Understanding the Basics of SMT PCB Assembly
Before diving into the step-by-step instructions, it’s essential to understand the basics of SMT PCB assembly. SMT is a method of assembling electronic components onto a PCB using automated machines. The components are placed on the surface of the PCB and soldered in place using a reflow oven or a wave soldering machine.
The main advantages of SMT over through-hole technology (THT) are:
- Smaller component sizes
- Higher component density
- Faster assembly process
- Lower manufacturing costs
Key Components of SMT PCB Assembly
To successfully complete your SMT PCB assembly, you need to be familiar with the key components involved in the process:
-
PCB: The printed circuit board is the foundation of the assembly. It consists of conductive tracks, pads, and other features etched from copper sheets laminated onto a non-conductive substrate.
-
Solder Paste: A mixture of tiny solder particles and flux, applied to the PCB pads where components will be placed. The paste temporarily holds the components in place before soldering.
-
Components: Surface mount components, such as resistors, capacitors, and integrated circuits (ICs), are the building blocks of the electronic assembly.
-
Stencil: A thin metal sheet with openings that match the PCB pads. It is used to apply solder paste to the PCB accurately.
-
Pick and Place Machine: An automated machine that picks up components from feeders and places them onto the PCB with high precision.
-
Reflow Oven: A machine that heats the PCB assembly to melt the solder paste and create permanent electrical connections between the components and the PCB.
Step-by-Step Instructions for SMT PCB Assembly
Now that you have a basic understanding of SMT PCB assembly let’s dive into the 9 detailed instructions to complete your assembly process.
Step 1: Design and Manufacture the PCB
The first step in SMT PCB assembly is to design and manufacture the PCB. This involves creating a schematic diagram, laying out the PCB, and generating the necessary files for manufacturing (e.g., Gerber files).
When designing your PCB, consider the following factors:
- Component placement and orientation
- Pad sizes and shapes
- Trace widths and spacing
- Thermal management
- Electromagnetic compatibility (EMC)
Once your PCB design is complete, send the files to a PCB manufacturer for fabrication.
Step 2: Prepare the Solder Paste Stencil
A solder paste stencil is essential for applying solder paste to the PCB accurately. The stencil should have openings that match the pads on the PCB where components will be placed.
To prepare the stencil:
- Create a stencil design file based on your PCB layout.
- Send the stencil design file to a stencil manufacturer for fabrication.
- Clean the stencil thoroughly before use to remove any contaminants.
Step 3: Apply Solder Paste to the PCB
With the solder paste stencil ready, you can now apply solder paste to the PCB:
- Align the stencil with the PCB using alignment pins or a vision system.
- Place solder paste on the stencil and spread it evenly using a squeegee.
- Carefully lift the stencil from the PCB, leaving solder paste deposits on the pads.
- Inspect the solder paste deposits for any defects or inconsistencies.
Step 4: Place Components onto the PCB
After applying solder paste, it’s time to place the surface mount components onto the PCB. This is typically done using a pick and place machine:
- Load the component feeders into the pick and place machine.
- Program the machine with the component placement data from your PCB design files.
- Start the pick and place process, allowing the machine to place components onto the PCB accurately.
- Visually inspect the placed components for any misalignments or missing components.
Step 5: Reflow Soldering
Reflow soldering is the process of melting the solder paste to create permanent electrical connections between the components and the PCB:
- Preheat the PCB assembly in the reflow oven to activate the flux and remove any moisture.
- Gradually increase the temperature to melt the solder particles and form solder joints.
- Cool the PCB assembly to allow the solder joints to solidify.
- Inspect the solder joints for any defects, such as bridging, insufficient solder, or poor wetting.
Step 6: Inspection and Quality Control
After reflow soldering, it’s crucial to perform thorough inspections and quality control checks:
- Visually inspect the PCB assembly for any obvious defects, such as misaligned components, solder bridges, or damaged components.
- Use automated optical inspection (AOI) equipment to detect smaller defects and ensure consistent quality.
- Perform electrical testing to verify the functionality of the assembled PCB.
- Document any defects or issues found during the inspection process and take corrective actions as needed.
Step 7: Rework and Repair
If any defects are found during the inspection process, rework and repair may be necessary:
- Identify the specific defects and their locations on the PCB.
- Use appropriate tools, such as a soldering iron, hot air rework station, or desoldering equipment, to remove the defective components or correct the solder joints.
- Replace any removed components with new ones and resolder them onto the PCB.
- Re-inspect the reworked areas to ensure the defects have been successfully corrected.
Step 8: Conformal Coating (Optional)
Depending on the application and environmental requirements, you may need to apply a conformal coating to the PCB assembly:
- Clean the PCB assembly to remove any flux residues or contaminants.
- Apply the conformal coating using a spray, dip, or brush method, ensuring even coverage.
- Cure the coating according to the manufacturer’s instructions, typically using heat or UV light.
- Inspect the coated PCB assembly for any defects, such as bubbles, pinholes, or incomplete coverage.
Step 9: Final Assembly and Packaging
The final step in the SMT PCB assembly process is to complete any remaining assembly tasks and package the finished product:
- Attach any additional components, such as connectors, heat sinks, or mechanical parts.
- Perform final functional testing to ensure the assembled PCB meets all performance requirements.
- Package the PCB assembly in an appropriate enclosure or packaging material, depending on the application and shipping requirements.
- Label the packaged product with relevant information, such as part numbers, serial numbers, and handling instructions.
Frequently Asked Questions (FAQ)
-
What are the main advantages of SMT PCB assembly over through-hole technology?
SMT PCB assembly offers several advantages over through-hole technology, including smaller component sizes, higher component density, faster assembly process, and lower manufacturing costs. -
How do I select the right solder paste for my SMT PCB assembly?
