Introduction to DDR2 Memory and PCB Design
DDR2 (Double Data Rate 2) is a type of synchronous dynamic random-access memory (SDRAM) that has been widely used in computer systems since its introduction in 2003. DDR2 memory operates at higher speeds and lower voltages compared to its predecessor, DDR memory. When designing a printed circuit board (PCB) for DDR2 memory, signal integrity is a crucial factor to ensure reliable performance and data transfer.
In this article, we will explore the key aspects of DDR2 800 memory and discuss the best practices for PCB signal integrity design when working with DDR2. We will cover topics such as:
- DDR2 800 specifications and benefits
- Signal integrity challenges in DDR2 PCB design
- PCB layout considerations for DDR2
- Routing techniques for DDR2 signals
- Termination and impedance matching
- Power delivery and decoupling
- Testing and validation of DDR2 PCB designs
By understanding these concepts and applying the appropriate design techniques, engineers can create robust and reliable PCB designs that take full advantage of DDR2 800 memory performance.
DDR2 800 Specifications and Benefits
DDR2 800 memory operates at a clock frequency of 400 MHz, which translates to an effective data rate of 800 MT/s (megatransfers per second) due to its double data rate nature. This means that data is transferred on both the rising and falling edges of the clock signal, effectively doubling the data throughput compared to single data rate (SDR) memory.
Some key specifications of DDR2 800 memory include:
- Clock frequency: 400 MHz
- Data rate: 800 MT/s
- Voltage: 1.8V
- Prefetch architecture: 4n
- Burst length: 4 or 8
- On-die termination (ODT) support
Compared to its predecessor, DDR memory, DDR2 offers several benefits:
-
Higher data throughput: The increased clock frequency and data rate of DDR2 800 enable faster data transfer and improved system performance.
-
Lower power consumption: DDR2 operates at a lower voltage (1.8V) compared to DDR (2.5V), reducing power consumption and heat generation.
-
On-die termination (ODT): DDR2 memory modules include built-in termination resistors, simplifying PCB design and improving signal integrity.
-
Prefetch architecture: DDR2 employs a 4n prefetch architecture, which allows for more efficient data access and higher bandwidth.
Signal Integrity Challenges in DDR2 PCB Design
Designing a PCB for DDR2 memory presents several signal integrity challenges that must be addressed to ensure reliable performance. Some of these challenges include:
-
High-speed signals: DDR2 800 operates at high frequencies, making the PCB Traces more susceptible to signal integrity issues such as reflections, crosstalk, and attenuation.
-
Tight timing requirements: DDR2 memory has strict timing requirements for data transfer, necessitating careful control of signal propagation delays and skew.
-
Simultaneous switching noise (SSN): The simultaneous switching of multiple DDR2 signals can generate noise on power and ground planes, potentially causing signal integrity problems.
-
Impedance matching: Proper impedance matching is essential to minimize reflections and ensure clean signal transmission between the memory controller and DDR2 memory modules.
To mitigate these challenges, PCB designers must follow best practices and employ appropriate layout and routing techniques.
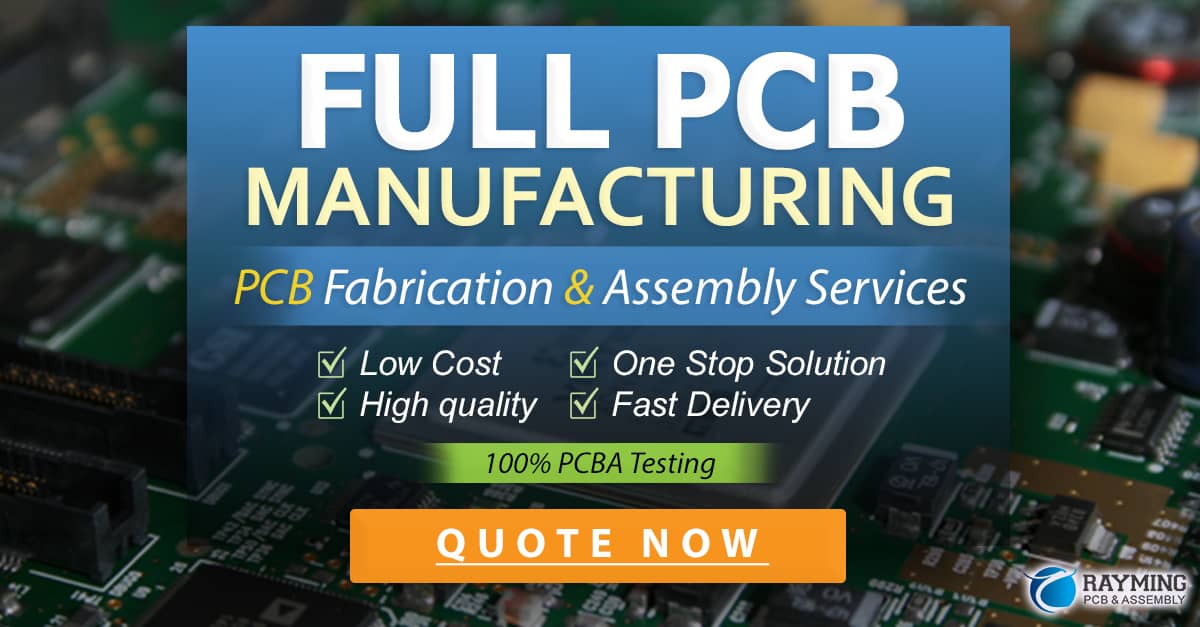
PCB Layout Considerations for DDR2
When laying out a PCB for DDR2 memory, several key considerations should be taken into account:
-
Component placement: Position the DDR2 memory modules as close to the memory controller as possible to minimize trace lengths and signal propagation delays. Ensure that the placement allows for proper routing and meets the required clearances.
