Introduction to Flexible PCBs
Flexible printed circuit boards (PCBs) are a versatile and increasingly popular choice for many electronic applications. Unlike traditional rigid PCBs, flexible PCBs can bend, twist, and conform to various shapes, enabling them to fit into tight spaces and withstand repeated flexing. This makes them ideal for applications such as wearable devices, medical equipment, automotive electronics, and aerospace systems.
Flexible PCBs are constructed using a combination of thin, flexible substrates, conductive traces, and protective coverlay materials. The choice of materials and the specific construction techniques used can greatly impact the performance, reliability, and cost of the final product.
In this article, we will explore the various materials used in flexible PCB construction, the different types of flexible PCBs, and the key considerations for designing and manufacturing these versatile circuits.
Flexible PCB Substrates
Polyimide (PI)
Polyimide (PI) is the most common substrate material used in flexible PCBs. It is known for its excellent thermal stability, chemical resistance, and mechanical strength. PI can withstand temperatures up to 300°C and maintains its flexibility over a wide temperature range. There are several types of PI films used in flexible PCBs, including:
-
Kapton: Developed by DuPont, Kapton is the most widely used PI film in the industry. It offers high tensile strength, dimensional stability, and dielectric properties.
-
Upilex: Manufactured by UBE Industries, Upilex has similar properties to Kapton but offers better tear resistance and lower moisture absorption.
-
Apical: Produced by Kaneka Corporation, Apical is known for its high heat resistance and low coefficient of thermal expansion (CTE).
Polyethylene Terephthalate (PET)
Polyethylene terephthalate (PET) is another popular substrate material for flexible PCBs. It is less expensive than PI and offers good electrical properties, making it suitable for low-cost, high-volume applications. However, PET has lower thermal stability compared to PI, with a maximum operating temperature of around 105°C.
Flexible Copper Clad Laminate (FCCL)
Flexible copper clad laminate (FCCL) is a composite material consisting of a thin layer of copper foil bonded to a flexible substrate, such as PI or PET. FCCL is the starting material for most flexible PCBs and comes in various thicknesses and copper weights to suit different applications.
Substrate | Max. Operating Temp. (°C) | Key Properties |
---|---|---|
Polyimide | 300 | High thermal stability, chemical resistance, and mechanical strength |
PET | 105 | Lower cost, good electrical properties |
Conductive Materials
Copper
Copper is the most common conductive material used in flexible PCBs due to its excellent electrical conductivity, thermal conductivity, and mechanical properties. Copper foils used in flexible PCBs are typically thinner than those used in rigid PCBs to maintain flexibility. Common copper foil thicknesses range from 9 μm to 70 μm (0.5 oz to 2 oz).
Silver Ink
Silver ink is a conductive material that can be screen printed or inkjet printed onto flexible substrates. It offers lower cost and faster production compared to copper etching but has lower conductivity and current-carrying capacity. Silver ink is often used for low-power applications, such as RFID antennas and membrane switches.
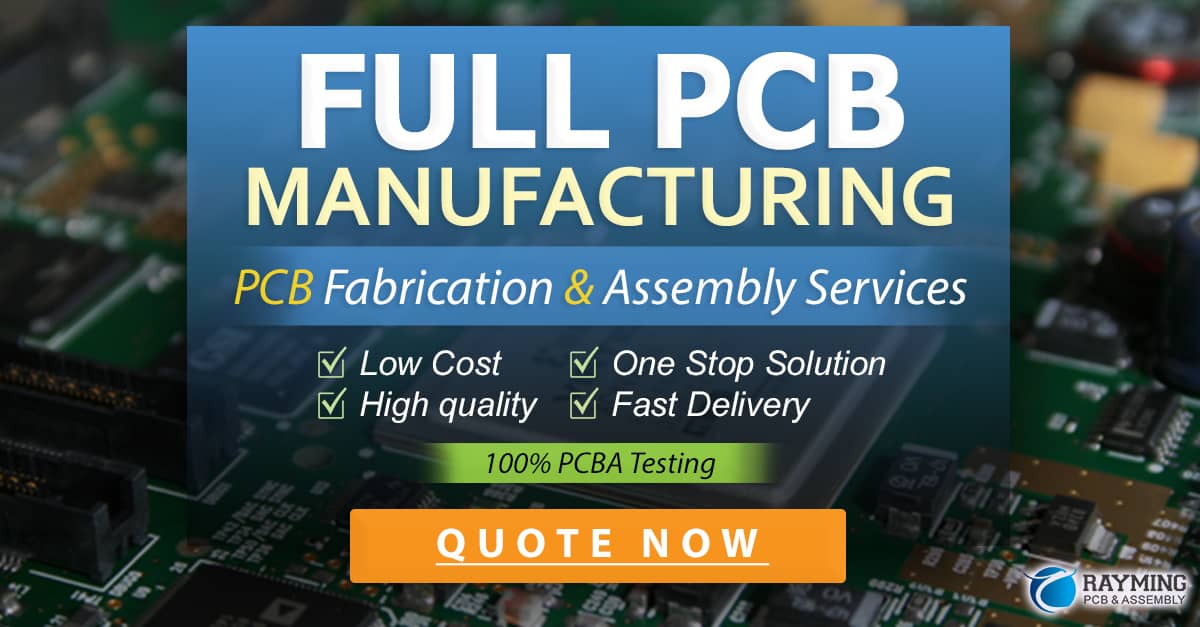
Coverlay Materials
Coverlay is a protective layer applied over the exposed copper traces on a flexible PCB to provide insulation and mechanical protection. Common coverlay materials include:
-
Polyimide (PI): PI coverlay offers excellent thermal stability, chemical resistance, and durability. It is often used in high-reliability applications.
