Introduction to Surface-Mount-Cleaning
Surface-mount technology (SMT) has revolutionized the electronics manufacturing industry by enabling the production of smaller, lighter, and more complex printed circuit boards (PCBs). However, after the surface mount soldering process, it is crucial to clean the PCBs thoroughly to ensure optimal performance and longevity. In this comprehensive article, we will discuss the importance of cleaning PCBs after surface mount soldering and provide step-by-step guidance on how to effectively clean your PCBs.
Why is Surface-Mount-Cleaning Important?
Cleaning PCBs after surface mount soldering is essential for several reasons:
-
Removing flux residues: During the soldering process, flux is used to facilitate the bonding of components to the PCB. However, flux residues can be corrosive and cause long-term damage to the PCB if not removed properly.
-
Preventing short circuits: Excess solder or conductive debris left on the PCB can lead to short circuits, which can cause the device to malfunction or even damage the components.
-
Improving aesthetic appeal: A clean PCB not only functions better but also looks more professional and attractive.
-
Enhancing inspectability: A clean PCB is easier to inspect for any defects or issues, making it simpler to identify and rectify problems during the quality control process.
Types of Contaminants Found on PCBs after Surface Mount Soldering
After surface mount soldering, various contaminants can be found on the PCB, including:
-
Flux residues: Leftover flux from the soldering process can be either water-soluble or rosin-based.
-
Solder balls: Tiny spheres of solder that accidentally adhere to the PCB during the soldering process.
-
Solder bridges: Excess solder that connects adjacent pins or pads, causing short circuits.
-
Dust and debris: Particles that settle on the PCB during the manufacturing process or handling.
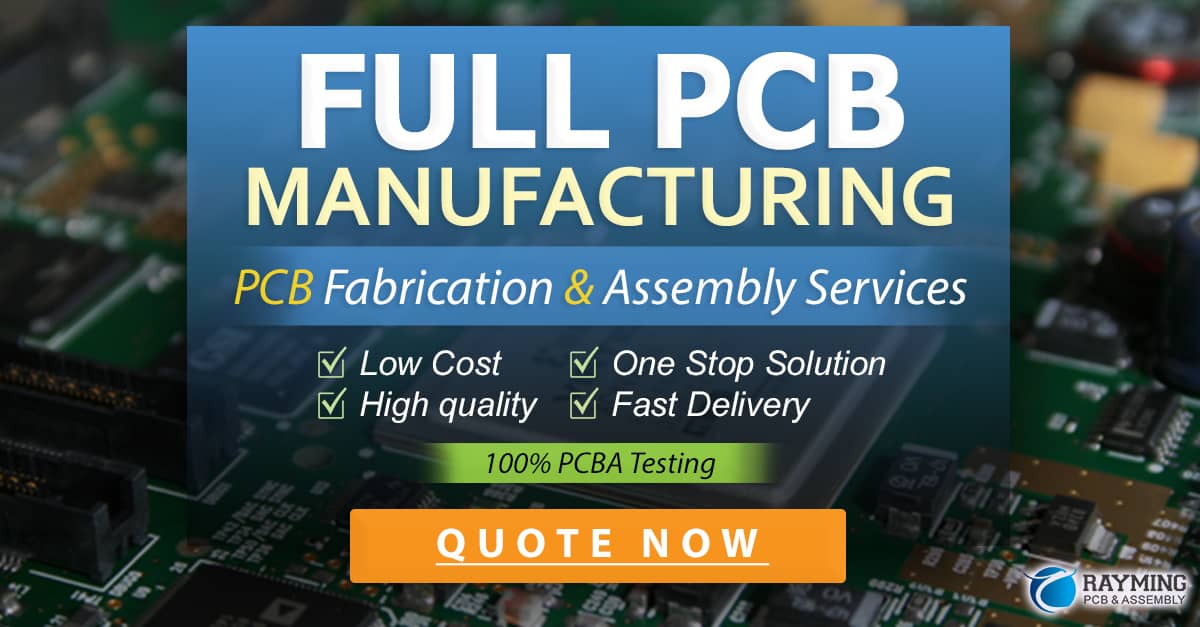
Cleaning Methods for Surface-Mount-Cleaning
There are several methods for cleaning PCBs after surface mount soldering, each with its advantages and disadvantages. The most common cleaning methods include:
Manual Cleaning
Manual cleaning involves using brushes, swabs, or wipes to remove contaminants from the PCB physically. This method is suitable for small-scale production or quick spot-cleaning.
Advantages:
– Low cost
– No special equipment required
– Suitable for small-scale production
Disadvantages:
– Time-consuming
– Labor-intensive
– Inconsistent results
Ultrasonic Cleaning
Ultrasonic cleaning uses high-frequency sound waves to agitate a cleaning solution, creating tiny bubbles that implode and release energy, effectively removing contaminants from the PCB.
Advantages:
– Thorough cleaning
– Efficient for large-scale production
– Suitable for complex PCB designs
Disadvantages:
– Higher initial investment
– Requires specialized equipment
– Potential damage to delicate components
Spray Cleaning
Spray cleaning involves using a pressurized spray of cleaning solution to remove contaminants from the PCB. This method is often combined with other cleaning techniques for optimal results.
Advantages:
– Fast and efficient
– Suitable for large-scale production
– Consistent results
Disadvantages:
– Higher initial investment
– Requires specialized equipment
– Potential for over-spraying and waste
Vapor Degreasing
Vapor degreasing uses a boiling solvent to create a vapor that condenses on the PCB, dissolving and removing contaminants.
