Introduction to PCB Drilling
Printed Circuit Boards (PCBs) are the backbone of modern electronics. They provide a platform for mounting and interconnecting electronic components, enabling the creation of complex circuits in a compact and efficient manner. One crucial step in the PCB manufacturing process is drilling, which involves creating holes in the board to accommodate components and facilitate electrical connections.
PCB drilling is a precise and delicate operation that requires specialized equipment and techniques. The accuracy and quality of the drilled holes directly impact the functionality and reliability of the final product. In this article, we will delve into the world of PCB drilling, exploring its importance, methods, challenges, and best practices.
The Importance of PCB Drilling
PCB drilling plays a vital role in the overall manufacturing process. Here are some key reasons why drilling is crucial:
Component Mounting
Many electronic components, such as through-hole components, require holes to be drilled in the PCB for mounting. These holes allow the component leads to pass through the board and be soldered onto the opposite side. Accurate drilling ensures proper alignment and secure mounting of components.
Electrical Connections
Drilled holes are also used to create electrical connections between different layers of a multi-layer PCB. These holes, known as vias, allow signals to travel vertically through the board, enabling more complex routing and circuit design. Precise drilling is essential to maintain the integrity of these connections.
Mechanical Stability
In addition to electrical considerations, drilled holes contribute to the mechanical stability of the PCB. They provide anchor points for mounting the board to enclosures or other mechanical structures. Accurate drilling ensures proper alignment and secure attachment.
PCB Drilling Methods
There are several methods used for drilling PCBs, each with its own advantages and limitations. Let’s explore the most common drilling methods:
Mechanical Drilling
Mechanical drilling is the most traditional and widely used method for PCB drilling. It involves using high-speed drill bits, typically made of carbide or diamond-coated materials, to create holes in the board. The drill bits are mounted on a computer-controlled drilling machine that precisely positions and rotates the bits to create the desired hole pattern.
Advantages of mechanical drilling include:
– Versatility: It can drill a wide range of hole sizes and materials.
– Speed: Modern drilling machines can drill thousands of holes per minute.
– Cost-effectiveness: Mechanical drilling is relatively inexpensive compared to other methods.
Limitations of mechanical drilling include:
– Wear and tear: Drill bits are subject to wear and need regular replacement.
– Minimum hole size: Mechanical drilling is limited by the smallest available drill bit size.
Laser Drilling
Laser drilling is a non-contact method that uses high-powered lasers to create holes in the PCB. The laser beam vaporizes the material, creating precise and small-diameter holes. Laser drilling is particularly useful for creating micro-vias, which are tiny holes used for high-density interconnects.
Advantages of laser drilling include:
– Precision: Laser drilling can create extremely small and accurate holes.
– No wear and tear: Since there is no physical contact, laser drilling eliminates tool wear.
– Flexibility: Laser drilling can create holes in various shapes and patterns.
Limitations of laser drilling include:
– Higher cost: Laser drilling equipment is more expensive than mechanical drilling machines.
– Material limitations: Some materials may not be suitable for laser drilling due to their thermal properties.
Punching
Punching is a method used for creating larger holes or irregular shapes in PCBs. It involves using a punch and die set to cut through the board material. Punching is often used for creating mounting holes or cutouts for connectors.
Advantages of punching include:
– Speed: Punching can create holes quickly, especially for larger sizes.
– Consistency: Punching produces consistent hole shapes and sizes.
Limitations of punching include:
– Limited hole sizes: Punching is not suitable for creating small holes.
– Tooling costs: Custom punch and die sets can be expensive.
