What are Flexible PCBs?
Flexible PCBs, also known as flex circuits, are a type of printed circuit board that can bend and flex without damaging the electrical components. Unlike traditional rigid PCBs, flexible PCBs are made from a thin, flexible substrate such as polyimide or polyester. This allows them to be used in applications where space is limited or where the PCB needs to conform to a specific shape.
Flexible PCBs can be single-sided, double-sided, or multi-layered, depending on the complexity of the circuit design. They can also be combined with rigid PCBs to create rigid-flex PCBs, which offer the best of both worlds in terms of flexibility and stability.
Benefits of Flexible PCBs
Flexible PCBs offer several advantages over traditional rigid PCBs, including:
-
Space savings: Flexible PCBs can be bent and folded to fit into tight spaces, making them ideal for applications where space is at a premium, such as wearable devices, medical implants, and aerospace equipment.
-
Weight reduction: Because flexible PCBs are thinner and lighter than rigid PCBs, they can help reduce the overall weight of a device, which is especially important in applications where weight is a critical factor, such as drones and satellites.
-
Increased reliability: Flexible PCBs are more resistant to vibration and shock than rigid PCBs, which makes them less likely to fail in harsh environments. They also have a longer lifespan due to their ability to flex and bend without cracking or breaking.
-
Improved signal integrity: Flexible PCBs can be designed with shorter signal paths and reduced crosstalk, which can improve signal integrity and reduce electromagnetic interference (EMI).
-
Cost-effectiveness: Although flexible PCBs may have a higher initial cost than rigid PCBs, they can be more cost-effective in the long run due to their increased reliability and longer lifespan. They also require fewer connectors and cables, which can further reduce costs.
The FlexPCBAssembly Process
The FlexPCBAssembly process involves several steps, from design and fabrication to assembly and testing. Here’s a brief overview of each step:
1. Design
The first step in the FlexPCBAssembly process is to design the circuit using computer-aided design (CAD) software. The designer must take into account the specific requirements of the application, such as the size and shape of the device, the number of layers needed, and the type of components that will be used.
2. Fabrication
Once the design is complete, the next step is to fabricate the flexible PCB. This involves creating a photomask of the circuit design and using it to expose a light-sensitive polymer substrate. The exposed areas are then etched away, leaving behind the copper traces that form the circuit.
3. Lamination
After the circuit has been etched, the next step is to laminate the layers together using heat and pressure. This creates a strong, flexible bond between the layers and helps to protect the circuit from damage.
4. Drilling
Once the lamination is complete, the next step is to drill holes in the PCB for component placement. This is typically done using a computer-controlled drilling machine to ensure accuracy and precision.
5. Component Placement
After the holes have been drilled, the next step is to place the components on the PCB. This is typically done using a pick-and-place machine, which uses a vacuum nozzle to pick up the components and place them on the PCB with high accuracy.
6. Soldering
Once the components have been placed, the next step is to solder them to the PCB. This is typically done using a reflow oven, which heats the PCB to a specific temperature to melt the solder and create a strong electrical and mechanical connection between the components and the PCB.
7. Testing
After the soldering is complete, the final step is to test the PCB to ensure that it functions correctly. This involves using specialized equipment to test for continuity, short circuits, and other defects.
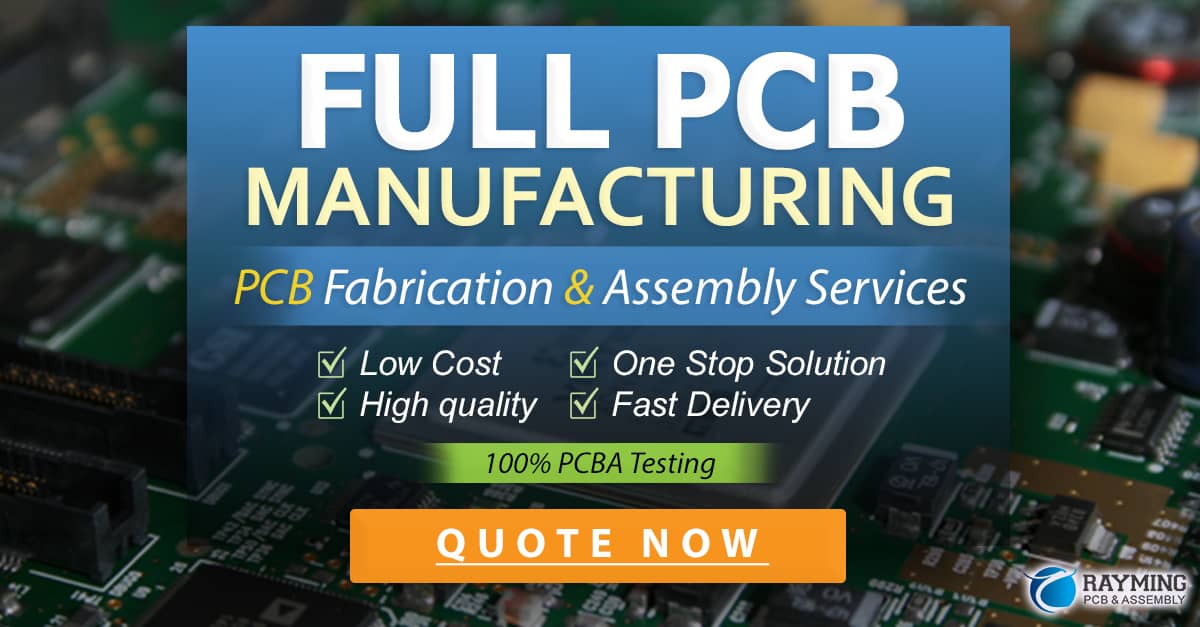
Top Flexible PCB Assembly Companies
There are many companies that offer flexible PCB assembly services, but some stand out from the rest in terms of quality, experience, and customer service. Here are some of the top flexible PCB assembly companies:
1. Cirexx International, Inc.
Cirexx International, Inc. is a leading provider of flexible PCB assembly services, with over 30 years of experience in the industry. They offer a wide range of services, including design, fabrication, assembly, and testing, and have the capability to handle both small and large production runs.
