Introduction to Rogers 4003 PCB Material
Rogers 4003 is a high-performance printed circuit board (PCB) material known for its excellent electrical properties, low dielectric constant, and low dissipation factor. This material is widely used in high-frequency applications, such as wireless communications, aerospace, and defense industries. The unique properties of Rogers 4003 make it an ideal choice for designing and manufacturing PCBs that require superior signal integrity and reliability.
Composition and Properties of Rogers 4003
Rogers 4003 is a hydrocarbon ceramic laminate material composed of a woven glass reinforced hydrocarbon and ceramic filled thermoset plastic. The material has a dielectric constant (Dk) of 3.38 and a dissipation factor (Df) of 0.0027 at 10 GHz. These properties remain stable over a wide range of frequencies and temperatures, ensuring consistent performance in demanding applications.
Property | Value |
---|---|
Dielectric Constant (Dk) | 3.38 |
Dissipation Factor (Df) | 0.0027 |
Thermal Conductivity | 0.64 W/mK |
Coefficient of Thermal Expansion (CTE) | 11 ppm/°C |
Moisture Absorption | 0.06% |
PCB Manufacturing Process Using Rogers 4003
Material Preparation
The first step in manufacturing Rogers 4003 PCBs is to prepare the material. The Rogers 4003 laminate is cut to the desired size using a precision cutting machine. The copper foil is then laminated onto the Rogers 4003 substrate using heat and pressure. The lamination process ensures a strong bond between the copper and the substrate, minimizing the risk of delamination during the subsequent manufacturing steps.
Drilling and Plating
Once the material is prepared, the next step is to drill holes in the PCB for through-hole components and vias. High-speed CNC drilling machines are used to ensure precise and consistent hole sizes. After drilling, the holes are plated with copper to establish electrical connections between the layers of the PCB.
Patterning and Etching
The copper-clad Rogers 4003 laminate is then patterned using photolithography. A photoresist layer is applied to the copper surface and exposed to UV light through a photomask containing the desired circuit pattern. The exposed areas of the photoresist are then developed and removed, leaving the copper exposed in the desired pattern.
The exposed copper is etched away using a chemical etching process, typically involving an acidic solution such as ferric chloride or cupric chloride. The remaining photoresist is then stripped away, leaving the final copper circuit pattern on the Rogers 4003 substrate.
Solder Mask Application
A solder mask is applied to the PCB to protect the copper traces from oxidation and to prevent solder bridges during the assembly process. The solder mask is typically a green or blue color and is applied using screen printing or photoimaging techniques.
Surface Finish
The final step in the PCB manufacturing process is to apply a surface finish to the exposed copper areas, such as contact pads and component leads. Common surface finishes for Rogers 4003 PCBs include:
- Hot Air Solder Leveling (HASL)
- Electroless Nickel Immersion Gold (ENIG)
- Immersion Silver (IAg)
- Immersion Tin (ISn)
The choice of surface finish depends on the specific requirements of the application, such as solderability, durability, and cost.
Rogers 4003 PCB Assembly
Component Selection
When assembling Rogers 4003 PCBs, it is essential to select components that are compatible with the material and the high-frequency application. Factors to consider when choosing components include:
- Packaging: Surface mount (SMT) or through-hole (THT)
- Tolerance: Tighter tolerances may be required for high-frequency applications
- Power rating: Ensure components can handle the required power levels
- Frequency response: Components should perform well at the intended operating frequencies
Soldering Techniques
Soldering Rogers 4003 PCBs requires special consideration due to the material’s unique properties. The two primary soldering methods used are:
-
Reflow Soldering: This method is used for surface mount components. The PCB is screen printed with solder paste, and components are placed on the board using pick-and-place machines. The assembly is then heated in a reflow oven, melting the solder paste and forming a strong bond between the components and the PCB.
-
Wave Soldering: This method is used for through-hole components. The PCB is passed over a wave of molten solder, which flows through the plated holes and forms a strong bond between the component leads and the PCB.
