Introduction
DownStream Technologies, a leading provider of PCB post-processing solutions, has recently announced significant updates to its suite of CAM and engineering software products. The latest releases offer enhanced support for flex, rigid-flex, and embedded component designs, addressing the growing demand for advanced PCB technologies in various industries.
The company’s flagship products, including CAM350, BluePrint-PCB, and DFMStream, have been upgraded with new features and capabilities that streamline the design and manufacturing processes for complex PCB designs. These improvements aim to help PCB designers and manufacturers tackle the challenges associated with flex, rigid-flex, and embedded component designs, ultimately reducing time-to-market and improving product quality.
Flex and Rigid-Flex Design Support
Enhanced Layer Stackup Definition
One of the key enhancements in DownStream Technologies’ software updates is the improved layer stackup definition for flex and rigid-flex designs. The new releases offer a more intuitive and flexible approach to defining layer stackups, allowing users to easily create and manage complex stackups with multiple materials and thicknesses.
The updated layer stackup interface provides a visual representation of the board structure, enabling users to quickly identify and modify layer properties, materials, and thicknesses. This feature ensures that the designed stackup accurately reflects the intended manufacturing process, reducing the risk of errors and inconsistencies.
Improved Bend Area Management
Flex and rigid-flex designs often involve intricate bend areas that require special attention during the design and manufacturing stages. DownStream Technologies has introduced advanced tools for managing bend areas in their software products, making it easier for designers to create and optimize these critical regions.
The new releases include features such as automatic bend area detection, bend radius validation, and bend area annotation. These tools help designers ensure that bend areas are properly defined and meet the manufacturing requirements, minimizing the risk of mechanical stress and failures in the final product.
Comprehensive Design Rule Checks (DRC)
To further support flex and rigid-flex designs, DownStream Technologies has expanded its Design Rule Check (DRC) capabilities. The updated DRC engine now includes a comprehensive set of rules specifically tailored for flex and rigid-flex designs, ensuring that designs comply with industry standards and manufacturing constraints.
The enhanced DRC checks cover various aspects of flex and rigid-flex design, including minimum bend radius, copper balance, tear-drop placement, and more. By running these checks early in the design process, users can identify and resolve potential issues before they impact manufacturing, saving time and reducing costs.
Embedded Component Design Support
Automated Cavity Creation
Embedded component designs involve placing components within the layers of the PCB, offering benefits such as reduced board size, improved signal integrity, and enhanced thermal management. DownStream Technologies’ software updates introduce automated cavity creation tools that simplify the process of designing embedded component structures.
The new cavity creation feature allows users to define the size, shape, and location of cavities based on the embedded component requirements. The software automatically generates the necessary cutouts and clearances in the surrounding layers, ensuring proper fit and isolation of the embedded components.
Intelligent Component Placement
In addition to automated cavity creation, DownStream Technologies has enhanced its component placement capabilities to support embedded component designs. The updated software includes intelligent algorithms that optimize the placement of embedded components, considering factors such as signal routing, thermal dissipation, and manufacturing constraints.
The intelligent placement tools analyze the design and suggest optimal locations for embedded components, minimizing the impact on signal integrity and manufacturability. Users can fine-tune the placement results based on their specific requirements, ensuring the best possible performance and reliability of the embedded component design.
3D Visualization and Analysis
To provide designers with a comprehensive understanding of embedded component designs, DownStream Technologies has integrated advanced 3D visualization and analysis capabilities into its software products. The new releases allow users to generate detailed 3D models of the PCB, including embedded components and cavities.
The 3D visualization features enable users to inspect the design from various angles, identify potential clearance issues, and verify the proper placement of embedded components. Additionally, the software offers thermal analysis tools that simulate the heat distribution within the embedded component structure, helping designers optimize thermal management strategies.
