Introduction to BGA Assembly
Ball Grid Array (BGA) is a surface-mount packaging technology that uses a grid of solder balls to connect the integrated circuit (IC) package to the printed circuit board (PCB). BGA assembly has become increasingly popular in the electronics industry due to its ability to accommodate high-density interconnects, improved thermal and electrical performance, and reduced package size compared to traditional through-hole and quad flat pack (QFP) packages.
Advantages of BGA Assembly
- High-density interconnects
- Improved thermal and electrical performance
- Reduced package size
- Better signal integrity
- Increased reliability
Challenges in BGA Assembly
Despite its numerous advantages, BGA assembly presents some challenges, including:
- Difficulty in inspecting solder joints
- Requirement for precise placement and reflow processes
- Increased complexity in PCB design and layout
- Higher cost compared to traditional packaging technologies
BGA Package Types
There are several types of BGA packages, each with its own characteristics and applications.
Plastic BGA (PBGA)
PBGA packages use a plastic substrate and are commonly used in consumer electronics, such as smartphones, tablets, and laptops. They offer a cost-effective solution for high-volume production.
Ceramic BGA (CBGA)
CBGA packages use a ceramic substrate and are known for their superior thermal and mechanical properties. They are often used in high-reliability applications, such as aerospace, military, and medical devices.
Tape BGA (TBGA)
TBGA packages use a flexible tape substrate and are designed for applications that require a thin profile and flexibility, such as smartcards and wearable devices.
Comparison of BGA Package Types
Package Type | Substrate Material | Key Characteristics | Typical Applications |
---|---|---|---|
PBGA | Plastic | Cost-effective, high-volume production | Consumer electronics (smartphones, tablets, laptops) |
CBGA | Ceramic | Superior thermal and mechanical properties | High-reliability applications (aerospace, military) |
TBGA | Flexible tape | Thin profile, flexibility | Smartcards, wearable devices |
BGA Assembly Process
The BGA assembly process involves several steps to ensure proper attachment of the BGA package to the PCB.
1. PCB Design and Layout
The first step in BGA assembly is designing and laying out the PCB to accommodate the BGA package. This includes ensuring proper pad size, pitch, and solder mask openings, as well as optimizing signal routing and power distribution.
2. Solder Paste Printing
Solder paste, a mixture of tiny solder particles and flux, is precisely printed onto the PCB pads using a stencil. The stencil ensures that the correct amount of solder paste is deposited on each pad.
3. BGA Package Placement
The BGA package is carefully aligned and placed onto the PCB using a pick-and-place machine. Accurate placement is crucial to ensure proper solder joint formation during the reflow process.
4. Reflow Soldering
The assembled PCB is then subjected to a controlled heating process called reflow soldering. During reflow, the solder paste melts and forms a metallurgical bond between the BGA package and the PCB pads. The reflow profile must be carefully controlled to ensure optimal solder joint formation and to prevent defects such as bridging, voiding, or incomplete wetting.
5. Inspection and Testing
After the reflow process, the assembled PCB undergoes inspection and testing to verify the quality of the solder joints and the overall functionality of the assembly. Common inspection methods include X-ray imaging, automated optical inspection (AOI), and electrical testing.
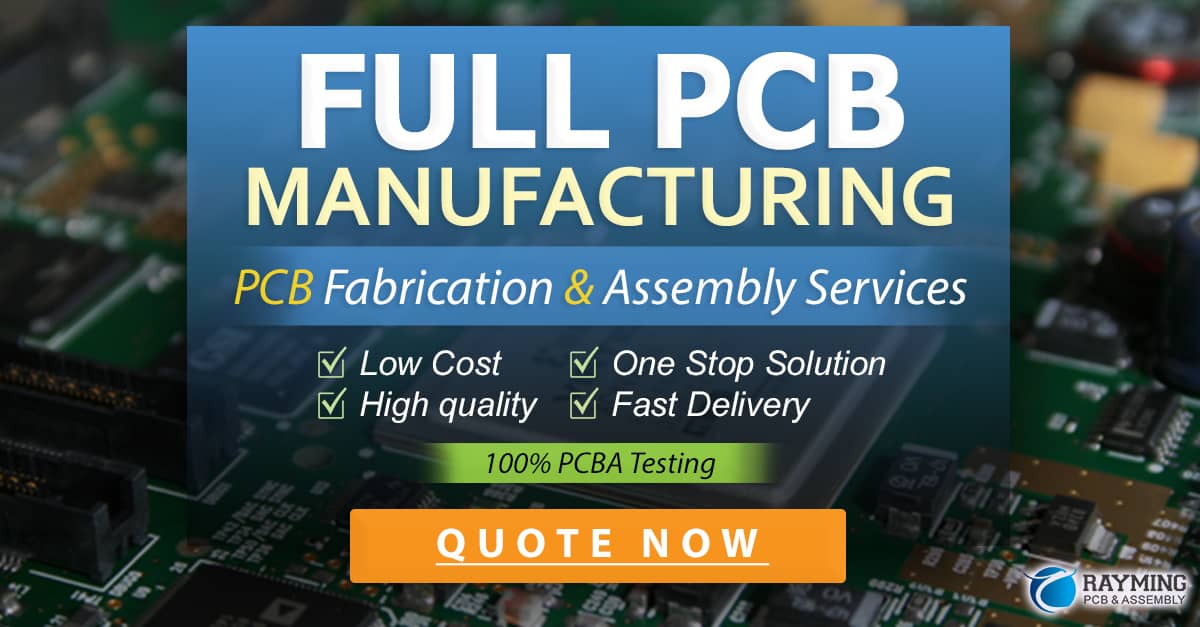
BGA Rework and Repair
Despite careful process control, BGA assembly may sometimes result in defects or failures that require rework or repair.
