What is a Microcontroller Circuit?
A microcontroller circuit is a self-contained system with a microcontroller chip at its core that can be programmed to control electronic devices. It integrates a processor, memory, I/O peripherals, and other support circuitry onto a single chip or board.
Some key characteristics of microcontroller circuits:
– Low power consumption
– Small size
– Reprogrammable
– Integrated RAM, ROM, I/O ports on chip
– Ideal for embedded applications
Popular microcontroller families include Arduino, PIC, AVR, and ARM. These offer a range of capabilities, memory sizes, speeds, and peripheral options to suit different project requirements.
Planning Your Microcontroller PCB Design
Defining Project Requirements
Before starting your PCB design, clearly define what you want your microcontroller circuit to do. Outline the required functionality, inputs/outputs, power supply, physical size constraints, and operating conditions. This will guide component selection and circuit design.
Selecting a Microcontroller
Choose a microcontroller that meets your project’s processing, memory, I/O, and peripheral requirements. Consider factors such as:
– Number and type of I/O pins
– Memory (Flash, SRAM, EEPROM)
– Clock speed
– Peripheral interfaces (UART, I2C, SPI, USB, etc.)
– ADC/DAC resolution
– Power consumption
– Cost and availability
– Development tools and ecosystem
Refer to microcontroller datasheets and compare options to find the best fit. Popular choices for hobbyists and makers include chips like the ATmega328 (Arduino Uno), ATmega32U4 (Arduino Leonardo), PIC16F/PIC18F series, and STM32 ARM Cortex-M MCUs.
Creating a Block Diagram
Organize your system into a high-level block diagram showing the main functional units and how they interconnect. Blocks to include:
– Microcontroller
– Power supply
– Crystal oscillator
– Reset circuitry
– Digital I/O
– Analog inputs
– External memory
– Communication interfaces
– Connectors for off-board components
The block diagram provides a roadmap for your schematic design.
Drafting a Schematic
Translate your block diagram into a detailed schematic, adding the specific components for each section. Use your microcontroller’s reference schematic as a starting point. Key steps:
1. Place microcontroller symbol and label power pins
2. Add decoupling/filtering capacitors near VCC/GND
3. Connect oscillator components (crystal, capacitors)
4. Wire up reset circuitry (reset IC or RC filters)
5. Assign GPIO pins for digital inputs/outputs
6. Configure ADC input pins with filters or protection
7. Hook up external memory ICs if used
8. Include communication interface transceivers and connectors
9. Provide debug/programming header
10. Add power input jack, voltage regulator, reverse polarity protection
Double-check pinouts, power connections, and refer frequently to datasheets. Simulate the circuit to verify expected operation.
Microcontroller PCB Layout
Component Placement
Arrange components on your PCB logically, balancing electrical and mechanical constraints:
– Group components by function (power, analog, digital, RF)
– Minimize distance between decoupling caps and IC power pins
– Provide adequate clearance around connectors, mounting holes, heatsinks
– Orient IC pin 1 consistently for easier assembly
– Consider PCB mounting and enclosure requirements
Routing Guidelines
Route the traces on your PCB to efficiently connect components while minimizing noise and interference:
– Route power traces first, using thick traces and dedicated layers if possible
– Minimize loop areas in high di/dt traces to reduce EMI
– Avoid acute angles and provide smooth corners in traces
– Maintain controlled impedance for high-speed traces
– Isolate sensitive analog traces from noisy digital ones
– Avoid routing traces under noisy components like crystals or switching regulators
– Provide ground planes for shielding and current return paths
Stackup and Layer Planning
Choose a layer stackup that meets your signal integrity, EMC, and manufacturing needs. A common 4-layer stackup for mixed-signal boards is:
1. Top layer: signals, components
2. Inner layer 1: ground plane
3. Inner layer 2: power planes
4. Bottom layer: signals, components
For simpler 2-layer boards, use a thicker core and keep power/ground traces short and wide.
DRC and Manufacturing Checks
Run design rule checks (DRC) to verify your PCB layout meets manufacturing constraints such as:
– Minimum trace width and spacing
– Minimum drill size and annular rings
– Solder mask and silkscreen clearances
– Copper-to-board edge clearance
– Acute angles and trace corners
Generate manufacturing files (Gerbers, drill files, BOM) and review them carefully before sending to a PCB fab.
