Introduction to FR4 and Its Upgrades
FR4 (Flame Retardant 4) is a widely used material in the manufacturing of printed circuit boards (PCBs). It is a composite material made of woven fiberglass cloth with an epoxy resin binder. FR4 is known for its excellent mechanical, electrical, and thermal properties, making it an ideal choice for various electronic applications.
Over the years, there have been several upgrades to the standard FR4 material to enhance its performance and meet the evolving needs of the electronics industry. One such upgrade is the Tg150 covered ALLPCB Prototype, which offers improved thermal stability and reliability.
Understanding the Tg150 Upgrade
What is Tg150?
Tg150 refers to the glass transition temperature of the FR4 material, which is the temperature at which the material transitions from a rigid, glassy state to a softer, rubbery state. The standard FR4 material has a Tg of around 130°C, while the upgraded Tg150 material has a higher glass transition temperature of 150°C.
Benefits of Tg150 Upgrade
The Tg150 upgrade offers several benefits over the standard FR4 material:
-
Improved Thermal Stability: With a higher glass transition temperature, Tg150 FR4 can withstand higher operating temperatures without deforming or losing its mechanical properties. This makes it suitable for applications that generate more heat or operate in high-temperature environments.
-
Enhanced Reliability: The increased thermal stability of Tg150 FR4 also contributes to improved reliability of the PCB. It reduces the risk of thermal stress-induced failures, such as delamination or warping, which can occur in standard FR4 materials when subjected to high temperatures.
-
Better High-Frequency Performance: Tg150 FR4 exhibits lower dielectric loss and higher dielectric constant stability at higher frequencies compared to standard FR4. This makes it a preferred choice for high-frequency applications, such as RF and microwave circuits.
-
Compatibility with Lead-Free Soldering: The higher glass transition temperature of Tg150 FR4 makes it compatible with lead-free soldering processes, which typically require higher reflow temperatures. This ensures the material can withstand the soldering process without compromising its integrity.
ALLPCB Prototype with Tg150 FR4
ALLPCB, a leading PCB manufacturer, has introduced a prototype PCB service that utilizes the Tg150 FR4 material. This service combines the benefits of the upgraded FR4 material with ALLPCB’s expertise in PCB fabrication to deliver high-quality prototypes for various applications.
Advantages of ALLPCB Tg150 FR4 Prototype
-
Quick Turnaround: ALLPCB offers fast turnaround times for Tg150 FR4 prototypes, ensuring that designers and engineers can quickly validate their designs and move to the next stage of product development.
-
Cost-Effective: The Tg150 FR4 prototype service from ALLPCB is cost-effective, making it accessible to a wide range of customers, from startups to large enterprises.
-
Customization Options: ALLPCB provides various customization options for Tg150 FR4 prototypes, including different layer counts, board thicknesses, copper weights, and surface finishes. This allows customers to tailor the prototype to their specific requirements.
-
High-Quality Manufacturing: ALLPCB maintains strict quality control measures throughout the manufacturing process to ensure that the Tg150 FR4 prototypes meet the highest standards of quality and reliability.
Applications of Tg150 FR4 Prototype
The Tg150 FR4 prototype from ALLPCB is suitable for a wide range of applications, including:
-
Automotive Electronics: The improved thermal stability of Tg150 FR4 makes it ideal for automotive electronics that are exposed to high temperatures, such as engine control units (ECUs) and power modules.
-
Industrial Controls: Tg150 FR4 prototypes can be used in industrial control systems that operate in harsh environments with elevated temperatures, such as factory automation and process control equipment.
-
High-Power LED Lighting: LED lighting applications generate significant heat, which can be effectively managed by using Tg150 FR4 PCBs. The improved thermal stability ensures reliable operation and longer lifetimes for LED lighting systems.
-
Aerospace and Defense: The enhanced reliability and high-frequency performance of Tg150 FR4 make it suitable for aerospace and defense applications that demand robust and reliable PCBs.
-
Medical Devices: Tg150 FR4 prototypes can be used in medical devices that require high reliability and thermal stability, such as imaging equipment and patient monitoring systems.
