What is PCB Drilling?
PCB drilling is the process of creating holes in a printed circuit board substrate to accommodate components and establish electrical connections between layers. These holes can be categorized into two main types:
- Through holes: These holes extend through the entire thickness of the PCB and are used for mounting components or creating electrical connections between layers.
- Blind and buried vias: These holes connect inner layers of the PCB without extending to the outer surfaces. Blind vias start from an outer layer and terminate at an inner layer, while buried vias connect two or more inner layers without reaching the outer surfaces.
Types of Drills Used in PCB Manufacturing
Several types of drills are used in the PCB manufacturing process, each with its own advantages and applications. Let’s explore the most common types:
Mechanical Drills
Mechanical drills are the most widely used type of drill in PCB manufacturing. They consist of a rotating drill bit that physically removes material from the PCB substrate to create holes. Mechanical drills can be further classified into two categories:
- Standard twist drills: These drills have a cylindrical shape with two or more cutting edges spiraling around the axis. They are suitable for drilling through holes and are available in a wide range of sizes.
- Stepped drills: These drills have multiple diameters along their length, allowing them to create holes with different diameters in a single operation. Stepped drills are often used for creating countersink or counterbore holes.
Laser Drills
Laser drilling is a non-contact method that uses high-energy laser beams to vaporize the PCB substrate material, creating precise holes. Laser drills offer several advantages over mechanical drills:
- Higher precision: Laser drills can create holes with diameters as small as 25 microns, making them ideal for high-density PCB designs.
- No wear and tear: Since laser drilling is a non-contact process, there is no physical wear on the drill bit, resulting in consistent hole quality and reduced maintenance costs.
- Faster drilling speeds: Laser drills can create holes at a much faster rate compared to mechanical drills, reducing the overall manufacturing time.
However, laser drilling is generally more expensive than mechanical drilling and may not be suitable for all PCB materials.
Plasma Drills
Plasma drilling is another non-contact method that uses a high-energy plasma beam to remove material from the PCB substrate. The plasma beam is generated by ionizing a gas, such as argon or nitrogen, and focusing it onto the PCB surface. Plasma drills offer similar advantages to laser drills, including high precision, no wear and tear, and fast drilling speeds.
The PCB Drilling Process
The PCB drilling process typically involves the following steps:
- Drill file generation: The PCB design software generates a drill file that contains information about the hole locations, sizes, and types.
- Drill program creation: The drill file is used to create a drill program, which includes the sequence of drilling operations and tool changes.
- Drilling machine setup: The PCB panels are loaded into the drilling machine, and the appropriate drill bits are installed.
- Drilling operation: The drilling machine executes the drill program, creating holes in the PCB panels according to the specified locations and sizes.
- Inspection and cleaning: After drilling, the PCB panels are inspected for accuracy and cleaned to remove any debris or burrs.
