Introduction to Device Packaging
Device packaging is a crucial aspect of the semiconductor industry, as it plays a vital role in protecting and interconnecting electronic components and integrated circuits (ICs). The International Microelectronics Assembly and Packaging Society (IMAPS) is a leading organization that focuses on advancing the field of microelectronics packaging and interconnection technologies. In this article, we will explore the various aspects of device packaging, including its importance, types, and current trends in the industry.
What is Device Packaging?
Device packaging refers to the process of enclosing and protecting electronic components and ICs in a suitable package that allows for reliable electrical connections and efficient heat dissipation. The primary goals of device packaging are to ensure the proper functioning of the device, protect it from environmental factors such as moisture and contamination, and facilitate its integration into larger electronic systems.
Importance of Device Packaging
Device packaging is essential for several reasons:
-
Protection: Packaging protects the delicate electronic components from physical damage, moisture, and other environmental factors that can adversely affect their performance and reliability.
-
Interconnection: Packaging provides a means for connecting the device to other components in an electronic system, such as printed circuit boards (PCBs) or other packages.
-
Heat dissipation: Packaging helps dissipate the heat generated by the device during operation, preventing overheating and ensuring optimal performance.
-
Miniaturization: Advanced packaging technologies enable the creation of smaller, more compact devices, which is crucial for the development of portable and wearable electronics.
Types of Device Packaging
There are several types of device packaging, each with its own advantages and applications. Some of the most common types include:
Through-Hole Packaging
Through-hole packaging involves inserting the leads of electronic components through holes drilled in a PCB and soldering them to pads on the opposite side. This type of packaging is known for its strong mechanical bonds and is often used for larger components or in applications where high reliability is required.
Surface Mount Packaging
Surface mount packaging (SMT) is a more modern approach where components are mounted directly onto the surface of a PCB. SMT packages are smaller and allow for higher component density compared to through-hole packaging. Some common SMT package types include:
- Small Outline Integrated Circuit (SOIC)
- Quad Flat Package (QFP)
- Ball Grid Array (BGA)
- Chip Scale Package (CSP)
Flip Chip Packaging
Flip chip packaging is a type of interconnection where the IC is flipped upside down and connected to the package substrate using conductive bumps. This method provides a shorter electrical path, reducing inductance and improving high-frequency performance. Flip chip packaging is commonly used in high-performance applications, such as microprocessors and graphics processing units (GPUs).
Multi-Chip Modules (MCMs)
Multi-chip modules involve packaging multiple ICs or other components into a single package. This approach offers several benefits, such as improved performance, reduced system size, and enhanced functionality. MCMs can be classified into several categories, including:
- MCM-L (Laminated)
- MCM-C (Ceramic)
- MCM-D (Deposited)
System-in-Package (SiP)
System-in-package is an advanced packaging technology that integrates multiple ICs and other components, such as passive devices and MEMS, into a single package. SiP offers a high level of integration and functionality in a compact form factor, making it suitable for applications such as smartphones, wearables, and IoT devices.
Packaging Materials
The choice of packaging materials is crucial for ensuring the performance, reliability, and longevity of electronic devices. Some common materials used in device packaging include:
Plastics
Plastic packages, such as epoxy resins, are widely used in the semiconductor industry due to their low cost, ease of molding, and good electrical insulation properties. However, plastic packages have limitations in terms of heat dissipation and mechanical strength compared to other materials.
Ceramics
Ceramic packages offer excellent thermal conductivity, mechanical stability, and hermetic sealing capabilities. They are often used in high-reliability applications, such as aerospace, defense, and medical devices. However, ceramic packages are generally more expensive than plastic ones.
Metals
Metal packages, such as copper and aluminum, are used in applications that require high thermal conductivity and mechanical strength. They are often used in power electronics and RF devices.