Common BGA Defects
- Solder bridging: Unintended connection between adjacent solder balls
- Solder Voiding: Trapped gases within the solder joint, reducing its strength and reliability
- Incomplete wetting: Insufficient solder coverage on the PCB pad or BGA ball
- Misalignment: Improper placement of the BGA package on the PCB
BGA Rework Process
BGA rework involves removing the defective BGA package and replacing it with a new one. The process typically includes the following steps:
- Site preparation: Removing the solder residue and cleaning the PCB pads
- BGA package removal: Using a hot air rework station to melt the solder and remove the defective package
- Solder paste application: Printing fresh solder paste onto the PCB pads
- Replacement BGA package placement: Aligning and placing the new BGA package
- Reflow soldering: Reflowing the new BGA package to form solder joints
- Inspection and testing: Verifying the quality of the reworked assembly
BGA Repair Techniques
In some cases, BGA repair may be possible without complete removal and replacement of the package. Some common BGA repair techniques include:
- Solder joint re-balling: Replacing damaged or missing solder balls on the BGA package
- Solder joint re-wetting: Applying flux and heat to improve solder joint quality
- Underfill repair: Removing and replacing the underfill material that provides mechanical support to the BGA package
BGA Assembly Services
Many electronics manufacturers outsource their BGA assembly requirements to specialized service providers. These BGA assembly services offer several advantages, including:
- Access to advanced equipment and expertise
- Cost savings through economies of scale
- Flexibility in production volume and turnaround time
- Improved quality and reliability through proven processes and quality control measures
When selecting a BGA assembly service provider, consider the following factors:
- Experience and expertise in BGA assembly
- Quality certifications and standards compliance
- Range of services offered (design, prototyping, production, testing, etc.)
- Capacity and turnaround time
- Customer support and communication
Future Trends in BGA Assembly
As electronic devices continue to evolve, BGA assembly technology must also advance to meet new challenges and requirements.
Miniaturization and Increased Density
The trend towards miniaturization and increased functionality in electronic devices is driving the need for even smaller BGA packages with higher interconnect densities. This requires advancements in substrate materials, package design, and assembly processes.
Advanced Packaging Technologies
New packaging technologies, such as 2.5D and 3D packaging, are emerging to address the limitations of traditional BGA packages. These technologies enable the integration of multiple ICs in a single package, offering improved performance, reduced power consumption, and smaller form factors.
Automation and Industry 4.0
The increasing adoption of automation and Industry 4.0 technologies in electronics manufacturing is transforming BGA assembly processes. Smart factories equipped with robotics, machine learning, and real-time data analytics can optimize process control, improve quality, and reduce costs.
Conclusion
BGA assembly is a critical technology in the production of high-density, high-performance electronic devices. By understanding the various BGA package types, assembly processes, and rework techniques, electronics manufacturers can ensure the quality and reliability of their products. As the industry continues to evolve, staying up-to-date with the latest trends and advancements in BGA assembly is essential for success in the competitive electronics market.
Frequently Asked Questions (FAQ)
-
What is BGA, and why is it used in electronics assembly?
BGA (Ball Grid Array) is a surface-mount packaging technology that uses a grid of solder balls to connect the IC package to the PCB. It is used in electronics assembly because it allows for high-density interconnects, improved thermal and electrical performance, and reduced package size compared to traditional packaging technologies. -
What are the main types of BGA packages?
The main types of BGA packages are Plastic BGA (PBGA), Ceramic BGA (CBGA), and Tape BGA (TBGA). PBGA is cost-effective and commonly used in consumer electronics, CBGA offers superior thermal and mechanical properties for high-reliability applications, and TBGA is designed for thin profile and flexibility in applications like smartcards and wearable devices. -
What are the key steps in the BGA assembly process?
The key steps in the BGA assembly process are: - PCB design and layout
- Solder paste printing
- BGA package placement
- Reflow soldering
-
Inspection and testing
-
What are some common defects in BGA assembly, and how can they be addressed?
Common defects in BGA assembly include solder bridging, solder voiding, incomplete wetting, and misalignment. These defects can be addressed through BGA rework and repair techniques, such as solder joint re-balling, solder joint re-wetting, and underfill repair. -
What factors should be considered when selecting a BGA assembly service provider?
When selecting a BGA assembly service provider, consider their experience and expertise in BGA assembly, quality certifications and standards compliance, range of services offered, capacity and turnaround time, and customer support and communication. These factors can help ensure a successful partnership and high-quality BGA assembly services.
0 Comments