Advantages:
– Thorough cleaning
– Suitable for heavy contamination
– Fast and efficient
Disadvantages:
– Higher initial investment
– Requires specialized equipment
– Potential health and environmental concerns
Choosing the Right Cleaning Solution for Surface-Mount-Cleaning
Selecting the appropriate cleaning solution is crucial for effective surface-mount-cleaning. The choice of cleaning solution depends on several factors, such as the type of contaminants, the PCB material, and the cleaning method employed.
Cleaning Solution | Contaminants Removed | Compatibility | Considerations |
---|---|---|---|
Isopropyl Alcohol (IPA) | Flux residues, light oils, grease | Most PCB materials | Flammable, quick evaporation |
Deionized (DI) Water | Water-soluble flux residues, salts | Most PCB materials | May require additional cleaners for non-polar contaminants |
Aqueous Cleaners | Flux residues, oils, greases | Most PCB materials | Requires rinsing and drying |
Solvent-based Cleaners | Stubborn flux residues, heavy oils | Check compatibility with PCB materials | Potential health and environmental concerns |
When choosing a cleaning solution, always consider the manufacturer’s recommendations and ensure compatibility with the PCB materials and components.
Step-by-Step Guide to Cleaning PCBs after Surface Mount Soldering
- Preparation:
- Ensure proper ventilation and wear appropriate personal protective equipment (PPE) such as gloves and safety glasses.
- Disconnect any power sources and remove batteries from the device.
-
Disassemble the device, if necessary, to access the PCB.
-
Dry Cleaning:
- Use an anti-static brush or compressed air to remove loose debris and dust from the PCB gently.
-
Inspect the PCB for any visible contaminants or solder bridges.
-
Cleaning Solution Application:
- Choose an appropriate cleaning solution based on the type of contaminants and PCB materials.
- Apply the cleaning solution using the selected cleaning method (manual, ultrasonic, spray, or vapor degreasing).
-
Ensure that the cleaning solution reaches all areas of the PCB, including hard-to-reach spots.
-
Agitation:
- If using manual cleaning, gently scrub the PCB with a brush or swab to loosen and remove contaminants.
- For ultrasonic cleaning, allow the PCB to soak in the cleaning solution for the recommended duration.
-
In spray cleaning, adjust the pressure and nozzle settings to ensure thorough coverage without damaging the components.
-
Rinsing:
- Rinse the PCB with deionized water or an appropriate solvent to remove any remaining cleaning solution and dissolved contaminants.
-
Ensure that all areas of the PCB are rinsed thoroughly.
-
Drying:
- Use compressed air or a low-temperature oven to dry the PCB completely.
-
Avoid using high temperatures, as they may damage the components or cause warping of the PCB.
-
Inspection:
- Visually inspect the PCB for any remaining contaminants, solder bridges, or damage.
-
Use a magnifying glass or microscope for more detailed inspection, if necessary.
-
Reassembly:
- If the device was disassembled, carefully reassemble it, ensuring that all components are securely in place.
-
Reconnect any power sources or batteries.
-
Final Testing:
- Power on the device and perform any necessary functional tests to ensure that it is working correctly.
- If any issues are detected, repeat the cleaning process or consult with a professional for further assistance.
Common Mistakes to Avoid during Surface-Mount-Cleaning
-
Using incompatible cleaning solutions: Always ensure that the cleaning solution is compatible with the PCB materials and components to avoid damage.
-
Over-scrubbing or using excessive force: Gentle cleaning is key to preventing damage to delicate components and PCB traces.
-
Inadequate rinsing: Failing to rinse the PCB thoroughly can leave behind cleaning solution residues that may cause long-term damage or affect the device’s performance.
-
Improper drying: Insufficient drying or using high temperatures can lead to moisture-related issues or damage to the components.
-
Neglecting safety precautions: Always work in a well-ventilated area and wear appropriate PPE to protect yourself from potential health risks associated with cleaning solutions and solvents.
Frequently Asked Questions (FAQ)
-
How often should I clean my PCBs after surface mount soldering?
It is recommended to clean your PCBs immediately after the soldering process to prevent flux residues and contaminants from causing long-term damage. However, the frequency of cleaning may also depend on the specific application and the environment in which the device will be used. -
Can I use household cleaners to clean my PCBs?
No, it is not advisable to use household cleaners for PCB cleaning, as they may contain substances that can damage the PCB or leave behind residues. Always use cleaning solutions specifically designed for electronics and PCBs. -
Is it necessary to clean PCBs if I’m using no-clean flux?
While no-clean flux is designed to leave minimal residues, it is still recommended to clean the PCBs to ensure optimal performance and longevity. No-clean flux residues can still attract moisture and contaminants over time, which may lead to issues in the long run. -
How do I know if my PCB is clean enough?
A visually clean PCB is a good indication that the cleaning process was successful. However, for critical applications or to ensure thorough cleaning, you can use tools such as ionic contamination testers or perform a visual inspection under a microscope to check for any remaining contaminants. -
Can I reuse the cleaning solution?
It is generally not recommended to reuse cleaning solutions, as they may become contaminated with dissolved flux residues and debris over time. Using contaminated cleaning solutions can lead to ineffective cleaning and may even deposit contaminants back onto the PCB. Always use fresh cleaning solutions for optimal results.
Conclusion
Cleaning PCBs after surface mount soldering is a critical step in ensuring the optimal performance, reliability, and longevity of electronic devices. By understanding the importance of surface-mount-cleaning, the types of contaminants involved, and the various cleaning methods available, you can effectively clean your PCBs and maintain their integrity.
Remember to choose the appropriate cleaning solution, follow the step-by-step cleaning process, and avoid common mistakes to achieve the best results. Regular and thorough cleaning of your PCBs will not only enhance their functionality but also contribute to the overall success of your electronic projects.
0 Comments