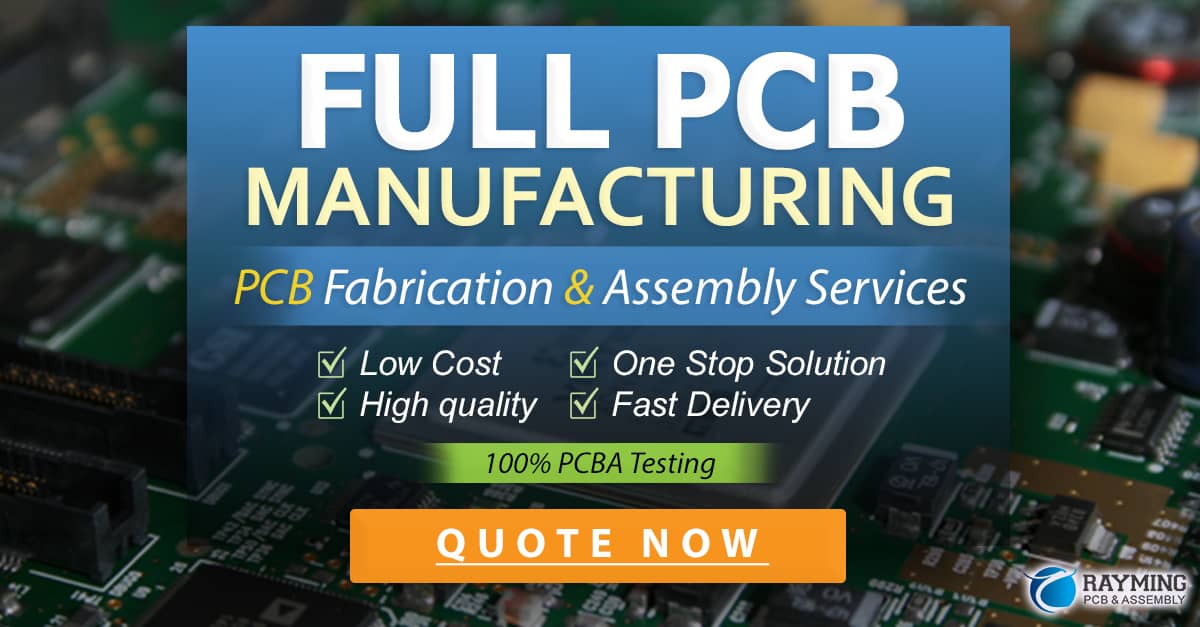
Advanced Packaging Technologies
As the demand for smaller, faster, and more efficient electronic devices continues to grow, advanced packaging technologies have emerged to address these challenges. Some of these technologies include:
3D Packaging
3D packaging involves stacking multiple ICs or packages vertically to create a compact, high-performance device. This approach offers several advantages, such as reduced interconnect lengths, improved bandwidth, and lower power consumption. Some common 3D packaging technologies include:
- Through-Silicon Via (TSV)
- Stacked Die
- Package-on-Package (PoP)
Wafer-Level Packaging (WLP)
Wafer-level packaging is a technology where the packaging process is performed at the wafer level before the individual ICs are singulated. WLP offers several benefits, such as smaller package size, lower cost, and improved electrical performance. Some common WLP technologies include:
- Wafer-Level Chip-Scale Packaging (WLCSP)
- Fan-Out Wafer-Level Packaging (FOWLP)
Embedded Die Packaging
Embedded die packaging involves embedding ICs or other components directly into the substrate or PCB. This approach eliminates the need for separate packages and improves the overall system integration and performance. Embedded die packaging is particularly useful in applications with limited space, such as wearables and IoT devices.
Challenges and Future Trends in Device Packaging
As the semiconductor industry continues to evolve, device packaging faces several challenges and opportunities. Some of the key challenges include:
-
Increasing complexity: With the growing demand for more advanced and integrated electronic devices, packaging technologies must keep pace with the increasing complexity of ICs and system architectures.
-
Thermal management: As device densities and power consumption continue to rise, efficient thermal management becomes crucial for maintaining device performance and reliability.
