Understanding PCB Safe Distance and Its Importance
When designing and manufacturing printed circuit boards (PCBs), it is crucial to consider the safe distance between various components, traces, and layers. This distance, known as the PCB safe distance, helps ensure the proper functioning, reliability, and longevity of the PCB. In this comprehensive article, we will delve into the details of PCB safe distance, its importance, and the factors that influence it.
What is PCB Safe Distance?
PCB safe distance refers to the minimum spacing required between different elements on a printed circuit board to prevent electrical interference, short circuits, and other issues that can compromise the integrity of the PCB. These elements include:
- Conductive traces
- Components (e.g., resistors, capacitors, integrated circuits)
- Vias and through-holes
- Copper planes
- Board edges
Maintaining proper safe distances between these elements is essential for ensuring the PCB functions as intended and meets the required standards for quality and reliability.
Why is PCB Safe Distance Important?
There are several reasons why adhering to PCB safe distance guidelines is crucial:
-
Signal Integrity: Proper spacing between traces and components helps minimize crosstalk, electromagnetic interference (EMI), and signal distortion, ensuring the signals remain clean and undistorted as they travel through the PCB.
-
Insulation and Isolation: Adequate safe distance prevents electrical shorts and leakage currents between adjacent traces or components, maintaining proper insulation and isolation.
-
Manufacturing Feasibility: Adhering to safe distance guidelines ensures that the PCB can be manufactured reliably and consistently, reducing the risk of defects and yield issues.
-
Compliance with Standards: Many industries have specific standards and regulations that dictate the minimum safe distances for PCBs, such as the IPC (Association Connecting Electronics Industries) standards. Complying with these standards is essential for ensuring the quality and reliability of the final product.
Factors Affecting PCB Safe Distance
Several factors influence the determination of appropriate safe distances in PCB Design:
1. Operating Voltage
The operating voltage of the PCB is one of the primary factors that determine the required safe distance. Higher voltages necessitate greater spacing between conductive elements to prevent arcing and ensure proper insulation. The table below provides a general guideline for minimum safe distances based on different voltage ranges:
Voltage Range | Minimum Safe Distance |
---|---|
< 50 V | 0.1 mm |
50 V – 100 V | 0.2 mm |
100 V – 150 V | 0.3 mm |
150 V – 300 V | 0.5 mm |
> 300 V | 1.0 mm |
It is important to note that these values are just a starting point, and the actual safe distance may vary depending on other factors such as the PCB material, environmental conditions, and applicable standards.
2. PCB Material and Thickness
The choice of PCB material and its thickness also play a role in determining the safe distance. Different materials have varying dielectric constants and breakdown voltages, which affect the insulation properties and the ability to withstand potential differences between conductive elements.
Some common PCB materials and their typical dielectric constants are:
- FR-4: 4.5
- Rogers 4003C: 3.38
- Polyimide: 3.5
- Alumina: 9.8
Thicker PCB materials generally provide better insulation and allow for smaller safe distances compared to thinner materials, assuming the same voltage rating.
3. Environmental Factors
The environment in which the PCB will operate can also influence the safe distance requirements. Factors such as temperature, humidity, and the presence of contaminants (e.g., dust, chemicals) can affect the insulation properties and the risk of electrical breakdown.
For example, in high-temperature environments, the insulation properties of the PCB material may degrade, necessitating larger safe distances. Similarly, in high-humidity environments, there is a greater risk of conductive particles or moisture bridging the gap between traces, leading to short circuits.
4. Applicable Standards and Regulations
Various industries have specific standards and regulations that dictate the minimum safe distances for PCBs. These standards take into account factors such as the operating voltage, PCB material, and environmental conditions to ensure the reliability and safety of the final product.
Some commonly used standards for PCB design include:
- IPC-2221: Generic Standard on Printed Board Design
- IPC-2222: Sectional Design Standard for Rigid Organic Printed Boards
- IPC-6012: Qualification and Performance Specification for Rigid Printed Boards
- UL 94: Standard for Safety of Flammability of Plastic Materials for Parts in Devices and Appliances
It is crucial to consult the relevant standards and regulations for your specific industry and application to ensure compliance and optimal PCB design.
Calculating PCB Safe Distance
Calculating the appropriate safe distance for a PCB involves considering the factors mentioned above and applying the relevant guidelines and formulas. While the exact calculation may vary depending on the specific standard or guideline being followed, here is a general approach to determining the minimum safe distance:
- Determine the maximum operating voltage of the PCB.
- Consider the PCB material and its dielectric constant.
- Take into account any environmental factors that may affect insulation properties.
- Consult the applicable standards and regulations for your industry and application.
- Use the provided formulas or tables in the relevant standard to calculate the minimum safe distance based on the above factors.
For example, IPC-2221 provides the following formula for calculating the minimum electrical conductor spacing:
D = V/500 + 0.005d
Where:
– D is the minimum electrical conductor spacing in mm
– V is the maximum operating voltage in volts
– d is the distance through the insulation in mm
It is important to note that this is just one example, and the actual calculation may differ depending on the specific standard and the factors involved.
