Introduction to PCB in Mobile Phones
In the modern world, mobile phones have become an integral part of our daily lives. These compact devices are packed with advanced features and capabilities that allow us to stay connected, entertain ourselves, and manage our tasks on the go. At the heart of every mobile phone lies a complex network of electronic components, all interconnected through a printed circuit board (PCB). In this article, we will delve into the world of class carrier mobile phone PCBs, exploring their design, manufacturing, and the crucial role they play in the functionality and performance of our beloved smartphones.
What is a PCB?
A printed circuit board, or PCB, is a thin board made of insulating materials, such as fiberglass or plastic, with conductive pathways etched onto its surface. These pathways, known as traces, connect various electronic components, such as resistors, capacitors, and integrated circuits (ICs), allowing them to communicate and function as a cohesive system. PCBs provide a stable and organized platform for these components, ensuring reliable electrical connections and minimizing the risk of short circuits or signal interference.
The Importance of PCBs in Mobile Phones
In the context of mobile phones, PCBs serve as the backbone of the device, connecting and supporting all the essential components that make a smartphone work. From the processor and memory chips to the display and camera modules, every component relies on the PCB to receive power and exchange data. The quality and design of the PCB directly impact the performance, reliability, and durability of the mobile phone.
Types of PCBs Used in Mobile Phones
Mobile phone PCBs come in various types, each with its own unique characteristics and manufacturing processes. The choice of PCB type depends on factors such as the device’s size, complexity, and intended use. Let’s explore some of the most common types of PCBs found in mobile phones.
1. Single-Layer PCBs
Single-layer PCBs, as the name suggests, consist of a single conductive layer on one side of the insulating substrate. These PCBs are the most basic and cost-effective option, making them suitable for simple mobile phone designs or low-end devices. However, single-layer PCBs have limitations in terms of component density and signal routing, which can restrict their use in more advanced smartphones.
2. Double-Layer PCBs
Double-layer PCBs have conductive layers on both sides of the insulating substrate, allowing for more complex component placement and signal routing. The two layers are connected through small holes called vias, which enable electrical connections between the top and bottom layers. Double-layer PCBs offer improved functionality and space utilization compared to single-layer PCBs, making them a popular choice for many mobile phone designs.
3. Multi-Layer PCBs
As mobile phones become more sophisticated and feature-rich, the need for higher component density and more intricate signal routing arises. Multi-layer PCBs address this need by stacking multiple conductive layers, separated by insulating layers, within a single board. These PCBs can have four, six, eight, or even more layers, depending on the complexity of the device. Multi-layer PCBs enable the integration of a large number of components in a compact space, making them ideal for high-end smartphones with advanced features and capabilities.
PCB Type | Layers | Complexity | Cost |
---|---|---|---|
Single-Layer | 1 | Low | Low |
Double-Layer | 2 | Medium | Medium |
Multi-Layer | 4+ | High | High |
PCB Design Considerations for Mobile Phones
Designing a PCB for a mobile phone is a complex process that involves numerous considerations to ensure optimal performance, reliability, and manufacturability. Let’s explore some of the key factors that influence the design of class carrier mobile phone PCBs.
1. Component Placement
The placement of components on the PCB is crucial for several reasons. Firstly, it affects the overall size and shape of the mobile phone, as the PCB must fit within the device’s housing. Secondly, component placement impacts signal integrity and electromagnetic compatibility (EMC). Components that generate or are sensitive to electromagnetic interference (EMI) must be strategically placed to minimize crosstalk and signal degradation. Additionally, thermal management is a critical consideration, as heat-generating components, such as the processor, need to be placed in a way that allows for effective heat dissipation.
2. Signal Routing
Signal routing refers to the design of the conductive traces that connect the various components on the PCB. Proper signal routing is essential for ensuring reliable communication between components and minimizing signal loss or interference. High-speed signals, such as those used for data transmission or clock synchronization, require careful routing to maintain signal integrity and avoid issues like crosstalk or reflections. Ground planes and power planes are also incorporated into the PCB design to provide stable reference voltages and reduce noise.
