Introduction to Computer-Aided Manufacturing (CAM)
Computer-Aided Manufacturing (CAM) is a technology that uses computer software and hardware to automate and control the manufacturing process. CAM systems are designed to improve efficiency, accuracy, and repeatability in the production of various products, from simple components to complex assemblies. By integrating CAM with other technologies such as Computer-Aided Design (CAD) and Computer Numerical Control (CNC) machines, manufacturers can streamline their processes and reduce lead times.
Benefits of CAM
- Increased productivity
- Improved accuracy and consistency
- Reduced labor costs
- Shorter lead times
- Enhanced flexibility in product design and manufacturing
Automated High-Speed Machining
Automated high-speed machining is a key application of CAM technology. It involves using CNC machines to perform cutting, drilling, and other machining operations at high speeds and with high precision. This process is particularly useful for manufacturing complex parts with tight tolerances, such as those used in the aerospace, automotive, and medical industries.
Components of an Automated High-Speed Machining System
- CNC machine tools (e.g., mills, lathes, routers)
- CAM software for generating toolpaths and G-code
- Workholding devices (e.g., fixtures, vises, chucks)
- Cutting tools (e.g., end mills, drills, inserts)
- Coolant and lubrication systems
Advantages of Automated High-Speed Machining
- Faster machining times compared to conventional methods
- Ability to produce complex geometries and features
- Reduced tool wear and longer tool life
- Improved surface finish and part quality
- Decreased human intervention and error
CAM Software for Automated High-Speed Machining
CAM software plays a crucial role in automated high-speed machining by generating the toolpaths and G-code that control the CNC machine’s movements. Some popular CAM software packages include:
- Autodesk PowerMill
- Mastercam
- Siemens NX CAM
- ESPRIT CAM
- Delcam FeatureCAM
These software packages offer various features and capabilities, such as:
- 2D and 3D milling and turning
- High-speed machining strategies
- Simulation and verification tools
- Post-processing for different CNC controllers
- Integration with CAD systems
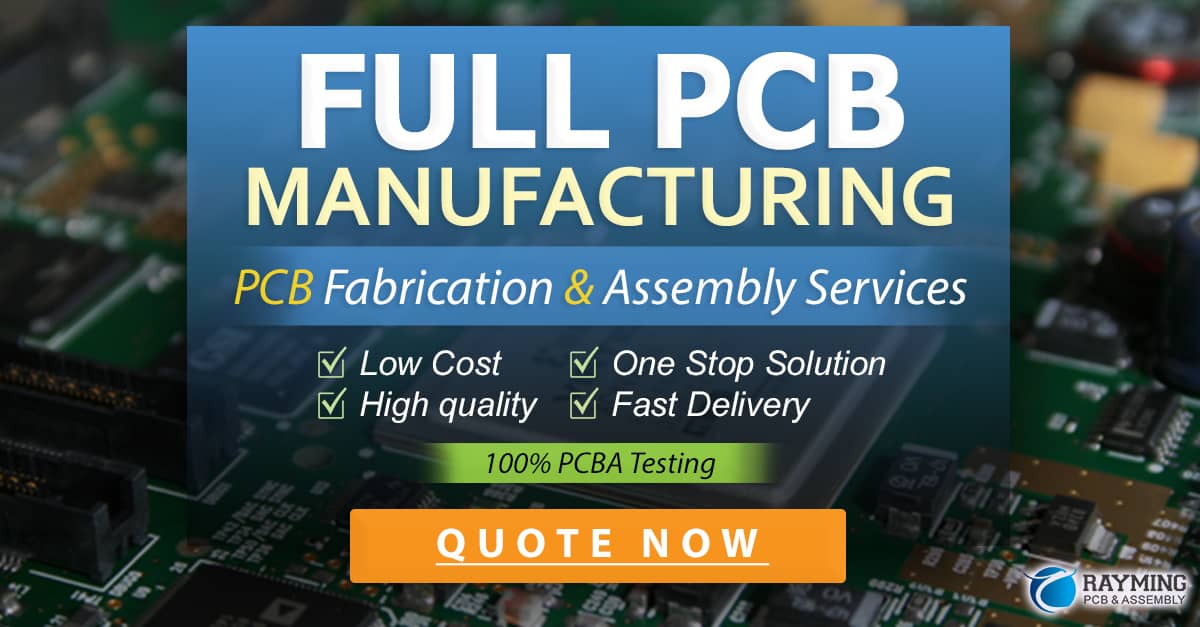
Tooling and Workholding for Automated High-Speed Machining
Proper tooling and workholding are essential for successful automated high-speed machining. Cutting tools must be designed to withstand the high speeds and forces involved in the process, while workholding devices must securely hold the workpiece in place without causing deformation or vibration.
