Introduction to ENEPIG
ENEPIG (Electroless Nickel/Electroless Palladium/Immersion Gold) is a popular surface finish for printed circuit boards (PCBs) and electronic components. This advanced plating technology combines the benefits of electroless nickel, electroless palladium, and immersion gold to create a robust, reliable, and solderable surface finish that meets the demanding requirements of high-performance devices.
The Importance of Surface Finishes in Electronics Manufacturing
Surface finishes play a crucial role in the performance and reliability of electronic devices. They serve multiple purposes, including:
- Protecting the underlying copper from oxidation and corrosion
- Enhancing solderability and ensuring strong solder joints
- Providing a smooth, uniform surface for component assembly
- Improving electrical conductivity and signal integrity
- Extending the shelf life of PCBs and components
Why Choose ENEPIG?
ENEPIG has gained popularity in recent years due to its superior performance compared to other surface finishes. Some of the key advantages of ENEPIG include:
- Excellent solderability: The immersion gold layer provides a clean, oxide-free surface that promotes strong solder joints.
- Enhanced durability: The electroless nickel layer offers excellent wear and corrosion resistance, while the palladium layer prevents the diffusion of nickel into the gold layer.
- Compatibility with various assembly processes: ENEPIG is suitable for both lead-free and leaded soldering, as well as wire bonding and other advanced packaging techniques.
- Extended shelf life: The combination of nickel, palladium, and gold layers provides long-term protection against oxidation and contamination.
- RoHS compliance: ENEPIG is a lead-free surface finish that meets the requirements of the Restriction of Hazardous Substances (RoHS) directive.
The ENEPIG Plating Process
The ENEPIG plating process involves three main steps: electroless nickel plating, electroless palladium plating, and immersion gold plating. Each step plays a specific role in creating the final surface finish.
Step 1: Electroless Nickel Plating
Electroless nickel plating is the first step in the ENEPIG process. This step involves depositing a thin layer of nickel (typically 3-6 μm) onto the copper surface using an autocatalytic chemical reaction. The nickel layer serves as a barrier between the copper and the subsequent palladium and gold layers, preventing the diffusion of copper and improving the overall durability of the surface finish.
The electroless nickel plating process consists of the following sub-steps:
- Cleaning: The copper surface is thoroughly cleaned to remove any contaminants or oxides that may interfere with the plating process.
- Activation: The surface is activated using a palladium-based catalyst to promote the adhesion of the nickel layer.
- Plating: The PCB or component is immersed in an electroless nickel plating solution, where the nickel ions are reduced and deposited onto the copper surface.
- Rinsing: The plated surface is rinsed with deionized water to remove any residual plating solution.
Step 2: Electroless Palladium Plating
The second step in the ENEPIG process is electroless palladium plating. This step involves depositing a thin layer of palladium (typically 0.05-0.2 μm) onto the nickel surface using a similar autocatalytic chemical reaction. The palladium layer acts as a barrier between the nickel and gold layers, preventing the diffusion of nickel into the gold and maintaining the solderability of the surface finish.
The electroless palladium plating process consists of the following sub-steps:
- Cleaning: The nickel surface is cleaned to remove any contaminants or oxides.
- Activation: The surface is activated using a palladium-based catalyst to promote the adhesion of the palladium layer.
- Plating: The PCB or component is immersed in an electroless palladium plating solution, where the palladium ions are reduced and deposited onto the nickel surface.
- Rinsing: The plated surface is rinsed with deionized water to remove any residual plating solution.
Step 3: Immersion Gold Plating
The final step in the ENEPIG process is immersion gold plating. This step involves depositing a thin layer of gold (typically 0.05-0.2 μm) onto the palladium surface using a displacement reaction. The gold layer provides a clean, oxide-free surface that promotes strong solder joints and enhances the overall solderability of the surface finish.
The immersion gold plating process consists of the following sub-steps:
- Cleaning: The palladium surface is cleaned to remove any contaminants or oxides.
- Plating: The PCB or component is immersed in an immersion gold plating solution, where the gold ions displace the palladium ions on the surface.
- Rinsing: The plated surface is rinsed with deionized water to remove any residual plating solution.
- Drying: The PCB or component is dried to remove any moisture and prevent oxidation.
Advantages of ENEPIG in High-Performance Devices
ENEPIG offers several advantages that make it an ideal surface finish for high-performance devices. These advantages include:
1. Improved Signal Integrity
The thin, uniform layers of nickel, palladium, and gold in ENEPIG provide a smooth, low-resistance surface that enhances signal integrity. This is particularly important in high-frequency applications, where signal loss and distortion can significantly impact device performance.