3. Electromagnetic Compatibility (EMC)
Mobile phones are subject to strict electromagnetic compatibility (EMC) regulations to ensure they do not cause interference with other electronic devices and can operate reliably in the presence of external electromagnetic fields. PCB designers must adhere to EMC guidelines and employ various techniques to minimize electromagnetic interference (EMI). These techniques include proper component placement, use of shielding materials, and the implementation of filters and suppression components.
4. Manufacturing Considerations
PCB design must also take into account the limitations and requirements of the manufacturing process. Factors such as minimum trace width, minimum clearance between traces, and the size of vias and pads must be considered to ensure the PCB can be reliably manufactured. Additionally, the choice of materials, such as the type of substrate and the finish of the conductive layers, can impact the performance and durability of the PCB.
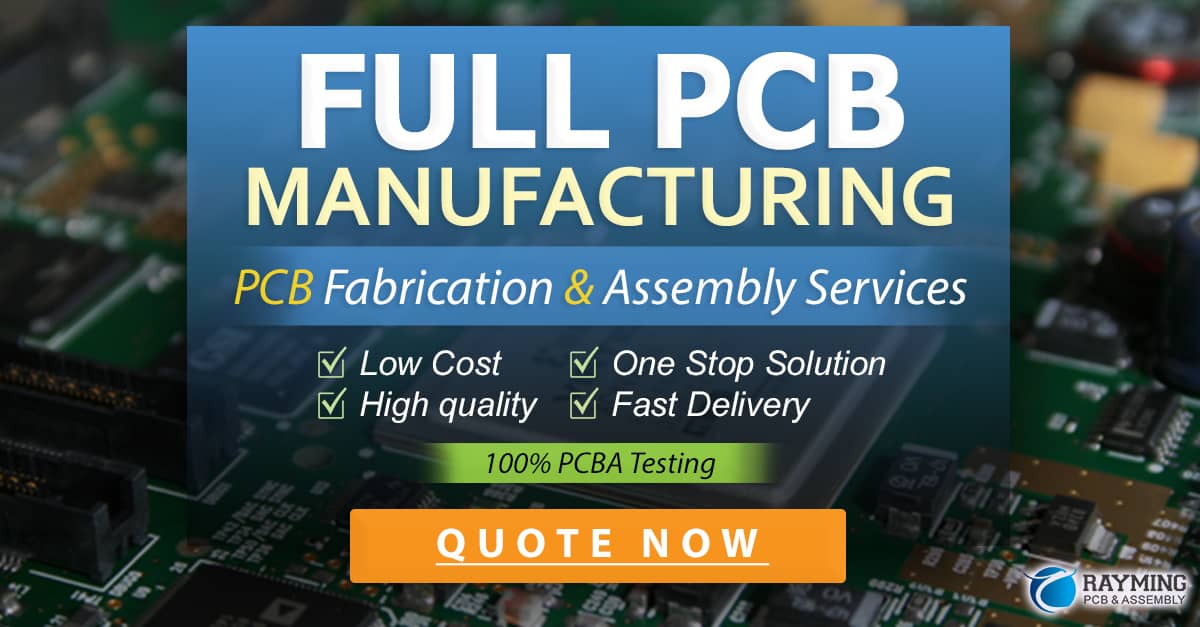
PCB Manufacturing Process for Mobile Phones
The manufacturing process for class carrier mobile phone PCBs involves several stages, each requiring precision and adherence to strict quality control measures. Let’s take a closer look at the key steps involved in PCB manufacturing.
1. PCB Design and Layout
The first step in the PCB manufacturing process is the design and layout of the board. Using specialized software, PCB designers create a digital representation of the PCB, including the placement of components, routing of traces, and the creation of necessary layers. The design is then thoroughly reviewed and verified to ensure it meets all the required specifications and design rules.