-
Layer stackup: Use a multi-layer PCB Stackup with dedicated signal, power, and ground layers. Typically, a 6-layer or 8-layer stackup is recommended for DDR2 PCB designs. The signal layers should be adjacent to reference planes (power or ground) to maintain controlled impedance and minimize crosstalk.
-
Power and ground planes: Provide solid power and ground planes to minimize impedance and ensure a low-impedance return path for high-speed signals. Use separate power planes for the DDR2 memory and other components to minimize noise coupling.
-
Decoupling Capacitors: Place decoupling capacitors close to the DDR2 memory modules and the memory controller to provide a stable power supply and minimize simultaneous switching noise. Use a combination of bulk and ceramic capacitors with different values to target various frequency ranges.
Routing Techniques for DDR2 Signals
Proper routing techniques are essential to maintain signal integrity in DDR2 PCB designs. Some key routing guidelines include:
-
Trace length matching: Match the lengths of the data, address, and control signals within a byte lane to minimize skew. The maximum length difference should be within the specified tolerance, typically less than 0.025 inches (0.635 mm).
-
Differential pair routing: Route differential signals, such as DQS (data strobe) and DQSn, as tightly coupled differential pairs. Maintain a constant spacing between the traces and avoid discontinuities to minimize impedance variations.
-
Trace width and spacing: Use appropriate trace widths and spacing to achieve the target impedance, typically 50 ohms for single-ended signals and 100 ohms for differential pairs. Consult the PCB Manufacturer’s guidelines and use impedance calculators to determine the optimal trace geometry.
-
Via optimization: Minimize the number of vias on DDR2 signal traces to reduce discontinuities and reflections. When vias are necessary, use microvias or blind/Buried Vias to minimize stub lengths.
-
Crosstalk mitigation: Implement crosstalk mitigation techniques, such as trace shielding, guard traces, or ground plane cutouts, to minimize coupling between adjacent signals.
Termination and Impedance Matching
Proper termination and impedance matching are crucial for maintaining signal integrity in DDR2 PCB designs. DDR2 memory modules incorporate on-die termination (ODT) resistors, which help to minimize reflections and improve signal quality.
When designing the PCB, consider the following termination and impedance matching guidelines:
-
ODT configuration: Configure the ODT settings in the memory controller and the DDR2 memory modules according to the manufacturer’s recommendations. The ODT values should be selected based on the system’s impedance requirements and the number of memory modules in the system.
-
Trace impedance: Ensure that the PCB traces are designed to match the target impedance, typically 50 ohms for single-ended signals and 100 ohms for differential pairs. Use controlled impedance techniques, such as stripline or microstrip, to maintain a consistent impedance along the trace length.
-
Termination components: If additional termination components, such as resistors or capacitors, are required, place them close to the source or destination of the signal to minimize reflections. Follow the manufacturer’s guidelines for component selection and placement.
Power Delivery and Decoupling
Proper power delivery and decoupling are essential for maintaining signal integrity and ensuring reliable operation of DDR2 memory. Consider the following guidelines:
-
Power plane design: Use dedicated power planes for the DDR2 memory and the memory controller. Ensure that the power planes have sufficient copper coverage and are properly connected to the power supply. Avoid splitting the power planes, as this can introduce impedance discontinuities.
