What is a Wire Harness?
A wire harness, also known as a cable harness or wiring loom, is an organized assembly of electrical cables or wires that transmit signals or electrical power throughout a vehicle, machine, or electronic device. The primary purpose of a wire harness is to simplify the wiring system by bundling and routing wires in a secure, efficient, and organized manner. Wire harnesses are essential components in various industries, including automotive, aerospace, medical equipment, telecommunications, and consumer electronics.
Components of a Wire Harness
A typical wire harness consists of several components, including:
- Wires: The main component of a wire harness, wires are chosen based on their gauge (thickness), material (copper, aluminum, etc.), and insulation properties.
- Connectors: Used to join wires to other components or harnesses, connectors ensure secure and reliable electrical connections.
- Terminals: Crimped or soldered onto the ends of wires, terminals provide a means to connect wires to connectors or other components.
- Splice joints: Used to join two or more wires together, splice joints are typically sealed with heat shrink tubing or adhesive-lined tubing to protect against environmental factors.
- Protective coverings: Harnesses are often wrapped in materials such as tape, conduit, or braided sleeving to provide additional protection against abrasion, heat, or moisture.
The Importance of Custom Wire Harnesses
Custom wire harnesses are designed and manufactured to meet the specific requirements of a particular application or product. By tailoring the wire harness to the unique needs of a system, manufacturers can ensure optimal performance, reliability, and safety. Some key benefits of custom wire harnesses include:
- Simplified installation: Custom wire harnesses are designed to fit perfectly within the designated space, making installation quicker and more efficient.
- Reduced maintenance: Well-designed custom wire harnesses minimize the risk of electrical failures and simplify troubleshooting when issues arise.
- Improved reliability: By using high-quality materials and adhering to strict manufacturing standards, custom wire harnesses offer enhanced durability and performance in demanding environments.
- Cost-effectiveness: Custom wire harnesses streamline the assembly process and reduce the need for additional components, ultimately lowering production costs.
The Wire Harness Manufacturing Process
The production of custom wire harnesses involves several key steps:
1. Design and Engineering
The first step in creating a custom wire harness is to develop a detailed design based on the customer’s specifications and requirements. This process involves:
- Reviewing the application’s electrical schematics and wiring diagrams
- Selecting appropriate wires, connectors, and other components
- Determining the optimal routing and layout of the wire harness
- Creating detailed CAD drawings or 3D models of the wire harness
2. Prototype Development and Testing
Once the design is finalized, a prototype wire harness is produced for testing and validation. This step allows manufacturers to:
- Verify the form, fit, and function of the wire harness
- Conduct rigorous testing to ensure the harness meets performance and safety requirements
- Make any necessary adjustments to the design before moving into full-scale production
3. Wire Cutting and Stripping
With the design validated, the wire harness manufacturing process begins with cutting wires to the required lengths and stripping the insulation from the ends. This step is typically performed using automated wire cutting and stripping machines to ensure precision and consistency.
4. Crimping and Soldering
Next, terminals are attached to the stripped ends of the wires using either crimping or soldering techniques. Crimping involves using a specialized tool to compress the terminal onto the wire, while soldering uses heat and a conductive material to bond the wire and terminal together.
5. Assembly and Routing
The prepared wires are then laid out and bundled according to the harness design, with wires being secured together using tape, cable ties, or other fastening methods. Connectors are attached to the appropriate wires, and any necessary labeling or marking is applied to facilitate installation and maintenance.
6. Testing and Quality Control
Before a wire harness is considered complete, it undergoes thorough testing and quality control procedures to ensure its electrical integrity and conformance to specifications. This may include:
- Continuity testing to verify proper connections between components
- Insulation resistance testing to check for potential shorts or leaks
- High-potential (hipot) testing to ensure the harness can withstand specified voltage levels without breakdown
- Visual inspections to check for any defects or inconsistencies
7. Packaging and Shipping
Once a wire harness has passed all quality control checks, it is packaged according to customer requirements and shipped to its destination. Proper packaging ensures the harness remains protected during transit and arrives ready for installation.
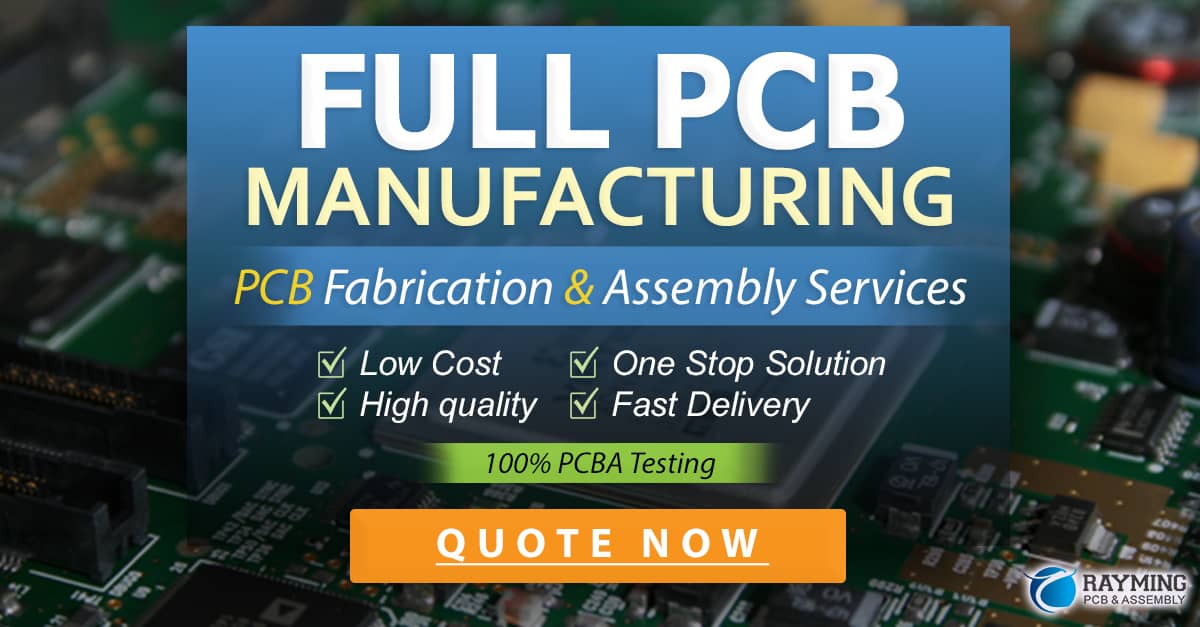
Choosing the Right Custom Wire Harness Manufacturer
When selecting a custom wire harness manufacturer, there are several key factors to consider:
- Experience and expertise: Look for a manufacturer with a proven track record of producing high-quality wire harnesses for applications similar to yours.
