeated bending and flexing without breaking. |
Lightweight | Flexible PCBs are lighter than rigid PCBs, making them more comfortable to wear for extended periods. |
2. High-Density Interconnect (HDI) PCBs
HDI PCBs are designed to accommodate a large number of components in a small area, making them ideal for the development of compact medical devices. These PCBs feature fine-pitch traces and micro-vias, allowing for the creation of complex circuit designs with high component density. HDI PCBs are commonly used in the development of implantable medical devices, such as pacemakers and neurostimulators.
Advantage | Description |
---|---|
Miniaturization | HDI PCBs allow for the development of smaller and more compact medical devices. |
High component density | HDI PCBs can accommodate a large number of components in a small area, enabling the creation of complex circuit designs. |
Improved signal integrity | The fine-pitch traces and micro-vias in HDI PCBs help reduce signal loss and improve signal integrity. |
3. 3D Printed PCBs
3D printing technology has revolutionized the manufacturing industry, and the PCB sector is no exception. 3D printed PCBs offer several advantages over traditional PCBs, such as rapid prototyping, customization, and the ability to create complex geometries. In the medical and bio-medical industries, 3D printed PCBs are being explored for the development of personalized medical devices, such as prosthetics and implants.
Advantage | Description |
---|---|
Rapid prototyping | 3D printing allows for the quick and cost-effective production of PCB Prototypes, reducing development time and costs. |
Customization | 3D printed PCBs can be easily customized to meet specific requirements, such as unique shapes or sizes. |
Complex geometries | 3D printing enables the creation of PCBs with complex geometries, which may not be possible with traditional manufacturing methods. |
4. Embedded PCBs
Embedded PCBs are a relatively new development in the PCB manufacturing industry, where electronic components are embedded within the layers of the PCB. This approach offers several benefits, such as reduced size, improved reliability, and enhanced thermal management. In the medical and bio-medical industries, embedded PCBs are being explored for the development of implantable devices, where size and reliability are critical factors.
Advantage | Description |
---|---|
Reduced size | Embedding components within the PCB layers helps reduce the overall size of the device. |
Improved reliability | Embedded components are protected from external factors, such as moisture and vibration, improving the reliability of the device. |
Enhanced thermal management | Embedding components within the PCB layers helps dissipate heat more efficiently, reducing the risk of thermal-related failures. |
The Impact of Bio-Medical PCB Innovations on Healthcare
The innovations in bio-medical PCB manufacturing have had a profound impact on the healthcare industry, contributing to the development of more advanced, reliable, and cost-effective medical devices. Some of the key areas where these innovations have made a significant difference include:
1. Improved Patient Care
The development of smaller, more reliable, and more functional medical devices has led to improved patient care. For example, the use of wearable health monitoring devices, made possible by flexible PCBs, allows for continuous monitoring of vital signs, enabling early detection and intervention in case of any abnormalities. Similarly, the use of implantable devices, such as pacemakers and neurostimulators, has greatly improved the quality of life for patients with chronic conditions.
2. Cost Reduction
The innovations in bio-medical PCB manufacturing have also contributed to the reduction of healthcare costs. The use of advanced manufacturing techniques, such as 3D printing and HDI PCBs, has helped reduce the cost of producing medical devices, making them more affordable and accessible to a wider range of patients. Additionally, the improved reliability and longevity of medical devices, made possible by innovations such as embedded PCBs, have helped reduce the need for frequent replacements, further cutting down on healthcare costs.
3. Personalized Medicine
The advent of 3D printed PCBs has opened up new possibilities for personalized medicine. With the ability to create customized PCBs that match the unique requirements of individual patients, medical devices can now be tailored to meet specific needs. This approach has the potential to greatly improve patient outcomes and satisfaction, as well as reduce the risk of complications associated with generic medical devices.