Cutting Tools for High-Speed Machining
- Carbide end mills and drills
- Polycrystalline diamond (PCD) tools
- Ceramic inserts
- High-feed milling cutters
- Trochoidal milling tools
Workholding Devices for High-Speed Machining
- Hydraulic and pneumatic fixtures
- Vacuum chucks
- Magnetic chucks
- Mechanical vises and clamps
- Custom-designed fixtures for specific parts
Process Optimization in Automated High-Speed Machining
To achieve the best results in automated high-speed machining, it is essential to optimize the process parameters and strategies. This involves selecting the appropriate cutting tools, speeds, feeds, and toolpaths for each operation, as well as minimizing vibration and chatter.
Factors Affecting High-Speed Machining Performance
- Spindle speed and feed rate
- Depth of cut and width of cut
- Tool geometry and coating
- Workpiece material properties
- Machine tool rigidity and dynamic stability
Strategies for Optimizing High-Speed Machining
- Trochoidal milling for improved tool life and material removal rate
- Dynamic milling for reduced cutting forces and vibration
- High-feed milling for faster machining times
- Adaptive clearing for efficient roughing operations
- Constant engagement toolpaths for consistent tool load and surface finish
Case Studies: Applications of Automated High-Speed Machining
Automated high-speed machining has been successfully applied in various industries to improve productivity, quality, and cost-effectiveness. Some notable examples include:
Aerospace Industry
- Machining of titanium and aluminum parts for aircraft engines and structures
- Production of complex, lightweight components with tight tolerances
Automotive Industry
- Manufacturing of engine blocks, cylinder heads, and transmission components
- High-volume production of precision parts with consistent quality
Medical Industry
- Machining of implants, prosthetics, and surgical instruments
- Fabrication of complex geometries and biocompatible materials
Future Trends and Developments in CAM and High-Speed Machining
As technology advances, CAM and high-speed machining are expected to evolve and offer even greater capabilities and benefits. Some future trends and developments include:
- Integration of artificial intelligence (AI) and machine learning in CAM software
- Increased use of additive manufacturing (3D printing) in combination with high-speed machining
- Development of new materials and coatings for cutting tools
- Adoption of Industry 4.0 technologies, such as the Internet of Things (IoT) and big data analytics
- Expansion of hybrid manufacturing processes that combine multiple machining techniques
Frequently Asked Questions (FAQ)
1. What is the difference between CAM and CNC?
CAM (Computer-Aided Manufacturing) refers to the software and technology used to create toolpaths and generate G-code for manufacturing processes. CNC (Computer Numerical Control) refers to the machines that execute the G-code and perform the actual machining operations.
2. Can high-speed machining be used for all materials?
High-speed machining can be used for a wide range of materials, including metals, plastics, and composites. However, the specific process parameters and tooling must be optimized for each material to ensure successful machining and avoid issues such as excessive tool wear or poor surface finish.
3. What are the main challenges in implementing automated high-speed machining?
Some of the main challenges in implementing automated high-speed machining include:
- High initial investment costs for CNC machines and CAM software
- Need for skilled personnel to program and operate the machines
- Ensuring proper tooling and workholding for specific applications
- Optimizing process parameters to achieve the desired quality and productivity
- Managing tool wear and maintenance to avoid downtime and defects
4. How does automated high-speed machining compare to traditional machining methods?
Compared to traditional machining methods, automated high-speed machining offers several advantages:
- Faster machining times and higher productivity
- Improved accuracy and consistency in part quality
- Ability to produce complex geometries and features
- Reduced labor costs and human error
- Increased flexibility in product design and manufacturing
However, automated high-speed machining also requires a higher initial investment and specialized knowledge to implement and operate effectively.
5. What is the future outlook for CAM and high-speed machining?
The future outlook for CAM and high-speed machining is positive, with continued growth and adoption expected across various industries. As technology advances, CAM software and CNC machines are likely to become more intelligent, integrated, and efficient, enabling manufacturers to produce higher-quality parts at lower costs. Additionally, the integration of additive manufacturing and hybrid processes will expand the capabilities and applications of high-speed machining.
Conclusion
Computer-Aided Manufacturing (CAM) and automated high-speed machining are transforming the manufacturing landscape by enabling faster, more accurate, and more cost-effective production of complex parts and components. By leveraging advanced software, CNC machines, and optimized tooling and workholding, manufacturers can achieve significant improvements in productivity, quality, and flexibility.
As technology continues to evolve, the integration of artificial intelligence, additive manufacturing, and Industry 4.0 technologies will further enhance the capabilities of CAM and high-speed machining. Manufacturers that invest in these technologies and adapt to the changing landscape will be well-positioned to meet the demands of the future and maintain a competitive edge in their respective industries.
0 Comments