- Manufacturing capabilities: Ensure the manufacturer has the necessary equipment, facilities, and processes in place to meet your specific requirements.
- Quality control: Choose a manufacturer that adheres to strict quality control standards and has a robust testing and inspection process.
- Customer service: Select a manufacturer that is responsive, communicative, and willing to work closely with you to ensure your needs are met.
- Scalability: Consider a manufacturer’s ability to scale production to meet your current and future demand.
Common Applications for Custom Wire Harnesses
Custom wire harnesses are used in a wide range of industries and applications, including:
Automotive Industry
Wire harnesses are critical components in modern vehicles, connecting and powering various systems such as:
- Engine management systems
- Infotainment and navigation systems
- Lighting and signaling systems
- Safety and security systems
Aerospace Industry
In aircraft and spacecraft, custom wire harnesses ensure the reliable operation of:
- Flight control systems
- Avionics and communication systems
- Cabin management systems
- Propulsion systems
Medical Equipment
Custom wire harnesses are essential for the safe and effective functioning of medical devices, such as:
- Patient monitoring systems
- Diagnostic imaging equipment
- Surgical instruments
- Therapy delivery devices
Industrial Machinery
Wire harnesses play a vital role in connecting and controlling various components within industrial equipment, including:
- Robotics and automation systems
- Material handling equipment
- Packaging machinery
- Printing and labeling machines
Telecommunications
Custom wire harnesses are used extensively in telecommunications equipment to enable:
- Data transmission
- Signal processing
- Networking and routing
- Power distribution
Frequently Asked Questions (FAQ)
- What is the difference between a wire harness and a cable assembly?
-
A wire harness is a collection of wires, connectors, and terminals that are bundled together to transmit signals or power within a system. A cable assembly, on the other hand, typically consists of a single cable with connectors on either end, often used to connect two separate devices or systems.
-
Can custom wire harnesses be designed for harsh environments?
-
Yes, custom wire harnesses can be engineered to withstand harsh environmental conditions such as extreme temperatures, moisture, vibration, and chemical exposure. This is achieved through the use of specialized materials, protective coverings, and robust design techniques.
-
How long does it take to design and manufacture a custom wire harness?
-
The lead time for a custom wire harness depends on factors such as the complexity of the design, the availability of components, and the manufacturer’s production capacity. In general, the process can take anywhere from a few weeks to several months, with more complex harnesses requiring longer lead times.
-
What is the minimum order quantity for custom wire harnesses?
-
Minimum order quantities (MOQs) for custom wire harnesses vary among manufacturers and depend on factors such as the complexity of the harness and the required components. Some manufacturers may offer low MOQs for prototypes or small-scale production runs, while others may require larger quantities for cost-effective production.
-
How can I ensure the quality and reliability of my custom wire harnesses?
- To ensure the quality and reliability of your custom wire harnesses, partner with a reputable manufacturer that has a proven track record of producing high-quality harnesses. Look for manufacturers that adhere to strict quality control standards, employ rigorous testing procedures, and use premium materials and components in their manufacturing process.
Conclusion
Custom wire harnesses are essential components in a wide range of industries, providing organized, efficient, and reliable electrical connections within vehicles, machines, and electronic devices. By working with an experienced and reputable custom wire harness manufacturer, businesses can ensure their products are equipped with high-quality, purpose-built harnesses that meet their specific performance, reliability, and safety requirements.
When selecting a custom wire harness manufacturer, it is essential to consider factors such as experience, manufacturing capabilities, quality control, customer service, and scalability. By partnering with the right manufacturer, businesses can streamline their production processes, reduce costs, and deliver products that exceed customer expectations.
As technology continues to advance and the demand for more complex and reliable electrical systems grows, the importance of custom wire harnesses will only continue to increase. By staying at the forefront of wire harness design and manufacturing, businesses can position themselves for success in an ever-evolving market.
Industry | Application | Key Benefits of Custom Wire Harnesses |
---|---|---|
Automotive | Engine management systems | Optimized performance, increased reliability, simplified installation |
Aerospace | Flight control systems | Enhanced safety, reduced weight, improved maintainability |
Medical | Patient monitoring systems | Ensured patient safety, enhanced device functionality, simplified assembly |
Industrial | Robotics and automation | Improved efficiency, reduced downtime, enhanced system integration |
Telecommunications | Data transmission and signal processing | Optimal signal integrity, reduced interference, simplified maintenance |
0 Comments