Step | Description |
---|---|
Drill file generation | PCB design software generates a drill file with hole locations, sizes, and types. |
Drill program creation | Drill file is used to create a drill program with the sequence of drilling operations and tool changes. |
Drilling machine setup | PCB panels are loaded into the drilling machine, and appropriate drill bits are installed. |
Drilling operation | Drilling machine executes the drill program, creating holes in the PCB panels according to specifications. |
Inspection and cleaning | PCB panels are inspected for accuracy and cleaned to remove debris or burrs after drilling. |
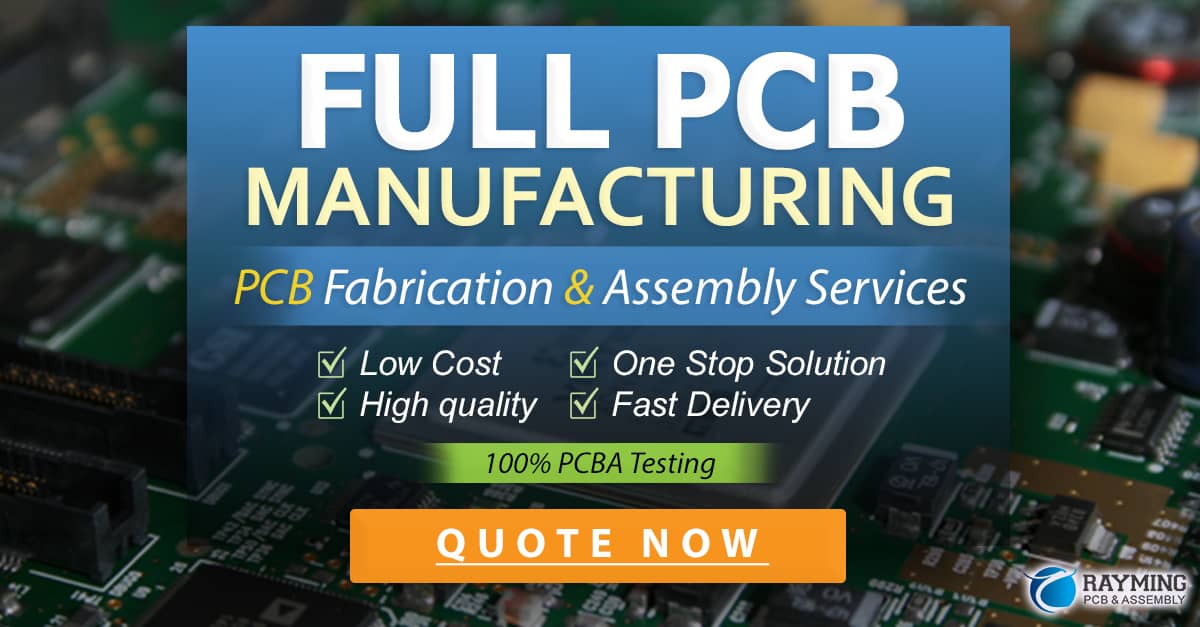
Common Challenges in PCB Drilling
Several challenges can arise during the PCB drilling process, affecting the quality and reliability of the final product. Some of the most common challenges include:
Hole Size and Position Accuracy
Maintaining accurate hole sizes and positions is crucial for ensuring proper component fit and electrical connections. Factors that can impact hole accuracy include:
- Drill bit wear and breakage
- Spindle runout and vibration
- Material thickness variations
- Thermal expansion and contraction of the PCB substrate
To minimize these issues, it is essential to use high-quality drill bits, regularly maintain and calibrate the drilling equipment, and implement proper drilling parameters and feed rates.
Burrs and Smear
Burrs are raised edges or protrusions around the drilled holes, while smear is a thin layer of melted material that can coat the hole walls. Both burrs and smear can interfere with proper component insertion and electrical connections. To reduce burrs and smear:
- Use sharp, high-quality drill bits
- Optimize drilling parameters, such as spindle speed and feed rate
- Implement a deburring process, such as mechanical or chemical deburring
- Use an anti-smear coating on the drill bits or an anti-smear treatment on the PCB substrate
Delamination and Tear-Out
Delamination is the separation of the PCB layers due to the stresses induced during the drilling process. Tear-out occurs when the drill bit exits the PCB, causing the material to break or tear around the hole exit. To minimize delamination and tear-out:
- Use a backing material to support the PCB during drilling
- Optimize drilling parameters to reduce stress on the PCB substrate
- Implement a multi-step drilling process for thicker PCBs
- Use a drill bit with a reduced chisel edge to minimize tear-out
Hole Wall Quality
The quality of the hole walls is essential for ensuring reliable electrical connections and preventing signal integrity issues. Factors that can affect hole wall quality include:
- Drill bit geometry and coating
- Drilling parameters, such as spindle speed and feed rate
- PCB material properties and thickness
- Cooling and lubrication during the drilling process
To improve hole wall quality, use drill bits with optimized geometry and coatings, adjust drilling parameters based on the PCB material and thickness, and ensure proper cooling and lubrication during the drilling process.