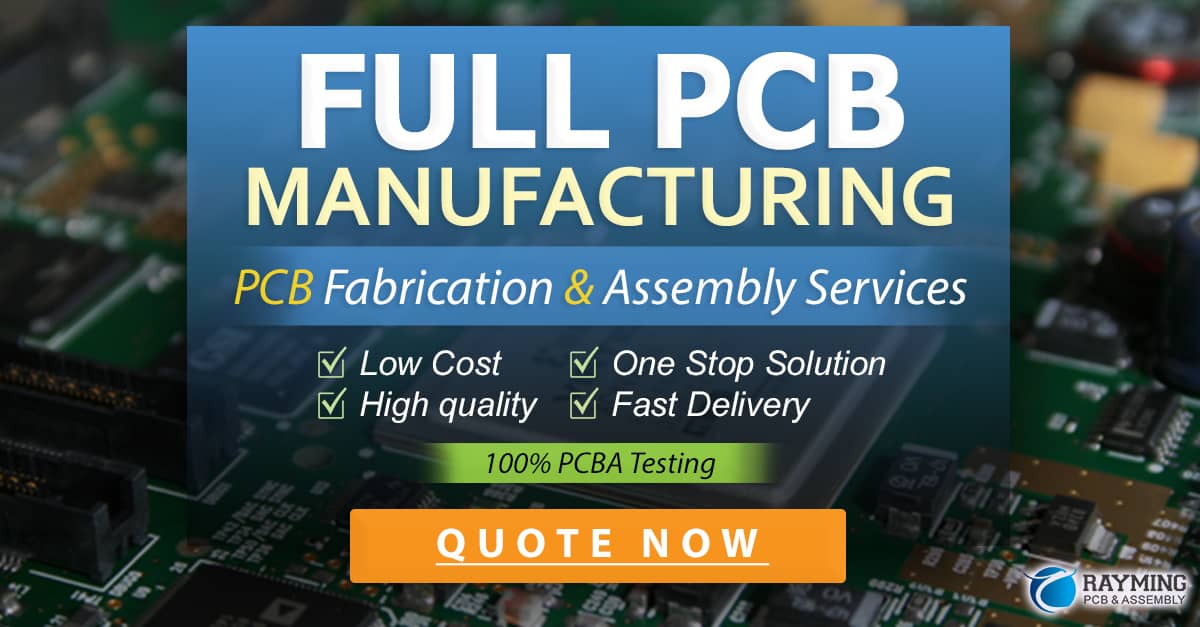
Challenges in PCB Drilling
While PCB drilling is a well-established process, it comes with its own set of challenges. Let’s discuss some common challenges encountered during PCB drilling:
Hole Size and Aspect Ratio
As electronic devices become smaller and more complex, the demand for smaller hole sizes and higher aspect ratios (the ratio of hole depth to diameter) increases. Drilling small holes with high aspect ratios poses challenges in terms of accuracy, drill bit stability, and material removal.
To overcome these challenges, manufacturers employ specialized drill bits, such as multi-fluted bits or stepped bits, which provide better hole quality and reduce the risk of drill breakage. Additionally, advanced drilling machines with high-speed spindles and precise depth control are used to achieve the desired hole dimensions.
Material Compatibility
PCBs can be made from various materials, each with its own drilling characteristics. Some materials, such as high-density interconnect (HDI) substrates or ceramic-based boards, can be more challenging to drill due to their hardness or abrasive properties.
To address material compatibility issues, manufacturers select appropriate drill bits and adjust drilling parameters, such as spindle speed, feed rate, and coolant flow, based on the specific material being drilled. Special coatings, such as diamond-like carbon (DLC) or polycrystalline diamond (PCD), can be applied to drill bits to enhance their durability and performance when drilling challenging materials.
Hole Positioning Accuracy
Accurate hole positioning is critical for ensuring proper component placement and alignment. Even slight deviations in hole position can lead to assembly issues or performance problems.
To achieve high hole positioning accuracy, manufacturers use Computer-Aided Manufacturing (CAM) software to generate precise drilling programs. These programs control the movement of the drilling machine, ensuring that holes are drilled at the exact locations specified in the PCB design.
Additionally, advanced drilling machines incorporate high-resolution encoders and servo motors to provide precise positioning control. Vision systems or alignment marks on the PCB can also be used to verify and adjust the drilling position in real-time.
Minimizing Drill Breakage and Wear
Drill breakage and excessive wear are common challenges in PCB drilling. Broken drill bits can cause damage to the PCB, lead to production delays, and increase manufacturing costs.
To minimize drill breakage and wear, manufacturers implement several strategies:
– Proper drill bit selection: Choosing the right drill bit material, geometry, and coating based on the PCB material and hole requirements.
– Optimized drilling parameters: Setting appropriate spindle speeds, feed rates, and peck drilling cycles to reduce stress on the drill bits.
– Regular maintenance: Inspecting and replacing drill bits at regular intervals to ensure optimal performance.
– Coolant management: Using effective coolant systems to lubricate and cool the drill bits, reducing friction and heat generation.
Best Practices for PCB Drilling
To ensure high-quality and efficient PCB drilling, manufacturers follow certain best practices. Here are some key guidelines:
Drill Bit Selection
Selecting the right drill bit is crucial for achieving accurate and reliable drilling results. Factors to consider when choosing drill bits include:
– Material: Carbide bits are commonly used for general-purpose drilling, while diamond-coated bits are preferred for harder materials.
– Geometry: The drill bit geometry, such as the flute design and point angle, should be optimized for the specific material and hole requirements.
– Coating: Coatings, such as TiN or TiAlN, can enhance the wear resistance and lubricity of the drill bits.
Drilling Parameters Optimization
Optimizing drilling parameters is essential for achieving the desired hole quality and minimizing drill wear. Key parameters to consider include:
– Spindle speed: The rotational speed of the drill bit, measured in revolutions per minute (RPM). Higher speeds are typically used for smaller hole sizes.
– Feed rate: The speed at which the drill bit advances into the material, measured in inches per minute (IPM). Feed rates should be adjusted based on the material and hole size.
