Understanding Electrostatic Discharge (ESD)
Electrostatic Discharge (ESD) is a sudden and rapid transfer of electrostatic charge between two objects. This occurs when two objects with different electrical potentials come into contact or when an electrically charged object comes near a conductive surface. ESD events can generate high voltages, sometimes reaching tens of thousands of volts, which can easily damage sensitive electronic components.
Triboelectric Charging
One of the primary causes of ESD is triboelectric charging. This happens when two materials come into contact and then separate, causing electrons to transfer from one material to another. The material that loses electrons becomes positively charged, while the material that gains electrons becomes negatively charged. Common examples of triboelectric charging include:
- Walking across a carpet
- Rubbing a balloon against hair
- Removing plastic packaging materials
Conductive and Insulative Materials
Materials can be classified into three categories based on their electrical conductivity:
-
Conductors: These materials allow electrons to flow freely, making them excellent carriers of electrical current. Examples include metals like copper, aluminum, and gold.
-
Insulators: These materials have high electrical resistance and do not allow electrons to flow easily. Examples include rubber, plastic, and glass.
-
Static Dissipative Materials: These materials have electrical resistance between conductors and insulators. They can conduct electricity, but at a slower rate, allowing charges to dissipate gradually. Examples include certain types of plastics and coatings.
Understanding the properties of these materials is essential for implementing effective ESD protection measures.
ESD Sensitivity of Electronic Components
Electronic components vary in their sensitivity to ESD. Some components can withstand relatively high voltages, while others can be damaged by just a few volts. The ESD sensitivity of a component depends on factors such as its size, material composition, and manufacturing process.
ESD Sensitivity Classifications
The Electronics Industry Association (EIA) has established a classification system for the ESD sensitivity of electronic components. The system divides components into three categories:
-
Class 0: These components are extremely sensitive to ESD and can be damaged by voltages less than 250 volts.
-
Class 1: These components are sensitive to ESD and can be damaged by voltages between 250 and 1,999 volts.
-
Class 2: These components are less sensitive to ESD and can withstand voltages between 2,000 and 3,999 volts.
It is essential to identify the ESD sensitivity of the components used in a PCB Assembly to determine the appropriate level of ESD protection required.
Common ESD-Sensitive Components
Some of the most common ESD-sensitive components used in PCB assemblies include:
- Metal Oxide Semiconductor Field Effect Transistors (MOSFETs)
- Complementary Metal Oxide Semiconductors (CMOS)
- Bipolar Junction Transistors (BJTs)
- Integrated Circuits (ICs)
- Laser diodes
- Thin film resistors
These components require special handling and protection measures to prevent ESD damage during the assembly process.
ESD Protection Measures for PCB Assembly
To ensure maximum PCB ESD Protection during electronics assembly, a comprehensive approach involving both equipment and personnel is necessary. Here are some key measures to implement:
ESD-Safe Workstations
An ESD-safe workstation is a designated area where PCB assembly takes place. This area should be equipped with the following:
-
ESD-Safe Work Surfaces: These surfaces are made of static dissipative materials that prevent the buildup of electrostatic charges. They are typically connected to a common ground point to ensure a safe electrical potential.
-
ESD-Safe Floors: ESD-safe floors are made of conductive or static dissipative materials that prevent the accumulation of electrostatic charges. They are also connected to a common ground point.
-
ESD-Safe Chairs: Chairs used in ESD-safe workstations should have conductive casters and be covered with static dissipative materials to prevent the buildup of charges on the operator’s body.
-
ESD-Safe Storage Containers: PCBs and components should be stored in ESD-safe containers made of static dissipative materials. These containers shield the contents from external ESD events and prevent the buildup of charges inside.
Personnel Grounding
One of the most critical aspects of ESD protection is personnel grounding. This involves ensuring that operators are electrically connected to a common ground point to prevent the buildup of electrostatic charges on their bodies. Personnel grounding can be achieved through the following methods:
-
Wrist Straps: Wrist straps are conductive bands worn around the wrist and connected to a common ground point through a cord. They ensure a continuous electrical connection between the operator’s body and ground, preventing the buildup of charges.