Best Practices for PCB Drilling Design
To optimize PCB drilling and minimize potential issues, consider the following best practices when designing your PCBs:
- Use standard hole sizes: Whenever possible, use standard hole sizes to reduce tooling costs and improve drilling efficiency.
- Maintain proper hole-to-copper clearance: Ensure that there is sufficient clearance between the drilled holes and the copper traces to prevent short circuits and signal integrity issues.
- Avoid drilling through copper: When possible, design your PCBs so that drilling does not occur through copper layers, as this can cause burrs and smear.
- Use teardrops and anchors: Incorporate teardrops and anchors at the intersection of drilled holes and copper traces to strengthen the connection and prevent tear-out.
- Consider via type and placement: Choose the appropriate via type (through hole, blind, or buried) based on your design requirements and place vias strategically to minimize drilling complexity and cost.
- Optimize drill bit selection: Select drill bits with the appropriate geometry, coating, and size for your specific PCB material and thickness to ensure optimal hole quality and drilling performance.
- Communicate with your manufacturer: Work closely with your PCB manufacturer to discuss your drilling requirements, design constraints, and any potential challenges to ensure the best possible results.
FAQ
1. What is the difference between through holes and vias?
Through holes extend through the entire thickness of the PCB and are used for mounting components or creating electrical connections between layers. Vias, on the other hand, are used to connect different layers of the PCB without necessarily extending to the outer surfaces. Blind vias start from an outer layer and terminate at an inner layer, while buried vias connect two or more inner layers without reaching the outer surfaces.
2. What are the advantages of laser drilling compared to mechanical drilling?
Laser drilling offers several advantages over mechanical drilling, including higher precision (with hole diameters as small as 25 microns), no wear and tear on the drill bit, and faster drilling speeds. However, laser drilling is generally more expensive than mechanical drilling and may not be suitable for all PCB materials.
3. How can I minimize burrs and smear during the PCB drilling process?
To reduce burrs and smear, use sharp, high-quality drill bits, optimize drilling parameters (such as spindle speed and feed rate), implement a deburring process (mechanical or chemical), and consider using an anti-smear coating on the drill bits or an anti-smear treatment on the PCB substrate.
4. What is the importance of hole wall quality in PCB drilling?
The quality of the hole walls is essential for ensuring reliable electrical connections and preventing signal integrity issues. Factors that can affect hole wall quality include drill bit geometry and coating, drilling parameters, PCB material properties and thickness, and cooling and lubrication during the drilling process.
5. How can I optimize my PCB design for drilling?
To optimize your PCB design for drilling, consider using standard hole sizes, maintaining proper hole-to-copper clearance, avoiding drilling through copper layers when possible, using teardrops and anchors to strengthen connections, selecting the appropriate via type and placement, optimizing drill bit selection, and communicating with your PCB manufacturer to discuss drilling requirements and potential challenges.
Conclusion
PCB drilling is a critical step in the manufacturing process, and understanding its various aspects is essential for designing high-quality, reliable PCBs. By familiarizing yourself with the different types of drills, the drilling process, common challenges, and best practices for PCB drilling design, you can optimize your designs and collaborate effectively with your PCB manufacturer to ensure the best possible results.
Remember to consider factors such as hole size and position accuracy, burrs and smear, delamination and tear-out, and hole wall quality when designing your PCBs. Implementing best practices, such as using standard hole sizes, maintaining proper clearances, and optimizing drill bit selection, can help you minimize potential issues and achieve optimal drilling performance.
As PCB technology continues to advance, staying up-to-date with the latest drilling techniques and best practices will be crucial for designing cutting-edge, high-performance PCBs. By continuously expanding your knowledge of PCB drilling and working closely with your manufacturing partners, you can push the boundaries of PCB design and create innovative solutions for a wide range of applications.
0 Comments