2. PCB Fabrication
Once the design is finalized, the PCB fabrication process begins. This involves the following sub-steps:
a. Substrate Preparation: The insulating substrate, typically made of fiberglass or other materials, is cut to the required size and shape.
b. Copper Lamination: Thin sheets of copper are laminated onto the substrate using heat and pressure, forming the conductive layers of the PCB.
c. Drilling: Holes are drilled into the PCB to accommodate components and create vias for inter-layer connections.
d. Patterning: The desired circuit pattern is transferred onto the copper layers using a photolithography process. This involves applying a light-sensitive resist, exposing it to UV light through a patterned mask, and then etching away the unwanted copper.
e. Plating: The holes and vias are plated with copper to ensure reliable electrical connections between layers.
f. Solder Mask Application: A protective solder mask is applied to the PCB, covering the copper traces while leaving the pads exposed for component soldering.
g. Silkscreen Printing: Text, symbols, and logos are printed onto the PCB using a silkscreen process for identification and assembly purposes.
3. Component Placement and Soldering
After the PCB fabrication is complete, the next step is to place and solder the electronic components onto the board. This process can be done manually for low-volume production or prototyping, but automated pick-and-place machines are used for high-volume manufacturing. The components are positioned on the PCB and then soldered in place using reflow soldering or wave soldering techniques.
4. Inspection and Testing
To ensure the quality and functionality of the manufactured PCBs, rigorous inspection and testing procedures are carried out. These may include:
a. Visual Inspection: The PCBs are visually inspected for any defects, such as misaligned components, solder bridges, or damaged traces.
b. Automated Optical Inspection (AOI): Automated systems use high-resolution cameras to detect any visible defects or anomalies on the PCB.
c. X-Ray Inspection: For multi-layer PCBs, X-ray inspection is used to verify the integrity of internal connections and check for any hidden defects.
d. Electrical Testing: The PCBs undergo electrical testing to ensure all the components are functioning correctly and the board meets the required performance specifications. This may involve in-circuit testing (ICT), flying probe testing, or functional testing.
5. Final Assembly and Packaging
Once the PCBs have passed all the necessary inspections and tests, they are ready for final assembly into the mobile phone housing. The PCB is integrated with other components, such as the display, battery, and camera modules, to create a complete mobile phone unit. The finished products are then packaged and prepared for distribution.
Manufacturing Step | Description |
---|---|
PCB Design and Layout | Creation of digital PCB representation |
PCB Fabrication | Substrate preparation, copper lamination, drilling, patterning, plating, solder mask application, and silkscreen printing |
Component Placement and Soldering | Positioning and soldering of electronic components onto the PCB |
Inspection and Testing | Visual inspection, automated optical inspection, X-ray inspection, and electrical testing |
Final Assembly and Packaging | Integration of PCB with other components and packaging of the finished product |
Future Trends in Mobile Phone PCB Technology
As mobile phones continue to evolve and push the boundaries of technology, PCB design and manufacturing must keep pace with these advancements. Let’s explore some of the future trends in mobile phone PCB technology that are shaping the industry.
1. Miniaturization and High-Density Packaging
The demand for smaller, thinner, and more powerful mobile phones is driving the trend towards miniaturization and high-density packaging of PCBs. This involves the use of advanced technologies, such as embedded components, 3D packaging, and chip-on-board (COB) assembly. These techniques allow for the integration of more components in a smaller space, enabling the development of compact and feature-rich mobile devices.
2. Flexible and Stretchable PCBs
Flexible and stretchable PCBs are gaining traction in the mobile phone industry, as they offer new possibilities for device design and functionality. These PCBs are made using flexible substrates, such as polyimide or TPU, and can bend, fold, or stretch without losing their electrical properties. Flexible and stretchable PCBs enable the creation of curved or foldable displays, wearable devices, and other innovative form factors.
