Introduction
Printed circuit boards (PCBs) are essential components in nearly all electronic devices today. From computers and smartphones to industrial equipment and medical devices, PCBs provide the necessary electrical connections between various components. As products become more advanced, PCBs have also grown more complex, requiring specialized skills and equipment to manufacture. This has led many companies to outsource PCB assembly to contract manufacturers (CMs), allowing them to focus on their core competencies while leveraging the CM’s expertise in PCB fabrication and assembly.
This article provides a comprehensive overview of contract PCB assembly in 2023—exploring the key benefits, how to select the right CM, critical factors in the assembly process, costs and pricing, and more. With the insights from this guide, you’ll be well-equipped to successfully partner with a CM for your next PCB assembly project.
Benefits of Contract PCB Assembly
There are several compelling reasons to outsource PCB assembly to a contract manufacturer rather than keeping it in-house:
1. Focus on Core Competencies
For most companies, PCB assembly is not a core part of their business. Outsourcing it allows them to free up resources to focus on critical product development, marketing, and other priorities that drive growth. The CM handles all aspects of assembling PCBs efficiently.
2. Access Specialized Skills and Equipment
PCB assembly requires working with tiny electronics components and SMT equipment for accurately placing and soldering them onto boards. Keeping these skills and expensive equipment in-house is challenging. Contract manufacturers invest heavily in staying on the cutting edge.
3. Improve Quality and Yields
Given their scale and experience, contract manufacturers are adept at finding ways to optimize the PCB assembly process. This leads to improved quality, higher yields, and reduced costs over time.
4. Flexibility for Fluctuating Demand
A contract manufacturer can easily scale production up and down as the customer’s requirements change. The customer avoids investing in equipment and staff for peak capacity they won’t fully utilize.
5. Reduce Time to Market
Outsourcing PCB assembly parallelizes manufacturing with other development activities, helping products get to market faster. The CM’s expertise also reduces revisions and errors that can cause delays.
How to Select a Contract Manufacturer for PCB Assembly
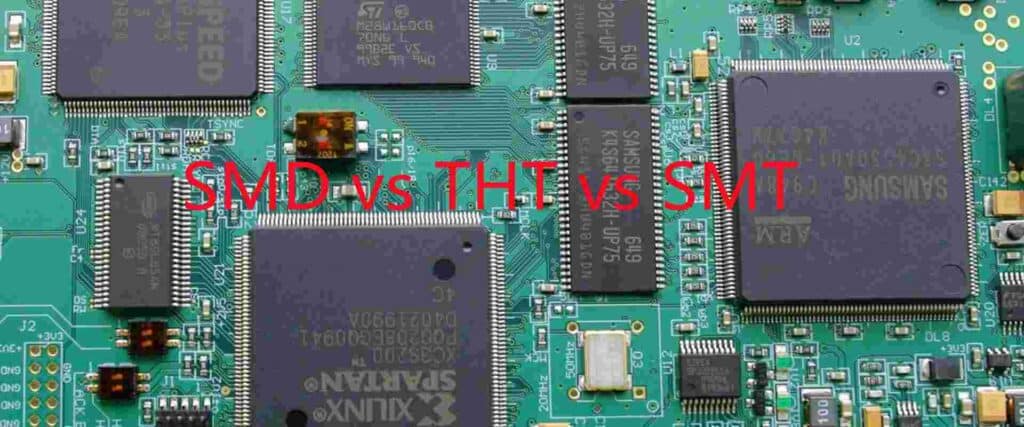
With the benefits clear, the next step is finding the right CM for your specific PCB assembly needs. Here are key factors to evaluate:
Technical Capabilities
- Services – Many CMs today provide turnkey services spanning design for manufacturing (DFM), prototyping, full production, and post-manufacturing support. Seek a partner offering this full spectrum.
- Quality certifications – Look for ISO-9001 and other certifications to ensure quality management.
- Equipment – Evaluate machinery for SMT, testing, inspection, etc. Leading edge equipment ensures high precision assembly.