When selecting a solder paste, consider factors such as the alloy composition, particle size, flux type, and viscosity. Consult with your solder paste supplier or refer to industry standards (e.g., IPC-J-STD-005) for guidance on selecting the appropriate solder paste for your application. -
What are some common defects in SMT PCB assembly, and how can I prevent them?
Common defects in SMT PCB assembly include solder bridges, insufficient solder, poor wetting, component misalignment, and tombstoning. To prevent these defects, ensure proper solder paste application, optimize reflow soldering profiles, use appropriate component placement techniques, and maintain a clean and controlled assembly environment. -
How can I ensure consistent quality in my SMT PCB assembly process?
To ensure consistent quality, implement a robust quality control system that includes visual inspections, automated optical inspection (AOI), electrical testing, and statistical process control (SPC). Regularly monitor and analyze process data to identify trends and take corrective actions as needed. -
What are the environmental considerations for SMT PCB assembly?
SMT PCB assembly involves the use of lead-based solder alloys, which can have environmental and health impacts. To minimize these impacts, consider using lead-free solder alloys and implementing proper waste management practices. Additionally, ensure proper ventilation and personal protective equipment (PPE) for operators to minimize exposure to fumes and chemicals.
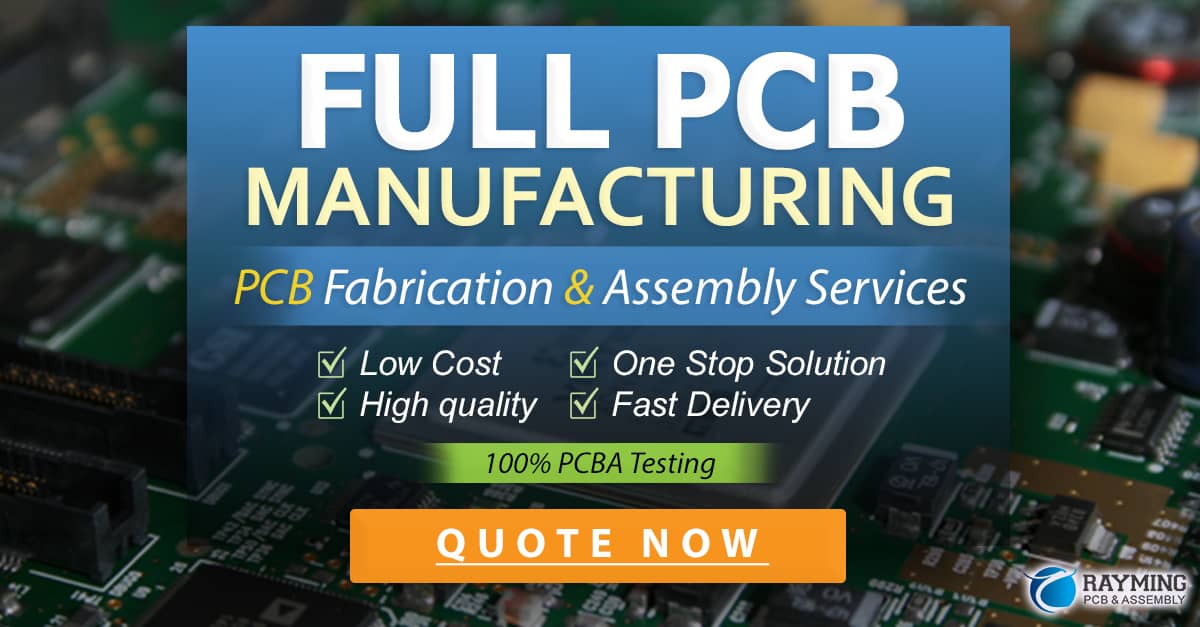
Conclusion
SMT PCB assembly is a complex process that requires careful planning, attention to detail, and adherence to best practices. By following these 9 detailed instructions, you can successfully complete your SMT PCB assembly project and ensure high-quality, reliable electronic assemblies.
Remember to prioritize quality control throughout the assembly process, and don’t hesitate to seek guidance from experienced professionals or industry resources when needed. With practice and continuous improvement, you can master the art of SMT PCB assembly and take your electronic projects to the next level.
Step | Description | Key Considerations |
---|---|---|
1 | Design and Manufacture the PCB | – Component placement and orientation – Pad sizes and shapes – Trace widths and spacing – Thermal management – Electromagnetic compatibility (EMC) |
2 | Prepare the Solder Paste Stencil | – Create stencil design file based on PCB layout – Clean stencil thoroughly before use |
3 | Apply Solder Paste to the PCB | – Align stencil with PCB – Spread solder paste evenly – Inspect solder paste deposits for defects |
4 | Place Components onto the PCB | – Load component feeders into pick and place machine – Program machine with component placement data – Visually inspect placed components |
5 | Reflow Soldering | – Preheat PCB assembly – Gradually increase temperature to melt solder – Cool PCB assembly – Inspect solder joints for defects |
6 | Inspection and Quality Control | – Visually inspect PCB assembly – Use automated optical inspection (AOI) equipment – Perform electrical testing – Document defects and take corrective actions |
7 | Rework and Repair | – Identify defects and locations – Use appropriate tools for rework – Replace defective components – Re-inspect reworked areas |
8 | Conformal Coating (Optional) | – Clean PCB assembly – Apply conformal coating evenly – Cure coating according to manufacturer’s instructions – Inspect coated PCB assembly for defects |
9 | Final Assembly and Packaging | – Attach additional components – Perform final functional testing – Package PCB assembly appropriately – Label packaged product with relevant information |
0 Comments