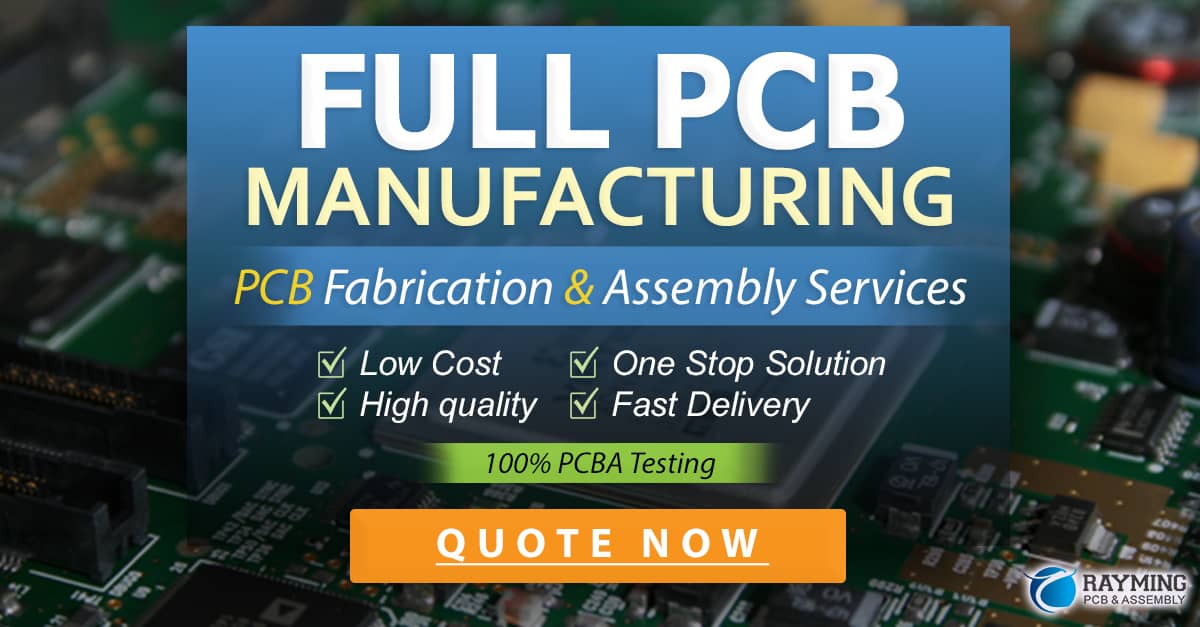
PCB Assembly and Bring-Up
Soldering Components
After receiving your fabricated PCB, gather the components and carefully solder them in place. Use a fine-tip soldering iron, quality solder, and follow proper technique:
1. Apply small amount of solder to one pad
2. Hold component in place while heating pad
3. Allow solder to flow around lead and cool
4. Solder remaining pins individually
5. Inspect joints for good wetting and fillets
Use a microscope to examine fine-pitch ICs. Rework any weak joints.
Visual Inspection
Visually inspect the fully assembled PCB for quality issues:
– Correct component placement and orientation
– Solder bridges or splashes
– Cold or cracked solder joints
– Damaged traces or lifted pads
– Foreign debris or contamination
Clean flux residue with IPA and a brush. Rework defects as needed.
Hardware Bring-Up
Power up the assembled board gradually while monitoring current draw. Check for expected voltage levels at key testpoints. Verify clock and reset signals. Test I/O pins and periperals individually. Hook up a debug interface and ensure you can program the microcontroller.
Typical bring-up sequence:
1. Visual inspection
2. Power supplies
3. Clocks and reset
4. Microcontroller
5. Digital I/O
6. Analog interfaces
7. Memories
8. Serial communication
9. Special peripherals
10. Full functional test
Take a methodical approach and check off each subunit before moving on. Use an oscilloscope or logic analyzer to probe signals and diagnose issues.
Programming and Debugging
Development Environment Setup
Install the appropriate IDE, compiler toolchain, and programmers for your selected microcontroller. Popular environments include:
– Arduino IDE
– MPLAB X IDE (PIC)
– Atmel Studio (AVR)
– ARM Keil MDK
– Eclipse-based IDEs with GCC
– PlatformIO
Configure the IDE for your specific chip and board. Set up a programming interface like ICSP, JTAG, or SWD.
Downloading and Debugging Code
Write your application firmware in C/C++ or the Arduino language. Structure it into logical modules and use well-defined interfaces. Implement device drivers for external peripherals. Include error handling and diagnostic output.
Download the compiled code to your microcontroller’s flash memory using a programmer. Set breakpoints and step through code in the debugger. Watch variables and memory. Use Serial.print() or similar for text output.