-
Cost pressure: The semiconductor industry is highly competitive, and there is constant pressure to reduce packaging costs while maintaining or improving device performance.
Despite these challenges, the future of device packaging looks promising, with several trends shaping the industry:
-
Heterogeneous integration: The integration of multiple functionalities, such as digital, analog, and RF, into a single package is becoming increasingly important for enabling next-generation electronic devices.
-
Advanced materials: The development of new packaging materials, such as advanced ceramics and composites, will help address the challenges of thermal management and mechanical stability.
-
Additive manufacturing: The use of additive manufacturing techniques, such as 3D printing, in device packaging can enable the creation of complex, customized packages with improved performance and reduced lead times.
-
Sustainable packaging: As environmental concerns continue to grow, there is an increasing focus on developing sustainable packaging solutions that minimize waste and reduce the environmental impact of electronic devices.
FAQ
-
What is the difference between through-hole and surface mount packaging?
Through-hole packaging involves inserting component leads through holes in a PCB and soldering them to pads on the opposite side, while surface mount packaging involves mounting components directly onto the surface of a PCB. Surface mount packages are generally smaller and allow for higher component density compared to through-hole packages. -
What are the advantages of flip chip packaging?
Flip chip packaging offers several advantages, including shorter electrical paths, reduced inductance, and improved high-frequency performance. This packaging method is commonly used in high-performance applications, such as microprocessors and GPUs. -
What are the main challenges faced by the device packaging industry?
The main challenges in device packaging include increasing complexity of ICs and system architectures, efficient thermal management, and cost pressure. As devices become more advanced and integrated, packaging technologies must keep pace while maintaining or improving performance and reliability. -
What are some emerging trends in device packaging?
Some emerging trends in device packaging include heterogeneous integration, advanced materials, additive manufacturing, and sustainable packaging solutions. These trends are driven by the need for more advanced, efficient, and environmentally friendly packaging technologies. -
What is the importance of packaging materials in device performance and reliability?
The choice of packaging materials is crucial for ensuring the performance, reliability, and longevity of electronic devices. Different materials, such as plastics, ceramics, and metals, offer unique properties in terms of electrical insulation, thermal conductivity, and mechanical strength. The selection of appropriate packaging materials depends on the specific requirements of the application and the operating environment.
Conclusion
Device packaging is a critical aspect of the semiconductor industry, playing a vital role in protecting and interconnecting electronic components and ICs. As the demand for more advanced and integrated electronic devices continues to grow, packaging technologies must evolve to address the challenges of increasing complexity, thermal management, and cost pressure.
The IMAPS organization is at the forefront of advancing microelectronics packaging and interconnection technologies, providing a platform for industry professionals to collaborate, share knowledge, and drive innovation. By staying abreast of the latest trends and developments in device packaging, such as heterogeneous integration, advanced materials, and sustainable solutions, the industry can continue to push the boundaries of what is possible in the world of electronics.
As we look to the future, it is clear that device packaging will play an increasingly important role in shaping the electronic devices that we rely on in our daily lives. With the continued efforts of organizations like IMAPS and the dedication of industry professionals, we can expect to see exciting new developments in device packaging that will enable the next generation of electronic devices.
Packaging Type | Advantages | Disadvantages | Common Applications |
---|---|---|---|
Through-Hole | Strong mechanical bonds, high reliability | Larger size, lower component density | Larger components, high-reliability applications |
Surface Mount | Smaller size, higher component density | Weaker mechanical bonds compared to through-hole | Most modern electronic devices |
Flip Chip | Shorter electrical paths, reduced inductance, improved high-frequency performance | Higher cost, more complex assembly process | High-performance applications (e.g., microprocessors, GPUs) |
Multi-Chip Module | Improved performance, reduced system size, enhanced functionality | Higher cost, more complex design and assembly | Applications requiring high integration and functionality |
System-in-Package | High level of integration and functionality, compact form factor | Higher cost, more complex design and assembly | Smartphones, wearables, IoT devices |
0 Comments