What are HDI PCBs?
High-Density Interconnect (HDI) Printed Circuit Boards, also known as HDI PCBs, are a type of advanced circuit board that feature higher wiring density per unit area compared to conventional PCBs. These boards are designed to accommodate a greater number of components and interconnections in a smaller space, enabling the development of more compact, lightweight, and high-performance electronic devices.
HDI PCBs are characterized by their fine line widths, small via diameters, and high connection pad density. They often incorporate multiple layers of copper interconnects, with microvias used to connect between layers. This allows for shorter signal paths, reduced signal loss, and improved signal integrity, making HDI PCBs ideal for high-speed and high-frequency applications.
Advantages of HDI PCBs
1. Miniaturization and Space Savings
One of the primary advantages of HDI PCBs is their ability to enable miniaturization of electronic devices. With the increasing demand for smaller, more portable, and functionally dense products, HDI technology allows designers to pack more components and interconnections into a limited space. This space-saving capability is particularly valuable in applications such as smartphones, wearables, and medical devices, where size and weight are critical factors.
2. Enhanced Electrical Performance
HDI PCBs offer improved electrical performance compared to traditional PCBs. The shorter signal paths and reduced layer count in HDI designs minimize signal loss, crosstalk, and electromagnetic interference (EMI). The use of microvias and blind/buried vias also contributes to better signal integrity by providing more direct connections between layers. These characteristics make HDI PCBs well-suited for high-speed digital circuits, high-frequency RF applications, and designs with strict signal integrity requirements.
3. Increased Reliability
The manufacturing processes and materials used in HDI PCBs contribute to their increased reliability. The use of laser drilling for microvias results in precise and consistent via formation, reducing the risk of manufacturing defects. Additionally, the smaller via sizes and shorter signal paths in HDI designs lead to reduced thermal stress and improved thermal management. These factors collectively enhance the overall reliability and longevity of the PCB Assembly.
4. Cost Reduction
Although the initial design and fabrication costs of HDI PCBs may be higher compared to traditional PCBs, they offer long-term cost savings in several ways. The miniaturization enabled by HDI technology allows for smaller device footprints, reducing material costs and saving on overall system size and packaging. Moreover, the improved electrical performance and reliability of HDI PCBs can lead to reduced testing and rework costs, as well as lower field failure rates and warranty expenses.
HDI PCB Design Considerations
1. Layer Stack-up
The layer stack-up is a critical aspect of HDI PCB design. It determines the arrangement and interconnection of the conductive layers and dielectric materials. A typical HDI PCB stack-up may include a combination of signal layers, power/ground planes, and microvias. The number of layers and their sequence depend on the specific design requirements, such as signal integrity, power distribution, and EMI Shielding. Careful consideration should be given to the layer stack-up to ensure optimal performance and manufacturability.
2. Via Technology
HDI PCBs heavily rely on advanced via technologies to achieve high interconnect density. Microvias, with diameters typically less than 150 microns, are commonly used to connect between layers. There are several types of microvias, including blind vias (connecting outer layers to inner layers), buried vias (connecting inner layers), and through-hole vias (connecting all layers). The selection of via technology depends on the design requirements, layer stack-up, and manufacturing capabilities. Designers must adhere to the via design rules specified by the PCB manufacturer to ensure proper fabrication and reliability.
3. Signal Integrity
Signal integrity is a critical consideration in HDI PCB design, especially for high-speed and high-frequency applications. Factors such as trace width, spacing, impedance matching, and termination play a significant role in maintaining signal quality. Designers must carefully route traces to minimize crosstalk, reflections, and signal distortion. Simulation tools and analysis techniques, such as signal integrity analysis and electromagnetic simulation, are often employed to optimize the design and ensure robust signal performance.
4. Thermal Management
HDI PCBs, with their high component density and increased power dissipation, require careful thermal management. Proper thermal design is essential to prevent overheating, ensure reliable operation, and prolong the life of the PCB assembly. Thermal management techniques for HDI PCBs include the use of thermal vias, heat spreaders, and thermal interface materials. Designers must also consider the placement and orientation of components to facilitate heat dissipation and avoid hot spots.
