What is ENEPIG Plating?
ENEPIG is a type of surface finish that consists of three layers: electroless nickel, electroless palladium, and immersion gold. These layers are deposited onto the copper pads of a PCB to protect the copper from oxidation and provide a reliable surface for soldering components.
Layers of ENEPIG Plating
-
Electroless Nickel (Ni): The first layer, typically 3-6 microns thick, serves as a barrier between the copper and subsequent layers. It prevents the diffusion of copper into the palladium and gold layers, which could lead to brittleness and reduced solderability.
-
Electroless Palladium (Pd): The second layer, usually 0.05-0.15 microns thick, acts as a barrier between the nickel and gold layers. It prevents the formation of nickel-gold intermetallic compounds, which could cause joint brittleness.
-
Immersion Gold (Au): The final layer, typically 0.05-0.15 microns thick, provides excellent solderability and protects the palladium layer from oxidation. The thin gold layer allows for easy fusion with the solder during the assembly process.
Advantages of ENEPIG Plating
ENEPIG plating offers several advantages over other surface finishes:
-
Excellent Solderability: The thin gold layer provides excellent wettability and solderability, ensuring reliable solder joints.
-
Long Shelf Life: ENEPIG-plated PCBs have a long shelf life, as the gold layer protects the underlying layers from oxidation.
-
Compatibility: ENEPIG is compatible with a wide range of soldering processes, including reflow soldering, wave soldering, and hand soldering.
-
Fine Pitch Capability: The thin layers of ENEPIG allow for fine pitch components, making it suitable for high-density PCB designs.
-
Aluminum Wire Bonding: ENEPIG is compatible with aluminum wire bonding, which is commonly used in certain applications, such as automotive and aerospace industries.
Applications of ENEPIG Plating
ENEPIG plating is widely used in various industries and applications:
-
Consumer Electronics: Smartphones, tablets, laptops, and other consumer electronic devices often use ENEPIG-plated PCBs for their high reliability and compatibility with fine pitch components.
-
Automotive Electronics: ENEPIG’s compatibility with aluminum wire bonding makes it suitable for automotive electronics, where reliability under harsh conditions is crucial.
-
Aerospace and Defense: The long shelf life and reliability of ENEPIG-plated PCBs make them a popular choice for aerospace and defense applications.
-
Medical Devices: ENEPIG’s excellent solderability and reliability are essential for medical devices, where failure can have severe consequences.
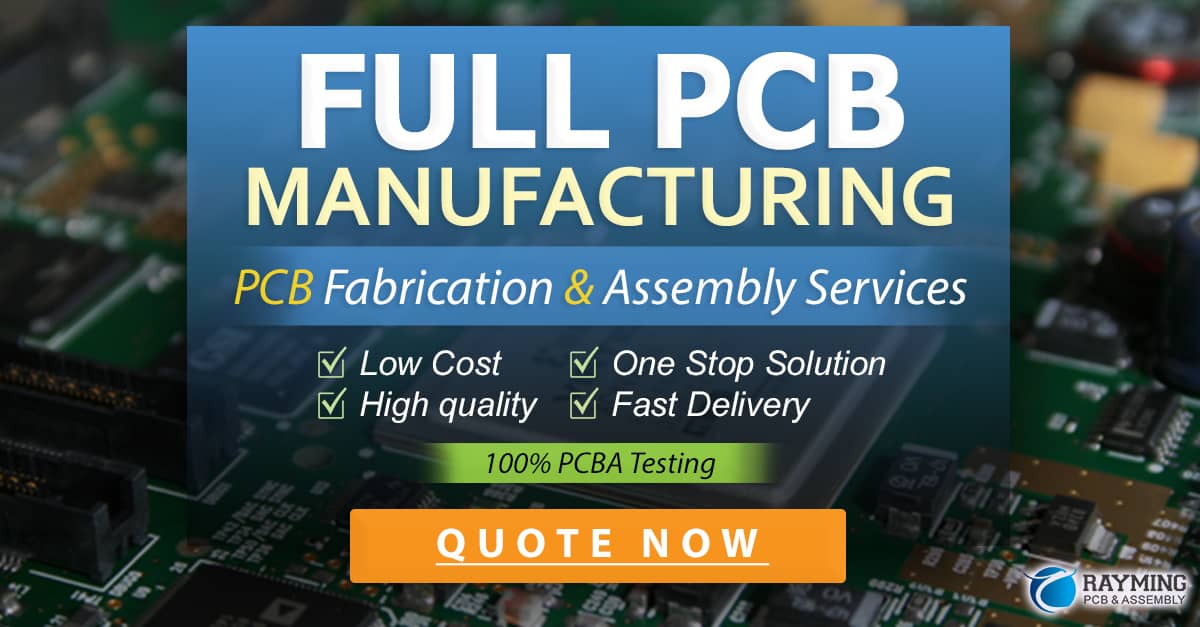
ENEPIG Plating Process
The ENEPIG plating process involves several steps:
-
Cleanliness: The PCB is thoroughly cleaned to remove any contaminants that could affect the plating process.
