Introduction to High-Voltage PCB Design
High-voltage printed circuit boards (PCBs) are essential components in various applications, including power supplies, industrial control systems, and medical equipment. Designing high-voltage PCBs requires careful consideration of several factors to ensure reliable performance, safety, and longevity. In this article, we will explore the key aspects of high-voltage PCB design and provide insights on how to create PCBs that meet your specific requirements.
Understanding the Challenges of High-Voltage PCB Design
Designing high-voltage PCBs comes with unique challenges that must be addressed to ensure proper functionality and safety. Some of the main challenges include:
- Insulation and creepage distances
- Material selection
- Component placement and routing
- Thermal management
- Electromagnetic interference (EMI) and electromagnetic compatibility (EMC)
By understanding these challenges and implementing appropriate design techniques, you can create high-voltage PCBs that perform reliably and meet industry standards.
Key Considerations for High-Voltage PCB Design
Insulation and Creepage Distances
One of the most critical aspects of high-voltage PCB design is maintaining proper insulation and creepage distances. Insulation refers to the distance through the insulating material between two conductive parts, while creepage is the shortest distance along the surface of the insulating material between two conductive parts.
The required insulation and creepage distances depend on factors such as:
- Operating voltage
- Pollution degree
- Material group (CTI)
- Altitude
To determine the appropriate distances, refer to standards such as IEC 60950-1 or IEC 61010-1. These standards provide guidelines for calculating the minimum required distances based on the aforementioned factors.
Voltage (V) | Pollution Degree | Material Group (CTI) | Minimum Creepage Distance (mm) |
---|---|---|---|
≤ 250 | 1 | I | 1.25 |
≤ 250 | 2 | I | 1.5 |
≤ 250 | 3 | I | 2.0 |
> 250 to ≤ 500 | 1 | I | 2.5 |
> 250 to ≤ 500 | 2 | I | 3.0 |
> 250 to ≤ 500 | 3 | I | 4.0 |
Table 1: Minimum creepage distances based on voltage, pollution degree, and material group (adapted from IEC 60950-1).
Material Selection
Choosing the right materials for your high-voltage PCB is crucial for ensuring proper insulation and heat dissipation. The most common base material for high-voltage PCBs is FR-4, which offers good mechanical and electrical properties. However, for more demanding applications, specialized materials such as ceramics, polyimides, or PTFE may be required.
When selecting materials, consider the following properties:
- Dielectric strength
- Comparative Tracking Index (CTI)
- Thermal conductivity
- Coefficient of thermal expansion (CTE)
- Moisture absorption
Component Placement and Routing
Proper component placement and routing are essential for minimizing electromagnetic interference (EMI) and ensuring reliable performance. When placing components on a high-voltage PCB, consider the following guidelines:
- Group components based on their voltage levels and functions
- Maintain appropriate spacing between components and traces
- Use guard rings or equipotential planes to isolate high-voltage areas
- Minimize the loop area of high-current traces to reduce EMI
- Use appropriate trace widths and copper weights to handle the required current
Thermal Management
High-voltage PCBs often generate significant amounts of heat, which must be dissipated effectively to prevent component failure and ensure long-term reliability. To manage thermal issues, consider the following techniques:
- Use thermal vias to conduct heat away from components
- Incorporate heatsinks or cooling fans for high-power components
- Use thermal interface materials (TIMs) to improve heat transfer
- Design your PCB layout to promote natural convection cooling
- Monitor temperature-sensitive components using sensors and control circuitry
Electromagnetic Interference (EMI) and Electromagnetic Compatibility (EMC)
High-voltage PCBs can be sources of electromagnetic interference (EMI) and must be designed to meet electromagnetic compatibility (EMC) requirements. To minimize EMI and ensure EMC compliance, consider the following strategies:
- Use shielding techniques, such as grounded enclosures or shielding gaskets
- Implement proper grounding and bonding techniques
- Use filters and suppressors to attenuate noise
- Minimize the use of high-frequency components or use spread-spectrum techniques
- Conduct EMC testing to ensure compliance with relevant standards
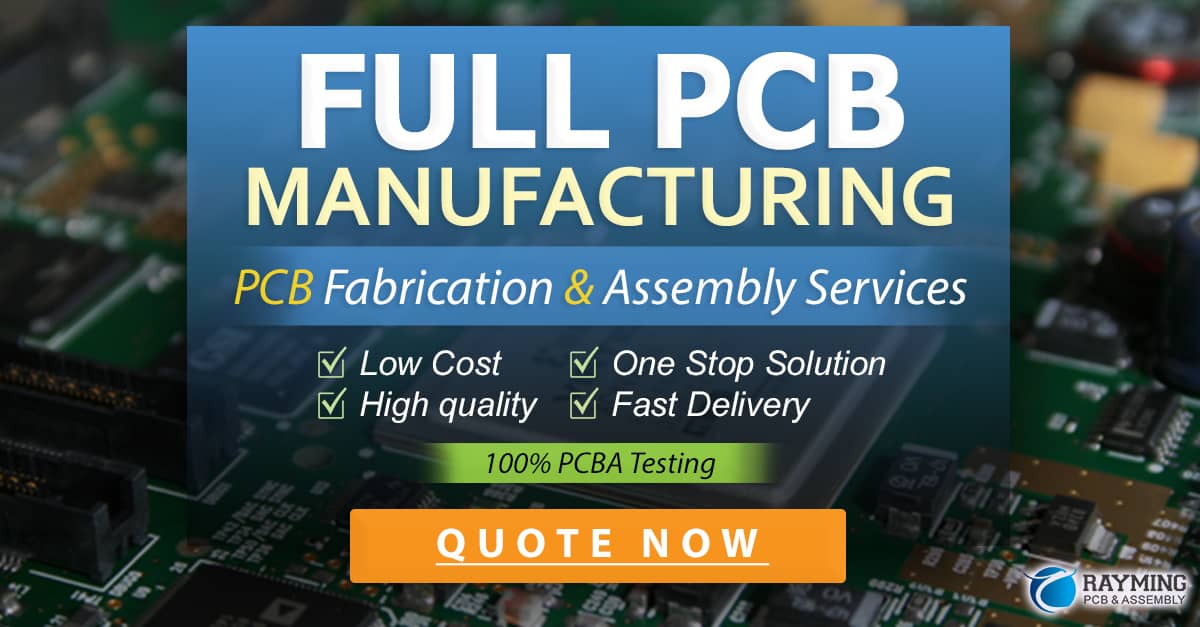