-
Decoupling capacitors: Place decoupling capacitors close to the DDR2 memory modules and the memory controller to minimize power supply noise and provide a stable voltage reference. Use a combination of bulk and ceramic capacitors with different values to target various frequency ranges.
-
Power sequencing: Implement proper power sequencing to ensure that the DDR2 memory and the memory controller are powered up in the correct order. Follow the manufacturer’s guidelines for power sequencing requirements.
Testing and Validation of DDR2 PCB Designs
To ensure the reliability and performance of a DDR2 PCB design, thorough testing and validation should be conducted. Some key testing and validation steps include:
-
Signal integrity simulations: Perform pre-layout and post-layout signal integrity simulations to analyze the DDR2 signals’ behavior and identify potential issues. Use simulation tools to assess signal quality, timing, and crosstalk.
-
Prototype testing: Fabricate prototype PCBs and conduct comprehensive testing to validate the design. Perform functional tests, memory stress tests, and signal integrity measurements to ensure that the DDR2 memory and the PCB perform as expected.
-
Compliance testing: Verify that the DDR2 PCB design meets the relevant industry standards and specifications, such as JEDEC (Joint Electron Device Engineering Council) standards for DDR2 memory.
-
Thermal and power analysis: Conduct thermal and power analysis to ensure that the PCB and components operate within their specified temperature and power limits. Verify that the cooling solution is adequate and that the power delivery system meets the DDR2 memory’s requirements.
Conclusion
Designing a PCB for DDR2 800 memory requires careful consideration of signal integrity, power delivery, and layout techniques. By understanding the specifications and benefits of DDR2 memory, addressing signal integrity challenges, and following best practices for PCB layout, routing, termination, and decoupling, engineers can create robust and reliable designs that optimize DDR2 performance.
Thorough testing and validation, including signal integrity simulations, prototype testing, compliance testing, and thermal and power analysis, are essential to ensure the quality and reliability of the final product.
By adhering to these guidelines and staying up-to-date with industry standards and best practices, PCB designers can successfully implement DDR2 800 memory in their designs and achieve optimal system performance.
Frequently Asked Questions (FAQ)
-
What is the difference between DDR2 and DDR memory?
DDR2 memory operates at higher clock frequencies and data rates compared to DDR memory. DDR2 also has a lower operating voltage (1.8V vs. 2.5V), a 4n prefetch architecture, and on-die termination (ODT) support, which improves signal integrity and simplifies PCB design. -
What is the importance of signal integrity in DDR2 PCB design?
Signal integrity is crucial in DDR2 PCB design because DDR2 memory operates at high speeds and has tight timing requirements. Maintaining good signal integrity helps to ensure reliable data transfer, minimizes errors, and prevents system instability or failures. -
What are some key layout considerations for DDR2 PCB design?
Key layout considerations for DDR2 PCB design include component placement, layer stackup, power and ground plane design, and the proper use of decoupling capacitors. Placing the DDR2 memory close to the memory controller, using a multi-layer stackup with dedicated signal and reference layers, and strategically placing decoupling capacitors help to maintain signal integrity and ensure reliable performance. -
What is the purpose of on-die termination (ODT) in DDR2 memory?
On-die termination (ODT) in DDR2 memory helps to minimize signal reflections and improve signal quality. The ODT resistors are built into the DDR2 memory modules, which simplifies PCB design and reduces the need for external termination components. -
How can engineers ensure the reliability and performance of a DDR2 PCB design?
To ensure the reliability and performance of a DDR2 PCB design, engineers should conduct thorough testing and validation, including signal integrity simulations, prototype testing, compliance testing, and thermal and power analysis. Following industry standards and best practices for PCB layout, routing, termination, and power delivery is also essential for creating robust and reliable DDR2 PCB designs.
Parameter | DDR2 800 |
---|---|
Clock frequency | 400 MHz |
Data rate | 800 MT/s |
Voltage | 1.8V |
Prefetch architecture | 4n |
Burst length | 4 or 8 |
On-die termination (ODT) | Supported |
Table 1: Key specifications of DDR2 800 memory.
Component | Description |
---|---|
Bulk capacitors | Used for low-frequency decoupling, typically 1-10 µF |
Ceramic capacitors | Used for high-frequency decoupling, typically 0.01-0.1 µF |
Placement | Place decoupling capacitors close to the DDR2 memory modules and memory controller |
Table 2: Decoupling capacitor recommendations for DDR2 PCB design.
0 Comments