2. Enhanced Solder Joint Reliability
The immersion gold layer in ENEPIG promotes strong, reliable solder joints by providing a clean, oxide-free surface for soldering. This reduces the risk of solder joint failures, such as cold solder joints or solder bridging, which can lead to device malfunction or premature failure.
3. Compatibility with Advanced Packaging Techniques
ENEPIG is compatible with a wide range of advanced packaging techniques, including wire bonding, flip-chip bonding, and ball grid array (BGA) packaging. The smooth, uniform surface finish provided by ENEPIG ensures reliable bonding and minimizes the risk of package-related failures.
4. Improved Durability and Shelf Life
The combination of electroless nickel, electroless palladium, and immersion gold layers in ENEPIG provides excellent protection against oxidation, corrosion, and wear. This extends the shelf life of PCBs and components, reducing the risk of device failure due to surface finish degradation.
5. RoHS Compliance
ENEPIG is a lead-free surface finish that meets the requirements of the Restriction of Hazardous Substances (RoHS) directive. This makes it an environmentally friendly choice for high-performance devices, as it reduces the use of hazardous substances in electronics manufacturing.
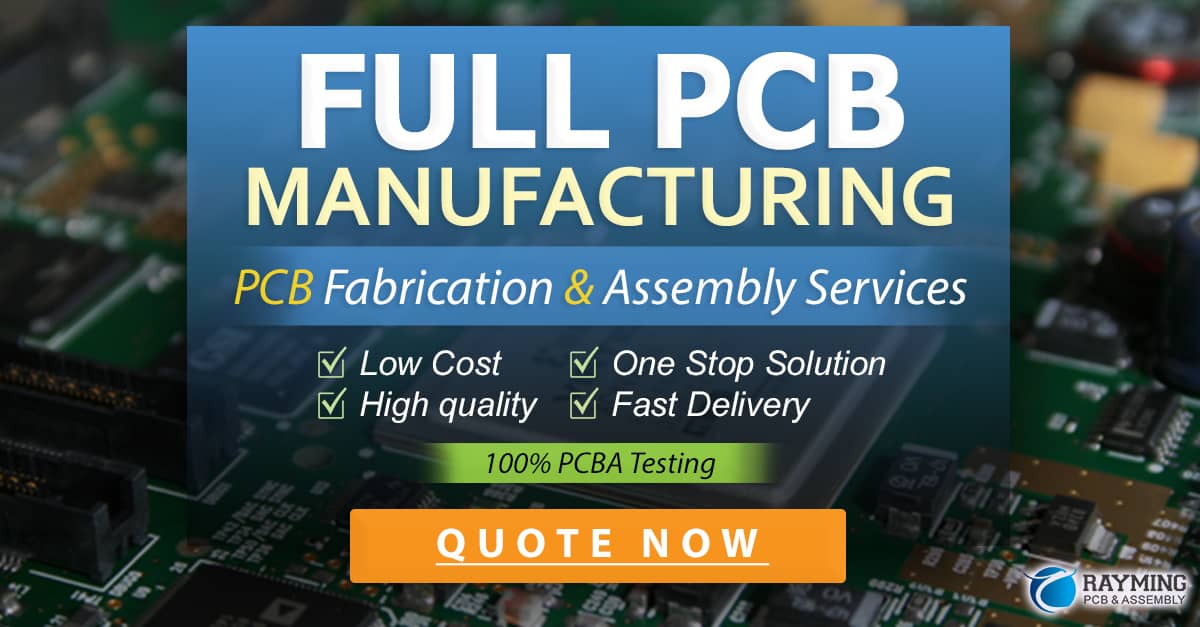
ENEPIG vs. Other Surface Finishes
ENEPIG is one of several surface finishes used in electronics manufacturing. Some of the most common alternatives to ENEPIG include:
1. HASL (Hot Air Solder Leveling)
HASL is a traditional surface finish that involves dipping the PCB or component in molten solder and then leveling the surface using hot air. While HASL is relatively inexpensive and easy to apply, it has several drawbacks, including:
- Uneven surface finish due to solder buildup
- Limited compatibility with fine-pitch components
- Potential for solder bridging and shorts
- Presence of lead in some HASL formulations
2. OSP (Organic Solderability Preservative)
OSP is a lead-free surface finish that involves applying a thin, organic coating to the copper surface to prevent oxidation. OSP offers several advantages, such as:
- Low cost compared to other surface finishes
- Good solderability
- Compatibility with a wide range of soldering processes
However, OSP also has some limitations, including:
- Limited shelf life due to the degradation of the organic coating
- Potential for inconsistent surface finish due to variations in coating thickness
- Incompatibility with some advanced packaging techniques, such as wire bonding
3. ENIG (Electroless Nickel/Immersion Gold)
ENIG is another popular surface finish that combines electroless nickel and immersion gold plating. ENIG offers several benefits, including:
- Good solderability and wire bonding compatibility
- Excellent corrosion resistance
- RoHS compliance
However, ENIG also has some drawbacks, such as:
- Potential for “black pad” formation due to the corrosion of the nickel layer
- Limited shelf life compared to ENEPIG
- Higher cost compared to OSP and HASL
The table below summarizes the key differences between ENEPIG, HASL, OSP, and ENIG:
Surface Finish | Composition | Advantages | Disadvantages |
---|---|---|---|
ENEPIG | Electroless Ni/Pd/Immersion Au | – Excellent solderability and durability – Compatibility with advanced packaging – Extended shelf life – RoHS compliance |
– Higher cost compared to HASL and OSP |
HASL | Solder (Sn/Pb or Pb-free) | – Low cost – Easy to apply |
– Uneven surface finish – Limited fine-pitch compatibility – Potential for lead content |
OSP | Organic coating | – Low cost – Good solderability – RoHS compliance |
– Limited shelf life – Potential for inconsistent surface finish – Incompatibility with some advanced packaging techniques |
