What is a Heavy Copper PCB?
A Heavy Copper Printed Circuit Board (PCB) is a specialized type of PCB that uses thicker copper traces and planes compared to standard PCBs. The increased copper thickness allows for higher current carrying capacity, improved thermal management, and enhanced mechanical strength.
Typical PCB Copper weights range from 0.5 oz/ft² to 2 oz/ft², while Heavy Copper PCBs can have copper weights of 3 oz/ft² or more, with some specialized applications using up to 20 oz/ft².
Heavy Copper PCB Applications
Heavy Copper PCBs find applications in various industries where high current, heat dissipation, and mechanical stability are critical factors:
- Power Electronics
- Inverters
- Motor Drives
- Power Supplies
-
Battery Management Systems
-
Automotive Electronics
- Electric Vehicle (EV) Charging Systems
-
High-Current Automotive Modules
-
Industrial Equipment
- Welding Machines
- High-Power Lighting Systems
-
Induction Heating Systems
-
Aerospace and Defense
- Radar Systems
- High-Power RF Amplifiers
- Satellite Power Systems
Advantages of Heavy Copper PCBs
1. Higher Current Carrying Capacity
The primary advantage of Heavy Copper PCBs is their ability to carry higher currents compared to standard PCBs. The increased copper thickness reduces the resistance of the traces and planes, allowing for more current to flow without causing excessive heating or voltage drops.
The current carrying capacity of a copper trace depends on several factors, such as the trace width, copper thickness, ambient temperature, and the maximum allowed temperature rise. The following table compares the current carrying capacity of different copper weights for a 1 mm wide trace, assuming a 10°C temperature rise:
Copper Weight (oz/ft²) | Trace Thickness (µm) | Current Carrying Capacity (A) |
---|---|---|
1 | 35 | 2.8 |
2 | 70 | 5.6 |
3 | 105 | 8.4 |
4 | 140 | 11.2 |
As seen from the table, doubling the copper weight from 1 oz/ft² to 2 oz/ft² doubles the current carrying capacity, while tripling the copper weight to 3 oz/ft² triples the current carrying capacity.
2. Improved Thermal Management
Another significant advantage of Heavy Copper PCBs is their improved thermal management capabilities. The increased copper thickness provides a larger cross-sectional area for heat conduction, allowing the PCB to dissipate heat more efficiently.
The thermal conductivity of copper (400 W/mK) is significantly higher than that of the PCB substrate material, such as FR-4 (0.3 W/mK). By using thicker copper layers, the PCB can spread the heat generated by components more effectively, reducing hot spots and improving overall thermal performance.
In high-power applications, Heavy Copper PCBs can be combined with thermal management techniques such as heat sinks, thermal vias, and copper coin technology to further enhance heat dissipation.
3. Enhanced Mechanical Strength
Heavy Copper PCBs offer enhanced mechanical strength compared to standard PCBs due to the increased copper thickness. The thicker copper layers provide better support for components and reduce the risk of trace cracking or delamination under mechanical stress.
This is particularly important in applications where the PCB is subjected to vibration, shock, or high-stress mounting conditions, such as in automotive or aerospace systems.
Designing with Heavy Copper PCBs
1. Trace Width and Spacing
When designing with Heavy Copper PCBs, it is essential to consider the trace width and spacing requirements. The increased copper thickness allows for narrower traces and smaller spacing compared to standard PCBs while maintaining the same current carrying capacity.
However, it is essential to ensure that the trace width and spacing meet the manufacturing capabilities of the PCB fabricator. The following table provides general guidelines for minimum trace width and spacing based on copper weight:
Copper Weight (oz/ft²) | Minimum Trace Width (mm) | Minimum Trace Spacing (mm) |
---|---|---|
1 | 0.15 | 0.15 |
2 | 0.20 | 0.20 |
3 | 0.25 | 0.25 |
4 | 0.30 | 0.30 |
It is always recommended to consult with the PCB fabricator to ensure that the design meets their specific manufacturing capabilities and guidelines.
2. Via Design
Via design is another important consideration when working with Heavy Copper PCBs. The increased copper thickness can make it challenging to achieve reliable via connections, especially for high aspect ratio vias.