-
Copper Preparation: The exposed copper pads are treated with a micro-etch solution to remove any oxides and provide a uniform surface for plating.
-
Electroless Nickel Plating: The PCB is immersed in an electroless nickel plating bath, where a thin layer of nickel is deposited onto the copper pads through an auto-catalytic chemical reaction.
-
Electroless Palladium Plating: After rinsing, the PCB is immersed in an electroless palladium plating bath, where a thin layer of palladium is deposited onto the nickel layer.
-
Immersion Gold Plating: Finally, the PCB is immersed in an immersion gold plating bath, where a thin layer of gold is deposited onto the palladium layer through a displacement reaction.
-
Inspection and Testing: The plated PCB is inspected for any defects and tested to ensure it meets the required specifications.
Comparison with Other Surface Finishes
ENEPIG plating is often compared to other popular surface finishes, such as ENIG (Electroless Nickel Immersion Gold) and HASL (Hot Air Solder Leveling).
Surface Finish | Advantages | Disadvantages |
---|---|---|
ENEPIG | Excellent solderability, long shelf life, compatibility with various processes, fine pitch capability, aluminum wire bonding compatibility | Higher cost compared to other finishes, more complex process |
ENIG | Good solderability, flat surface, suitable for fine pitch components | Potential for “black pad” defect, shorter shelf life compared to ENEPIG |
HASL | Low cost, good solderability, easy to inspect | Uneven surface, not suitable for fine pitch components, shorter shelf life compared to ENEPIG |
Frequently Asked Questions (FAQ)
-
Q: What is the typical thickness of each layer in ENEPIG plating?
A: The typical thickness of the electroless nickel layer is 3-6 microns, while the electroless palladium and immersion gold layers are usually 0.05-0.15 microns each. -
Q: How does ENEPIG compare to ENIG in terms of cost?
A: ENEPIG is generally more expensive than ENIG due to the additional palladium layer and the more complex plating process. -
Q: Can ENEPIG-plated PCBs be reworked?
A: Yes, ENEPIG-plated PCBs can be reworked using standard soldering techniques. However, care must be taken not to damage the plating during the rework process. -
Q: What is the shelf life of ENEPIG-plated PCBs?
A: ENEPIG-plated PCBs have a relatively long shelf life, typically 12 months or more, due to the protection provided by the gold layer. -
Q: Is ENEPIG suitable for press-fit connectors?
A: Yes, ENEPIG is suitable for press-fit connectors, as the nickel and palladium layers provide a hard, wear-resistant surface that can withstand the mechanical stress of the press-fit process.
Conclusion
ENEPIG plating is a highly reliable and versatile surface finish technology that offers excellent solderability, long shelf life, and compatibility with various assembly processes. Its unique three-layer structure, consisting of electroless nickel, electroless palladium, and immersion gold, provides superior protection for the copper pads and ensures reliable solder joints. While more expensive than some other surface finishes, ENEPIG’s benefits make it a popular choice for a wide range of applications, from consumer electronics to automotive, aerospace, and medical devices.
As the electronics industry continues to evolve, with increasing demands for higher density, reliability, and performance, ENEPIG plating is well-positioned to meet these challenges. By understanding the advantages, applications, and process involved in ENEPIG plating, PCB manufacturers and designers can make informed decisions when selecting the most appropriate surface finish for their projects.
0 Comments