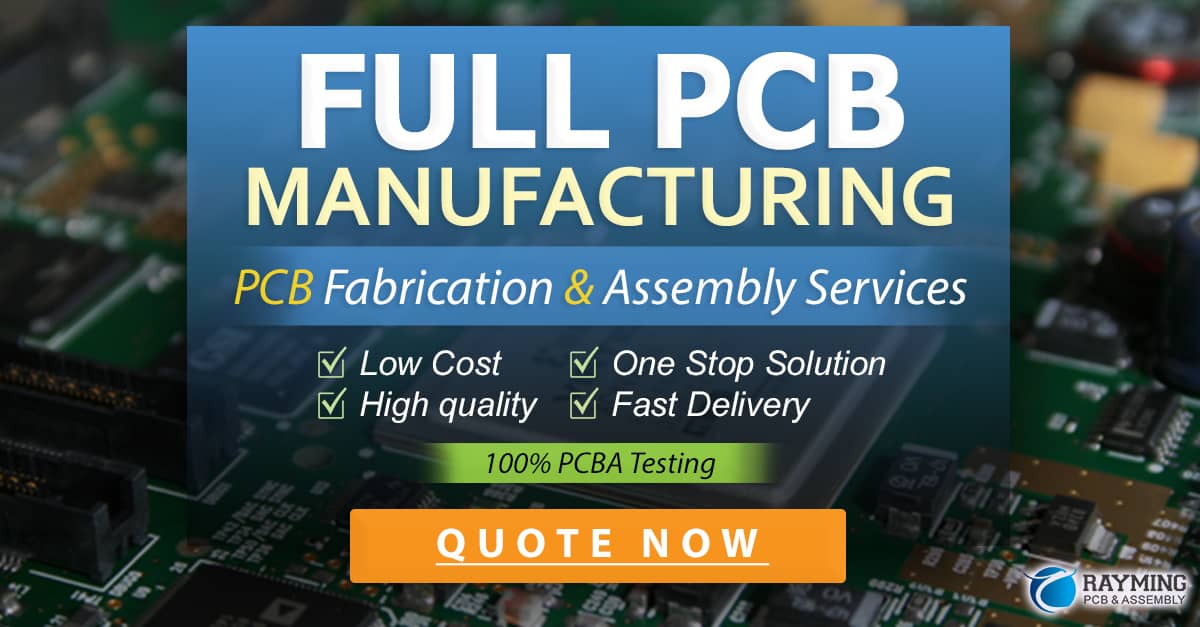
Collaborative Design Environment
Multi-User Project Management
DownStream Technologies recognizes the importance of collaboration in the PCB design process, especially when dealing with complex flex, rigid-flex, and embedded component designs. The latest software releases introduce enhanced multi-user project management capabilities that facilitate seamless collaboration among design teams.
The new project management features allow multiple users to work on the same design simultaneously, with real-time synchronization and conflict resolution. This collaborative environment streamlines the design process, ensures data consistency, and enables faster iterations and decision-making.
Revisions and Change Management
To further support collaborative design, DownStream Technologies has strengthened its revisions and change management capabilities. The updated software provides a robust version control system that tracks design changes, maintains a complete history of revisions, and allows users to easily compare and merge different versions of the design.
The enhanced change management features enable design teams to efficiently handle design modifications, track the impact of changes across the project, and ensure that all stakeholders are working with the latest and most accurate design data.
Integration and Automation
Seamless CAD/CAM Integration
DownStream Technologies’ software products are designed to seamlessly integrate with popular CAD/CAM tools, enabling a smooth transition from design to manufacturing. The latest releases further strengthen this integration, offering improved data exchange and synchronization capabilities.
The enhanced CAD/CAM integration allows users to easily import design data from various CAD formats, perform necessary post-processing tasks, and generate manufacturing-ready outputs. This seamless integration reduces manual effort, minimizes the risk of errors, and accelerates the overall design-to-manufacturing cycle.
Automated Manufacturing Outputs
To streamline the manufacturing process, DownStream Technologies has expanded its automated manufacturing output capabilities. The updated software can generate a wide range of manufacturing outputs, including Gerber files, drill files, pick-and-place data, and assembly drawings, with minimal manual intervention.
The automated output generation ensures consistent and accurate data transfer to manufacturing, reducing the chances of misinterpretation or errors. Additionally, the software offers customizable output templates and naming conventions, allowing users to align the outputs with their specific manufacturing requirements and preferences.