- Engineering skills – The CM should have engineers to vet designs for manufacturability and optimize the assembly process.
- Miniaturization capabilities – With electronics shrinking, find a CM able to work with micro-scale components.
- Materials management – They should have robust processes for procuring and qualifying components.
Industry Experience
Seek CMs with expertise in your specific industry and product type. This focuses their knowledge and optimizes processes for your application.
Capacity Scalability
Look for flexible capacity from small prototyping runs through high volume production. Make sure they can location production globally.
Quality Systems
Robust quality systems and process controls are crucial for consistent, defect-free PCB assembly. Auditing these distinguishes strong CMs.
Pricing & Cost Reduction Methodology
Understand the pricing model – per component, per joint, etc. Also examine their approach to driving down costs over a product’s lifecycle.
Customer Service
From engineering collaboration to order management and post-delivery support, ensure the CM is easy to work with and responsive.
By thoroughly vetting CMs on these criteria, you can select the ideal partner for your PCB assembly needs.
Critical Factors in the PCB Assembly Process
Once you select a contract manufacturer, it’s important to understand the key factors that drive quality, yields, and costs during the assembly process:
Component Sourcing & Management
The bill of materials (BOM) largely defines the cost and availability of a PCB assembly. Work closely with your CM on component engineering to lower BOM costs and ensure available supply.
Design for Manufacturing
Perform DFM analysis before finalizing any design to avoid issues like insufficient spacing between components. This prevents costly re-spins later.
SMT Programming
Fine-tuning SMT machine programming for each board maximizes placement accuracy and efficiency. Different board geometries require different programs.
Solder Paste Printing
This process deposits the solder paste onto PCB pads where components will be placed. Ensuring the proper amount is dispensed is essential for solder joint quality.
Component Placement
High precision component placement is critical, especially for boards with tightly spaced components or devices on both sides. Optimizing feeder setups can boost efficiency.
Reflow Soldering
Tweaking thermal profiles and conveyor speed during reflow soldering is needed to ensure uniform heating and prevent defects like solder balls.
Cleaning & Inspection
Post-reflow cleaning removes harmful flux residue while inspection using AOI machines catches any errors. This prevents passage of defects to functional testing.
Functional Testing
Thoroughly testing assembled boards for functionality using fixtures that replicate operation conditions is vital to ensure boards work properly before shipping.
By working closely with your CM to optimize each step above, you’ll achieve higher assembly yields, quality, and reliability.
PCB Assembly Costs & Pricing Models
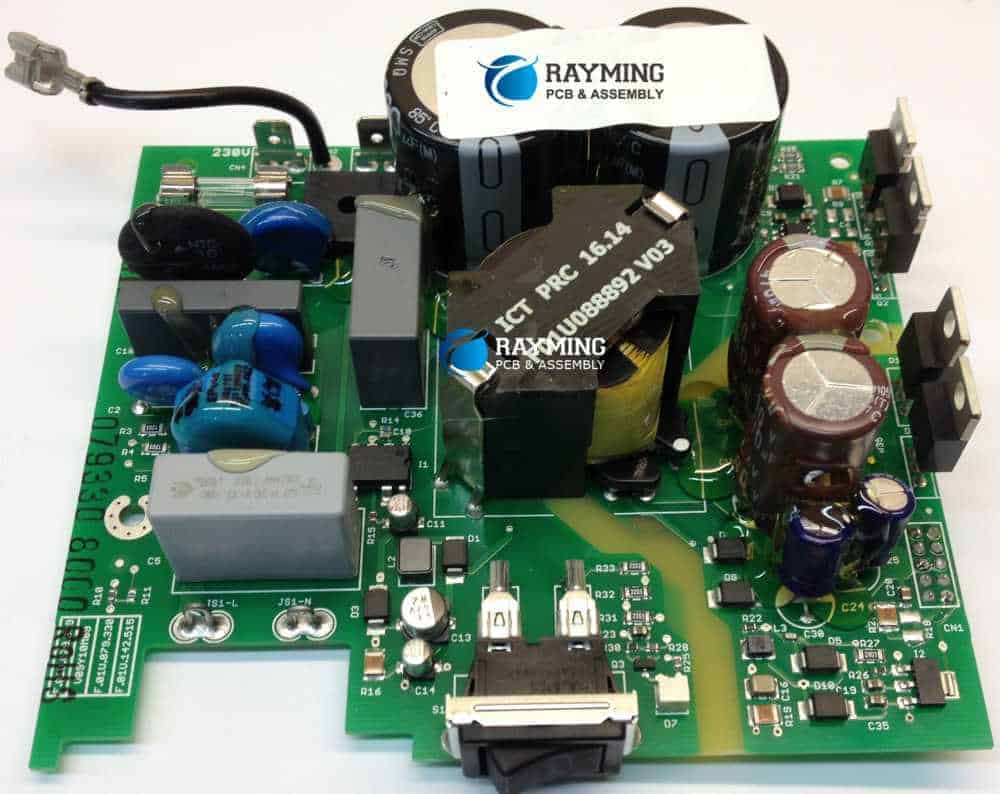
For most companies, costs are a primary factor in choosing to outsource PCB assembly versus keeping it in-house. The leading pricing models in contract manufacturing include:
