Introduction to Flex-Rigid PCBs
Flexible Rigid PCBs, also known as Flex-Rigid PCBs or Rigid-Flex PCBs, are a unique type of printed circuit board that combines the benefits of both flexible and rigid PCBs. These hybrid PCBs consist of multiple layers of flexible and rigid substrates that are laminated together to form a single board. Flex-Rigid PCBs offer numerous advantages over traditional rigid PCBs, including improved reliability, increased design flexibility, and reduced overall size and weight.
Key Benefits of Flex-Rigid PCBs
- Increased Reliability: Flex-Rigid PCBs eliminate the need for connectors and cables between rigid boards, reducing the number of potential failure points and increasing overall reliability.
- Space Savings: By combining flexible and rigid sections, Flex-Rigid PCBs can be folded and shaped to fit into smaller spaces, reducing the overall size of the device.
- Weight Reduction: The use of flexible substrates and the elimination of connectors and cables result in a lighter PCB Assembly.
- Enhanced Design Flexibility: Flex-Rigid PCBs allow for more complex and creative designs, enabling engineers to create products with unique form factors and improved functionality.
Designing Flex-Rigid PCBs for Simplified Assembly
Choose the Right Materials
Selecting the appropriate materials is crucial for ensuring the reliability and performance of your Flex-Rigid PCB assembly. Some common materials used in Flex-Rigid PCBs include:
Material | Description |
---|---|
Polyimide | A flexible, high-temperature resistant polymer used for the flexible layers of the PCB. |
FR-4 | A rigid, glass-reinforced epoxy laminate used for the rigid layers of the PCB. |
Copper | The conductive material used for creating traces and pads on both flexible and rigid layers. |
When choosing materials, consider factors such as the operating temperature range, mechanical stresses, and environmental conditions your Flex-Rigid PCB will be exposed to.
Optimize Layer Stackup
The layer stackup of your Flex-Rigid PCB plays a significant role in its assembly and reliability. Here are some tips for optimizing your layer stackup:
- Minimize the number of layers: Reducing the number of layers in your Flex-Rigid PCB can simplify the assembly process and reduce costs.
- Use symmetrical stackups: Symmetrical layer stackups help prevent warping and twisting of the board during the assembly process.
- Avoid sudden transitions: Gradual transitions between flexible and rigid sections can help reduce stress concentrations and improve reliability.
Design for Manufacturability (DFM)
Designing your Flex-Rigid PCB with manufacturability in mind can greatly simplify the assembly process and improve reliability. Some DFM guidelines include:
- Adhere to minimum feature sizes: Ensure that your design follows the manufacturer’s minimum feature size guidelines for trace widths, spacings, and hole sizes.
- Provide sufficient clearances: Maintain adequate clearances between components, traces, and board edges to prevent short circuits and mechanical interference.
- Use standard component sizes: Whenever possible, use standard component sizes and packages to simplify sourcing and assembly.
Assembling Flex-Rigid PCBs
Choose the Right Assembly Partner
Partnering with an experienced and reputable PCB assembly provider is essential for ensuring the success of your Flex-Rigid PCB project. When selecting an assembly partner, consider the following:
- Experience with Flex-Rigid PCBs: Choose a provider with a proven track record of successfully assembling Flex-Rigid PCBs.
- Advanced equipment and processes: Ensure that your assembly partner has the necessary equipment and processes in place to handle the unique challenges of Flex-Rigid PCB assembly, such as specialized handling and bonding techniques.
- Quality control and testing: Look for a provider with robust quality control measures and comprehensive testing capabilities to ensure the reliability of your assembled Flex-Rigid PCBs.
Optimize the Assembly Process
To streamline the assembly process and improve reliability, consider the following:
- Use surface mount components: Surface mount components are easier to place and solder than through-hole components, reducing the complexity of the assembly process.
- Implement automated assembly: Automated assembly processes, such as pick-and-place machines and reflow soldering, can improve consistency and reduce the risk of human error.
- Conduct thorough testing: Perform comprehensive testing, including functional, environmental, and reliability tests, to identify and address any issues before the final product release.
