What is a Rigid-Flex PCB?
A Rigid-Flex PCB is a hybrid of rigid and flexible PCBs, combining the best of both worlds. It consists of rigid PCB sections connected by flexible PCB sections, allowing the board to be bent and folded into various shapes while maintaining the stability and durability of rigid PCBs in certain areas.
Construction of Rigid-Flex PCBs
Rigid-Flex PCBs are constructed using a combination of rigid and flexible substrates. The rigid sections are typically made of FR-4 material, while the flexible sections are made of polyimide or other flexible materials. The layers are laminated together using adhesives, and conductive traces are printed on the surfaces to establish electrical connections.
Advantages of Rigid-Flex PCBs
-
Space Savings: Rigid-Flex PCBs allow for more compact designs by eliminating the need for connectors and cables between rigid sections. This leads to smaller overall package sizes and reduced weight.
-
Increased Reliability: By eliminating connectors and cables, Rigid-Flex PCBs reduce potential points of failure, resulting in higher reliability compared to separate rigid and flexible PCBs connected through cables.
-
Enhanced Signal Integrity: Rigid-Flex PCBs offer improved signal integrity by minimizing the distance signals need to travel between components. This is particularly important for high-speed and high-frequency applications.
-
Design Flexibility: Rigid-Flex PCBs allow for unique and complex shapes that can be folded and bent to fit into tight spaces or conform to specific product designs.
Disadvantages of Rigid-Flex PCBs
-
Higher Cost: Rigid-Flex PCBs are generally more expensive to manufacture compared to traditional rigid PCBs due to the specialized materials and manufacturing processes involved.
-
Longer Lead Times: The complexity of Rigid-Flex PCB design and manufacturing often results in longer lead times compared to standard rigid PCBs.
-
Design Complexity: Designing Rigid-Flex PCBs requires careful consideration of the mechanical and electrical aspects to ensure proper functionality and reliability. This complexity can increase design time and effort.
Applications of Rigid-Flex PCBs
Rigid-Flex PCBs find applications in various industries where space constraints, reliability, and design flexibility are critical factors. Some common applications include:
- Aerospace and Defense
- Medical Devices
- Wearable Electronics
- Automotive Electronics
- Consumer Electronics
What is a Flexible PCB?
A Flexible PCB, also known as a flex circuit, is a type of PCB that is designed to be flexible and bendable. Unlike rigid PCBs, flexible PCBs can conform to various shapes and can be bent, twisted, or folded as per the application requirements.
Construction of Flexible PCBs
Flexible PCBs are constructed using a thin, flexible substrate material, typically polyimide or polyester. Conductive traces are printed on the substrate using techniques such as screen printing, photolithography, or etching. The traces are usually made of copper and can be coated with a protective layer to enhance durability.
Advantages of Flexible PCBs
-
Flexibility: The primary advantage of flexible PCBs is their ability to bend and flex, allowing them to fit into tight spaces or conform to specific shapes.
-
Lightweight: Flexible PCBs are generally lighter than rigid PCBs due to the use of thin, lightweight substrate materials.
-
Vibration Resistance: The flexibility of flex circuits allows them to absorb vibrations and shocks better than rigid PCBs, making them suitable for applications subjected to vibrations.
-
Reduced Assembly Time: Flexible PCBs can simplify the assembly process by eliminating the need for separate Wire Harnesses or connectors, leading to reduced assembly time and costs.
Disadvantages of Flexible PCBs
-
Limited Layer Count: Flexible PCBs typically have a limited number of layers compared to rigid PCBs due to the thickness and flexibility requirements.
-
Reduced Heat Dissipation: The thin and flexible nature of flex circuits can limit their ability to dissipate heat effectively, which may impact the performance of high-power components.
-
Challenging Rework: Reworking or repairing flexible PCBs can be more challenging compared to rigid PCBs due to the delicate nature of the materials and the compact design.