3. 5G and High-Frequency PCBs
With the advent of 5G networks, mobile phones require PCBs that can handle high-frequency signals and support faster data transmission rates. High-frequency PCBs use advanced materials, such as low-loss dielectrics and high-performance laminates, to minimize signal loss and maintain signal integrity at higher frequencies. Additionally, PCB designers must employ specialized routing techniques, such as controlled impedance routing and microstrip transmission lines, to ensure optimal performance in 5G devices.
4. Eco-Friendly and Sustainable PCB Materials
As environmental concerns gain prominence, there is a growing trend towards the use of eco-friendly and sustainable materials in PCB manufacturing. This includes the adoption of halogen-free and lead-free materials, as well as the use of biodegradable and recyclable substrates. PCB manufacturers are also implementing green manufacturing practices, such as energy-efficient processes and waste reduction initiatives, to minimize their environmental impact.
Frequently Asked Questions (FAQ)
1. What is the difference between a single-layer and a multi-layer PCB in mobile phones?
Single-layer PCBs have a single conductive layer on one side of the insulating substrate, while multi-layer PCBs have multiple conductive layers stacked and separated by insulating layers. Multi-layer PCBs offer higher component density and more complex signal routing, making them suitable for advanced mobile phones with numerous features and capabilities.
2. Why is component placement important in mobile phone PCB design?
Component placement on a mobile phone PCB is crucial for several reasons. It affects the overall size and shape of the device, as the PCB must fit within the phone’s housing. Additionally, proper component placement helps minimize electromagnetic interference, ensures optimal signal integrity, and facilitates effective thermal management.
3. What is the purpose of the solder mask on a mobile phone PCB?
The solder mask is a protective layer applied to the PCB during the manufacturing process. It covers the copper traces while leaving the pads exposed for component soldering. The solder mask prevents accidental short circuits, protects the traces from oxidation and damage, and provides electrical insulation between adjacent traces.
4. How are mobile phone PCBs tested for quality and functionality?
Mobile phone PCBs undergo rigorous inspection and testing procedures to ensure their quality and functionality. These include visual inspection, automated optical inspection (AOI), X-ray inspection for multi-layer PCBs, and electrical testing such as in-circuit testing (ICT), flying probe testing, or functional testing. These tests help identify any defects, anomalies, or performance issues before the PCBs are assembled into the final mobile phone units.
5. What are some of the future trends in mobile phone PCB technology?
Future trends in mobile phone PCB technology include miniaturization and high-density packaging, which involve techniques like embedded components and 3D packaging to integrate more components in a smaller space. Flexible and stretchable PCBs are also gaining prominence, enabling innovative device form factors. With the rise of 5G networks, high-frequency PCBs that can handle faster data transmission rates are becoming increasingly important. Additionally, there is a growing trend towards the use of eco-friendly and sustainable materials in PCB manufacturing to reduce environmental impact.
Conclusion
Class carrier mobile phone PCBs are the unsung heroes of the smartphone world, providing the foundation upon which all the advanced features and capabilities of modern mobile devices are built. From the basic single-layer PCBs to the complex multi-layer boards, PCB technology continues to evolve to keep pace with the ever-increasing demands of the mobile phone industry.
Designing and manufacturing mobile phone PCBs is a complex process that requires a deep understanding of electrical engineering, material science, and manufacturing techniques. PCB designers must balance numerous considerations, such as component placement, signal routing, and electromagnetic compatibility, to create boards that are reliable, efficient, and cost-effective.
As mobile phones continue to advance, so too will PCB technology. Trends such as miniaturization, flexible and stretchable PCBs, and high-frequency materials are shaping the future of the industry, enabling the development of even more innovative and powerful mobile devices.
By understanding the critical role that PCBs play in mobile phones and staying informed about the latest advancements in PCB technology, we can better appreciate the incredible engineering and manufacturing feats that go into creating the devices that keep us connected, entertained, and productive in our daily lives.
0 Comments