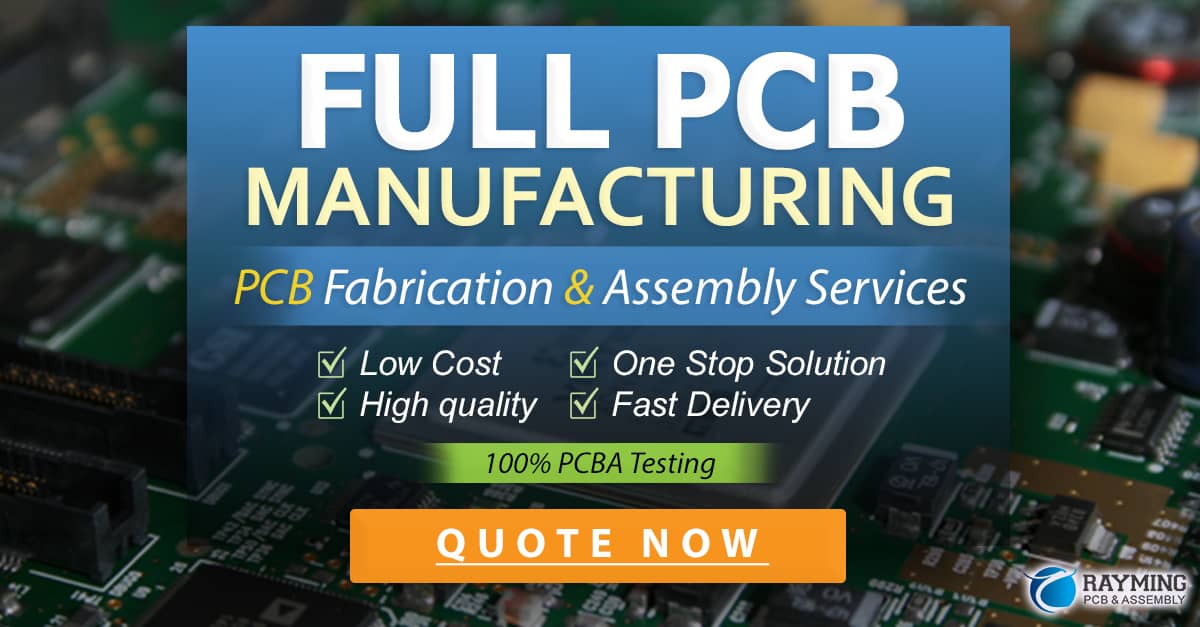
HDI PCB Manufacturing Process
The manufacturing process for HDI PCBs involves several advanced techniques and technologies to achieve the required precision and reliability. Some key steps in the HDI PCB manufacturing process include:
-
Material Selection: The choice of base materials, such as the substrate and copper foil, is crucial for HDI PCBs. High-quality, high-performance materials with good thermal and electrical properties are typically used to ensure the desired performance and reliability.
-
Patterning: The conductive patterns on the PCB Layers are created through a photolithography process. High-resolution photomasks and advanced imaging systems are employed to achieve fine line widths and precise feature sizes.
-
Drilling: Mechanical drilling is used to create through-holes, while laser drilling is commonly used for microvias. Laser drilling offers high precision and the ability to create small-diameter vias, which is essential for HDI PCB fabrication.
-
Plating: The drilled vias and conductive patterns are plated with copper to establish electrical connections between layers. Various plating techniques, such as electroless and electrolytic plating, are used depending on the specific requirements.
-
Lamination: The individual PCB layers are laminated together under high pressure and temperature to form a solid, multilayer structure. The lamination process ensures proper bonding and alignment of the layers.
-
Surface Finish: A surface finish, such as ENIG (Electroless Nickel Immersion Gold) or OSP (Organic Solderability Preservative), is applied to the exposed copper surfaces to protect against oxidation and enhance solderability.
