Introduction to Flex-Rigid PCBs
Flex-rigid PCBs are a unique type of printed circuit board that combines the best features of both flexible and rigid PCBs. These hybrid boards consist of multiple layers of flexible and rigid substrates that are laminated together to form a single board. The flexible layers allow for bending and folding of the PCB, while the rigid layers provide structural support and stability.
Flex-rigid PCBs offer several advantages over traditional rigid PCBs, including:
- Increased design flexibility
- Reduced size and weight
- Improved reliability and durability
- Enhanced electrical performance
Applications of Flex-Rigid PCBs
Flex-rigid PCBs are used in a wide range of applications, including:
- Aerospace and defense
- Medical devices
- Automotive electronics
- Consumer electronics
- Industrial automation
The ability to bend and fold the PCB allows for more compact and lightweight designs, which is particularly important in aerospace and defense applications where space and weight are at a premium. In medical devices, flex-rigid PCBs enable the creation of smaller, more advanced devices that can be implanted or worn on the body. In the automotive industry, flex-rigid PCBs are used in a variety of applications, from infotainment systems to advanced driver assistance systems (ADAS).
Flex-Rigid PCB Manufacturing Process
The manufacturing process for flex-rigid PCBs is more complex than that of traditional rigid PCBs due to the combination of flexible and rigid materials. The process typically involves the following steps:
- Design and layout
- Material selection
- Fabrication of flexible and rigid layers
- Lamination of flexible and rigid layers
- Drilling and plating of vias
- Etching of copper traces
- Solder Mask application
- Surface finish application
- Electrical testing and inspection
Design and Layout
The design and layout of a flex-rigid PCB is critical to its performance and reliability. The designer must consider the mechanical and electrical requirements of the application, as well as the limitations of the manufacturing process. The layout must also account for the bending and folding of the flexible layers, as well as the placement of components on both the flexible and rigid layers.
Material Selection
The materials used in the construction of a flex-rigid PCB must be carefully selected to ensure the desired performance and reliability. The flexible layers are typically made from polyimide or other flexible substrates, while the rigid layers are made from FR-4 or other rigid materials. The adhesives used to bond the layers together must also be selected based on the specific requirements of the application.
Material | Typical Thickness (mm) | Dielectric Constant | Dissipation Factor | Thermal Conductivity (W/mK) |
---|---|---|---|---|
Polyimide | 0.025 – 0.127 | 3.5 | 0.002 | 0.12 |
FR-4 | 0.2 – 3.2 | 4.5 | 0.02 | 0.3 |
Fabrication of Flexible and Rigid Layers
The flexible and rigid layers of the PCB are fabricated separately using different processes. The flexible layers are typically fabricated using a roll-to-roll process, where the substrate material is unwound from a roll, coated with copper, and then rewound onto another roll. The rigid layers are fabricated using a standard PCB manufacturing process, which involves laminating the substrate material with copper foil, drilling holes, and plating the holes with copper.
Lamination of Flexible and Rigid Layers
Once the flexible and rigid layers have been fabricated, they must be laminated together to form the final PCB Assembly. This is typically done using a process called “bookbinding”, where the flexible layers are sandwiched between the rigid layers and then pressed together under high temperature and pressure. The adhesive used to bond the layers together is critical to the performance and reliability of the final assembly.
Drilling and Plating of Vias
After the layers have been laminated together, holes are drilled through the board to create vias that connect the different layers together. The holes are then plated with copper to create electrical connections between the layers.
Etching of Copper Traces
The copper traces on the surface of the board are then etched using a photolithographic process. This involves applying a photoresist material to the surface of the board, exposing it to light through a photomask, and then developing the photoresist to create a pattern of copper traces.
Solder Mask Application
A solder mask is then applied to the surface of the board to protect the copper traces from oxidation and to prevent solder bridging during the assembly process.