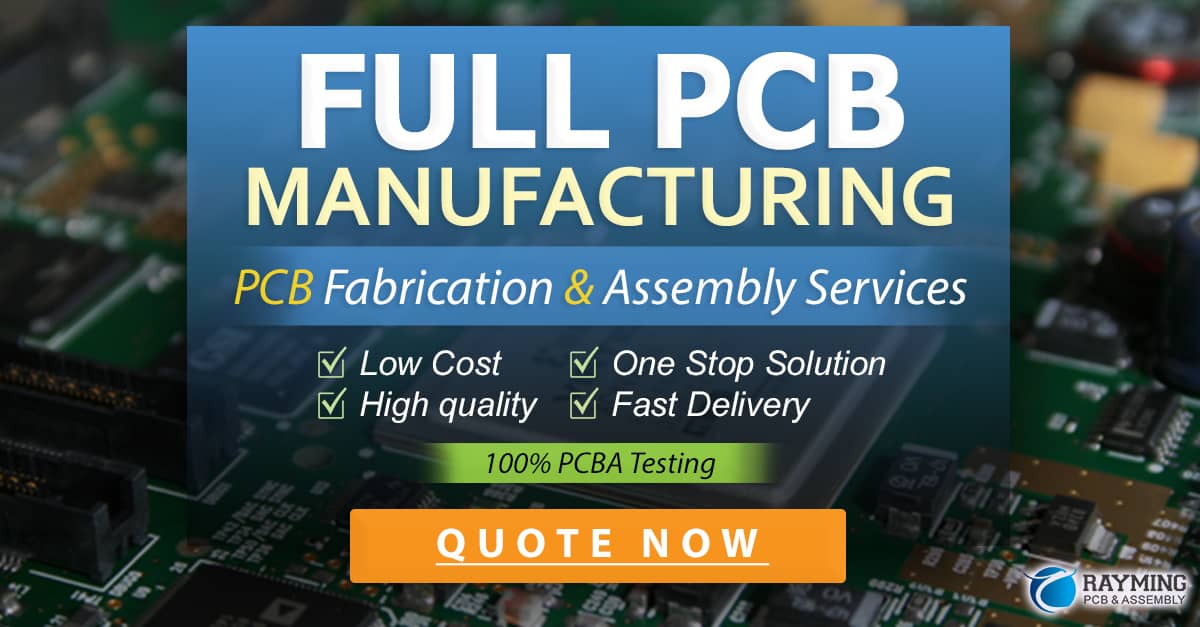
Frequently Asked Questions (FAQ)
1. What are the key advantages of using PCBs in medical and bio-medical devices?
The key advantages of using PCBs in medical and bio-medical devices include miniaturization, reliability, and cost-effectiveness. PCBs allow for the development of smaller and more compact devices, ensure reliable operation, and help reduce manufacturing costs.
2. How have flexible PCBs contributed to the development of wearable medical devices?
Flexible PCBs have enabled the development of wearable medical devices, such as smart bandages and health monitoring patches, due to their ability to conform to various shapes and sizes. These PCBs are made from flexible materials and can be bent or folded without compromising their electrical properties, making them ideal for wearable applications.
3. What are HDI PCBs, and how are they used in the medical and bio-medical industries?
HDI (High-Density Interconnect) PCBs are designed to accommodate a large number of components in a small area, making them ideal for the development of compact medical devices. These PCBs feature fine-pitch traces and micro-vias, allowing for the creation of complex circuit designs with high component density. HDI PCBs are commonly used in the development of implantable medical devices, such as pacemakers and neurostimulators.
4. How has 3D printing technology impacted the PCB manufacturing industry, particularly in the medical and bio-medical sectors?
3D printing technology has revolutionized the PCB manufacturing industry by offering several advantages, such as rapid prototyping, customization, and the ability to create complex geometries. In the medical and bio-medical sectors, 3D printed PCBs are being explored for the development of personalized medical devices, such as prosthetics and implants, enabling the creation of devices that match the unique requirements of individual patients.
5. What are embedded PCBs, and how are they beneficial in the development of implantable medical devices?
Embedded PCBs are a relatively new development in the PCB manufacturing industry, where electronic components are embedded within the layers of the PCB. This approach offers several benefits, such as reduced size, improved reliability, and enhanced thermal management. In the medical and bio-medical industries, embedded PCBs are being explored for the development of implantable devices, where size and reliability are critical factors. By embedding components within the PCB layers, the overall size of the device can be reduced, and the reliability can be improved, as the components are protected from external factors.
Conclusion
The medical and bio-medical PCB manufacturing industry has witnessed significant advancements in recent years, driven by the need for more efficient, reliable, and cost-effective medical devices. Innovations such as flexible PCBs, HDI PCBs, 3D printed PCBs, and embedded PCBs have revolutionized the development of medical devices, contributing to improved patient care, cost reduction, and personalized medicine.
As technology continues to evolve, it is expected that the medical and bio-medical PCB manufacturing industry will witness further innovations, pushing the boundaries of what is possible in the development of medical devices. The subtle tuning of health to technology, made possible by these advancements, holds immense promise for the future of healthcare, offering the potential for more accessible, affordable, and effective medical solutions.
0 Comments