-
Inspection and Testing: Rigorous inspection and testing procedures are carried out to ensure the quality and reliability of the manufactured HDI PCBs. This includes visual inspection, electrical testing, and automated optical inspection (AOI) to detect any defects or anomalies.
Applications of HDI PCBs
HDI PCBs find applications in a wide range of industries and products where high performance, miniaturization, and reliability are critical. Some common applications include:
-
Consumer Electronics: Smartphones, tablets, wearables, and other portable devices extensively use HDI PCBs to achieve compact form factors and high functionality.
-
Telecommunications: HDI PCBs are used in communication equipment, such as routers, switches, and base stations, to handle high-speed data transmission and complex signal processing.
-
Automotive Electronics: Advanced driver assistance systems (ADAS), infotainment systems, and electronic control units (ECUs) in vehicles rely on HDI PCBs for reliable and high-performance operation.
-
Medical Devices: HDI PCBs are used in medical equipment, such as implantable devices, diagnostic tools, and monitoring systems, where miniaturization, reliability, and high precision are essential.
-
Aerospace and Defense: Avionics systems, radar equipment, and military communication devices employ HDI PCBs to meet the stringent requirements of size, weight, and performance in harsh environments.
-
Industrial Automation: HDI PCBs are used in industrial control systems, sensors, and automation equipment to enable high-density interconnections and reliable operation in industrial settings.
Future Trends in HDI PCBs
As technology continues to advance and the demand for miniaturization and high performance grows, HDI PCBs are expected to evolve further. Some future trends in HDI PCB technology include:
-
Increased Density: The trend towards even higher interconnect densities and finer feature sizes will continue, enabling the development of more compact and functionally dense electronic devices.
-
Advanced Materials: The adoption of advanced materials, such as low-loss dielectrics and high-performance substrates, will enhance the electrical and thermal performance of HDI PCBs.
-
3D Packaging: The integration of HDI PCBs with 3D packaging technologies, such as through-silicon vias (TSVs) and chip-on-board (CoB), will enable the development of highly integrated and vertically stacked electronic assemblies.
-
Embedded Components: The embedding of passive components, such as resistors and capacitors, within the PCB layers will further increase the component density and reduce the overall footprint of HDI PCBs.
-
Intelligent HDI: The incorporation of intelligent features, such as embedded sensors, self-diagnostics, and adaptive power management, will enable HDI PCBs to offer enhanced functionality and self-monitoring capabilities.
Frequently Asked Questions (FAQ)
1. What is the difference between HDI PCBs and traditional PCBs?
HDI PCBs differ from traditional PCBs in terms of their higher interconnect density, finer feature sizes, and the use of advanced technologies such as microvias and blind/buried vias. HDI PCBs offer improved electrical performance, miniaturization, and reliability compared to traditional PCBs.
2. What are the benefits of using HDI PCBs in electronic devices?
The benefits of using HDI PCBs include:
– Miniaturization and space savings
– Enhanced electrical performance and signal integrity
– Increased reliability and durability
– Potential for cost reduction through reduced material usage and improved yields
3. What are the common applications of HDI PCBs?
HDI PCBs are commonly used in various applications, including consumer electronics (smartphones, wearables), telecommunications equipment, automotive electronics, medical devices, aerospace and defense systems, and industrial automation.
4. What are the key design considerations for HDI PCBs?
The key design considerations for HDI PCBs include:
– Layer stack-up configuration
– Via technology selection (microvias, blind/buried vias)
– Signal integrity analysis and optimization
– Thermal management and heat dissipation
– Adherence to manufacturer’s design rules and guidelines
5. What are the future trends in HDI PCB technology?
The future trends in HDI PCB technology include increased interconnect density, adoption of advanced materials, integration with 3D packaging technologies, embedding of passive components, and the incorporation of intelligent features for enhanced functionality and self-monitoring capabilities.
0 Comments