Understanding the Importance of PCB Protection
PCBs are the backbone of electronic devices, and their proper functioning is critical for the overall performance and reliability of the system. Exposure to harmful elements can lead to corrosion, short circuits, and other issues that can compromise the integrity of the PCB and cause device failure. Implementing appropriate PCB protection measures not only extends the lifespan of electronic devices but also minimizes the risk of costly repairs and downtime.
Common Threats to PCBs
- Moisture: Exposure to humidity, condensation, or liquid spills can cause corrosion and short circuits on PCBs.
- Dust and debris: Accumulation of dust and debris can lead to insulation breakdown and overheating.
- Extreme temperatures: High temperatures can cause thermal stress, while low temperatures can lead to brittle solder joints.
- Mechanical stress: Physical impacts, vibrations, and bending can damage PCB Traces and components.
- Electromagnetic interference (EMI): External electromagnetic fields can disrupt the operation of PCBs.
Conformal Coating
Conformal coating is a popular method for protecting PCBs from environmental hazards. It involves applying a thin, protective layer over the surface of the PCB, covering the components and traces. Conformal coatings act as a barrier against moisture, dust, and other contaminants, preventing them from reaching the sensitive areas of the PCB.
Types of Conformal Coatings
Coating Type | Characteristics | Applications |
---|---|---|
Acrylic | Fast drying, easy to apply, good moisture resistance | Consumer electronics, automotive |
Silicone | Excellent flexibility, wide temperature range | Aerospace, military, high-temperature environments |
Polyurethane | Tough, abrasion-resistant, good chemical resistance | Industrial, marine, outdoor applications |
Epoxy | High dielectric strength, good adhesion, chemical resistance | Harsh environments, automotive, aerospace |
Parylene | Uniform coverage, pinhole-free, excellent barrier properties | Medical devices, sensitive electronics |
Applying Conformal Coatings
- Clean the PCB surface to remove any contaminants or residues.
- Mask off areas that should not be coated, such as connectors or test points.
- Apply the conformal coating using a spray, brush, or dip method, ensuring even coverage.
- Allow the coating to cure according to the manufacturer’s instructions.
- Inspect the coated PCB for any defects or missed areas, and touch up if necessary.
Enclosures and Housings
Enclosing PCBs in protective housings is another effective way to shield them from environmental hazards. Enclosures provide a physical barrier against moisture, dust, and mechanical damage, while also offering aesthetic benefits.
Types of Enclosures
Enclosure Material | Properties | Applications |
---|---|---|
Plastic | Lightweight, cost-effective, good electrical insulation | Consumer electronics, handheld devices |
Metal | Durable, EMI Shielding, heat dissipation | Industrial equipment, outdoor applications |
Composites | High strength-to-weight ratio, corrosion-resistant | Aerospace, automotive, marine |
3D-printed | Customizable, rapid prototyping, complex geometries | Prototypes, low-volume production |
Designing Enclosures for PCB Protection
- Consider the operating environment and select appropriate materials.
- Ensure proper sealing to prevent ingress of moisture and dust.
- Incorporate ventilation or cooling features to manage heat dissipation.
- Design for ease of assembly and maintenance, with access to connectors and controls.
- Incorporate EMI shielding if necessary, using conductive gaskets or coatings.
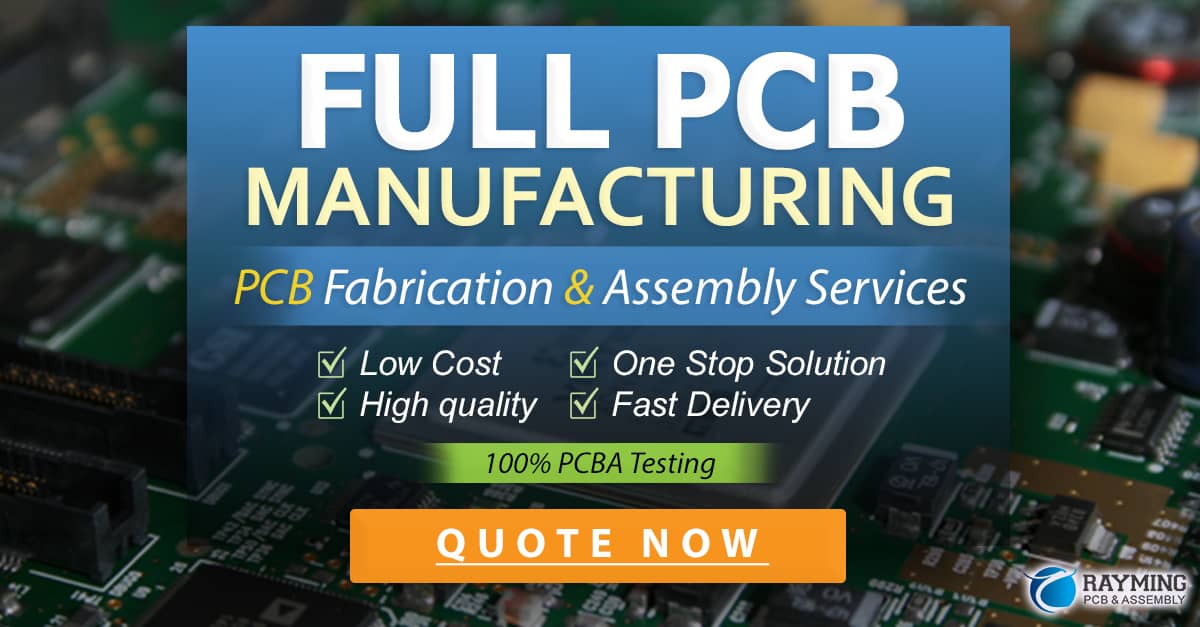
Potting and Encapsulation
Potting and encapsulation involve embedding PCBs in a protective compound, typically a polymer resin. This method provides excellent protection against moisture, vibration, and mechanical stress, making it suitable for harsh environments.