-
Polyethylene terephthalate (PET): PET coverlay is less expensive than PI and provides good electrical insulation and mechanical protection for low-cost applications.
-
Flexible solder mask: Flexible solder mask is a photoimageable coating that can be selectively applied to protect exposed copper traces while leaving pads and other features exposed for soldering.
Types of Flexible PCBs
Single-sided Flexible PCBs
Single-sided flexible PCBs have conductive traces on only one side of the substrate. They are the simplest and most cost-effective type of flexible PCB but have limited routing density and electrical performance.
Double-sided Flexible PCBs
Double-sided flexible PCBs have conductive traces on both sides of the substrate, allowing for higher routing density and better electrical performance compared to single-sided designs. The two sides are connected using plated through-holes (PTHs).
Multi-layer Flexible PCBs
Multi-layer flexible PCBs consist of three or more conductive layers separated by insulating layers. They offer the highest routing density and electrical performance but are also the most complex and expensive to manufacture. Multi-layer flexible PCBs are often used in high-density, high-speed applications.
Rigid-Flex PCBs
Rigid-flex PCBs combine rigid and flexible sections in a single circuit board. The rigid sections provide mechanical support and can accommodate larger components, while the flexible sections allow the board to bend and fit into tight spaces. Rigid-flex PCBs offer the benefits of both rigid and flexible PCBs but require careful design and manufacturing to ensure reliability.
Type | Layers | Routing Density | Cost |
---|---|---|---|
Single-sided | 1 | Low | Low |
Double-sided | 2 | Medium | Medium |
Multi-layer | 3+ | High | High |
Rigid-Flex | Varies | High | High |
Flexible PCB Manufacturing Process
The manufacturing process for flexible PCBs is similar to that of rigid PCBs but requires additional steps and specialized equipment to handle the flexible materials. The general steps involved in flexible PCB manufacturing include:
-
Material preparation: The flexible substrate, copper foil, and coverlay materials are cut to size and cleaned.
-
Lamination: The copper foil is laminated onto the flexible substrate using heat and pressure.
-
Patterning: The desired circuit pattern is transferred onto the copper layer using photolithography or laser direct imaging (LDI).
-
Etching: The unwanted copper is removed using a chemical etching process, leaving only the desired conductive traces.
-
via formation: Through-holes and vias are drilled or laser-cut into the substrate and plated with copper to connect the layers (for double-sided and multi-layer designs).
-
Coverlay application: The coverlay material is laminated onto the circuit to provide insulation and protection.
-
Surface finish: A surface finish, such as ENIG (Electroless Nickel Immersion Gold) or OSP (Organic Solderability Preservative), is applied to the exposed pads to improve solderability and protect the copper from oxidation.
-
Cutting and packaging: The finished flexible PCBs are cut to their final shape and packaged for shipping.
Design Considerations for Flexible PCBs
Designing flexible PCBs requires careful consideration of several factors to ensure reliable performance and manufacturability. Some key design considerations include:
-
Bend radius: The minimum bend radius of the flexible PCB must be specified to avoid damaging the copper traces and substrate during flexing.
-
Strain relief: Proper strain relief techniques, such as using stiffeners or incorporating tear-stops, should be employed to prevent excessive stress on the flexible circuit.
-
Adhesion: The adhesion between the copper traces, substrate, and coverlay must be sufficient to withstand the expected mechanical and environmental stresses.