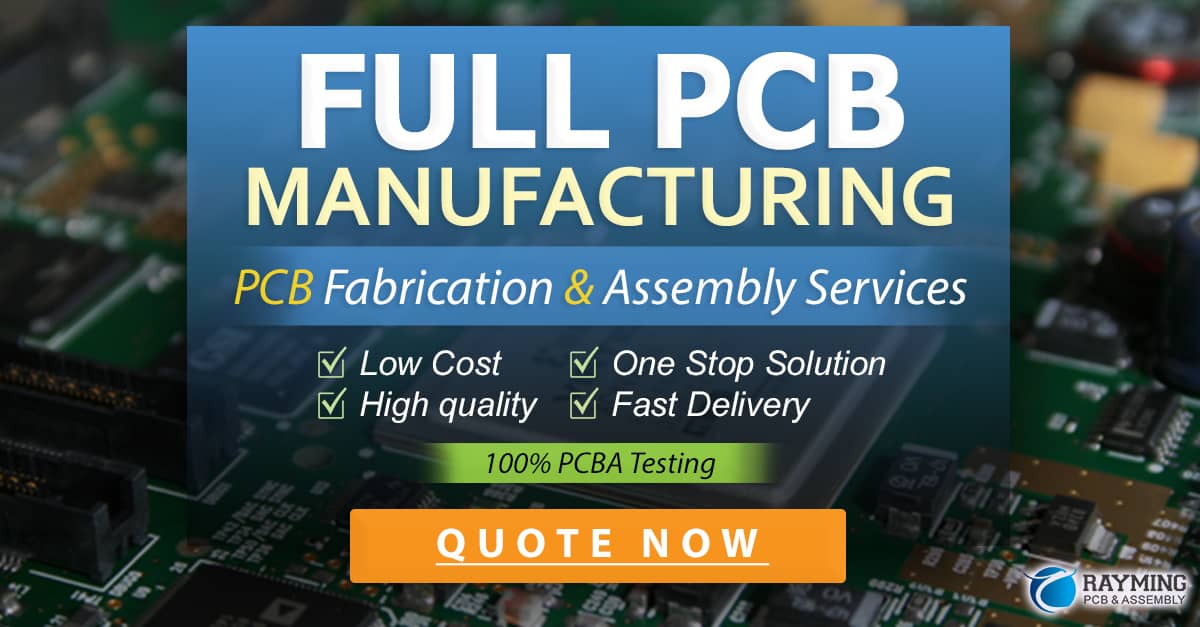
Common Challenges and Solutions
Handling and Flexing
One of the main challenges in assembling Flex-Rigid PCBs is handling the flexible sections without causing damage. To mitigate this risk:
- Use specialized fixtures: Design and use custom fixtures to support and protect the flexible sections during handling and assembly.
- Train personnel: Ensure that your assembly team is properly trained in handling Flex-Rigid PCBs to minimize the risk of damage.
Bonding and Adhesion
Achieving proper bonding and adhesion between the flexible and rigid sections is crucial for the reliability of your Flex-Rigid PCB. To improve bonding and adhesion:
- Use appropriate adhesives: Select adhesives that are compatible with the materials used in your Flex-Rigid PCB and can withstand the expected environmental conditions.
- Control the bonding process: Ensure that the bonding process is well-controlled, with proper temperature, pressure, and curing time to achieve optimal adhesion.
Strain Relief
Providing adequate strain relief is essential for preventing damage to the flexible sections of your Flex-Rigid PCB. Some strain relief techniques include:
- Using stiffeners: Attach stiffeners to the flexible sections to reduce the risk of damage from excessive bending or flexing.
- Incorporating strain relief features: Design your Flex-Rigid PCB with strain relief features, such as curves or loops, to distribute stress and prevent concentrated strain.
FAQ
-
What is a Flex-Rigid PCB?
A Flex-Rigid PCB is a hybrid printed circuit board that combines flexible and rigid substrates to create a single, integrated board. This allows for increased design flexibility, improved reliability, and reduced size and weight compared to traditional rigid PCBs. -
What are the benefits of using Flex-Rigid PCBs?
Flex-Rigid PCBs offer several benefits, including increased reliability, space savings, weight reduction, and enhanced design flexibility. By eliminating connectors and cables between rigid boards, Flex-Rigid PCBs reduce the number of potential failure points and allow for more compact and lightweight designs. -
How can I ensure the reliability of my Flex-Rigid PCB assembly?
To ensure the reliability of your Flex-Rigid PCB assembly, choose the right materials, optimize your layer stackup, and design for manufacturability. Partner with an experienced assembly provider, use surface mount components, implement automated assembly processes, and conduct thorough testing to identify and address any issues. -
What are some common challenges in assembling Flex-Rigid PCBs?
Common challenges in assembling Flex-Rigid PCBs include handling and flexing the flexible sections without causing damage, achieving proper bonding and adhesion between the flexible and rigid sections, and providing adequate strain relief to prevent damage from excessive bending or flexing. -
How can I select the right assembly partner for my Flex-Rigid PCB project?
When selecting an assembly partner for your Flex-Rigid PCB project, look for a provider with experience in assembling Flex-Rigid PCBs, advanced equipment and processes to handle the unique challenges of Flex-Rigid PCB assembly, and robust quality control measures and testing capabilities to ensure the reliability of your assembled boards.
Conclusion
Flex-Rigid PCBs offer numerous advantages over traditional rigid PCBs, including increased reliability, space savings, weight reduction, and enhanced design flexibility. By following best practices in design, material selection, and assembly, you can simplify the assembly process and improve the reliability of your Flex-Rigid PCB.
Partnering with an experienced and reputable assembly provider is crucial for the success of your Flex-Rigid PCB project. By optimizing your design for manufacturability, implementing automated assembly processes, and conducting thorough testing, you can ensure that your Flex-Rigid PCB assembly meets the highest standards of quality and reliability.
As technology continues to advance and the demand for more compact, lightweight, and flexible electronic devices grows, Flex-Rigid PCBs will play an increasingly important role in the electronics industry. By staying up-to-date with the latest developments and best practices in Flex-Rigid PCB design and assembly, you can position yourself at the forefront of this exciting and dynamic field.
0 Comments