To ensure reliable via connections, it is essential to consider the following factors:
- Via diameter: Use larger via diameters to accommodate the increased copper thickness and improve manufacturability.
- Via plating: Ensure that the via plating thickness is sufficient to provide reliable connections between layers.
- Via fill: Consider using via fill techniques, such as epoxy or conductive paste, to improve thermal and mechanical performance.
3. Layer Stackup
The layer stackup is a critical aspect of Heavy Copper PCB design. The increased copper thickness can impact the overall PCB thickness and the impedance of the traces.
When designing the layer stackup, consider the following factors:
- Copper balance: Ensure that the copper distribution is balanced across the layers to minimize warpage and improve mechanical stability.
- Dielectric thickness: Adjust the dielectric thickness between layers to achieve the desired impedance and minimize signal integrity issues.
- Symmetry: Use a symmetrical layer stackup to minimize warpage and improve mechanical stability.
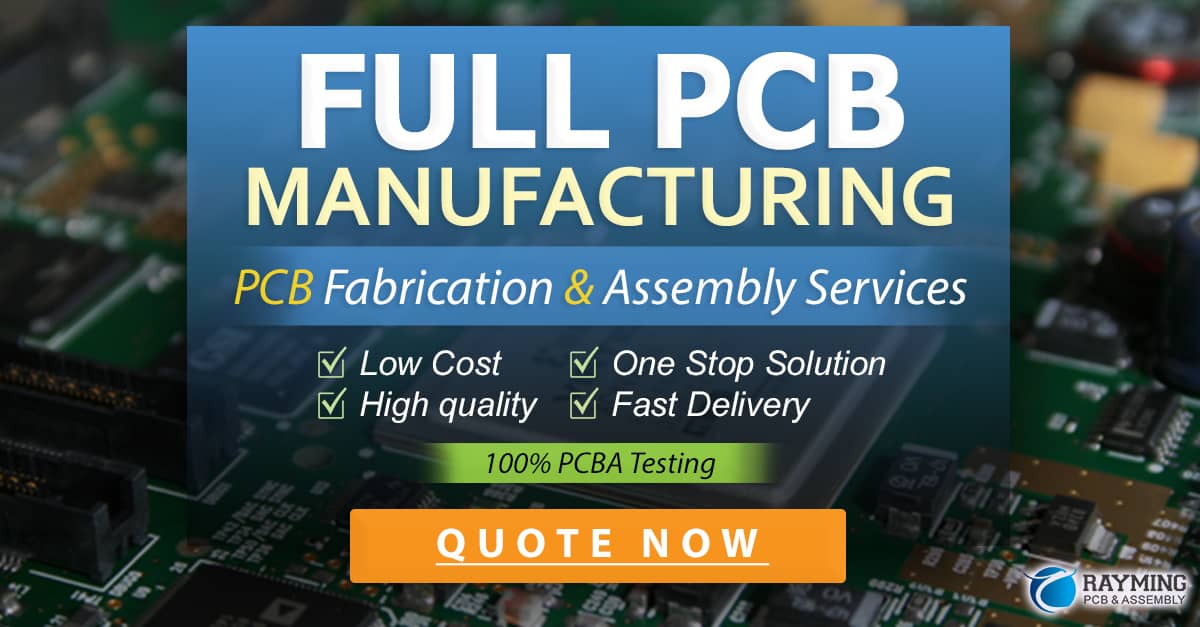
Manufacturing Considerations
1. PCB Fabrication Process
The fabrication process for Heavy Copper PCBs is similar to that of standard PCBs, with a few additional considerations:
- Copper plating: The increased copper thickness requires longer plating times and may require specialized plating equipment.
- Etching: The etching process needs to be optimized to ensure accurate trace formation and minimize undercut.
- Drilling: The increased copper thickness can make drilling more challenging, requiring specialized drill bits and optimized drilling parameters.
2. Cost Implications
Heavy Copper PCBs typically have higher manufacturing costs compared to standard PCBs due to the increased copper usage and specialized fabrication requirements. The cost increase depends on factors such as the copper weight, layer count, and overall PCB complexity.
