What is a Flexible PCB?
A flexible PCB, also known as a flex circuit, is a type of printed circuit board that is made from flexible materials such as polyimide or polyester. These materials allow the PCB to bend and flex without breaking or losing its electrical connectivity. Flexible PCBs consist of a thin layer of conductive material, typically copper, that is laminated between two layers of flexible insulating material.
Advantages of Flexible PCBs
Flexible PCBs offer several advantages over traditional rigid PCBs, including:
-
Flexibility: The most obvious advantage of flexible PCBs is their ability to bend and flex. This allows them to be used in applications where traditional rigid PCBs would not be suitable, such as wearable devices, medical implants, and aerospace equipment.
-
Durability: Flexible PCBs are more durable than rigid PCBs because they can withstand repeated bending and flexing without breaking or cracking. This makes them ideal for applications where the PCB may be subjected to physical stress or vibration.
-
Space-saving: Flexible PCBs can be designed to fit into tight spaces and conform to complex shapes, allowing for more compact and lightweight devices.
-
Cost-effective: Flexible PCBs can be more cost-effective than rigid PCBs in certain applications because they require fewer connectors and can be manufactured in a single piece, reducing assembly costs.
Key Characteristics of Flexible PCBs
Flexibility
The most important characteristic of flexible PCBs is their ability to bend and flex without breaking or losing electrical connectivity. This flexibility is achieved through the use of flexible materials such as polyimide or polyester, which can withstand repeated bending and flexing.
The flexibility of a flexible PCB is measured by its bend radius, which is the minimum radius that the PCB can be bent without damaging the conductive traces or insulating layers. The bend radius depends on several factors, including the thickness of the PCB, the type of material used, and the design of the conductive traces.
Thickness (mm) | Single-sided Bend Radius (mm) | Double-sided Bend Radius (mm) |
---|---|---|
0.05 | 0.8 | 1.6 |
0.1 | 1.6 | 3.2 |
0.2 | 3.2 | 6.4 |
0.3 | 4.8 | 9.6 |
Durability
Flexible PCBs are more durable than rigid PCBs because they can withstand repeated bending and flexing without breaking or cracking. This durability is achieved through the use of high-quality materials and advanced manufacturing techniques.
The durability of a flexible PCB is measured by its flex life, which is the number of times the PCB can be bent before it fails. The flex life depends on several factors, including the type of material used, the thickness of the PCB, and the bend radius.
Material | Thickness (mm) | Bend Radius (mm) | Flex Life (cycles) |
---|---|---|---|
Polyimide | 0.05 | 1.6 | >1,000,000 |
Polyimide | 0.1 | 3.2 | >500,000 |
Polyester | 0.05 | 1.6 | >100,000 |
Polyester | 0.1 | 3.2 | >50,000 |
High-Density Interconnect
Flexible PCBs can be designed with high-density interconnects (HDI), which allow for more complex circuits to be created in a smaller space. HDI flexible PCBs use microvias, which are small holes that connect the conductive layers of the PCB, to achieve higher circuit densities.
HDI flexible PCBs offer several advantages over traditional flexible PCBs, including:
-
Increased circuit density: HDI flexible PCBs can accommodate more components and circuits in a smaller space, enabling more compact and lightweight devices.
-
Improved signal integrity: HDI flexible PCBs use shorter signal paths and smaller vias, which reduces signal loss and improves signal integrity.
-
Reduced power consumption: HDI flexible PCBs can be designed with thinner conductive layers, which reduces the overall resistance of the circuit and leads to lower power consumption.
Thermal Management
Flexible PCBs can be designed with thermal management features to dissipate heat generated by electronic components. This is particularly important in applications where the PCB is subjected to high temperatures or where the components generate a significant amount of heat.
Thermal management in flexible PCBs can be achieved through several methods, including:
-
Thermal vias: Thermal vias are holes drilled through the PCB that are filled with a thermally conductive material, such as copper or aluminum. These vias help to transfer heat away from the components and into the surrounding air or a heat sink.
-
Thermal interface materials (TIMs): TIMs are materials that are placed between the components and the PCB to improve heat transfer. Common TIMs include thermal greases, thermal pads, and phase change materials.
-
Heatsinks: Heatsinks are metal structures that are attached to the PCB or the components to dissipate heat. Heatsinks can be designed in various shapes and sizes to optimize heat transfer and improve cooling performance.
Shielding
Flexible PCBs can be designed with shielding features to protect the circuits from electromagnetic interference (EMI) and radio frequency interference (RFI). Shielding is particularly important in applications where the PCB is exposed to high levels of interference, such as in medical devices or aerospace equipment.
Shielding in flexible PCBs can be achieved through several methods, including:
-
Conductive coatings: Conductive coatings, such as copper or silver, can be applied to the surface of the PCB to create a shield against EMI and RFI.
-
Conductive adhesives: Conductive adhesives can be used to attach shielding materials, such as metal foils or conductive fabrics, to the PCB.
-
Shielded cables: Shielded cables can be used to connect the PCB to other components or devices while providing protection against EMI and RFI.
Environmental Resistance
Flexible PCBs can be designed to withstand harsh environmental conditions, such as extreme temperatures, humidity, and chemical exposure. This is particularly important in applications where the PCB may be exposed to outdoor or industrial environments.
Environmental resistance in flexible PCBs can be achieved through the use of specialized materials and coatings, such as:
-
High-temperature materials: Materials such as polyimide and liquid crystal polymer (LCP) can withstand temperatures up to 300°C, making them suitable for high-temperature applications.