Potting Materials
Material | Characteristics | Applications |
---|---|---|
Epoxy | High strength, good chemical resistance, electrical insulation | Industrial, automotive, aerospace |
Silicone | Flexible, wide temperature range, low stress on components | Medical devices, sensors, wearables |
Polyurethane | Tough, abrasion-resistant, good thermal conductivity | Outdoor equipment, power electronics |
Acrylic | Fast curing, good adhesion, low shrinkage | Consumer electronics, LED lighting |
Potting Process
- Design the mold or housing to accommodate the PCB and potting material.
- Prepare the PCB by cleaning and masking off areas that should not be potted.
- Mix the potting compound according to the manufacturer’s instructions.
- Pour or inject the potting compound into the mold, ensuring complete coverage of the PCB.
- Allow the potting material to cure, following the recommended time and temperature.
Thermal Management
Proper thermal management is essential for protecting PCBs from overheating, which can lead to component failure and reduced reliability. Implementing effective cooling solutions helps to dissipate heat generated by components and maintain optimal operating temperatures.
Thermal Management Techniques
Technique | Description | Applications |
---|---|---|
Heat sinks | Metallic structures that dissipate heat from components | High-power components, processors |
Thermal interface materials | Compounds that enhance heat transfer between components and heat sinks | Power electronics, LEDs |
Fans and blowers | Active cooling solutions that move air across the PCB | High-density PCBs, enclosed systems |
Liquid cooling | Circulating a coolant to remove heat from components | High-performance computing, data centers |
PCB layout optimization | Designing PCBs with thermal considerations, such as component placement and copper pours | General PCB design |
Implementing Thermal Management
- Identify heat-generating components and their thermal requirements.
- Select appropriate thermal management techniques based on the application and environment.
- Design the PCB layout with thermal considerations, such as proper component spacing and thermal vias.
- Apply thermal interface materials between components and heat sinks, if necessary.
- Incorporate active cooling solutions, such as fans or liquid cooling, for high-heat applications.
Electromagnetic Interference (EMI) Shielding
EMI can disrupt the operation of PCBs and cause signal integrity issues. Implementing EMI shielding techniques helps to protect PCBs from external electromagnetic fields and prevent the emission of unwanted electromagnetic energy.
EMI Shielding Methods
Method | Description | Applications |
---|---|---|
Shielding enclosures | Metallic enclosures that surround the PCB, providing EMI protection | Sensitive electronics, medical devices |
Conductive coatings | Applying Conductive Paints or sprays to the inside of enclosures | Plastic enclosures, cost-effective shielding |
Shielding gaskets | Conductive materials that seal gaps between enclosure parts | Removable covers, access panels |
PCB design techniques | Proper grounding, trace routing, and component placement to minimize EMI | General PCB design |
Ferrite beads | Passive components that suppress high-frequency noise | Power supply lines, data cables |
Implementing EMI Shielding
- Identify the EMI sources and sensitive components on the PCB.
- Select appropriate shielding methods based on the application and EMI requirements.
- Design the PCB with EMI considerations, such as proper grounding and trace routing.
- Incorporate shielding enclosures or conductive coatings, if necessary.
- Use shielding gaskets to ensure proper sealing between enclosure parts.
- Test the PCB for EMI compliance and make necessary adjustments.
Frequently Asked Questions (FAQ)
- What is the most common method for protecting PCBs from environmental hazards?
-
Conformal coating is one of the most common methods for protecting PCBs. It provides a thin, protective layer that shields the PCB from moisture, dust, and other contaminants.
-
Can I apply conformal coating myself, or do I need professional services?
-
While it is possible to apply conformal coating yourself, it is recommended to use professional services, especially for critical applications. Professional coating services have the equipment, expertise, and controlled environment necessary for optimal results.
-
How do I choose the right enclosure material for my PCB?
-
The choice of enclosure material depends on the application and the environmental conditions the PCB will be exposed to. Consider factors such as durability, weight, cost, and EMI shielding requirements when selecting an enclosure material.
-
Is potting necessary for all PCBs?
-
Potting is not necessary for all PCBs, but it is highly recommended for applications that involve harsh environments, high vibration, or extreme temperature variations. Potting provides excellent protection against moisture, mechanical stress, and thermal shock.
-
How can I determine if my PCB requires EMI shielding?
- If your PCB is sensitive to external electromagnetic fields or if it emits unwanted electromagnetic energy, EMI shielding may be necessary. Conduct EMI testing to determine if your PCB meets the required emissions and immunity standards for your application.
Conclusion
Protecting PCBs is crucial for ensuring the reliability and longevity of electronic devices. By implementing appropriate protection measures, such as conformal coating, enclosures, potting, thermal management, and EMI shielding, engineers can safeguard PCBs from environmental hazards and maintain optimal performance. When designing PCBs, it is essential to consider the specific requirements of the application and select protection methods that balance cost, effectiveness, and ease of implementation. By following best practices and staying updated with the latest protection technologies, engineers can create robust and reliable electronic systems that withstand the challenges of various operating environments.
0 Comments