Surface Finish Application
Finally, a surface finish is applied to the exposed copper surfaces of the board to protect them from oxidation and to improve solderability. Common surface finishes include HASL (hot air solder leveling), ENIG (electroless nickel immersion gold), and OSP (organic solderability preservative).
Electrical Testing and Inspection
After the manufacturing process is complete, the board must undergo electrical testing and inspection to ensure that it meets the required specifications. This typically involves using automated test equipment (ATE) to measure the electrical characteristics of the board, such as resistance, capacitance, and inductance. Visual inspection is also performed to check for defects such as shorts, opens, and misalignments.
Advantages of Flex-Rigid PCBs
Flex-rigid PCBs offer several advantages over traditional rigid PCBs, including:
Increased Design Flexibility
The ability to bend and fold the PCB allows for more creative and compact designs that would not be possible with a rigid PCB. This is particularly important in applications where space is limited, such as in wearable devices or implantable medical devices.
Reduced Size and Weight
Flex-rigid PCBs can be made thinner and lighter than traditional rigid PCBs, which can help to reduce the overall size and weight of the final product. This is particularly important in aerospace and defense applications where weight is a critical factor.
Improved Reliability and Durability
Flex-rigid PCBs are more durable and reliable than traditional rigid PCBs due to the flexibility of the substrate material. This allows the PCB to withstand greater mechanical stress and strain without cracking or breaking.
Enhanced Electrical Performance
Flex-rigid PCBs can offer enhanced electrical performance compared to traditional rigid PCBs due to the reduced distance between components and the ability to use shorter trace lengths. This can help to reduce signal loss and improve signal integrity.
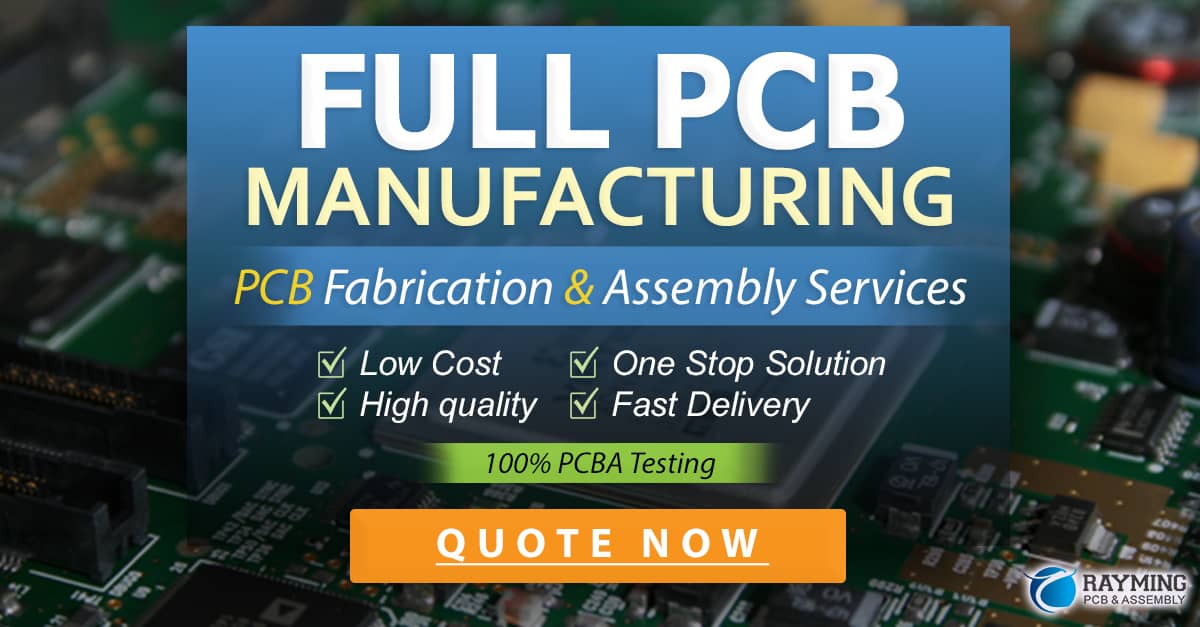
Challenges of Flex-Rigid PCB Manufacturing
Despite the many advantages of flex-rigid PCBs, there are also several challenges associated with their manufacturing, including:
Complex Design and Layout
The design and layout of a flex-rigid PCB is more complex than that of a traditional rigid PCB due to the need to account for the bending and folding of the flexible layers. This requires specialized design software and expertise to ensure that the PCB will function as intended.