However, the higher initial cost can be offset by the improved performance, reliability, and long-term savings in applications where high current carrying capacity, thermal management, and mechanical strength are critical.
3. Lead Time
The lead time for Heavy Copper PCBs may be longer compared to standard PCBs due to the specialized fabrication requirements and the need for additional processing steps. It is essential to factor in the lead time when planning projects and to communicate with the PCB fabricator to ensure that the required lead time can be met.
Testing and Quality Control
1. Electrical Testing
Electrical testing is crucial to ensure that Heavy Copper PCBs meet the required performance specifications. Key electrical tests include:
- Continuity Test: Verifies that all connections are intact and there are no open circuits.
- Insulation Resistance Test: Measures the resistance between isolated conductors to ensure adequate insulation.
- High-Voltage Test: Applies a high voltage between conductors to detect any insulation breakdowns or leakage currents.
2. Thermal Testing
Thermal testing is important to validate the thermal performance of Heavy Copper PCBs and ensure that they can operate safely under the expected operating conditions. Thermal tests may include:
- Temperature Rise Test: Measures the temperature rise of the PCB under various load conditions to ensure that it remains within acceptable limits.
- Thermal Cycling Test: Subjects the PCB to repeated temperature cycles to evaluate its ability to withstand thermal stress and identify any potential failures.
3. Microsectioning
Microsectioning is a destructive testing method used to evaluate the internal structure and quality of Heavy Copper PCBs. A cross-section of the PCB is examined under a microscope to assess factors such as:
- Copper thickness uniformity
- Via plating quality
- Lamination integrity
- Conformance to design specifications
Microsectioning is typically performed on a sample basis to ensure that the manufacturing process is consistent and meets the required quality standards.
Future Trends in Heavy Copper PCBs
As power electronics and high-current applications continue to evolve, the demand for Heavy Copper PCBs is expected to grow. Some of the future trends in Heavy Copper PCB technology include:
-
Increased Copper Thickness: The development of new manufacturing processes and materials may enable even thicker copper layers, allowing for higher current carrying capacity and improved thermal management.
-
Advanced Thermal Management Techniques: The integration of advanced thermal management techniques, such as embedded heat pipes or advanced substrates, can further enhance the thermal performance of Heavy Copper PCBs.
-
3D Printing: The adoption of 3D printing technologies for PCB fabrication may enable new design possibilities and faster prototyping of Heavy Copper PCBs.
-
High-Frequency Applications: The development of low-loss, high-frequency substrate materials may enable the use of Heavy Copper PCBs in high-frequency applications, such as 5G communications or radar systems.
Frequently Asked Questions (FAQ)
- What is the difference between Heavy Copper PCBs and standard PCBs?
Heavy Copper PCBs use thicker copper layers compared to standard PCBs, typically 3 oz/ft² or more, while standard PCBs use copper weights ranging from 0.5 oz/ft² to 2 oz/ft². The increased copper thickness allows for higher current carrying capacity, improved thermal management, and enhanced mechanical strength.
- What are the main applications for Heavy Copper PCBs?
Heavy Copper PCBs are commonly used in power electronics, automotive electronics, industrial equipment, aerospace, and defense applications where high current, heat dissipation, and mechanical stability are critical factors.
- Can Heavy Copper PCBs be combined with other thermal management techniques?
Yes, Heavy Copper PCBs can be combined with other thermal management techniques such as heat sinks, thermal vias, and copper coin technology to further enhance heat dissipation in high-power applications.
- Are there any special design considerations when working with Heavy Copper PCBs?
Yes, when designing with Heavy Copper PCBs, it is essential to consider factors such as trace width and spacing, via design, and layer stackup to ensure optimal performance and manufacturability. It is always recommended to consult with the PCB fabricator to ensure that the design meets their specific manufacturing capabilities and guidelines.
- How do the manufacturing costs of Heavy Copper PCBs compare to standard PCBs?
Heavy Copper PCBs typically have higher manufacturing costs compared to standard PCBs due to the increased copper usage and specialized fabrication requirements. However, the higher initial cost can be offset by the improved performance, reliability, and long-term savings in applications where high current carrying capacity, thermal management, and mechanical strength are critical.
0 Comments