When soldering Rogers 4003 PCBs, it is essential to control the temperature profile to prevent damage to the material and components. The recommended temperature profile for Rogers 4003 is shown below:
Reflow Phase | Temperature Range | Time |
---|---|---|
Preheat | 150°C – 200°C | 60-120 s |
Soak | 200°C – 250°C | 60-120 s |
Reflow | 250°C – 265°C | 30-60 s |
Cool Down | < 100°C | < 60 s |
Inspection and Testing
After assembly, Rogers 4003 PCBs should be thoroughly inspected and tested to ensure proper functionality and reliability. Common inspection and testing methods include:
- Visual inspection: Check for proper component placement, solder joint quality, and any visible defects
- Automated Optical Inspection (AOI): Uses cameras and image processing software to detect assembly defects
- X-ray inspection: Used to detect hidden defects, such as voids in solder joints or misaligned components
- In-Circuit Testing (ICT): Verifies the electrical connectivity and functionality of individual components and circuits
- Functional testing: Tests the overall performance of the assembled PCB under various operating conditions
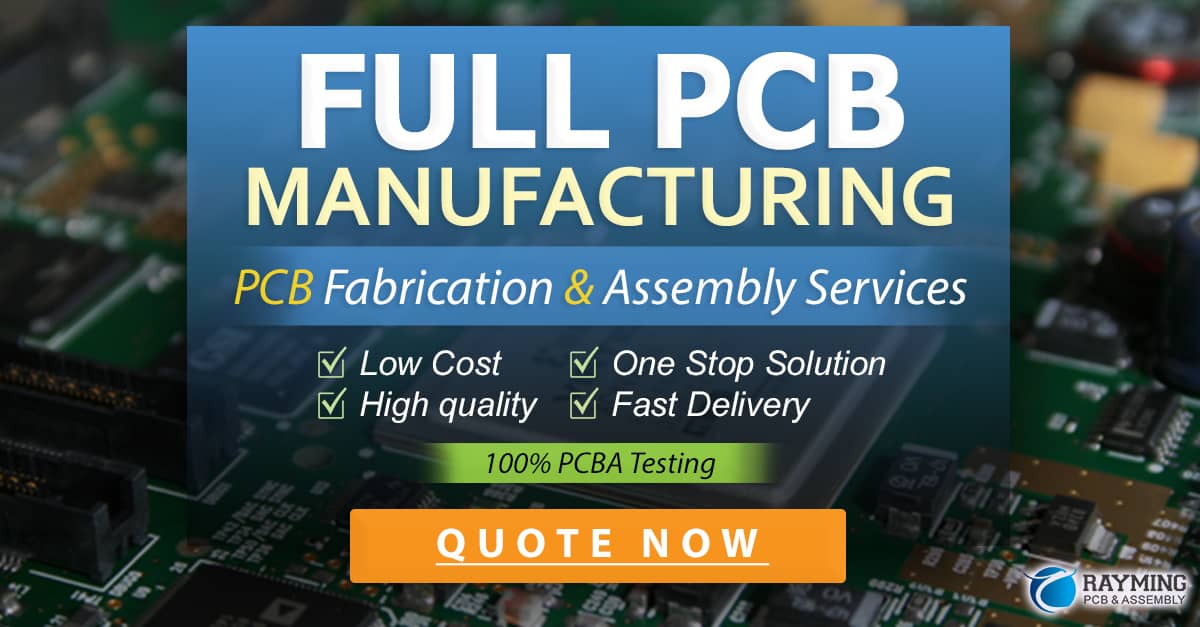
Applications of Rogers 4003 PCBs
Rogers 4003 PCBs are widely used in high-frequency applications due to their excellent electrical properties and reliability. Some common applications include:
- Wireless Communications:
- 5G networks
- Cellular base stations
- Satellite communications
-
Wi-Fi and Bluetooth devices
-
Aerospace and Defense:
- Radar systems
- Avionics
- Military communications equipment
-
Missile guidance systems
-
Automotive:
- Advanced Driver Assistance Systems (ADAS)
- Vehicle-to-vehicle (V2V) communication
- Vehicle-to-infrastructure (V2I) communication
-
Autonomous vehicles
-
Medical:
- High-frequency imaging systems
- Wireless medical devices
-
Implantable devices
-
Industrial:
- Industrial automation and control systems
- Wireless sensors and actuators
- High-speed data acquisition systems
Advantages of Using Rogers 4003 in PCB Manufacturing
-
Excellent electrical properties: Rogers 4003 has a low dielectric constant and low dissipation factor, which enables superior signal integrity and reduced signal loss at high frequencies.
