Preparing Your Soldering Station
Before you begin soldering, it’s crucial to set up your soldering station properly. A well-organized and equipped soldering station will make the process easier, safer, and more efficient. Here are the essential items you’ll need:
Item | Description |
---|---|
Soldering iron | A temperature-controlled soldering iron with a fine tip (1-2mm) is recommended for thru-hole soldering. |
Soldering iron stand | A stand to safely hold your soldering iron when not in use, preventing accidental burns or damage. |
Solder | Use rosin-core solder with a diameter between 0.5mm and 0.8mm for optimal results. |
Sponge or brass wool | A damp sponge or brass wool is used to clean the soldering iron tip between joints. |
Flux (optional) | Additional flux can help improve solder flow and create cleaner joints, especially for larger components. |
Desoldering tools | Desoldering wick or a solder sucker can be used to remove excess solder or correct mistakes. |
Safety glasses | Protect your eyes from solder splashes and fumes. |
Ventilation | Work in a well-ventilated area or use a fume extractor to minimize exposure to solder fumes. |
Setting the Soldering Iron Temperature
The correct soldering iron temperature is crucial for creating strong, reliable solder joints. The ideal temperature range for most thru-hole soldering applications is between 650°F (343°C) and 750°F (399°C). If the temperature is too low, the solder may not flow properly, resulting in weak joints. If the temperature is too high, you risk damaging the component or the PCB.
Preparing the Component and PCB
Before soldering the thru-hole component, you need to prepare both the component and the PCB. Follow these steps:
-
Identify the component: Ensure that you have the correct component by checking its value, package type, and orientation.
-
Bend the leads: If necessary, gently bend the component leads to fit the PCB hole spacing. Use needle-nose pliers to create a 90-degree bend close to the component body.
-
Clean the PCB: If the PCB is new, it may have a protective coating that needs to be removed. Gently sand the area around the holes with fine-grit sandpaper or a fiberglass pen.
-
Insert the component: Place the component on the PCB, ensuring that the leads pass through the corresponding holes. If the component is polarized (e.g., electrolytic capacitors or diodes), make sure it is oriented correctly.
-
Secure the component: Gently bend the leads outward on the underside of the PCB to hold the component in place during soldering.
Soldering the Component
With your soldering station prepared and the component in place, you’re ready to begin soldering. Follow these steps for each lead:
Step 1: Heat the Joint
-
Place the soldering iron tip on the joint, contacting both the component lead and the PCB pad simultaneously.
-
Keep the soldering iron in place for 1-2 seconds to allow the joint to heat up evenly.
Step 2: Apply Solder
-
While keeping the soldering iron in contact with the joint, touch the solder to the joint (not the soldering iron tip).
-
Feed solder into the joint until it melts and flows around the lead and pad, creating a small mound.
-
Remove the solder wire while keeping the soldering iron in place for an additional 1-2 seconds to ensure proper flow.
Step 3: Remove the Soldering Iron
-
Swiftly remove the soldering iron from the joint, keeping the PCB and component steady.
-
Allow the solder to cool and solidify for a few seconds. Avoid moving the component or PCB during this time.
Step 4: Clean and Inspect the Joint
-
Use a damp sponge or brass wool to clean the soldering iron tip, removing any excess solder.
-
Visually inspect the solder joint for quality. A good solder joint should be shiny, smooth, and concave, with the solder evenly covering the lead and pad.
-
If the joint appears dull, lumpy, or incomplete, you may need to reheat the joint and add more solder.
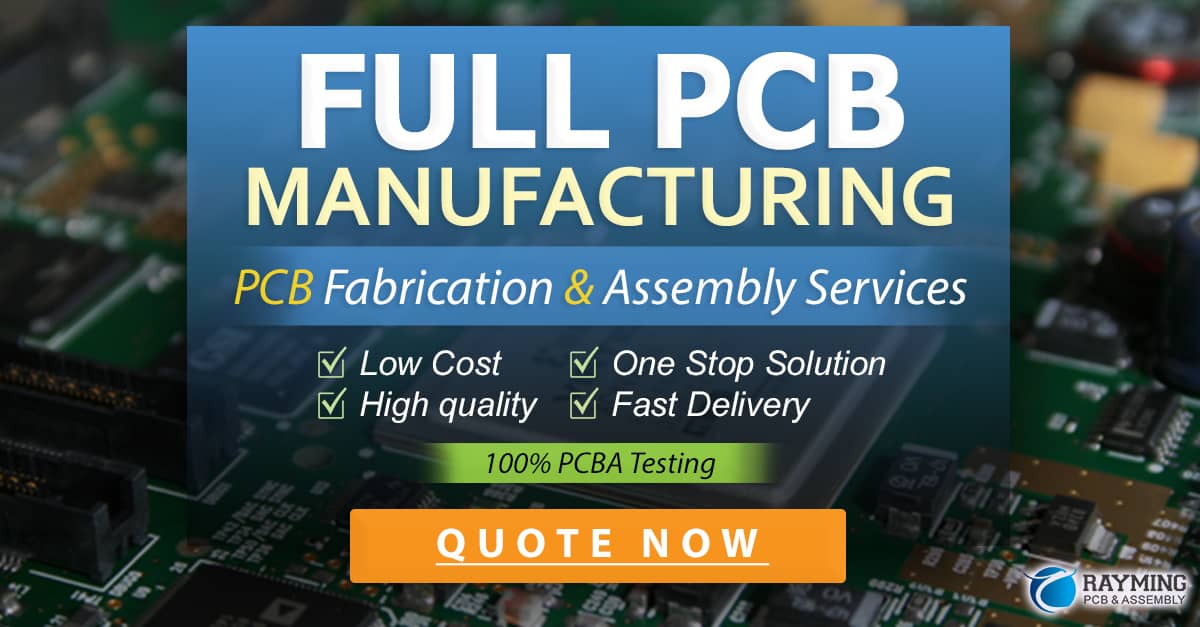
Trimming the Leads
After soldering all the leads, trim the excess lead length using wire cutters. Cut the leads close to the solder joint, leaving approximately 1-2mm of lead protruding from the PCB. Be careful not to apply too much force, as this may damage the solder joint or the PCB.