-
ESD-Safe Footwear: ESD-safe footwear, such as conductive shoes or heel grounders, provide a path for electrostatic charges to dissipate from the operator’s body to the ESD-safe floor.
-
ESD-Safe Clothing: ESD-safe clothing, such as lab coats and smocks, are made of static dissipative materials that prevent the buildup of charges on the operator’s clothing.
ESD-Safe Tools and Equipment
In addition to personnel grounding, it is essential to use ESD-safe tools and equipment during PCB assembly. This includes:
-
ESD-Safe Soldering Irons: Soldering irons used in ESD-safe environments should have grounded tips to prevent the buildup of charges during the soldering process.
-
ESD-Safe Tweezers and Pliers: ESD-safe tweezers and pliers are made of static dissipative materials and have grounded tips to prevent ESD events when handling components.
-
ESD-Safe Brushes: Brushes used for cleaning PCBs should be made of static dissipative materials to prevent the buildup of charges during the cleaning process.
ESD Training and Awareness
Effective ESD protection requires a well-trained and aware workforce. All personnel involved in PCB assembly should receive comprehensive ESD training, covering topics such as:
- Understanding ESD and its effects on electronic components
- Proper use of ESD-safe equipment and tools
- Personnel grounding procedures
- Handling and storage of ESD-sensitive components
- Identifying and reporting ESD events
Regular refresher training and audits should be conducted to ensure that ESD protection procedures are being followed consistently.
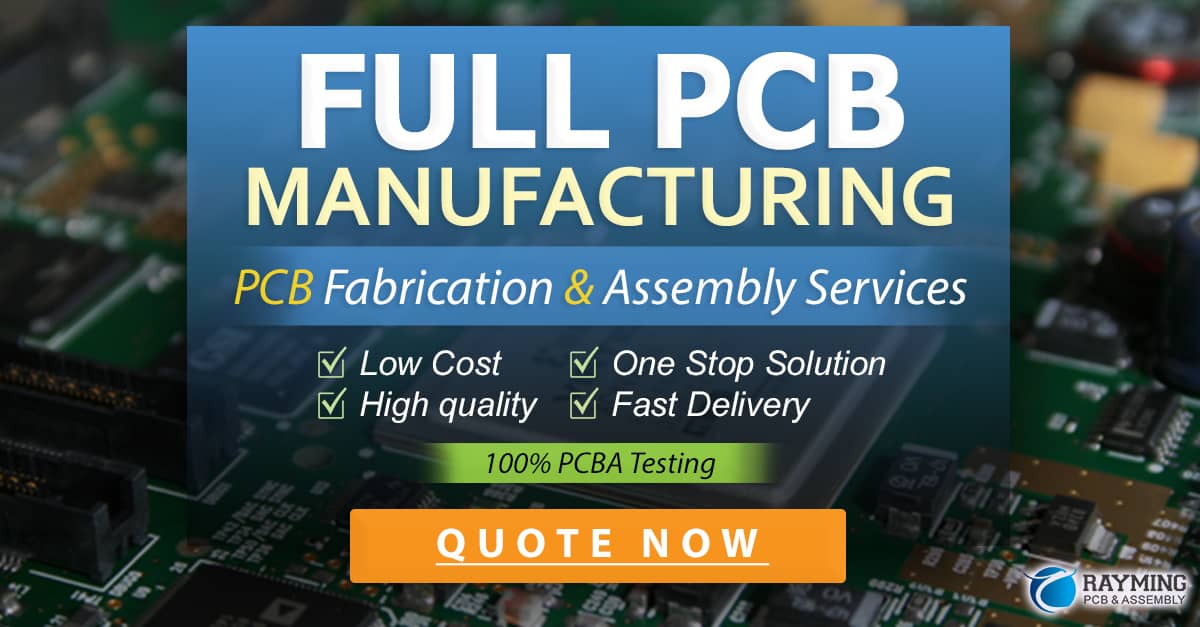
ESD Protection in PCB Design
In addition to implementing ESD protection measures during assembly, it is crucial to consider ESD protection during the PCB design phase. By incorporating ESD protection features into the PCB layout, designers can minimize the risk of ESD damage to sensitive components.