Increased Manufacturing Cost
The manufacturing process for flex-rigid PCBs is more complex and time-consuming than that of traditional rigid PCBs, which can increase the overall cost of the final product. This is due to the need for specialized equipment and materials, as well as the additional steps involved in the manufacturing process.
Limited Material Options
The material options for flex-rigid PCBs are more limited than those for traditional rigid PCBs due to the need for flexibility and durability. This can make it more difficult to find materials that meet the specific requirements of the application.
Difficulty in Rework and Repair
Flex-rigid PCBs can be more difficult to rework and repair than traditional rigid PCBs due to the complexity of the layered structure. This can make it more challenging to replace damaged components or repair faulty connections.
RAYPCB: Your Partner for Flex-Rigid PCB Manufacturing
RAYPCB is a leading manufacturer of high-quality flex-rigid PCBs for a wide range of applications. With state-of-the-art manufacturing facilities and a team of experienced engineers and technicians, RAYPCB is committed to providing our customers with the highest level of quality and service.
Our flex-rigid PCB manufacturing capabilities include:
- Single-sided and double-sided flexible circuits
- Multilayer flexible circuits
- Rigid-Flex and flex-rigid circuits
- High-density interconnect (HDI) flex circuits
- Flex circuits with embedded components
- Flex circuits with shielding and grounding
We use only the highest quality materials and the latest manufacturing technologies to ensure that our flex-rigid PCBs meet or exceed the most stringent industry standards. Our manufacturing process is fully automated and controlled to ensure consistent quality and reliability.
In addition to our manufacturing capabilities, we also offer a range of value-added services to help our customers bring their products to market faster and more efficiently. These services include:
- Design and layout assistance
- Prototyping and small-batch production
- Assembly and testing
- Logistics and supply chain management
Whether you need a small batch of prototypes or a large-scale production run, RAYPCB has the expertise and capabilities to meet your needs. Contact us today to learn more about how we can help you with your flex-rigid PCB manufacturing requirements.
Frequently Asked Questions (FAQs)
-
What is a flex-rigid PCB?
A flex-rigid PCB is a type of printed circuit board that combines the benefits of both flexible and rigid PCBs. It consists of multiple layers of flexible and rigid substrates that are laminated together to form a single board. -
What are the advantages of using flex-rigid PCBs?
Flex-rigid PCBs offer several advantages over traditional rigid PCBs, including increased design flexibility, reduced size and weight, improved reliability and durability, and enhanced electrical performance. -
What are the typical applications of flex-rigid PCBs?
Flex-rigid PCBs are used in a wide range of applications, including aerospace and defense, medical devices, automotive electronics, consumer electronics, and industrial automation. -
What materials are used in the construction of flex-rigid PCBs?
The flexible layers of a flex-rigid PCB are typically made from polyimide or other flexible substrates, while the rigid layers are made from FR-4 or other rigid materials. The adhesives used to bond the layers together must also be carefully selected based on the specific requirements of the application. -
How does the manufacturing process for flex-rigid PCBs differ from that of traditional rigid PCBs?
The manufacturing process for flex-rigid PCBs is more complex than that of traditional rigid PCBs due to the combination of flexible and rigid materials. It involves additional steps such as the fabrication of flexible and rigid layers, lamination of these layers together, and the use of specialized equipment and materials.
0 Comments