-
Moisture-resistant coatings: Conformal coatings, such as parylene or acrylic, can be applied to the PCB to protect it from moisture and humidity.
-
Chemical-resistant materials: Materials such as polytetrafluoroethylene (PTFE) and ethylene tetrafluoroethylene (ETFE) are resistant to a wide range of chemicals, making them suitable for applications where the PCB may be exposed to harsh chemicals.
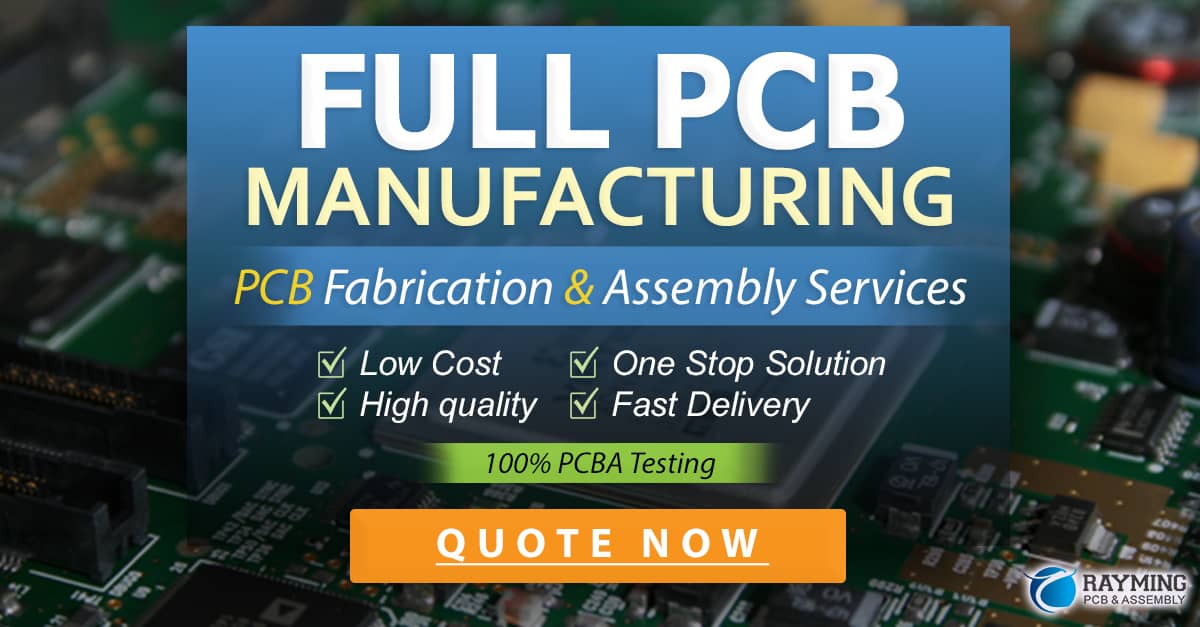
Applications of Flexible PCBs
Flexible PCBs are used in a wide range of applications across various industries, including:
-
Medical devices: Flexible PCBs are used in medical implants, such as pacemakers and hearing aids, where flexibility and durability are critical.
-
Wearable technology: Flexible PCBs are used in wearable devices, such as smartwatches and fitness trackers, where flexibility and compact design are essential.
-
Automotive electronics: Flexible PCBs are used in automotive applications, such as instrument clusters and infotainment systems, where space is limited and reliability is crucial.
-
Aerospace and defense: Flexible PCBs are used in aerospace and defense applications, such as satellites and military equipment, where environmental resistance and reliability are paramount.
-
Consumer electronics: Flexible PCBs are used in consumer electronics, such as smartphones and tablets, where compact design and high-density interconnects are necessary.
FAQ
-
Q: What is the difference between a flexible PCB and a rigid PCB?
A: A flexible PCB is made from flexible materials, such as polyimide or polyester, which allow it to bend and flex without breaking or losing electrical connectivity. A rigid PCB, on the other hand, is made from a rigid material, such as FR-4, and cannot bend or flex. -
Q: What are the advantages of using a flexible PCB?
A: Flexible PCBs offer several advantages, including flexibility, durability, space-saving, and cost-effectiveness. They can be used in applications where traditional rigid PCBs would not be suitable, such as wearable devices and medical implants. -
Q: How is the flexibility of a flexible PCB measured?
A: The flexibility of a flexible PCB is measured by its bend radius, which is the minimum radius that the PCB can be bent without damaging the conductive traces or insulating layers. The bend radius depends on several factors, including the thickness of the PCB, the type of material used, and the design of the conductive traces. -
Q: What is the difference between a single-sided and a double-sided flexible PCB?
A: A single-sided flexible PCB has conductive traces on only one side of the insulating layer, while a double-sided flexible PCB has conductive traces on both sides of the insulating layer. Double-sided flexible PCBs offer higher circuit density and improved signal integrity compared to single-sided flexible PCBs. -
Q: What are some common applications of flexible PCBs?
A: Flexible PCBs are used in a wide range of applications, including medical devices, wearable technology, automotive electronics, aerospace and defense, and consumer electronics. They are particularly useful in applications where flexibility, durability, and compact design are essential.
In conclusion, flexible PCBs have become increasingly popular due to their unique characteristics, such as flexibility, durability, high-density interconnects, thermal management, shielding, and environmental resistance. These characteristics enable flexible PCBs to be used in a wide range of applications across various industries, from medical devices to consumer electronics. As technology continues to advance and the demand for smaller, more compact, and more reliable electronic devices grows, the use of flexible PCBs is expected to increase even further in the coming years.
0 Comments