PCB Layout Techniques for High-Voltage Design
Layer Stackup
A well-designed layer stackup is crucial for high-voltage PCBs. A typical high-voltage PCB Stackup may include the following layers:
- Top layer: Components and high-voltage traces
- Ground plane: Provides shielding and reduces EMI
- Power plane: Distributes power to components
- Signal layers: Route low-voltage signals
- Bottom layer: Components and high-voltage traces
Ensure that the layer stackup provides adequate insulation between high-voltage and low-voltage layers, and use appropriate spacing between layers to minimize capacitive coupling.
Trace Routing
When routing traces on a high-voltage PCB, follow these guidelines:
- Use appropriate trace widths and copper weights based on the required current carrying capacity
- Maintain sufficient spacing between traces to prevent arcing and minimize crosstalk
- Use 45-degree angles instead of 90-degree angles to reduce electric field concentrations
- Avoid routing traces near board edges or through connector pins
- Use guard traces or equipotential planes to isolate high-voltage traces
Grounding and Shielding
Proper grounding and shielding are essential for ensuring the safety and reliability of high-voltage PCBs. When designing your PCB, consider the following grounding and shielding techniques:
- Use a single-point ground to avoid ground loops
- Implement a ground plane to provide a low-impedance return path and reduce EMI
- Use shielding techniques, such as grounded enclosures or shielding gaskets, to contain EMI
- Ensure proper bonding between ground planes, shields, and enclosures
- Use ground stitching vias to provide a low-impedance connection between ground planes
Testing and Verification
After designing and manufacturing your high-voltage PCB, it is essential to conduct thorough testing and verification to ensure proper functionality, safety, and compliance with relevant standards. Some of the key tests include:
- Insulation resistance testing
- Dielectric withstand testing (HiPot Testing)
- Leakage current testing
- Functional testing
- EMC testing
By conducting these tests and addressing any issues that arise, you can ensure that your high-voltage PCB meets your design requirements and is ready for use in your application.
FAQ
1. What is the difference between insulation and creepage distance?
Insulation distance refers to the shortest distance through the insulating material between two conductive parts, while creepage distance is the shortest distance along the surface of the insulating material between two conductive parts.
2. What are the most common base materials used for high-voltage PCBs?
The most common base material for high-voltage PCBs is FR-4. However, for more demanding applications, specialized materials such as ceramics, polyimides, or PTFE may be required.
3. How can I minimize electromagnetic interference (EMI) in high-voltage PCBs?
To minimize EMI in high-voltage PCBs, you can use shielding techniques, implement proper grounding and bonding, use filters and suppressors, minimize the use of high-frequency components, and conduct EMC testing to ensure compliance with relevant standards.
4. What are some key considerations for component placement on high-voltage PCBs?
When placing components on a high-voltage PCB, consider grouping components based on their voltage levels and functions, maintaining appropriate spacing between components and traces, using guard rings or equipotential planes to isolate high-voltage areas, minimizing the loop area of high-current traces, and using appropriate trace widths and copper weights.
5. What types of testing should be conducted on high-voltage PCBs?
Key tests for high-voltage PCBs include insulation resistance testing, dielectric withstand testing (hipot testing), leakage current testing, functional testing, and EMC testing.
Conclusion
Designing high-voltage PCBs requires careful consideration of various factors, including insulation and creepage distances, material selection, component placement and routing, thermal management, and EMI/EMC. By understanding the challenges and implementing appropriate design techniques, you can create high-voltage PCBs that perform reliably, safely, and meet your specific requirements.
Remember to refer to relevant industry standards, conduct thorough testing and verification, and stay up-to-date with the latest advancements in high-voltage PCB technology. With the right approach and attention to detail, you can design high-voltage PCBs that exceed your expectations and contribute to the success of your projects.
0 Comments