FAQ
1. What are the key benefits of using DownStream Technologies’ software for flex and rigid-flex designs?
DownStream Technologies’ software offers several key benefits for flex and rigid-flex designs:
- Enhanced layer stackup definition for managing complex stackups with multiple materials and thicknesses
- Improved bend area management tools for creating and optimizing critical bend regions
- Comprehensive Design Rule Checks (DRC) specifically tailored for flex and rigid-flex designs
- 3D visualization and analysis capabilities for verifying design integrity and manufacturability
2. How does DownStream Technologies’ software support embedded component designs?
DownStream Technologies’ software supports embedded component designs through the following features:
- Automated cavity creation tools for generating necessary cutouts and clearances for embedded components
- Intelligent component placement algorithms that optimize the location of embedded components
- 3D visualization and thermal analysis tools for evaluating the performance and reliability of embedded component structures
3. What collaboration features are available in the latest releases of DownStream Technologies’ software?
The latest releases of DownStream Technologies’ software offer the following collaboration features:
- Multi-user project management capabilities for simultaneous design work and real-time synchronization
- Revisions and change management tools for tracking design changes and maintaining version control
- Seamless integration with popular CAD/CAM tools for efficient data exchange and collaboration
4. How can DownStream Technologies’ software help streamline the manufacturing process?
DownStream Technologies’ software streamlines the manufacturing process through:
- Seamless CAD/CAM integration for smooth data transfer from design to manufacturing
- Automated generation of manufacturing outputs, such as Gerber files, drill files, and assembly drawings
- Customizable output templates and naming conventions for aligning with specific manufacturing requirements
5. What industries can benefit from using DownStream Technologies’ software for their PCB designs?
DownStream Technologies’ software is suitable for various industries that require advanced PCB technologies, such as:
- Aerospace and defense
- Automotive
- Medical devices
- Consumer electronics
- Telecommunications
- Industrial automation
The enhanced support for flex, rigid-flex, and embedded component designs makes DownStream Technologies’ software particularly valuable for industries that demand miniaturization, high performance, and reliability in their PCB designs.
Conclusion
DownStream Technologies’ latest software releases demonstrate the company’s commitment to providing cutting-edge solutions for the evolving challenges in PCB design and manufacturing. With enhanced support for flex, rigid-flex, and embedded component designs, DownStream Technologies empowers its users to tackle complex design requirements and deliver high-quality products to market faster.
The new features and capabilities introduced in CAM350, BluePrint-PCB, and DFMStream, such as improved layer stackup definition, automated cavity creation, and comprehensive DRC checks, streamline the design process and ensure manufacturability. The collaborative design environment and seamless CAD/CAM integration further enhance the efficiency and accuracy of the PCB design workflow.
As the demand for advanced PCB technologies continues to grow across various industries, DownStream Technologies remains at the forefront of innovation, offering powerful and reliable software solutions that meet the evolving needs of PCB designers and manufacturers. With these latest releases, the company reinforces its position as a trusted partner in the PCB industry, helping its customers stay competitive and succeed in the rapidly changing market landscape.
Feature | Benefit |
---|---|
Enhanced Layer Stackup Definition | Easily create and manage complex stackups with multiple materials and thicknesses |
Improved Bend Area Management | Ensure proper definition and optimization of critical bend regions |
Comprehensive Flex/Rigid-Flex DRC | Identify and resolve potential issues early in the design process |
Automated Cavity Creation | Simplify the process of designing embedded component structures |
Intelligent Component Placement | Optimize the placement of embedded components for best performance |
3D Visualization and Analysis | Inspect designs from various angles and verify proper placement of components |
Multi-User Project Management | Enable seamless collaboration among design teams |
Revisions and Change Management | Efficiently handle design modifications and track changes across the project |
Seamless CAD/CAM Integration | Reduce manual effort and accelerate the design-to-manufacturing cycle |
Automated Manufacturing Outputs | Ensure consistent and accurate data transfer to manufacturing |
0 Comments