Introduction
Flexible printed circuit boards (flex PCBs) are a vital component in modern electronics, enabling convenient and reliable connections between components in compact devices. As products continue getting smaller and more powerful, flex PCBs become increasingly critical by allowing circuitry to bend and flex with devices.
When designing a new product that will utilize a flex PCB, prototyping early is crucial to work out any issues and optimize the board’s performance. This article provides a comprehensive overview of best practices for designing and prototyping flexible PCBs.
Benefits of Flexible PCBs
Flexible PCBs provide unique advantages over their rigid counterparts:
- Flexibility – Can bend, fold and flex repeatedly to accommodate movement and small spaces.
- Lightweight – Weigh less than rigid boards.
- Thinness – Extremely thin profile, as little as 1 mil (0.001 inches).
- Durability – Withstand vibration, shock, and flexing.
- Reliability – Proven technology when designed properly.
Flex PCBs enable electronics that are impractical or impossible with rigid PCBs. This flexibility allows industrial designers to put circuitry in places unimaginable just a decade ago.
Flex PCB Materials
The base material of flex PCBs is a flexible plastic film made of polyimide or other polymers. The most common is Dupont’s Kapton polyimide film. The copper traces are bonded to the film with a flexible adhesive.
Here are the most common flex PCB material stacks:
Layer | Material | Description |
---|---|---|
Base | Polyimide film | Flexible plastic substrate, typically 12.5-250 μm thick |
Adhesive | Acrylic, epoxy, or urethane | Bonds copper to polyimide. Can be 8-25 μm thick |
Copper | Rolled annealed copper foil | Conductive traces, typically 12-35 μm thick |
Coverlay | Liquid photoimageable solder mask | Protective coating over traces |
Multi-layer flex PCBs sandwich additional circuit layers using adhesive dielectric films. Rigid sections can be integrated using stiffeners.
Design Considerations
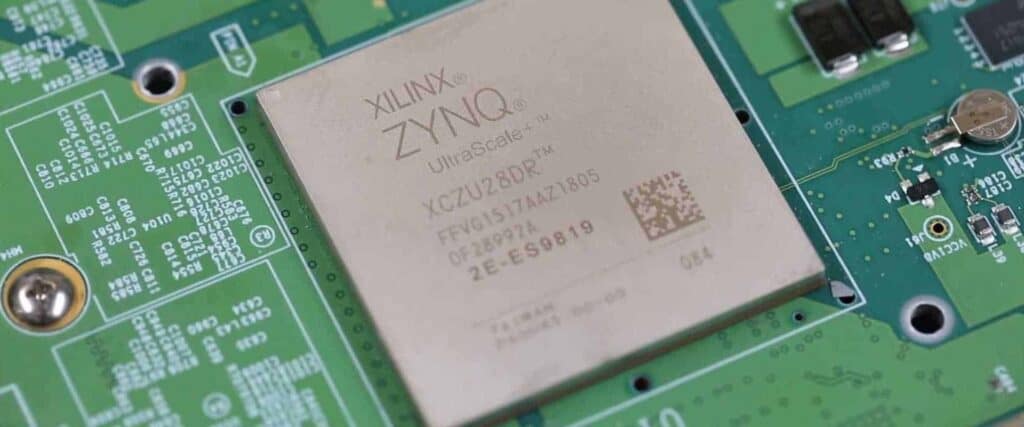
Designing a flex PCB requires special considerations for the flexible substrate. Here are some best practices:
- Avoid sharp corners or angles – Use curved traces instead to prevent cracking. Minimum bend radius is typically 3-10x trace width.
- Distribute traces evenly – Balance trace densities across layers to prevent distortion.
- Minimize components – Limit parts only to where needed. Use rigid sections for more components.
- Strategic stiffeners – Add rigid sections to stabilize connectors or components.
- Plan for motion – Design traces and spacing for repeated flexing motions.
Work closely with your flex PCB manufacturer during design to apply their capabilities and experience. Their input is invaluable for optimizing manufacturability.
Prototyping Flex PCBs
Prototyping is a critical phase of product development to test form, fit, and function. Here are proven methods for prototyping flex PCB designs:
CAD Models
Creating 3D CAD models allows visualization of the flex board integrated in the product assembly. This helps identify potential fit issues early before committing to an actual prototype.
Adhesive Mockups
Mockups using Kapton tape on a temporary substrate simulate the shape and bend radius of the planned flex board. This technique enables quick physical validation of the planned flexibility.
Rapid Prototyped Circuits
Special flex circuit materials printable on desktop inkjet printers enable rapid prototyping of circuits. This allows early circuit testing before finalizing the design.
Virtual Simulation
Software tools simulate how the flex board will bend and flex when integrated in the product. This reveals potential fracture points in the design before building prototypes.
Limited Production Prototypes
Having prototypes produced using the same flex materials and process as final production provides the most comprehensive test. Your manufacturer can produce a small batch of prototypes before full production.
