What are HDI PCBs?
HDI PCBs are printed circuit boards that feature higher wiring density per unit area compared to traditional PCBs. They are characterized by the use of microvias, which are small holes drilled in the PCB substrate to establish electrical connections between layers. HDI PCBs offer several advantages, including:
- Reduced board size and weight
- Improved signal integrity
- Enhanced thermal management
- Increased reliability
- Lower power consumption
The Role of UV Lasers in HDI PCB Manufacturing
UV lasers have become an essential tool in the manufacturing of HDI PCBs due to their ability to create precise and small features. Unlike traditional mechanical drilling methods, UV lasers can drill microvias with diameters as small as 50 microns, enabling higher wiring density and more compact designs.
Advantages of UV Laser Drilling in HDI PCBs
-
Precision: UV lasers offer high precision and accuracy, allowing for the creation of microvias with tight tolerances and minimal deviation from the desired dimensions.
-
Speed: UV laser drilling is a fast process, enabling higher throughput and shorter manufacturing times compared to mechanical drilling methods.
-
Reduced Damage: UV lasers cause minimal thermal and mechanical stress to the PCB substrate, reducing the risk of delamination, warping, or other damage during the drilling process.
-
Flexibility: UV lasers can drill microvias in a variety of shapes and sizes, providing designers with greater flexibility in their PCB layouts.
UV Laser Drilling Process
The UV laser drilling process involves the following steps:
-
PCB Preparation: The PCB substrate is cleaned and prepared for the drilling process.
-
Laser Alignment: The UV laser is aligned with the desired drilling locations on the PCB using a high-precision positioning system.
-
Laser Drilling: The UV laser beam is focused onto the PCB surface, vaporizing the substrate material and creating the microvias.
-
Cleaning: The drilled PCB is cleaned to remove any debris or residue left behind by the drilling process.
-
Inspection: The drilled PCB is inspected for accuracy and quality using automated optical inspection (AOI) systems.
Guidelines for Designing HDI PCBs
Designing HDI PCBs requires careful consideration of several factors to ensure optimal performance, reliability, and manufacturability. Here are some guidelines to follow when designing HDI PCBs:
1. Choose the Right HDI PCB Type
There are three main types of HDI PCBs, each with its own characteristics and applications:
HDI PCB Type | Description | Applications |
---|---|---|
Type I | Microvias in one layer only | Consumer electronics, mobile devices |
Type II | Microvias in two layers, stacked or staggered | Automotive, medical devices, industrial controls |
Type III | Microvias in three or more layers, stacked or staggered | High-performance computing, aerospace, defense |
Choose the appropriate HDI PCB type based on your application requirements, such as component density, signal integrity, and reliability.
2. Adhere to Microvia Design Rules
When designing microvias in HDI PCBs, follow these guidelines:
- Minimize microvia diameter to reduce the occupied space on the PCB surface.
- Maintain sufficient spacing between microvias to prevent shorting and signal interference.
- Use a minimum aspect ratio of 0.75:1 (depth to diameter) for reliable microvia formation.
- Avoid stacking microvias more than two layers deep to prevent manufacturing issues.
3. Optimize Signal Integrity
To ensure optimal signal integrity in HDI PCBs:
- Use controlled impedance design techniques to match the impedance of the signal traces to the desired value.
- Minimize the length of high-speed signal traces to reduce signal attenuation and distortion.
- Use ground planes and power planes to provide a low-impedance return path for signals and minimize crosstalk.
- Implement proper termination techniques, such as series termination or parallel termination, to prevent signal reflections.
4. Consider Thermal Management
HDI PCBs often have high component density, which can lead to increased heat generation. To manage thermal issues:
- Use thermal vias to conduct heat away from hot components and into the PCB substrate or heat sinks.
- Incorporate sufficient copper coverage in power and ground planes to distribute heat evenly across the PCB.
- Use high thermal conductivity materials, such as metal-core PCBs or thermal interface materials, to enhance heat dissipation.
5. Collaborate with PCB Manufacturers
Engage with PCB manufacturers early in the design process to ensure the manufacturability and reliability of your HDI PCB design. Discuss your requirements, such as layer stack-up, microvia specifications, and material choices, to optimize your design for the manufacturing process.