Applications of Flexible PCBs
Flexible PCBs are used in a wide range of applications where flexibility, lightweight, and space constraints are important factors. Some common applications include:
- Consumer Electronics (e.g., smartphones, wearables)
- Medical Devices (e.g., implantable devices, medical sensors)
- Automotive Electronics (e.g., dashboard displays, sensors)
- Aerospace and Defense (e.g., avionics, satellite systems)
- Industrial Electronics (e.g., robotics, automation systems)
Comparison Table: Rigid-Flex PCB vs. Flexible PCB
Feature | Rigid-Flex PCB | Flexible PCB |
---|---|---|
Construction | Combination of rigid and flexible sections | Entirely flexible |
Flexibility | Partially flexible | Fully flexible |
Reliability | High | Moderate |
Signal Integrity | Excellent | Good |
Heat Dissipation | Good | Limited |
Layer Count | High | Limited |
Cost | Higher | Lower |
Lead Time | Longer | Shorter |
Design Complexity | High | Moderate |
Typical Applications | Aerospace, Medical, Automotive | Consumer Electronics, Wearables |
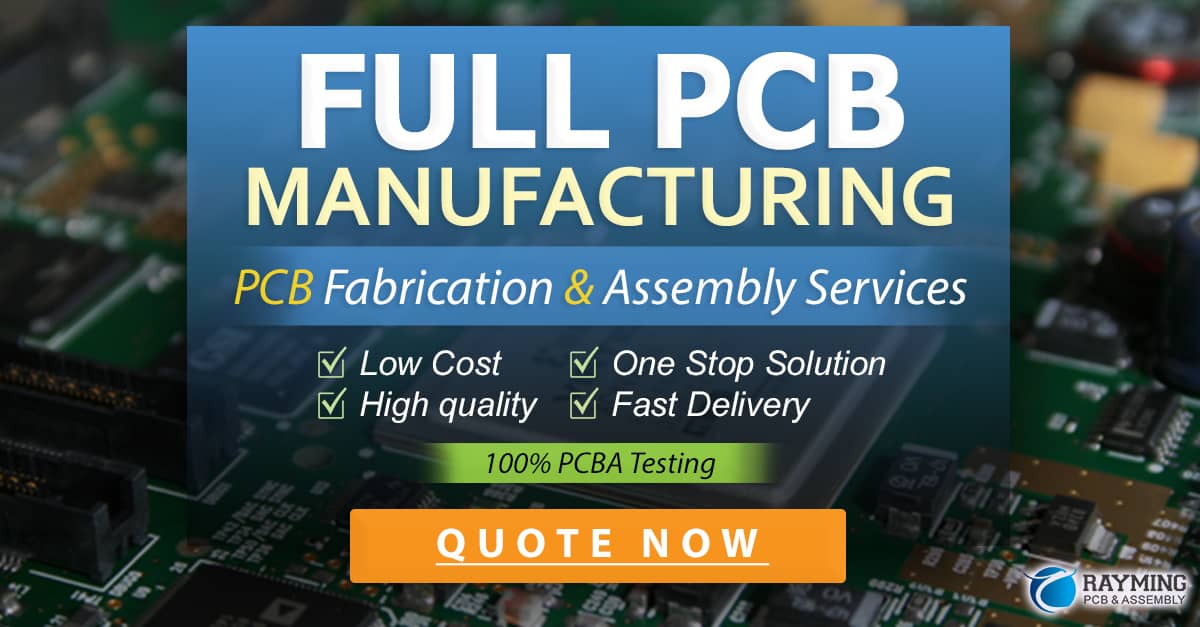
Frequently Asked Questions (FAQ)
1. Can Rigid-Flex PCBs be used in high-temperature environments?
Yes, Rigid-Flex PCBs can be designed to withstand high temperatures by using appropriate materials and manufacturing techniques. However, the specific temperature range depends on the materials used and the design requirements.
2. Are Flexible PCBs suitable for high-current applications?
Flexible PCBs can be used in high-current applications, but the current carrying capacity is limited compared to rigid PCBs due to the thin copper traces and limited heat dissipation. Proper design considerations, such as trace width and thickness, must be taken into account to ensure reliable operation.
3. How do the costs of Rigid-Flex PCBs and Flexible PCBs compare?
Rigid-Flex PCBs are generally more expensive than Flexible PCBs due to the complexity of the manufacturing process and the use of specialized materials. However, the cost difference can vary depending on factors such as the size, layer count, and quantity of the PCBs.
4. Can Rigid-Flex PCBs and Flexible PCBs be combined in a single design?
Yes, it is possible to combine Rigid-Flex PCBs and Flexible PCBs in a single design. This approach can be used to leverage the advantages of both types of PCBs and create highly customized solutions for specific applications.
5. What are the challenges in designing Rigid-Flex PCBs?
Designing Rigid-Flex PCBs requires careful consideration of both mechanical and electrical aspects. Some challenges include:
- Ensuring proper flexibility and bend radius in the flexible sections
- Minimizing stress on components during bending
- Managing signal integrity and impedance in the transition areas between rigid and flexible sections
- Selecting appropriate materials and adhesives for reliable performance
- Optimizing the layout and routing to accommodate the unique shape and requirements of the design
Conclusion
Rigid-Flex PCBs and Flexible PCBs are two distinct types of printed circuit boards that offer different advantages and are suited for various applications. Rigid-Flex PCBs combine the benefits of rigid and flexible sections, providing enhanced reliability, signal integrity, and design flexibility. On the other hand, Flexible PCBs excel in applications requiring full flexibility, lightweight, and conformity to specific shapes.
When choosing between Rigid-Flex PCBs and Flexible PCBs, designers must consider factors such as the application requirements, space constraints, reliability needs, cost, and manufacturing complexity. By understanding the characteristics and trade-offs of each type, engineers can make informed decisions and select the most suitable option for their specific project.
As technology advances and the demand for compact, flexible, and reliable electronics grows, both Rigid-Flex PCBs and Flexible PCBs will continue to play crucial roles in enabling innovative designs across various industries. By leveraging the strengths of each type and combining them when necessary, designers can create highly optimized and customized solutions that meet the evolving needs of modern electronics.
0 Comments