Introduction to DIY PCB Boards
Are you fascinated by the world of electronics and eager to create your own custom printed circuit boards (PCBs)? Look no further! In this comprehensive guide, we’ll walk you through the process of making your very own PCB Board from scratch. Whether you’re a hobbyist, a student, or simply curious about the inner workings of electronic devices, this article will provide you with the knowledge and tools to embark on your DIY PCB journey.
What is a PCB?
Before we dive into the nitty-gritty of creating a PCB, let’s first understand what it is. A printed circuit board, or PCB, is a thin board made of fiberglass or other composite materials that serves as the foundation for electronic components in various devices. PCBs provide mechanical support and electrical connections between components through conductive tracks, pads, and other features etched on the board.
Advantages of DIY PCB Boards
Creating your own PCB board offers several advantages:
- Customization: DIY PCBs allow you to design and tailor the board to your specific project requirements.
- Cost-effective: Making your own PCB can be more economical compared to purchasing pre-made boards or outsourcing the fabrication process.
- Learning experience: Building a PCB from scratch provides hands-on experience and deepens your understanding of electronics and circuit design.
- Rapid prototyping: With DIY PCBs, you can quickly iterate and refine your designs, enabling faster prototyping and testing.
Tools and Materials Required
To get started with your DIY PCB project, you’ll need the following tools and materials:
Tool/Material | Description |
---|---|
PCB design software | Software used to create schematic diagrams and PCB layouts (e.g., KiCad, Eagle) |
Copper-clad board | A thin board with a layer of copper on one or both sides |
Laser printer | Used to print the PCB design onto a transfer paper |
Transfer paper | Special paper used to transfer the PCB design onto the copper-clad board |
Clothes iron | Used to transfer the design from the transfer paper to the copper-clad board |
Etchant solution | A chemical solution used to remove unwanted copper from the board (e.g., ferric chloride) |
Drill or drill press | Used to drill holes for through-hole components |
Soldering iron and solder | Used to solder components onto the PCB |
Safety equipment | Gloves, goggles, and a well-ventilated workspace |
Step-by-Step Guide to Making a DIY PCB Board
Step 1: Design Your PCB
The first step in creating your DIY PCB is to design the circuit using PCB design software. Popular software options include KiCad and Eagle. These software tools allow you to create schematic diagrams and PCB layouts.
- Create a new project in your chosen PCB design software.
- Design the schematic diagram by placing components and connecting them with wires.
- Convert the schematic diagram into a PCB layout, arranging the components and routing the traces.
- Ensure proper trace widths, spacing, and design rules are followed.
- Generate Gerber files, which are the standard format for PCB Fabrication.
Step 2: Print the PCB Design
Once your PCB design is complete, it’s time to transfer it onto the copper-clad board. Follow these steps:
- Print the PCB design onto a transfer paper using a laser printer. Make sure to print on the glossy side of the paper.
- Cut out the printed design, leaving some margin around the edges.
- Clean the copper-clad board with fine sandpaper or a scouring pad to remove any oxidation and ensure good adhesion.
- Place the transfer paper onto the copper-clad board, with the printed side facing down.
- Use a clothes iron set to its highest setting (without steam) to apply heat and pressure evenly over the transfer paper for several minutes.
- Carefully peel off the transfer paper, ensuring the toner has fully transferred onto the copper-clad board.
Step 3: Etch the PCB
With the PCB design transferred onto the copper-clad board, it’s time to remove the unwanted copper using an etchant solution. Here’s how:
- Prepare the etchant solution according to the manufacturer’s instructions. Ferric chloride is a commonly used etchant.
- Wearing gloves and protective eyewear, immerse the PCB into the etchant solution.
- Agitate the solution gently to ensure even etching.
- Monitor the etching process closely. It typically takes 10-30 minutes, depending on the strength of the etchant and the size of the PCB.
- Once the unwanted copper is completely removed, take the PCB out of the solution and rinse it thoroughly with water.
- Clean the remaining toner from the PCB using acetone or a specialized PCB cleaner.
Step 4: Drill Holes and Solder Components
With the PCB etched, it’s time to drill holes for through-hole components and solder them onto the board. Follow these steps:
- Using a drill or drill press, carefully drill holes at the designated locations for through-hole components.
- Place the components into their respective holes on the PCB.
- Flip the board over and solder the component leads to the PCB pads using a soldering iron and solder.
- Trim any excess component leads using wire cutters.
- Inspect the soldered joints for any bridges or poor connections, and make necessary repairs.