Service | Description |
---|---|
Design | Cirexx has a team of experienced designers who can work with customers to create custom flexible PCB designs that meet their specific requirements. |
Fabrication | Cirexx uses state-of-the-art equipment and processes to fabricate high-quality flexible PCBs, including single-sided, double-sided, and multi-layered designs. |
Assembly | Cirexx offers both manual and automated assembly services, with the capability to place a wide range of components, including surface mount and through-hole components. |
Testing | Cirexx uses advanced testing equipment to ensure that each PCB meets the highest standards of quality and reliability. |
2. Printed Circuits, Inc.
Printed Circuits, Inc. is another top flexible PCB assembly company, with over 40 years of experience in the industry. They specialize in high-reliability applications, such as medical devices, aerospace equipment, and military systems.
Service | Description |
---|---|
Design | Printed Circuits has a team of experienced designers who can work with customers to create custom flexible PCB designs that meet their specific requirements. |
Fabrication | Printed Circuits uses advanced fabrication techniques to create high-quality flexible PCBs, including laser direct imaging (LDI) and chemical etching. |
Assembly | Printed Circuits offers both automated and manual assembly services, with the capability to place a wide range of components, including fine-pitch and BGA components. |
Testing | Printed Circuits uses advanced testing equipment to ensure that each PCB meets the highest standards of quality and reliability, including flying probe testing and 3D x-ray inspection. |
3. All Flex, Inc.
All Flex, Inc. is a leading provider of flexible PCB assembly services, with a focus on quick-turn prototyping and low-volume production. They offer a wide range of services, including design, fabrication, assembly, and testing.
Service | Description |
---|---|
Design | All Flex has a team of experienced designers who can work with customers to create custom flexible PCB designs that meet their specific requirements. |
Fabrication | All Flex uses advanced fabrication techniques to create high-quality flexible PCBs, including laser direct imaging (LDI) and chemical etching. |
Assembly | All Flex offers both automated and manual assembly services, with the capability to place a wide range of components, including fine-pitch and BGA components. |
Testing | All Flex uses advanced testing equipment to ensure that each PCB meets the highest standards of quality and reliability, including flying probe testing and 3D x-ray inspection. |
4. Pioneer Circuits, Inc.
Pioneer Circuits, Inc. is a leading provider of flexible PCB assembly services, with a focus on high-reliability applications, such as medical devices, aerospace equipment, and military systems. They offer a wide range of services, including design, fabrication, assembly, and testing.
Service | Description |
---|---|
Design | Pioneer Circuits has a team of experienced designers who can work with customers to create custom flexible PCB designs that meet their specific requirements. |
Fabrication | Pioneer Circuits uses advanced fabrication techniques to create high-quality flexible PCBs, including laser direct imaging (LDI) and chemical etching. |
Assembly | Pioneer Circuits offers both automated and manual assembly services, with the capability to place a wide range of components, including fine-pitch and BGA components. |
Testing | Pioneer Circuits uses advanced testing equipment to ensure that each PCB meets the highest standards of quality and reliability, including flying probe testing and 3D x-ray inspection. |
Frequently Asked Questions (FAQs)
1. What is the difference between a flexible PCB and a rigid PCB?
A flexible PCB is made from a thin, flexible substrate that can bend and flex without damaging the electrical components, while a rigid PCB is made from a rigid substrate that cannot be bent or flexed. Flexible PCBs are ideal for applications where space is limited or where the PCB needs to conform to a specific shape, while rigid PCBs are better suited for applications that require a more stable and rigid structure.
2. What are the advantages of using a flexible PCB?
Flexible PCBs offer several advantages over rigid PCBs, including space savings, weight reduction, increased reliability, improved signal integrity, and cost-effectiveness. They can be bent and folded to fit into tight spaces, are more resistant to vibration and shock, and require fewer connectors and cables, which can reduce costs.
3. What is the FlexPCBAssembly process?
The FlexPCBAssembly process involves several steps, including design, fabrication, lamination, drilling, component placement, soldering, and testing. Each step is critical to ensuring that the final product meets the highest standards of quality and reliability.
4. How do I choose a flexible PCB assembly company?
When choosing a flexible PCB assembly company, there are several factors to consider, including experience, capabilities, quality, and customer service. Look for a company that has a proven track record of success in the industry, offers a wide range of services, uses advanced equipment and processes, and provides excellent customer support.
5. What industries use flexible PCBs?
Flexible PCBs are used in a wide range of industries, including medical devices, aerospace, automotive, consumer electronics, military, and telecommunications. They are particularly well-suited for applications that require high reliability, space savings, and flexibility.
Conclusion
Flexible PCBs have become an increasingly important part of the electronics industry, offering several advantages over traditional rigid PCBs. As a result, the demand for flexible PCB assembly services has grown significantly in recent years. When choosing a FlexPCBAssembly company, it’s important to consider factors such as experience, capabilities, quality, and customer service. By working with a reputable and experienced company, you can ensure that your flexible PCBs are designed, fabricated, and assembled to the highest standards of quality and reliability.
0 Comments