Grounding and Shielding
One of the most effective ways to provide ESD protection in PCB design is through proper grounding and shielding. This involves creating a low-impedance path for electrostatic charges to dissipate safely, away from sensitive components. Some key grounding and shielding techniques include:
-
Ground Planes: Incorporating a solid ground plane in the PCB layout provides a low-impedance path for electrostatic charges to dissipate. This helps to minimize the voltage differences between components and reduces the risk of ESD damage.
-
Guard Rings: Guard rings are conductive traces placed around sensitive components to provide a protective barrier against ESD events. They work by diverting electrostatic charges away from the components and into the ground plane.
-
Shielding: Shielding sensitive components with conductive enclosures or coatings can help to reduce their exposure to external ESD events. This is particularly useful for components that are not easily protected by other means, such as connectors and switches.
Component Placement and Routing
The placement and routing of components on a PCB can also have a significant impact on ESD protection. Some best practices include:
-
Spacing: Placing sensitive components away from the edges of the PCB and maintaining adequate spacing between them can help to reduce the risk of ESD damage. This is because ESD events are more likely to occur at the edges of the board, where charges can accumulate.
-
Routing: Routing traces away from sensitive components and avoiding sharp bends or corners can help to reduce the risk of ESD damage. Sharp bends and corners can create voltage gradients that can lead to ESD events.
-
Connector Placement: Placing connectors and other external interfaces away from sensitive components can help to reduce the risk of ESD damage. This is because connectors are often exposed to external ESD events, such as when plugging in cables.
ESD Protection Devices
Incorporating ESD protection devices into the PCB design can provide an additional layer of protection against ESD events. These devices work by diverting electrostatic charges away from sensitive components and into the ground plane. Some common ESD protection devices include:
-
Transient Voltage Suppressors (TVS): TVS devices are designed to clamp the voltage across a sensitive component to a safe level during an ESD event. They work by quickly switching from a high-impedance state to a low-impedance state when the voltage exceeds a certain threshold.
-
Diodes: Diodes can be used to provide unidirectional ESD protection by allowing current to flow in only one direction. They are often used in pairs, with one diode connected to the positive supply rail and the other connected to the ground plane.
-
Varistors: Varistors are voltage-dependent resistors that provide bidirectional ESD protection. They work by changing their resistance based on the applied voltage, allowing them to clamp the voltage across a sensitive component to a safe level during an ESD event.
Testing and Verification
To ensure that a PCB assembly meets the required level of ESD protection, it is essential to conduct thorough testing and verification. This involves subjecting the assembly to simulated ESD events and measuring the response of the system to ensure that it meets the specified performance criteria.
ESD Simulation Testing
ESD simulation testing involves applying a controlled ESD pulse to the PCB assembly and measuring the response of the system. This can be done using specialized ESD testing equipment, such as:
-
ESD Guns: ESD guns are handheld devices that generate a controlled ESD pulse, which can be applied to specific points on the PCB assembly. The response of the system is then measured using an oscilloscope or other measurement device.
-
ESD Simulators: ESD simulators are bench-top devices that generate a controlled ESD pulse and apply it to the PCB assembly through a series of probes. The response of the system is then measured and analyzed to ensure that it meets the specified performance criteria.
System-Level ESD Testing
In addition to component-level ESD testing, it is essential to conduct system-level ESD testing to ensure that the entire PCB assembly is protected against ESD events. This involves subjecting the assembly to simulated ESD events in a controlled environment, such as an ESD testing chamber.
During system-level ESD testing, the PCB assembly is placed in the testing chamber and subjected to a series of ESD pulses at different voltages and polarities. The response of the system is then measured and analyzed to ensure that it meets the specified performance criteria.
Verification and Certification
To ensure that a PCB assembly meets the required level of ESD protection, it is essential to obtain verification and certification from a recognized testing laboratory. This involves submitting the assembly for testing and evaluation to ensure that it meets the relevant industry standards, such as:
- IEC 61000-4-2: Electromagnetic Compatibility (EMC) – Part 4-2: Testing and Measurement Techniques – Electrostatic Discharge Immunity Test
- ANSI/ESD S20.20: Protection of Electrical and Electronic Parts, Assemblies and Equipment (Excluding Electrically Initiated Explosive Devices)
Obtaining verification and certification from a recognized testing laboratory provides assurance that the PCB assembly meets the required level of ESD protection and is suitable for use in its intended application.