-
Trace width and spacing: The width and spacing of the copper traces should be optimized to maintain flexibility while providing adequate current-carrying capacity and signal integrity.
-
via design: vias in flexible PCBs should be designed with larger land pads and smaller drill holes to minimize stress concentration and improve reliability.
-
Component selection: Components used on flexible PCBs should be chosen based on their ability to withstand the expected mechanical and environmental stresses.
-
Testing and validation: Comprehensive testing and validation, including mechanical stress testing and environmental testing, should be performed to ensure the reliability of the flexible PCB in its intended application.
Applications of Flexible PCBs
Flexible PCBs are used in a wide range of applications across various industries. Some common applications include:
-
Wearable devices: Flexible PCBs are essential for creating compact, lightweight, and comfortable wearable devices, such as smartwatches, fitness trackers, and medical monitoring devices.
-
Medical equipment: Flexible PCBs are used in medical devices that require conformity to the human body, such as hearing aids, pacemakers, and diagnostic imaging equipment.
-
Automotive electronics: Flexible PCBs are used in automotive applications that require compact packaging and resistance to vibration and temperature extremes, such as dashboard displays, sensor modules, and lighting systems.
-
Aerospace and defense: Flexible PCBs are used in aerospace and defense applications that demand high reliability and resistance to harsh environments, such as satellite systems, military communications equipment, and avionics.
-
Consumer electronics: Flexible PCBs are increasingly used in consumer electronics to enable slim, flexible designs and improve device reliability, such as in smartphones, tablets, and laptops.
Future Trends in Flexible PCBs
As the demand for compact, lightweight, and flexible electronic devices continues to grow, the flexible PCB industry is poised for significant advancements. Some future trends in flexible PCBs include:
-
Increased use of high-frequency materials: The adoption of high-frequency materials, such as liquid crystal polymer (LCP) and PTFE, will enable faster data transmission and improved signal integrity in flexible PCBs.
-
Adoption of 3D printing technologies: 3D printing technologies, such as aerosol jet printing and inkjet printing, will enable the rapid prototyping and low-volume production of flexible PCBs with complex geometries.
-
Integration of flexible sensors and antennas: The integration of flexible sensors and antennas directly onto flexible PCBs will enable the development of smart, connected devices for applications such as wearable health monitoring and Internet of Things (IoT) systems.
-
Advancements in materials and manufacturing processes: Ongoing research and development in flexible PCB materials and manufacturing processes will lead to the creation of more robust, reliable, and cost-effective flexible circuits.
FAQ
-
What is the difference between flexible and rigid PCBs?
Flexible PCBs are made from thin, flexible substrates that can bend and twist, while rigid PCBs are made from solid, non-flexible materials such as FR-4. Flexible PCBs are used in applications that require conformity to curved surfaces or repeated flexing, while rigid PCBs are used in applications that require structural support and stability. -
Can flexible PCBs be soldered using standard soldering techniques?
Yes, flexible PCBs can be soldered using standard soldering techniques, such as hand soldering, wave soldering, and reflow soldering. However, care must be taken to avoid excessive heat and mechanical stress, which can damage the flexible substrate and coverlay materials. -
How long do flexible PCBs last compared to rigid PCBs?
The lifespan of a flexible PCB depends on various factors, such as the materials used, the application environment, and the level of mechanical stress experienced. In general, flexible PCBs can last as long as rigid PCBs when designed and manufactured properly, with some applications reporting lifespans of over 10 years. -
Can flexible PCBs be used in high-temperature applications?
Yes, flexible PCBs made with polyimide (PI) substrates can withstand temperatures up to 300°C, making them suitable for high-temperature applications. However, the choice of copper foil, coverlay, and surface finish must also be considered to ensure reliable performance at elevated temperatures. -
Are flexible PCBs more expensive than rigid PCBs?
In general, flexible PCBs are more expensive than rigid PCBs due to the specialized materials, equipment, and manufacturing processes required. However, the cost difference can vary depending on the specific design, volume, and application requirements. In some cases, the use of flexible PCBs can lead to overall system cost savings by enabling more compact packaging and reducing the need for connectors and cables.
Conclusion
Flexible PCBs are a versatile and increasingly important technology for creating compact, lightweight, and conformable electronic devices. By understanding the materials, construction techniques, and design considerations involved in flexible PCBs, engineers and designers can create reliable, high-performance circuits for a wide range of applications.
As the demand for flexible electronics continues to grow, ongoing advancements in materials, manufacturing processes, and integration technologies will drive the development of even more innovative and capable flexible PCBs in the future.
0 Comments