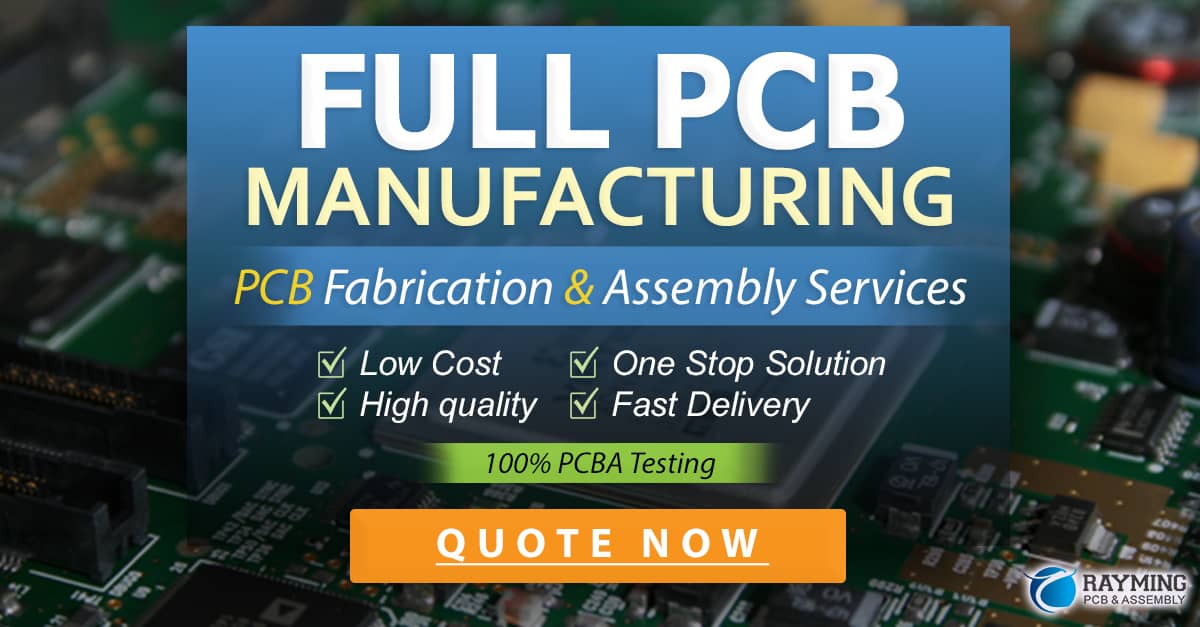
Best Practices for Ensuring Proper PCB Safe Distance
To ensure proper PCB safe distance and minimize the risk of issues related to spacing, consider the following best practices:
-
Consult applicable standards and guidelines: Always refer to the relevant industry standards and guidelines when designing your PCB to ensure compliance and optimal spacing.
-
Use PCB design software with built-in checks: Modern PCB design software often includes built-in Design Rule Checks (DRCs) that can help identify and flag any violations of safe distance guidelines, making it easier to catch and correct issues early in the design process.
-
Collaborate with your PCB Manufacturer: Work closely with your PCB manufacturer to ensure they are aware of your safe distance requirements and can provide guidance on manufacturability and best practices.
-
Consider the end-use environment: Take into account the expected operating environment of your PCB, including factors such as temperature, humidity, and potential contaminants, and adjust your safe distance calculations accordingly.
-
Allow for manufacturing tolerances: Keep in mind that there may be slight variations in the manufacturing process that can affect the final dimensions of your PCB. Allow for appropriate manufacturing tolerances when determining your safe distances to ensure the manufactured board meets your requirements.
Frequently Asked Questions (FAQ)
-
What happens if the safe distance between PCB elements is not maintained?
If the safe distance between PCB elements is not maintained, it can lead to various issues such as electrical shorts, signal integrity problems, electromagnetic interference, and even PCB failure. This can compromise the reliability and functionality of the final product. -
How do I determine the appropriate safe distance for my PCB?
To determine the appropriate safe distance for your PCB, consider factors such as the operating voltage, PCB material, environmental conditions, and applicable industry standards. Consult the relevant guidelines and standards for your specific application and use the provided formulas or tables to calculate the minimum safe distance. -
Can I use the same safe distance for all parts of my PCB?
No, the safe distance requirements may vary depending on the specific section of the PCB and the factors involved. For example, the safe distance between high-voltage traces may be different from the safe distance between low-voltage signals. It is important to consider the unique requirements of each section of your PCB. -
What role does the PCB material play in determining safe distance?
The PCB material and its properties, such as the dielectric constant and breakdown voltage, play a significant role in determining the safe distance. Materials with higher dielectric constants and breakdown voltages generally provide better insulation and may allow for smaller safe distances compared to materials with lower values. -
Are there any tools or software that can help me ensure proper PCB safe distance?
Yes, many modern PCB design software packages include built-in design rule checks (DRCs) that can help identify and flag any violations of safe distance guidelines. These tools can be valuable in catching and correcting spacing issues early in the design process. Additionally, working closely with your PCB manufacturer can provide further guidance and support in ensuring proper safe distances are maintained.
Conclusion
Maintaining proper PCB safe distance is crucial for ensuring the reliability, functionality, and compliance of your printed circuit board. By understanding the factors that influence safe distance, such as operating voltage, PCB material, environmental conditions, and applicable standards, you can make informed decisions when designing your PCB.
Remember to consult the relevant industry guidelines and standards, use PCB design software with built-in checks, collaborate with your PCB manufacturer, consider the end-use environment, and allow for manufacturing tolerances when determining your safe distances.
By following best practices and paying close attention to PCB safe distance requirements, you can minimize the risk of issues related to spacing and ensure the optimal performance and longevity of your PCB.
0 Comments