Frequently Asked Questions (FAQ)
-
What is Electrostatic Discharge (ESD)?
Electrostatic Discharge (ESD) is the sudden flow of electricity between two electrically charged objects. This can occur when two objects with different electrical potentials come into contact or when an electrically charged object comes near a conductive surface. -
Why is ESD protection important in PCB assembly?
ESD protection is important in PCB assembly because electronic components are sensitive to ESD events. Even a small ESD event can cause permanent damage to components, leading to reduced performance, malfunctions, and even complete failure of the final product. -
What are some common ESD-sensitive components?
Some common ESD-sensitive components used in PCB assemblies include Metal Oxide Semiconductor Field Effect Transistors (MOSFETs), Complementary Metal Oxide Semiconductors (CMOS), Bipolar Junction Transistors (BJTs), Integrated Circuits (ICs), laser diodes, and thin film resistors. -
What are some key measures for ensuring ESD protection during PCB assembly?
Some key measures for ensuring ESD protection during PCB assembly include using ESD-safe workstations, personnel grounding, ESD-safe tools and equipment, and providing ESD training and awareness to all personnel involved in the assembly process. -
How can ESD protection be incorporated into PCB design?
ESD protection can be incorporated into PCB design through proper grounding and shielding techniques, strategic component placement and routing, and the use of ESD protection devices such as Transient Voltage Suppressors (TVS), diodes, and varistors.
Conclusion
Ensuring maximum PCB ESD protection is essential for the quality and reliability of electronic assemblies. By implementing a comprehensive approach that includes ESD-safe workstations, personnel grounding, ESD-safe tools and equipment, and ESD training and awareness, manufacturers can significantly reduce the risk of ESD damage during the assembly process.
Furthermore, by incorporating ESD protection features into the PCB design, such as proper grounding and shielding, strategic component placement and routing, and the use of ESD protection devices, designers can provide an additional layer of protection against ESD events.
Finally, thorough testing and verification, including ESD simulation testing and system-level ESD testing, are crucial for ensuring that a PCB assembly meets the required level of ESD protection. Obtaining verification and certification from a recognized testing laboratory provides assurance that the assembly is suitable for use in its intended application.
By following these best practices and guidelines, manufacturers can ensure maximum PCB ESD protection and deliver high-quality, reliable electronic products to their customers.
ESD Protection Measure | Description |
---|---|
ESD-Safe Workstations | Designated areas equipped with ESD-safe work surfaces, floors, chairs, and storage containers to prevent the buildup of electrostatic charges. |
Personnel Grounding | Ensuring operators are electrically connected to a common ground point through wrist straps, ESD-safe footwear, and ESD-safe clothing. |
ESD-Safe Tools and Equipment | Using tools and equipment made of static dissipative materials and with grounded tips to prevent ESD events during assembly. |
ESD Training and Awareness | Providing comprehensive ESD training to all personnel involved in PCB assembly, covering topics such as proper use of ESD-safe equipment and handling of ESD-sensitive components. |
Grounding and Shielding | Incorporating ground planes, guard rings, and shielding in the PCB layout to provide a low-impedance path for electrostatic charges to dissipate safely. |
Component Placement and Routing | Placing sensitive components away from the edges of the PCB, maintaining adequate spacing, and routing traces away from sensitive components to reduce the risk of ESD damage. |
ESD Protection Devices | Incorporating devices such as Transient Voltage Suppressors (TVS), diodes, and varistors into the PCB design to divert electrostatic charges away from sensitive components. |
ESD Simulation Testing | Applying controlled ESD pulses to the PCB assembly using specialized testing equipment and measuring the response of the system to ensure it meets the specified performance criteria. |
System-Level ESD Testing | Subjecting the entire PCB assembly to simulated ESD events in a controlled environment, such as an ESD testing chamber, to ensure it is protected against ESD events. |
Verification and Certification | Obtaining verification and certification from a recognized testing laboratory to ensure the PCB assembly meets the relevant industry standards for ESD protection. |
0 Comments