- Per component – Each unique component is priced individually with additional fees per board and for other operations like programming, testing, etc.
- Per joint – Total solder joints on the board sets the base price. Additional operations add fees per board.
- Turnkey – A fixed price per fully assembled board based on expected volumes, often with tiers at different quantities. Additional fees apply for changes.
- Time & materials – Hourly billing rate for labor plus material costs incurred. Best for low volume or prototyping builds.
Optimal pricing depends on expected order volumes and complexity of the product. Work closely with prospective CMs to understand how pricing breaks down and where there is flexibility.
Also discuss opportunities to reduce costs over the product lifecycle through:
- Design optimizations
- Component cost reduction
- Process improvements
- Testing & inspection automation
- Moving to lower cost regions for production
The right contract manufacturer will share detailed cost information and be transparent about reducing expenses further over time.
Conclusion
This guide covers the major factors to consider with contract PCB assembly in 2023. The key takeaways include:
- Outsourcing to a CM provides flexibility, expertise, and rapid time to market most companies cannot achieve in-house.
- Carefully qualify CMs on technical capabilities, quality, scalability, pricing models and other criteria.
- Work closely with your CM to optimize every step of the assembly process for your specific product.
- Understand pricing models and cost reduction opportunities to maximize value.
With the right contract manufacturing partner and ongoing collaboration, nearly any company can have complex PCBs assembled quickly and economically. Use the insights from this article to successfully leverage the strengths of contract PCB assembly for your next electronics project.
Frequently Asked Questions
Q: What are the most common defects in PCB assembly?
A: The most frequent assembly defects are solder shorts, opens or insufficient solder; poor component placement; damaged PCBs/components; and foreign object debris. Robust quality control during production minimizes these.
Q: Should I use an overseas or domestic contract manufacturer?
A: The optimal location depends on factors like required lead times, production costs, intellectual property risks, travel requirements, and relevant government regulations. Discuss locations with your CM.
Q: How are PCB assembly designs transferred to the contract manufacturer?
A: Design files like Gerber, CAD, and bill of materials data are provided electronically, often via PLM or FTP systems. Work with your CM on preferred transfer methods.
Q: How long does it take to get assembled PCB samples for prototyping?
A: With an existing design, a CM can typically provide prototype samples in 5-10 working days. New designs take longer, emphasizing the importance of design for manufacturing analysis.
Q: What data do I receive from the contract manufacturer about my PCB assembly order?
A: You’ll typically receive full traceability data for your boards including component lot codes/expiration dates, solder paste information, assembly date/time, test results, etc.
0 Comments