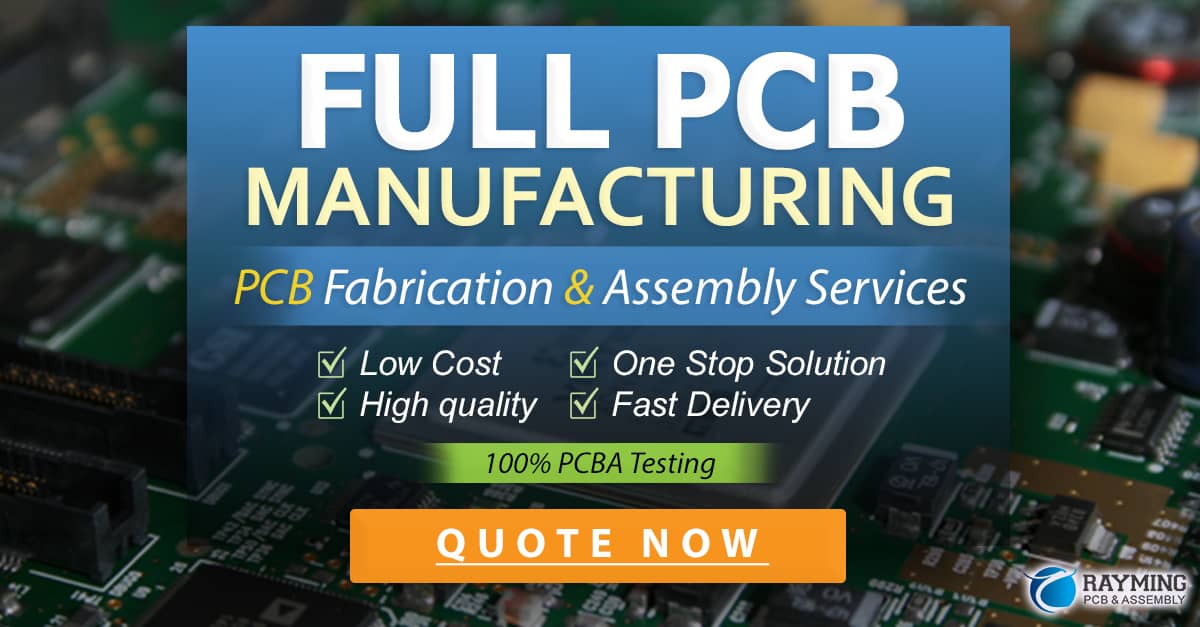
Frequently Asked Questions (FAQ)
-
What are the benefits of using UV lasers for HDI PCB manufacturing?
UV lasers offer several benefits for HDI PCB manufacturing, including high precision, speed, reduced damage to the PCB substrate, and flexibility in creating microvias of various shapes and sizes. -
How small can microvias be in HDI PCBs?
UV lasers can drill microvias with diameters as small as 50 microns in HDI PCBs, enabling higher wiring density and more compact designs. -
What are the different types of HDI PCBs?
There are three main types of HDI PCBs: Type I (microvias in one layer), Type II (microvias in two layers, stacked or staggered), and Type III (microvias in three or more layers, stacked or staggered). -
How can I optimize signal integrity in HDI PCBs?
To optimize signal integrity in HDI PCBs, use controlled impedance design techniques, minimize high-speed signal trace lengths, use ground and power planes, and implement proper termination techniques. -
Why is thermal management important in HDI PCBs?
HDI PCBs often have high component density, which can lead to increased heat generation. Proper thermal management, such as using thermal vias, sufficient copper coverage, and high thermal conductivity materials, is essential to ensure the reliability and performance of the PCB.
Conclusion
UV lasers play a crucial role in the manufacturing of HDI PCBs, enabling the creation of precise and small features such as microvias. By understanding the advantages and process of UV laser drilling, designers can optimize their HDI PCB layouts for high performance, reliability, and manufacturability. Following the guidelines for designing HDI PCBs, such as choosing the right PCB type, adhering to microvia design rules, optimizing signal integrity, considering thermal management, and collaborating with PCB manufacturers, will help ensure the success of your HDI PCB projects.
[HDI PCB]: High Density Interconnect Printed Circuit Board
[UV]: Ultraviolet
[PCB]: Printed Circuit Board
[AOI]: Automated Optical Inspection
0 Comments