ENIG | Electroless Ni/Immersion Au | – Good solderability and wire bonding compatibility – Excellent corrosion resistance – RoHS compliance |
– Potential for “black pad” formation – Limited shelf life compared to ENEPIG – Higher cost compared to OSP and HASL |
Implementing ENEPIG in Your Manufacturing Process
To implement ENEPIG in your electronics manufacturing process, consider the following steps:
-
Evaluate your product requirements: Determine whether ENEPIG is the most suitable surface finish for your application based on factors such as performance, reliability, and cost.
-
Select a qualified ENEPIG supplier: Choose a supplier with a proven track record of providing high-quality ENEPIG plating services. Consider factors such as technical expertise, process control, and customer support.
-
Design for manufacturability: Ensure that your PCB and component designs are compatible with the ENEPIG plating process. This may involve adjusting design parameters, such as pad sizes and spacing, to accommodate the plating process.
-
Establish process controls: Work with your ENEPIG supplier to establish appropriate process controls, such as plating bath composition, temperature, and time, to ensure consistent and reliable results.
-
Conduct quality assurance testing: Implement a comprehensive quality assurance program to verify the performance and reliability of your ENEPIG-plated products. This may include visual inspection, solderability testing, and accelerated life testing.
By following these steps and collaborating closely with your ENEPIG supplier, you can successfully implement ENEPIG in your manufacturing process and realize the benefits of this advanced surface finish technology.
Frequently Asked Questions (FAQ)
- Q: What is the typical thickness of each layer in ENEPIG?
A: The typical thickness of each layer in ENEPIG is as follows: - Electroless nickel: 3-6 μm
- Electroless palladium: 0.05-0.2 μm
-
Immersion gold: 0.05-0.2 μm
-
Q: Is ENEPIG suitable for both lead-free and leaded soldering processes?
A: Yes, ENEPIG is compatible with both lead-free and leaded soldering processes, making it a versatile choice for a wide range of applications. -
Q: How does ENEPIG compare to ENIG in terms of cost?
A: ENEPIG is generally more expensive than ENIG due to the additional palladium layer. However, the improved performance and reliability of ENEPIG may justify the higher cost in high-performance applications. -
Q: Can ENEPIG be used for wire bonding applications?
A: Yes, ENEPIG is compatible with wire bonding and other advanced packaging techniques, thanks to its smooth, uniform surface finish. -
Q: How does ENEPIG extend the shelf life of PCBs and components compared to other surface finishes?
A: The combination of electroless nickel, electroless palladium, and immersion gold layers in ENEPIG provides excellent protection against oxidation and contamination, extending the shelf life of PCBs and components compared to surface finishes like OSP and HASL.
Conclusion
ENEPIG is a high-performance surface finish that offers numerous benefits for demanding electronic applications. By combining the advantages of electroless nickel, electroless palladium, and immersion gold, ENEPIG provides excellent solderability, durability, and compatibility with advanced packaging techniques.
As the electronics industry continues to push the boundaries of performance and miniaturization, ENEPIG is poised to play an increasingly important role in enabling the next generation of high-performance devices. By understanding the benefits and implementation considerations of ENEPIG, electronics manufacturers can leverage this advanced surface finish technology to create products that meet the most stringent requirements for reliability, signal integrity, and environmental compliance.
0 Comments