-
Thermal stability: The material maintains its electrical properties over a wide range of temperatures, ensuring consistent performance in demanding environments.
-
Moisture resistance: Rogers 4003 has low moisture absorption, which minimizes the risk of delamination and other moisture-related failures.
-
Mechanical stability: The woven glass reinforcement provides excellent mechanical strength and dimensional stability, reducing the risk of warping or twisting during manufacturing and assembly.
-
Compatibility with standard PCB manufacturing processes: Rogers 4003 can be processed using standard PCB manufacturing equipment and techniques, making it a cost-effective solution for high-frequency applications.
Challenges and Considerations in Rogers 4003 PCB Manufacturing
-
Material cost: Rogers 4003 is more expensive than standard FR-4 PCB materials due to its unique properties and performance advantages.
-
Special processing requirements: Manufacturing Rogers 4003 PCBs may require specialized equipment and expertise, such as high-speed drilling machines and controlled impedance routing.
-
Design considerations: Designers must carefully consider factors such as trace width, spacing, and impedance matching to ensure optimal performance in high-frequency applications.
-
Assembly challenges: The unique properties of Rogers 4003 may require special soldering techniques and temperature profiles to ensure reliable assembly.
Conclusion
Rogers 4003 is a high-performance PCB material that offers excellent electrical properties, thermal stability, and mechanical strength for demanding high-frequency applications. By understanding the manufacturing process, assembly techniques, and design considerations involved in working with Rogers 4003, PCB manufacturers can create reliable and high-quality boards for a wide range of industries, including wireless communications, aerospace, defense, automotive, medical, and industrial applications.
Frequently Asked Questions (FAQ)
- What is the main difference between Rogers 4003 and standard FR-4 PCB materials?
-
Rogers 4003 has a lower dielectric constant and dissipation factor compared to FR-4, which makes it better suited for high-frequency applications. Rogers 4003 also offers better thermal and mechanical stability.
-
Can Rogers 4003 PCBs be manufactured using standard PCB production processes?
-
Yes, Rogers 4003 PCBs can be manufactured using standard PCB production processes, such as drilling, plating, and etching. However, some specialized equipment and expertise may be required to achieve optimal results.
-
What are the key considerations when designing Rogers 4003 PCBs for high-frequency applications?
-
Key considerations include trace width, spacing, impedance matching, and component selection. Designers must ensure that the PCB layout is optimized for the intended operating frequencies and that the components used are compatible with the Rogers 4003 material.
-
Are there any special soldering techniques required for assembling Rogers 4003 PCBs?
-
Yes, soldering Rogers 4003 PCBs may require special temperature profiles and techniques to prevent damage to the material and ensure reliable solder joints. Reflow soldering is typically used for surface mount components, while wave soldering is used for through-hole components.
-
What are some common applications for Rogers 4003 PCBs?
- Common applications for Rogers 4003 PCBs include wireless communications (5G, cellular, satellite), aerospace and defense (radar, avionics), automotive (ADAS, V2V, V2I), medical (imaging, wireless devices), and industrial (automation, sensors, high-speed data acquisition).
0 Comments