Tips for efficient debugging:
– Incremental testing – test each module separately
– Meaningful debug output – log key events and variable values
– Use asserts – catch invalid states early
– Hardware breakpoints – halt on specific memory accesses
– External interfaces – UART/SWD/JTAG for debug comms
– Measure signals – oscilloscope or logic analyzer for hardware issues
Optimize and refine your firmware iteratively. Test corner cases and error handling.
Example Microcontroller Circuits
To illustrate these concepts, let’s look at some common microcontroller circuit building blocks.
Minimal Arduino Circuit
Component | Value |
---|---|
Microcontroller | ATmega328P |
Capacitor C1 | 100nF |
Capacitor C2 | 100nF |
Capacitor C3 | 10uF |
Crystal Y1 | 16MHz |
Capacitor C4 | 22pF |
Capacitor C5 | 22pF |
Resistor R1 | 10K |
Programming Header | 2×3 Pin |
This minimal circuit has just the bare essentials to run an Arduino bootloader on the ATmega328P. It’s a good starting point for simple projects.
STM32 ARM Cortex-M Dev Board
Component | Value |
---|---|
Microcontroller | STM32F103C8T6 |
Voltage Regulator | AMS1117-3.3 |
Capacitor C1, C2 | 22uF |
Capacitor C3, C4 | 100nF |
Crystal Y1 | 8MHz |
Capacitor C5, C6 | 22pF |
Reset IC | ESD protection |
USB Connector | Mini-B USB |
SWD Header | 2×5 1.27mm |
User LED | 0603 Green |
This is a more full-featured development board for the STM32F103 ARM Cortex-M3 microcontroller. It includes a 3.3V regulator, crystal, USB, and a debug header in a compact form factor suitable for prototyping more complex projects.
FAQ
What software is needed to design a microcontroller PCB?
To design a microcontroller PCB, you’ll need:
1. Schematic capture tool (OrCAD, Eagle, KiCAD, Altium, etc.)
2. PCB layout tool (often integrated with schematic tool)
3. Microcontroller IDE and compiler (Arduino IDE, MPLAB X, Keil MDK, etc.)
4. Gerber viewer for verifying manufacturing files
How do I select the right microcontroller for my project?
Consider your project’s requirements for:
– Processing power and architecture
– Memory size (Flash, SRAM, EEPROM)
– Number and type of I/O pins
– Peripherals (ADC, PWM, USB, Ethernet, CAN, etc.)
– Power consumption
– Development ecosystem and tools
– Cost and availability
Refer to microcontroller datasheets and compare parametric tables to find options that meet your needs. If unsure, start with a popular beginner-friendly platform like Arduino or PIC and scale up as needed.
What are some common mistakes to avoid in microcontroller PCB design?
Common pitfalls to watch out for:
1. Insufficient decoupling or power supply filtering
2. Incorrect oscillator loading capacitor values
3. Lack of ESD protection on sensitive pins
4. Improper reset circuitry
5. Mixing analog and digital ground
6. Routing high-speed traces near noisy components
7. Failing to include test points and debug interfaces
8. Not verifying footprint dimensions against components
9. Neglecting DFM rules during PCB layout
10. Inadequate documentation for future reference
How can I troubleshoot a microcontroller PCB that isn’t working?
When debugging an unresponsive board:
1. Inspect all solder joints and rework any defects
2. Verify power supply voltages at expected testpoints
3. Check oscillator and reset signals with a scope
4. Confirm programming interface is functional
5. Use multimeter to check for shorts or open circuits
6. Measure I/O pin signals and compare to firmware
7. Simplify code and test in smaller sections
8. Consult datasheets and schematics for expected behavior
9. Compare against a known-good reference board
10. Search online forums or contact an experienced engineer for help
Take a systematic approach, document your findings, and don’t be afraid to ask for assistance if stuck.
What are the benefits of designing a custom microcontroller PCB vs using an off-the-shelf board?
Designing a custom microcontroller PCB allows you to:
– Tailor form factor, pinout, and aesthetics to your product
– Optimize BoM cost at production volumes
– Integrate the microcontroller with your required peripherals
– Customize power supplies and interfaces
– Implement application-specific features and branding
– Control the component supply chain
– Protect your intellectual property
An off-the-shelf dev board is better suited for:
– Quick prototyping and proof-of-concept
– Low-volume, low-cost projects
– Accessing a wide range of pre-built peripheral boards
– Taking advantage of open-source ecosystems
– Getting started with minimal PCB design experience
The best choice depends on your project’s specific needs, timeline, budget, and production scale.
I hope this guide provides a helpful overview of the process of creating a microcontroller circuit board, from planning and design through assembly and debugging. Let me know if you have any other questions!
0 Comments