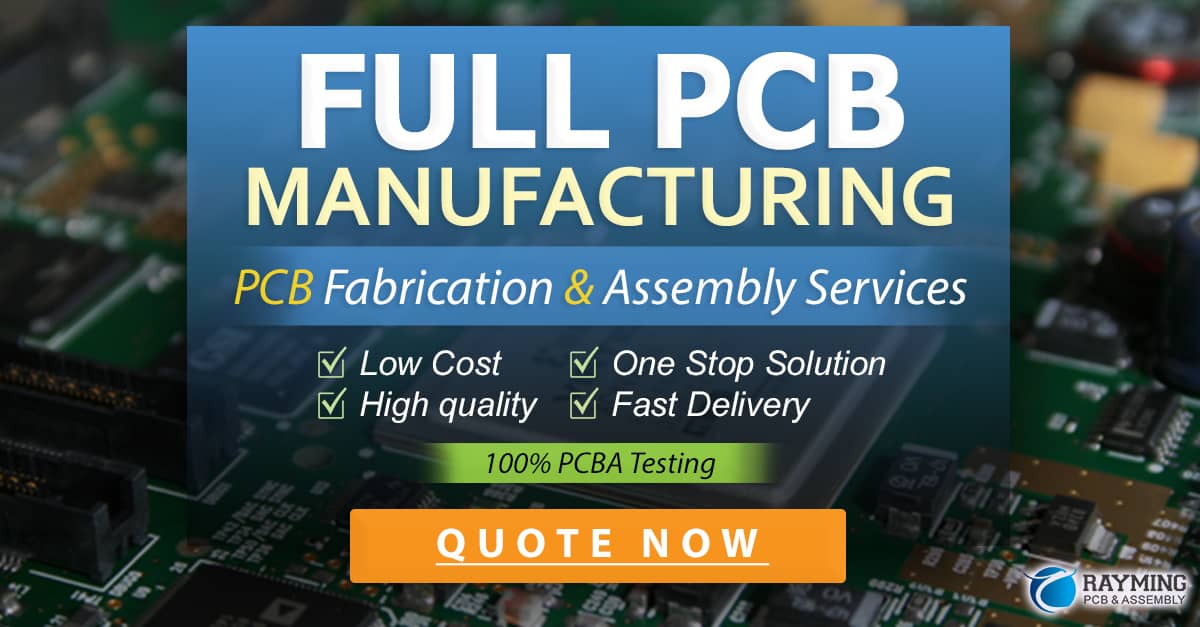
Tips and Tricks for Successful DIY PCB Fabrication
- Double-check your design: Before printing and etching, thoroughly review your PCB design for any errors or design rule violations.
- Use high-quality materials: Invest in good-quality copper-clad boards, transfer paper, and etchant solution for best results.
- Maintain a clean workspace: Keep your work area clean and organized to avoid contamination and ensure precise results.
- Practice proper safety measures: Always wear gloves, goggles, and work in a well-ventilated area when handling chemicals and solder.
- Start with simple designs: As a beginner, start with basic PCB designs and gradually work your way up to more complex layouts.
Frequently Asked Questions (FAQ)
-
Can I make double-sided PCBs using this method?
Yes, you can make double-sided PCBs using the toner transfer method. However, it requires precise alignment and registration of the designs on both sides of the board. -
What is the minimum trace width and spacing I can achieve with DIY PCBs?
The minimum trace width and spacing achievable with DIY PCBs depend on factors such as the resolution of your printer, the quality of the transfer paper, and your etching process. Generally, trace widths of 0.3mm to 0.5mm and spacing of 0.3mm to 0.4mm are achievable with careful design and execution. -
Can I reuse the etchant solution?
Yes, you can reuse the etchant solution multiple times until it becomes saturated with copper and loses its effectiveness. However, it’s essential to store the solution properly and dispose of it responsibly when it’s no longer usable. -
How can I add text and labels to my PCB?
Most PCB design software allows you to add text and labels to your PCB layout. These labels will be etched onto the board along with the traces and pads. -
What should I do if my PCB doesn’t work after assembly?
If your PCB doesn’t function as expected after assembly, troubleshoot the following: - Check for any bridged or shorted connections.
- Verify the component placement and orientation.
- Ensure proper soldering and connectivity.
- Double-check your PCB design for any errors or missing connections.
- Use a multimeter to test continuity and identify any potential issues.
Conclusion
Creating your own PCB board from scratch is an exciting and rewarding experience. By following this step-by-step guide and utilizing the right tools and materials, you can design, etch, and assemble your very own DIY PCB. Whether you’re working on a personal project or exploring the world of electronics, the skills and knowledge gained through this process will be invaluable.
Remember to start with simple designs, prioritize safety, and be patient throughout the fabrication process. As you gain experience and confidence, you can take on more complex projects and explore advanced techniques.
So, grab your tools, fire up your PCB design software, and embark on your DIY PCB journey today! Happy PCB making!
0 Comments