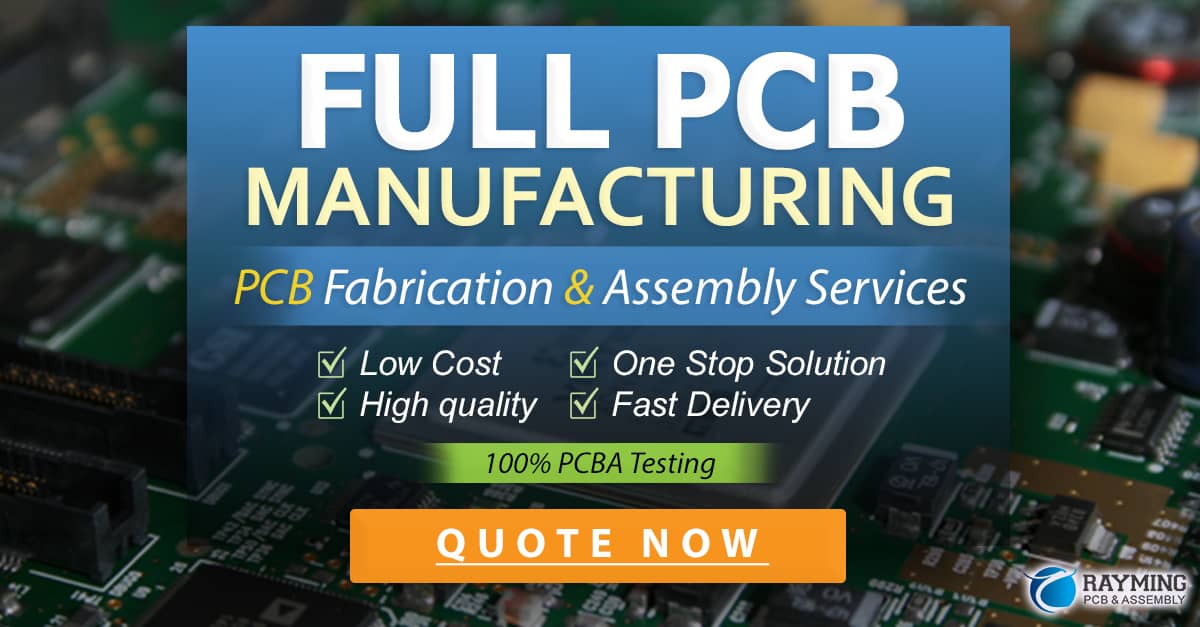
Comparison of Tg150 FR4 with Other Materials
To better understand the advantages of Tg150 FR4, let’s compare it with other commonly used PCB materials:
Material | Glass Transition Temperature (Tg) | Thermal Stability | High-Frequency Performance | Lead-Free Soldering Compatibility |
---|---|---|---|---|
Standard FR4 | 130°C | Good | Good | Limited |
Tg150 FR4 | 150°C | Excellent | Excellent | Compatible |
High Tg FR4 | 170°C | Excellent | Good | Compatible |
Polyimide | 250°C | Excellent | Excellent | Compatible |
As evident from the table, Tg150 FR4 offers a balance of high thermal stability, excellent high-frequency performance, and compatibility with lead-free soldering processes. While High Tg FR4 and Polyimide materials have even higher glass transition temperatures, they may come at a higher cost and may not be necessary for all applications.
Conclusion
The Tg150 FR4 material upgrade represents a significant advancement in PCB technology, offering improved thermal stability, enhanced reliability, and better high-frequency performance compared to standard FR4. ALLPCB’s Tg150 FR4 prototype service combines these benefits with fast turnaround times, cost-effectiveness, and high-quality manufacturing, making it an attractive option for designers and engineers across various industries.
As the electronics industry continues to evolve and demand more robust and reliable PCBs, the Tg150 FR4 material upgrade is poised to play a crucial role in enabling the development of next-generation electronic devices and systems.
Frequently Asked Questions (FAQ)
-
What is the main difference between standard FR4 and Tg150 FR4?
The main difference between standard FR4 and Tg150 FR4 is the glass transition temperature (Tg). Standard FR4 has a Tg of around 130°C, while Tg150 FR4 has a higher Tg of 150°C, offering improved thermal stability and reliability. -
Is Tg150 FR4 suitable for high-frequency applications?
Yes, Tg150 FR4 exhibits lower dielectric loss and higher dielectric constant stability at higher frequencies compared to standard FR4, making it a preferred choice for high-frequency applications such as RF and microwave circuits. -
Can Tg150 FR4 be used with lead-free soldering processes?
Yes, the higher glass transition temperature of Tg150 FR4 makes it compatible with lead-free soldering processes, which typically require higher reflow temperatures. This ensures the material can withstand the soldering process without compromising its integrity. -
What industries can benefit from using Tg150 FR4 prototypes?
Tg150 FR4 prototypes can benefit various industries, including automotive, industrial controls, high-power LED lighting, aerospace and defense, and medical devices. These industries often require PCBs with high thermal stability, reliability, and high-frequency performance. -
How does ALLPCB’s Tg150 FR4 prototype service compare to other PCB manufacturers?
ALLPCB’s Tg150 FR4 prototype service offers fast turnaround times, cost-effectiveness, customization options, and high-quality manufacturing. These features, combined with the benefits of the Tg150 FR4 material upgrade, make ALLPCB a competitive choice for PCB Prototyping services.
0 Comments