Tips for Effective Flex PCB Prototypes
Follow these tips for getting the most value from your flex PCB prototypes:
- Test form, fit, and function in representative enclosures
- Validate bend radius and flexibility for motions in use
- Include stress relief features like curved traces
- Check clearances for dynamic sections
- Thermally stress test at temperature extremes
- Confirm component placement and orientation
- Verify assembly methods and footprints
- Test vias and connections between layers
- Qualify adhesives planned for use
- Assess production processes like depaneling
- Apply environmental testing per specifications
Thoroughly evaluating prototypes reduces the risk of setbacks or delays after design files are finalized. Testing flex PCBs in their operating state reveals insights impossible to garner from just 2D drawings.
Producing Flex PCBs
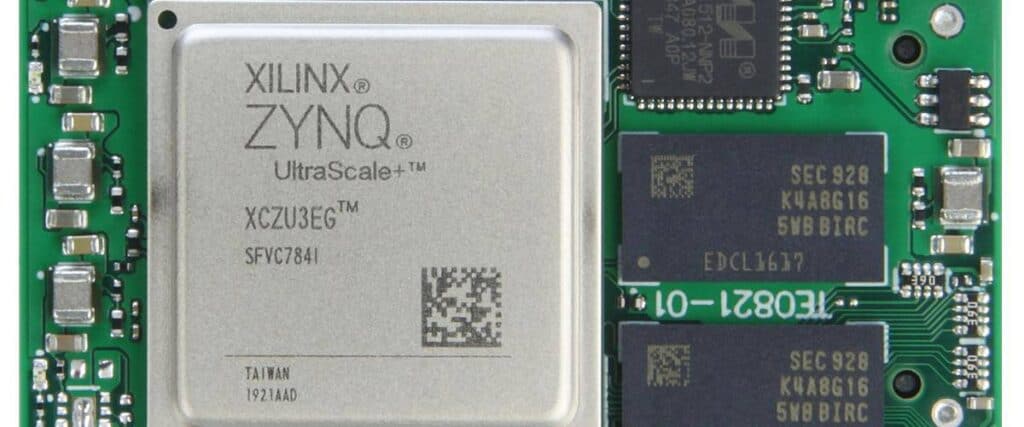
Once the design and prototypes are finalized, volume production can begin. Flex PCB production technology has improved tremendously in recent years, enabling very high yields and advanced features.
Here is an overview of the flex PCB production process:
- CAM – Computer aided manufacturing programs prepared based on PCB design files.
- Printing – Photoresist masks are printed on the copper-clad base material.
- Etching – Chemical etching removes unwanted copper, leaving the desired traces.
- Layer Alignment – Additional layers are precisely aligned using laser drilled fiducials.
- Lamination – Layers are bonded using heat and pressure.
- Component Assembly – Parts are attached on the surface using soldering or conductive adhesives.
- Testing – 100% electrical testing validates performance. Automated optical inspection checks quality.
- Singulation – Individual boards are cut or routed from the panel.
- Quality Assurance – Sampling inspection ensures reliability criteria are met.
Reputable flex PCB manufacturers will have expertise across this entire process to produce quality boards affordably. Work closely with them through the product development cycle for best results.
Potential Issues When Designing Flex PCBs
While flex PCBs provide many advantages, the technology also comes with some potential pitfalls to be aware of:
- Fractures from dynamic bending stress
- Cracks in solder mask or base material
- Lost flexibility from excessive stiffeners or components
- Creep corrosion under bending stress
- Overheating components without heat sinking
- Circuit damage from static electricity
Careful design, testing, and working with experienced flex PCB manufacturers helps avoid these issues. Take precautions to protect flex boards from damage during handling and assembly as well.
Frequently Asked Questions
Q: What are the main advantages of flexible PCBs?
A: The main advantages are flexibility to fit and move within tight spaces, thin and lightweight profiles, improved durability and reliability compared to wires, and ability to produce complex reliable circuits in very small packages.
Q: What are some common applications for flex PCBs?
A: Some common applications are wearable devices, medical devices, robotics, foldable/rollable displays, automotive electronics, aerospace avionics, and consumer electronics where space is extremely constrained.
Q: How durable are flex PCBs?
A: Properly designed flex PCBs can withstand millions of dynamic bending cycles, shock, vibration, and temperature cycling. Polyimide film and flexible adhesives provide good flex durability.
Q: Can components be mounted directly on flex PCBs?
A: Yes, components can be assembled on flex PCBs, but this should be minimized. Small SMT parts are ideal. Rigid sections with stiffeners help support more components.
Q: What are considerations for designing rigid-flex PCBs?
A: For rigid-flex designs, plan space for components on rigid sections, locate connectors at rigid sections, minimize components on dynamic areas, and ensure smooth reliable transitions between rigid and flex areas.
0 Comments