Cleaning and Inspecting the PCB
Once all the components are soldered and the leads are trimmed, clean the PCB to remove any flux residue. Use isopropyl alcohol and a soft brush or lint-free cloth to gently clean the soldered areas. Inspect the PCB for any missed joints, solder bridges, or other defects. If necessary, use desoldering tools to correct any issues.
Tips for Successful Thru-Hole Soldering
To ensure the best results when Soldering Thru-Hole components, keep these tips in mind:
-
Keep the soldering iron tip clean: Regularly wipe the tip on a damp sponge or brass wool to remove oxidation and excess solder. A clean tip ensures better heat transfer and solder flow.
-
Use the right amount of solder: Apply just enough solder to create a concave joint that fully covers the lead and pad. Avoid applying too much solder, as this can lead to solder bridges or a messy appearance.
-
Work quickly and efficiently: Minimize the time the soldering iron is in contact with the joint to avoid overheating the component or PCB. Develop a steady hand and a consistent soldering technique to work quickly and accurately.
-
Use additional flux when needed: If you’re having trouble getting the solder to flow properly, apply a small amount of flux to the joint before soldering. Flux helps remove oxidation and improves solder wetting.
-
Practice proper safety measures: Always work in a well-ventilated area, wear safety glasses, and avoid touching the hot soldering iron tip or newly soldered joints. Keep flammable materials away from your soldering station.
Frequently Asked Questions (FAQ)
-
What type of solder should I use for thru-hole soldering?
For thru-hole soldering, use rosin-core solder with a diameter between 0.5mm and 0.8mm. Lead-based solder (Sn63/Pb37) is easier to work with but is being phased out due to environmental and health concerns. Lead-free solder (Sn96.5/Ag3.0/Cu0.5) is a common alternative but requires slightly higher soldering temperatures. -
How do I prevent solder bridges between closely spaced leads?
To prevent solder bridges, use a fine-tipped soldering iron and apply just enough solder to create a concave joint. If a solder bridge does form, use desoldering wick or a solder sucker to remove the excess solder. You can also use a small amount of additional flux to help the solder flow away from the bridge. -
Can I reuse desoldered components?
While it is possible to reuse desoldered components, it’s generally not recommended. The desoldering process can stress the component and weaken its leads, making it more prone to failure. Additionally, the component may have been damaged during the initial soldering or desoldering process. It’s best to use new components whenever possible. -
How often should I replace my soldering iron tip?
Soldering iron tips should be replaced when they become worn, pitted, or excessively oxidized. The lifespan of a tip depends on factors such as usage frequency, soldering temperature, and the type of solder used. Tinning the tip regularly with fresh solder can help extend its life. On average, a well-maintained soldering iron tip can last for several months to a year. -
What should I do if I accidentally overheat a component or PCB?
If you accidentally overheat a component or PCB, stop soldering immediately and allow the area to cool down. Assess the damage, looking for signs of discoloration, charring, or melted plastic. If the component or PCB appears damaged, it may need to be replaced. To prevent future incidents, ensure your soldering iron is set to the correct temperature and minimize the time the iron is in contact with the joint.
Conclusion
Soldering thru-hole components is a fundamental skill for anyone working with electronics. By following the general steps outlined in this article and practicing proper technique, you can create strong, reliable solder joints that will ensure the longevity and performance of your projects. Remember to prioritize safety, work efficiently, and keep your soldering station well-maintained. With patience and practice, you’ll be able to confidently tackle any thru-hole soldering task.
0 Comments