– Peck drilling: A technique where the drill bit is periodically retracted to clear chips and reduce heat buildup. Peck drilling is particularly useful for drilling deep holes or challenging materials.
Manufacturers often conduct drilling tests and analyze the results to determine the optimal drilling parameters for a given PCB design and material.
Drilling Sequence Optimization
Optimizing the drilling sequence can significantly impact the efficiency and quality of the drilling process. Some best practices include:
– Grouping similar hole sizes: Drilling holes of similar sizes together reduces tool changeover time and improves drilling consistency.
– Minimizing drill path: Planning the drilling sequence to minimize the distance traveled by the drill bit, reducing cycle time and wear.
– Avoiding critical areas: Prioritizing the drilling of less critical areas first, allowing for any potential issues to be identified and addressed before drilling critical regions.
Advanced CAM software can automatically generate optimized drilling sequences based on the PCB design and user-defined criteria.
Quality Control and Inspection
Implementing robust quality control and inspection procedures is essential to ensure the accuracy and reliability of drilled holes. Some common practices include:
– Visual inspection: Visually examining drilled holes for any visible defects, such as burrs, breakouts, or misalignment.
– Automated optical inspection (AOI): Using computer vision systems to automatically detect and measure hole dimensions and positions.
– Electrical testing: Performing continuity and insulation resistance tests to verify the electrical integrity of the drilled holes.
– Cross-sectioning: Cutting through a sample of drilled holes to examine the hole wall quality and plating uniformity.
Regular quality control checks help identify any issues early in the manufacturing process, allowing for timely corrective actions.
Frequently Asked Questions (FAQ)
- What is the smallest hole size that can be drilled in a PCB?
-
The smallest hole size achievable depends on the drilling method and the capabilities of the drilling equipment. With mechanical drilling, hole sizes as small as 0.1mm (4 mil) can be consistently drilled. Laser drilling can achieve even smaller hole sizes, down to a few microns.
-
How do I choose the right drill bit for my PCB material?
-
When selecting a drill bit, consider factors such as the PCB material hardness, the desired hole size, and the required hole quality. Carbide drill bits are suitable for most common PCB materials, while diamond-coated bits are recommended for harder materials like ceramics or glass-reinforced substrates. Consult with your drill bit supplier or PCB Manufacturer for specific recommendations.
-
What is the difference between through-hole and blind-hole drilling?
-
Through-hole drilling creates holes that pass completely through the PCB, allowing components to be mounted on both sides of the board. Blind-hole drilling, on the other hand, creates holes that start from one surface of the PCB but do not pass through to the other side. Blind holes are commonly used for creating vias in multi-layer PCBs.
-
How often should I replace my drill bits?
-
The frequency of drill bit replacement depends on factors such as the material being drilled, the hole size, and the drilling parameters. As a general guideline, drill bits should be inspected regularly for wear and replaced when they show signs of dulling, chipping, or excessive wear. Most manufacturers establish drill bit replacement schedules based on the specific production requirements and historical data.
-
Can I drill holes in a PCB Prototype using a handheld drill?
- While it is possible to drill holes in a PCB prototype using a handheld drill, it is not recommended for achieving accurate and consistent results. Handheld drilling lacks the precision and control of dedicated PCB drilling machines. For prototyping purposes, it is better to use a small benchtop drill press or outsource the drilling to a PCB Prototyping service provider.
Conclusion
PCB drilling is a critical step in the manufacturing process, directly impacting the quality, reliability, and functionality of the final product. Understanding the importance of drilling, the various methods available, and the challenges involved is essential for designers, engineers, and manufacturers.
By selecting the right drilling methods, optimizing drilling parameters, and following best practices, manufacturers can achieve high-quality drilled holes while maximizing efficiency and minimizing costs. Continuous advancements in drilling technology, such as high-speed drilling machines, precise motion control systems, and intelligent software tools, are enabling the production of increasingly complex and high-density PCBs.
As the electronics industry continues to evolve, with the growing demand for miniaturization and high-performance devices, PCB drilling will remain a vital aspect of PCB manufacturing. Staying updated with the latest drilling techniques, materials, and best practices will be key to meeting the ever-changing requirements of modern electronics.
Drilling Method | Advantages | Limitations |
---|---|---|
Mechanical | – Versatility | – Wear and tear on drill bits |
– Speed | – Limited minimum hole size | |
– Cost-effectiveness | ||
Laser | – Precision | – Higher equipment costs |
– No wear and tear | – Material limitations | |
– Flexibility in hole shapes | ||
Punching | – Speed for larger holes | – Not suitable for small holes |
– Consistency in hole shapes and sizes | – Higher tooling costs for custom punch/die sets |
In conclusion, PCB drilling is a vital process that requires careful consideration and execution. By understanding the drilling methods, challenges, and best practices, manufacturers can optimize their drilling operations to produce high-quality PCBs that meet the demanding requirements of modern electronics.
0 Comments